2.3. Технология производства гипсовых вяжущих
Технологический процесс производства гипсовых вяжущих состоит в измельчении гипсового камня (дроблении и помоле) и тепловой обработке (дегидратации). Степень измельчения гипсового камня перед тепловой обработкой определяется типом теплового аппарата. В запарочные аппараты материал подают кусками размером до 400 мм, во вращающиеся печи—10— 35 мм, а в варочные котлы — в виде порошка. Используемые технологические схемы получения гипсовых вяжущих отличаются одна от другой видом и последовательностью основных операций. Наиболее распространенные технологические схемы условно можно представить следующим образом:
Дробление помол варка
Дробление сушка помол варка
Дробление сушка + помол варка
Дробление помол варка помол
Дробление сушка + помол варка помол
Дробление обжиг помол
Дробление обжиг + помол
Дробление запаривание помол
Первые
пять схем используют при производстве
гипсовых вяжущих в гипсоварочных котлах,
тепловая обработка материала в которых
носит название варки. Наиболее простая
схема 1, но ее применение возможно лишь
при сухом сырье. Если влажность сырья
превышает 1 %, то перед помолом его
необходимо сушить (схема 2). Целесообразно
совмещение этих двух операций в одном
технологическом аппарате (схема 3). Для
улучшения качества продукции желателен
вторичный помол полуводного гипса,
выходящего из варочных котлов (схемы 4
и 5). Схему 6 используют как при производстве
высокообжиговых, так и низкообжиговых
гипсовых вяжущих во вращающихся печах,
а схему 7 — в аппаратах совмещенного
помола и обжига. Схема 8 предназначена
для получения гипса повышенной прочности
на основе α-модификации полугидрата.
Выбор технологической схемы и типа
аппарата для тепловой обработки зависит
от масштабов производства, свойств
сырья, требуемого качества продукции
и других факторов.
Производство
гипсовых вяжущих в гипсоварочных
котлах получило наибольшее распространение
(рисунок). Гипсовый камень предварительно
дробится в щековой дробилке. Для той же
цели могут использоваться молотковые
и конусные дробилки. Дробленый материал
поступает на помол в шахтную мельницу
(или же аэробильную, ролико-маятниковую,
шаровую).
Широко применяется шахтная молотковая мельница. Она состоит из размольной камеры и быстровращающегося ротора с дисками, на которых шарнирно укреплены молотки. Над мельницей находится прямоугольная металлическая шахта высотой 9—14 м, а на высоте 1 м от размольной камеры — течка, через которую в мельницу поступает предварительно дробленое сырье. Попадая на вращающийся ротор, оно измельчается в тонкий порошок. В шахтной мельнице может одновременно осуществляться помол и сушка сырья. Это особенно ценно, так как наличие влаги затрудняет помол гипсового камня, а предварительная сушка сырья в отдельном аппарате, например, сушильном барабане, усложняет технологическую схему.
Источником
теплоты для сушки материала в шахтных
мельницах в большинстве случаев являются
отработанные в варочных котлах газы с
температурой 350— 500 °С и выше. Непрерывно
поступая под ротор мельницы, они уносят
с собой продукт помола вверх в шахту,
где он подсушивается. При этом процесс
саморегулируется— более крупные зерна
выпадают из газового потока и снова
поступают в мельницу, где повторно
измельчаются, а мелкие уносятся в
пылеулавливающие устройства. Обычно
скорость горячих газов в шахте составляет
4—б м/с. При ее уменьшении помол становится
более тонким, при увеличении —- более
грубым. Тонкодисперсные частицы,
уловленные системой пылеочистки,
поступают в гипсоварочный котел.
