Линия производства рельсовых подкладок
Технические характеристики
Производительность, тонн/год |
90 (с возможностью расширения до 180 тонн/сутки) |
Способ нагрева заготовки под штамповку |
индукционный ТВЧ нагрев |
Температура нагрева, ºС |
700±10 |
Вес оборудования, тонн |
90 (транспортное оборудование 25 тонн) |
Суммарная потребляемая мощность, кВт |
750 |
Расход воздуха, м3/мин |
5 (Р=0,5 МПа) |
Расход технической воды, м3/час |
6 |
Планировка по линии производства рельсовых подкладок 1 — толкатель |
После отрубания заготовок подкладок на прессе однокривошипном простого действия модели К04. 119.240 они поступают на существующую транспортную линию. Подкладки продолжают движение и по достижению толкателя 1 (поз.1) сталкиваются в зону индукционного нагрева, на транспортер зоны ТВЧ(поз. 3), где блоком нагрева ТВЧ (поз.2) подкладки нагревают до необходимой температуры, но не более 700ºС.
Суммарная установленная мощность зоны ТВЧ нагрева не менее 900 кВт. Напряжение питания 220/380 В. Частота тока нагрева от 5 до 12 кГц.
Зона нагрева состоит из четырех секций индукционного нагрева с установленной мощностью не менее 225 кВт каждый. Секция индукционного нагрева состоит из преобразователя частоты, водоохлаждаемых трансформаторно-согласующего устройства и индуктора длиной не менее 1 м.
Между секциями индукционного нагрева установлены промежуточные зоны выравнивания температуры по всему сечению рельсовой подкладки.
По достижению температуры нагрева заготовки подкладок поштучно поступают на пресс К1739 (поз.4) для прошивки отверстий, после чего толкатель 1 в зоне выдачи подкладок перемещает их на рольганг (поз.
После прохождения рольганга (поз.5) подкладки поступают в зону охлаждения, состоящую из транспортера холодильника длиной не менее 5 м (поз.6) и блока охлаждения (поз.7), где заготовки доводят до температуры не более 60ºС.
Блок охлаждения состоит из системы водовоздущных форсунок, которые дифференцированно подают охлаждающую среду на различные элементы профиля подкладки, и вспомогательных систем (ресиверы, фильтры, насосы). Расход воды не более 4 м3/час.
По прохождению блока охлаждения толкатель направляет заготовки в зачистную машину (поз.8), в которой производится удаление заусенцев и обработка краев подкладки. Затем заготовки поступают на пост выборочного контроля (поз.9) и далее по транспортеру (поз.10) перемещается до кантователя (поз.11) и магазина подготовки пакетов (поз.12). Транспортер пакетов (поз.13) помещает пакет в упаковщик (поз.14) и перемещает дальше по линии до манипулятора (поз.17). Манипулятор укладывает пакеты на поддоны, поддон помещается в упаковщик (поз.
Линии для производства листа — ООО «Полимермаш-сервис» — российский производитель оборудования для переработки пластмасс
Модель | ЛПС 45-300 | ЛПС 63-1000 | ЛПС 75-1200 | ЛПС 90-1500 |
Ширина производимого листа (мм) | 300 | 1000 | 1200 | 1500 |
Диаметр