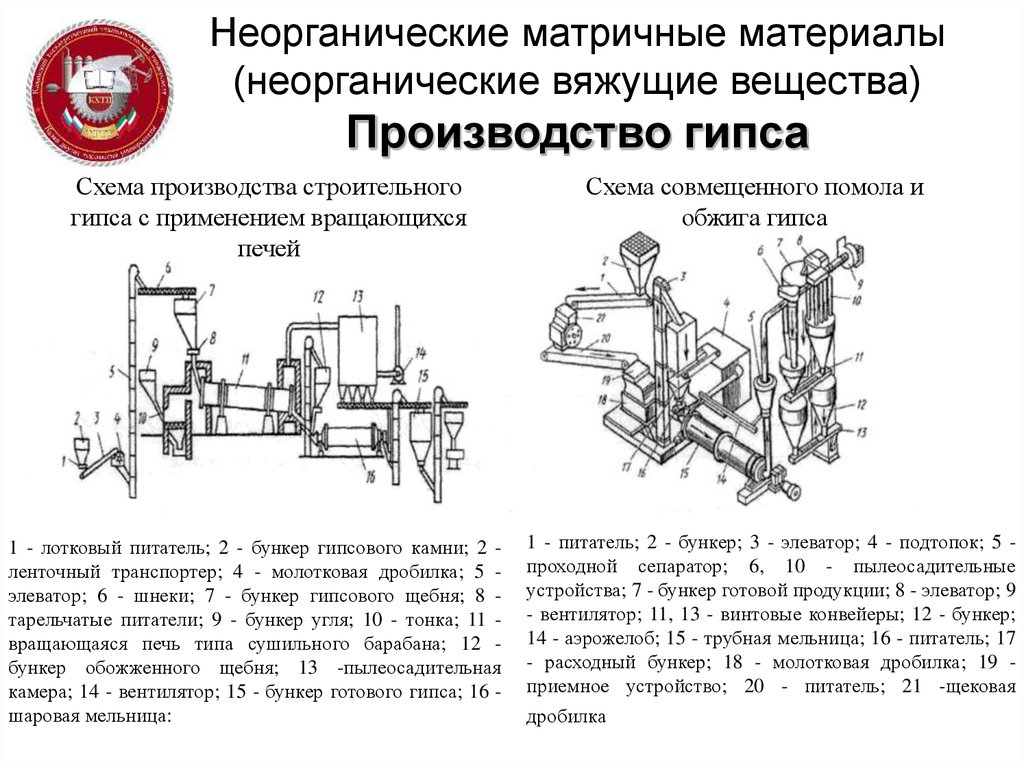
Предварительно разогретый котел загружают сверху через отверстие в крышке при непрерывной работе мешалки. После загрузки первой порции ожидают признаков «кипения», вызванного выделением паров воды. Затем продолжают постепенно засыпку гипсового порошка и следят, чтобы гипс все время находился в кипящем состоянии.
Продолжительность
дегидратации гипсового камня в котлах
зависит от их емкости, тонкости помола
порошка и т. д. Она колеблется от 50 мин
до 2,5 ч. В котлах, например, объемом 12 м3 температура сырья быстро поднимается
с 80 до 119°С. Затем, несмотря на поступление
теплоты, некоторое время она сохраняется
постоянной. Это соответствует периоду
выделения из гипса кристаллизационной
воды и превращения ее в пар. Бурное
кипение материала требует большого
расхода теплоты. По мере уменьшения в
порошке количества двугидрата теплота
начинает расходоваться не только на
физико-химические процессы, но и на
нагрев образовавшегося полугидрата. Слишком высокая температура (170—180°С)
может вызвать вторичное его кипение,
обусловленное дегидратацией полуводного
гипса. При этом возможна осадка материала,
что затрудняет выгрузку его из котла.
По окончании варки материал выгружают в бункер выдерживания для постепенного охлаждения в течение 20—30 мин. Объем бункера обычно вдвое больше объема котла. Выдерживание улучшает качество вяжущего. Оставшийся двугидрат за счет теплоты выгруженного материала переходит в полугидрат. Одновременно под действием паров воды растворимый ангидрит гидратируется до полугидрата. В результате выравнивается состав продукта, снижается его водопотребность и повышается качество.
Получаемый
в варочных котлах продукт в основном
состоит из -полугидрата.
Однако содержание в нем α-полугидрата
можно повысить подачей в варочный котел
небольших количеств солей, например
0,1 % NaCl. Раствор соли снижает упругость
пара у поверхности зерен, в итоге
ускоряется процесс варки и повышается
качество продукта.
Производительность наиболее перспективного варочного котла СМЛ-158 вместимостью 15,2 м3 составляет 8,5 т/ч. Удельный расход условного топлива на 1 т гипса составляет 52 кг при использовании твердого топлива и 40 кг при использовании газа и мазута. Удельный расход электроэнергии 105—110 МДж.
На многих заводах процесс варки гипса в котлах автоматизирован. Загрузка котла сырьем до определенного уровня, поддержание заданной температуры гипса в конце варки, перемещение выгрузочного шибера выполняются соответствующими исполнительными механизмами. В результате сокращаются затраты ручного труда, уменьшается вероятность перегрева обечаек и днищ котлов, стабилизируется процесс варки и повышается качество продукции.
Заполнение
котла гипсом контролируется сигнализатором
уровня. Сигнал датчика передается на
электродвигатель шнека-загрузчика и
отключает его.
Варочные котлы отличаются простотой обслуживания, удобством регулирования и контроля режима обжига. Обрабатываемый в них материал с пламенем и дымовыми газами не соприкасается и не загрязняется золой. Однако варочным котлам присущи и некоторые недостатки: периодичность работы, быстрая изнашиваемость днища и обечаек котлов, сложность улавливания гипсовой пыли.
Дальнейшим
усовершенствованием гипсоварочных
котлов является перевод их с периодического
режима работы на непрерывный. Тонкомолотый
гипс загружают в котел непрерывно ниже
уровня поверхности обрабатываемого
материала. Образующийся в процессе
варки полугидрат имеет меньшую плотность,
поэтому он вытесняется из нижней зоны
непрерывно поступающим в котел сырым
гипсовым порошком. Поднимаясь, полугидрат
доходит до окна в боковой стенке котла
и самотеком поступает в бункер
выдерживания. Производительность таких
котлов в 2—3 раза выше, чем котлов
периодического действия. Однако
конструктивная сложность снижает
надежность их работы и ограничивает
распространение.
Производство
гипса во вращающихся печах достаточно широко распространено в
отечественной и зарубежной практике.
Вращающаяся печь — наклонный металлический
барабан, по которому медленно перемещается
дробленый гипсовый камень с размером
кусков до 35 мм. Для обжига гипса на
полугидрат используют печи длиной до
8—14 м и диаметром 1,6—2,2 м. Топливо сжигают
в специальной топке. Между топкой и
печью часто помещают смесительную
камеру, в которой во избежание пережога
продукта температура выходящих из топки
газов несколько понижается за счет
смешения их с холодным воздухом.
Обжиг производят по методу как прямотока, так и противотока. Температура поступающих в печь горячих газов при прямотоке должна быть 950—1000 °С, при противотоке — 750—800 °С. При прямотоке достигается более равномерный обжиг гипса и, следовательно, лучшее его качество. При этом происходит своеобразное саморегулирование процесса обжига: мелкие, быстро дегидратирующиеся частицы транспортируются газами в холодный конец печи тем быстрее, чем меньше их размер и больше скорость газов. Однако при прямотоке выше расход топлива.
При
обжиге во вращающихся печах необходимо
создавать однородность размеров кусков
сырья, поступающего на обжиг, и их
сохранность при тепловой обработке. В
зависимости от времени нахождения
материала в печи определяют предельно
допустимый размер кусков. Так, куски
размером 40 мм должны находиться в печи
1,5—2 ч. Выходящий из ночи горячий материал
направляют в бункера выдерживания или
сразу подвергают помолу.
Производство гипсовых вяжущих во вращающихся печах может быть интенсифицировано улучшением теплообмена между теплоносителем и гипсовым камнем и увеличением коэффициента загрузки обжиговых агрегатов. Такая модернизация позволяет увеличить производительность печей, улучшить режим обжига гипсового камня, повысить однородность состава готового продукта и его качество, а также снизить затраты топлива и потери теплоты с отходящими газами.
Производительность
вращающейся печи зависит от объема
внутренней части, угла наклона и частоты
вращения печи, температуры и скорости
движения газов, качества сырья и других
факторов и составляет 125— 250 кг обожженного
гипса в час на 1 м3 объема печи. Производство гипсовых
вяжущих во вращающихся печах позволяет
выпускать более дешевый гипс при
меньших капитальных затратах. Полученный
гипс имеет более высокие прочностные
показатели, чем при использовании
варочных котлов. Он отличается пониженной
водопотребностью (48—57%), что позволяет
на 20—25 % снизить его расход при
приготовлении растворов и бетонов. Непрерывно действующие вращающиеся
печи обеспечивают компактность
технологической схемы, позволяют
автоматизировать процесс. Однако их
недостатком являются трудность
регулирования процесса, необходимость
обеспечения стабильности технологических
параметров, а также повышенный пылеунос.
Двухступенчатая тепловая обработка (сушка и варка) усложняет производственный процесс. Хотя при сушке гипсовый камень частично дегидратируется, содержание гидратной воды в сырье остается высоким, и для перевода в полугидрат его необходимо доваривать в варочном котле.
В
последние годы получил распространение совмещенный
помол и обжиг гипсовых вяжущих,
когда тепловая обработка происходит в
самом помольном агрегате в результате
интенсивного теплообмена между горячими
газами и измельчаемым материалом. У
мельницы дополнительно сооружается
предтопок, в котором сжигается топливо
и в мельницу поступают газы с температурой
700—800°С. Расход условного топлива при
этом составляет 40—50 кг на 1 т вяжущего. Мельницы снабжают сепараторами проходного
тина, после которых измельченный и
дегидратированный продукт поступает
в пылеуловители.
Схемы производства при совмещенном помоле и обжиге отличаются главным образом используемым типом мельниц (шахтные, шаровые, аэробильные), а также тем, что в одних случаях мельницы работают с однократным использованием теплоносителя, а в других— с возвратом в мельницу части газов после пылеочистки. Применение рециркуляции газов повышает расход электроэнергии, но снижает расход топлива. Один из вариантов производства гипсовых вяжущих при совмещении их помола и обжига представлен на рисунке.
Гипсовый
камень проходит две стадии дробления
в щековой и молотковой дробилке и в виде
частиц размером 10—15 мм поступает в
шаровую мельницу, куда также подаются
дымовые газы из предтопка. Дегидратированный
в процессе измельчения материал выносится
газовым потоком в сепаратор, где из него
отделяются крупные частицы, и возвращаются
в мельницу. Тонкие фракции гипса
улавливаются в пылеосадителях, после
чего очищенные газы выбрасываются и
атмосферу. Производственный цикл при
получении гипсовых вяжущих в мельницах
совмещенного помола и обжига — самый
короткий, и число агрегатов — минимальное.
Достоинство таких установок— их
компактность и высокая производительность.
Однако вследствие кратковременности
воздействия газов наиболее крупные
частицы не успевают полностью
дегидратироваться, а часть мелких частиц
пережигается, в результате полученное
вяжущее быстро схватывается и имеет
пониженную прочность.
Получение
гипсовых вяжущих α-модификации в среде,
насыщенной паром. Тепловая обработка гипсового камня в
варочных котлах, вращающихся печах и
мельницах происходит при атмосферном
давлении; кристаллизационная вода
удаляется из гипсового камня в виде
пара и в результате продукт тепловой
обработки состоит в основном из
-CaSO40,5H2O.
Для получения гипса повышенной прочности,
состоящего в основном из α-полугидрата,
необходимо создать такие условия, чтобы
кристаллизационная вода удалялась из
двуводного гипса в капельно-жидком
состоянии. Известны два основных способа
получения гипса повышенной прочности:
1) автоклавный, основанный на обезвоживании гипсового камня в герметических аппаратах в среде насыщенного пара под давлением выше атмосферного;
2) тепловая обработка в жидких средах, т. е. обезвоживание гипса кипячением в водных растворах некоторых солей.
Автоклавный
способ получения гипсовых вяжущих может
быть реализован в различных аппаратах.
Запарочный аппарат представляет собой
герметичный вертикальный металлический
резервуар с люками и затворами для
загрузки и выгрузки материала. В нижней
части аппарата имеется обезвоживающее
сито, через которое стекает конденсат,
а при продувании отводятся топочные
газы. Пар подается в аппарат сверху в
перфорированную трубу, размещенную в
центре. Запарник загружают гипсовым
камнем размером 15—40 мм и обрабатывают
его насыщенным паром под давлением 0,23
МП а при 114°С в течение 5—8 ч. Затем
в том же аппарате материал сушат газами
с температурой 120—160°С в течение 3—5 ч. Высушенный материал размалывают.
Недостатки этого способа: неравномерность
сушки, высокий расход топлива и энергии.
Получило распространение также производство высокопрочных гипсовых вяжущих способом «самозапаривания», при котором избыточное давление создается за счет испарения из гипсового камня части гидратной воды. Дробленый гипсовый камень загружают в герметически закрываемый вращающийся «самозапарник», куда подают топочные газы с температурой около 600°С. Проходя по находящимся внутри аппарата трубам, эти газы нагревают материал. В результате двуводный гипс разлагается, и выделяющаяся вода создает в аппарате избыточное давление. Дегидратация гипса протекает в паровой среде под давлением 0,23 МПа в течение 5—5,5 ч. Излишки пара периодически сбрасываются. После запаривания материал в этом же. аппарате сушат, снижая для этого давление до 0,13 МПа в течение 1,5 ч, а затем до атмосферного. Общая продолжительность цикла 12—14 ч. Полученный продукт измельчают в мельницах.
Известно
производство гипса повышенной прочности
запариванием в автоклаве гипсового
камня размером 300—400 мм (70 % общего
количества камня) и 100— 250 мм (остальные
30%). Запаривание осуществляют в течение
6 ч, доводя давление пара в автоклаве до
0,6 МПа. По окончании запаривания давление
пара в течение 1,5 ч снижают до атмосферного.
Затем гипсовый камень подвергают сушке
при закрытых крышках автоклавов 7 ч, при
открытых крышках 10 ч и охлаждают 4 ч.
Общий цикл запаривания и сушки гипсового
камня составляет 28—30 ч. Выгруженный из
автоклава продукт размалывают. Гипсовые
вяжущие, получаемые в среде, насыщенной
паром, отличаются большей мономинеральностью
структуры, более крупной и правильной
кристаллизацией, меньшей водопотребностью
и повышенной прочностью. Поэтому в
практике их называют высокопрочным
гипсом.
Получение
гипсовых вяжущих варкой в жидких средах. Относительно низкая температура перехода
двуводного гипса в полуводный дает
возможность получить высокопрочные
гипсовые вяжущие тепловой обработкой
порошка двугидрата в открытых
емкостях в растворах некоторых солей,
поскольку температура кипения растворов
при атмосферном давлении выше температуры
дегидратации гипса. В жидкой среде
происходит интенсивная передача теплоты
от солевого раствора к частицам гипса,
что ускоряет химические реакции.
Получаемый продукт однороден по составу
и состоит преимущественно из α-полугидрата.
В качестве жидких сред применяют водные
растворы солей СаС12,
MgCl2,
MgSO4,
Na2CО3,
NaCl и др. Продолжительность варки в
зависимости от вида раствора и его
концентрации составляет 45—90 мин.
Полученный таким образом полуводный
гипс отцеживают или отделяют от жидкой
среды центрифугированием, промывают
до полного удаления солей и сушат при
70—80 °С, затем материал размалывают в
порошок.
Возможно также получение гипсового вяжущего повышенной прочности кипячением молотого гипсового камня в воде с добавкой 1,5—3 % поверхностно-активных веществ (сульфитно-дрожжевой бражки, асидола, мылонафта). Температура кипения такого раствора 128—132 °С, время варки 70—90 мин.
Варка
в жидких средах позволяет получить
продукт высокого качества и сократить
длительность производственного цикла,
однако необходимость отделения гипса
от солевого раствора и дополнительная
операция сушки усложняют технологический
процесс.
Производство гипсовых вяжущих из отходов химической промышленности. Рост объемов гипсосодержащих отходов химической промышленности повышает актуальность их переработки в гипсовые вяжущие. Наиболее крупнотоннажный вид отходов — фосфогипс. Переработка его на гипсовые вяжущие усложняется наличием в нем до 5—7 % примесей фосфора, фтора, кремния и долей процента редкоземельных элементов, главным образом лантанидов, а также повышенной влажностью. Наиболее отрицательно влияют фосфаты, соединения фтора и редкоземельных элементов. Они или входят в кристаллическую решетку полугидрата, или образуют на поверхности его кристаллов труднорастворимые пленки, тормозящие гидратацию вяжущего. Поэтому гипсовое вяжущее высокого качества -модификации может быть получено из фосфогипса только после многократной предварительной отмывки водорастворимых и нейтрализации остальных примесей.
Если
фосфогипс содержит более 0,5 % водорастворимого
Р2О5,
то предварительная промывка необходима
и при переработке его в α-модификацию
полугидрата. Если же содержание примесей
меньше, то пульпа с соотношением жидкое
: твердое 1
подается в автоклав, где производится
гидротермальная обработка при температуре
150—175°С и давлении 0,4—0,7 МПа. Дегидратация
фосфогипса и последующая кристаллизация
α-полугидрата сопровождаются удалением
из продукта примесей, входящих в
кристаллическую решетку CaSO4-2H2O.
После гидротермальной обработки твердая
фаза α-полугидрата отделяется на
вакуум-фильтре. Корж с влажностью около
10 % сушится в сушильном барабане и
размалывается в мельнице. Разработана
также непрерывная технология
гидротермальной переработки фосфогипса
в высокопрочное гипсовое вяжущее или супергипс (α-полугидрат) (рисунок),
при которой вредные примеси во время
перекристаллизации гипса связываются
дополнительными компонентами, вводимыми
в технологический процесс, а размеры
кристаллов полугидрата регулируются
органическими и неорганическими
добавками.
Фосфогипс
подается в репульпатор, где смешивается
с водой и добавкой регулятора кристаллизации
до соотношения Ж:Т = 1 с учетом влажности
фосфогипса. Пульпа перекачивается
насосом в расходную емкость, где
нагревается до 60—70 °С. Отдельно готовят
комбинированную добавку, смешивая в
специальной емкости с пропеллерной
мешалкой портландцемент и активную
минеральную добавку с водой до соотношения
Ж:Т = 4—5:1. Комбинированная добавка и
пульпа фосфогипса насосом одновременно
накачиваются в автоклав, где происходит
гидротермальная обработка в течение
35—45 мин при давлении 0,4—0,7 МПа и
температуре 150—175°С. В процессе ее
суспензия непрерывно перемешивается
мешалкой. Из автоклава водно-полугидратная
пульпа подается в холодильник, а после
охлаждения до 98—100°С — на вакуум-фильтр.
Из пульпы отжимается вода, и остается
лепешка влажностью 10—15%. Она поступает
в сушильный барабан, где сушится
топливными газами при температуре 400—
500 °С. Материал собирается в бункере, из
которого потом направляется в шаровую
или вибрационную мельницу.
Технология производства высокопрочного гипса
Современное производство строительных материалов
В зависимости от характера тепловой обработки все известные способы производства высокопрочного гипса разделяют на автоклавные, основанные на обезвоживании гипса в среде насыщенного пара под давлением выше атмосферного в герметических аппаратах, и на термообработку в жидких средах, когда гипс обезвоживается в процессе кипячения в водных растворах некоторых солей при атмосферном давлении. При автоклавном способе производства с тепловой обработкой сырья в автоклаве, а сушкой продукта в сушильном барабане природный гипсовый камень дробится в щебенку с размерами кусков 10-50 мм и загружается в автоклав, представляющий собой вертикально установленный стальной цилиндрический резервуар с термостойкой облицовкой для предотвращения потери тепла. В верхней части резервуара имеется герметически закрывающийся люк для загрузки гипсовой щебенки. Здесь же расположен патрубок для пара и штуцер для термометра. Внизу автоклава имеется сферическая открывающаяся крышка, на которой расположена решетка, на которой находится щебенка в процессе пропаривания. Под этой решеткой скапливается конденсат, выпускаемый из автоклава через штуцер. Автоклав с помощью кронштейнов может крепиться к перекрытию. Над автоклавом обычно располагают бункер с готовой гипсовой щебенкой, которая загружается в люк но специальной течке или матерчатому рукаву. После загрузки автоклав герметизируется и в него подается насыщенный пар для термообработки сырья под давлением 0,13 МПа при температуре 124°С.
Тепловая обработка при таких параметрах пара и крупности гипсовой щебенки 10-50 мм длится в течение 5,5-6 час. В это время происходит дегидратация гипсового камня и выделение кристаллизационной воды и жидком состоянии. Образующийся полугидрат имеет вид хорошо оформленных крупных кристаллов. В процессе теплообработки конденсат периодически удаляется из автоклава по мере накопления, но так, чтобы горячая вода в известном количестве постоянно находилась в автоклаве под решеткой. Технологическая схема получения высокопрочного гипса представлена на рис. 3.4. Если тепловая обработка гипсового камня в варочных котлах и мельницах производится при атмосферном давлении и получаемый продукт состоит преимущественно из fi-CaS04 – 0,5ЩО, то для получения гипса повышенной прочности, состоящего в основном из а-полугидрата, необходимо создать такие условия, чтобы кристаллизационная вода удалялась из двуводного гипса в капельно-жидком состоянии. Это достигается обезвоживанием гипсового камня либо в герметических аппаратах в среде насыщенного пара под давлением выше атмосферного, либо кипячением в водных растворах некоторых солей, температура кипения которых не ниже температуры дегидратации гипсового камня.
Какую сетку выбрать для забора и ее виды
Заборы из сетки сегодня являются одними из самых востребованных на строительном рынке. Такой тип ограждений можно считать универсальным. Его используют в частном загородном строительстве, в городском и коммерческом секторе, на …
Технология производства высокообжиговых гипсовых вяжущих веществ
Гипсовые вяжущие материалы, воздушные вяжущие материалы, получаемые на основе полуводного сульфата кальция либо безводного сульфата кальция (ангидритовые вяжущие). По условиям термической обработки, а также по скорости схватывания и твердения гипсовые вяжущие материалы делятся на 2 …
Кровельные и гидроизоляционные материалы на битумной основе
Материалы, предназначенные для предохранения конструкций и инженерных сооружений от действия воды, называют гидроизоляционными. В зависимости от применяемого вяжущего гидроизоляционные мате-риалы подразделяют на битумные, дегтевые и полимерные. По способу нанесения их …
Новые и рекомендуемые материалы:
Малый бизнес
Гипс: производственные решения | Grenzebach
Модульные и индивидуальные технологии производства гипса
Опыт Grenzebach в обработке гипса
Grenzebach является вашим партнером по полному спектру услуг по переработке природного, синтетического и переработанного гипса. Наши технические специалисты и инженеры разрабатывают производственные решения, специально адаптированные к вашим потребностям, от концептуального планирования и отдельных компонентов до комплексных производственных установок. Основное внимание здесь уделяется вашим способностям и формулированию идей. Системы, которые мы разрабатываем для вас, столь же разнообразны, как ваше сырье и продукты, которые вы предоставляете своим клиентам.
Являясь одним из ведущих мировых поставщиков систем производства гипса, мы разделяем страсть к гипсу. Мы используем наши высокопроизводительные производственные решения, наш опыт и знания уже более 130 лет, чтобы обеспечить успех наших клиентов. Наш отраслевой опыт основан на ноу-хау давно зарекомендовавшей себя компании Babcock-BSH.
WE Service — Ваш партнер по жизненному циклу
Установки для производства гипсокартона
Ноу-хау Grenzebach для индивидуального создания помещений
Гипсокартон предоставляет огромные возможности для современного дизайна интерьера. Grenzebach предлагает свои глубокие знания процессов и многолетний опыт, чтобы сочетать разнообразные возможности применения с функциональностью гипсокартона. Тонкая настройка между природой сырья и характеристиками конечного продукта является одной из наших основных компетенций. Наши производственные линии представляют собой индивидуальные решения, которые предоставляют нашим клиентам широкий спектр преимуществ гипса высшего качества.
Производственные линии гипсокартона
Растворы для производства гипса
Домашний уют благодаря высококачественной штукатурке
Гипсовая штукатурка – это материал, история которого насчитывает тысячи лет и который до сих пор способствует улучшению качества жизни и здоровья людей. Его физические свойства создают идеальные условия для здорового микроклимата в помещении. Высококачественная гипсовая штукатурка также обеспечивает превосходную отделку поверхности. Функциональность, эстетика и строительная биология – эффекты, возникающие при обработке сырья. Благодаря точно настроенным технологическим решениям мы помогаем вам перерабатывать сырье в точном соответствии с вашими требованиями.
Производственные решения для гипса
Процессы производства гипсовых стеновых блоков
Высокотехнологичные решения от Grenzebach для элитного дизайна интерьеров
Гипсовые стеновые блоки представляют собой высокоэффективные элементы для гибкого разделения помещений. Они устанавливаются с использованием метода строительства из гипсокартона для формирования огнеупорных, устойчивых к вредителям и плесени стен. В соответствии со своим обещанием, Grenzebach является вашим партнером, предлагающим комплексные технологии вдоль линии производства гипсовых стеновых панелей, позволяющие вам производить полые и сплошные стеновые панели.
Линии гипсовых стеновых блоков
Наши услуги для вашего завода по производству гипса
партнерство
Проектирование, строительство и ввод в эксплуатацию новой линии по производству гипса — это только первые шаги в хороших отношениях с клиентами. Профессиональное обслуживание в повседневной эксплуатации не менее важно: мы хотим, чтобы ваши инвестиции приносили постоянную прибыль, поэтому наши инженеры готовы помочь и проконсультировать вас на протяжении всего жизненного цикла установки.
Гипс-Послепродажное обслуживание
Download
无法找到 Материалы Что такое гипс Как перерабатывается гипс %23Classification_Of_Gypsum
Щековая дробилка представляет собой горно-шахтное механическое оборудование, часто используемое при дроблении, производстве песка, обогащении и других областях. Щековая дробилка имеет большой коэффициент дробления и высокую мощность дробления, поэтому она часто используется в качестве первичного дробильного оборудования. Щековые дробилки в работе часто подвержены разной степени износу, поэтому неисправности неизбежны. Здесь мы резюмируем […]
5 Дефекты бетонных конструкций [Причины, профилактика и ремонт]
Дефекты бетонных конструкций влияют не только на внешний вид, но и на функцию использования, характеристики конструкции и срок службы объекта. Поэтому необходимо проводить эффективную профилактику и контроль. Эти дефекты могут быть вызваны различными причинами или причинами. В этой статье вы узнаете о 5 распространенных дефектах бетонных конструкций, […]
Экран для обезвоживания угля | Принцип работы | Особенности
Экран для обезвоживания угля представляет собой вид просеивающего оборудования, разработанного для обезвоживания, удаления шлама и удаления песка из шламовых материалов. Он широко используется для обезвоживания угольного шлама, разделения фильтрацией под давлением, обезвоживания и извлечения очень мелких материалов и т. д. Как работает грохот для обезвоживания угля В грохоте для обезвоживания угля применяется технология самосинхронизации с двойным двигателем, общий эксцентриковый блок и […]
6 советов, которые помогут сделать искусственный песок высокого качества
С ростом числа строительных проектов увеличивается количество бетона, а также увеличивается спрос на песок. Высококачественный искусственный песок может удовлетворить потребность в песке для различных строительных проектов. Так как же сделать качественный искусственный песок? Вам необходимо рассмотреть 6 советов: сырье, оборудование для производства песка, производственный процесс, […]
5 Различия между морским и речным песком
Речной песок представляет собой вид мелких частиц, образующихся в результате повторяющихся ударов, столкновений или трения камней о реку в течение длительного периода естественного состояния. Морской песок относится к песку, размытому морской водой без опреснения, в основном от слияния морской воды и рек, содержащему коррозионно-активные соли. Речной и морской песок […]
Что такое кирпичная кладка | Как осуществлять надзор за строительством кирпичной кладки
Что такое кирпичная кладка Кирпичная кладка, цельный материал, состоящий из кирпича и раствора, является наиболее широко используемым строительным материалом в настоящее время.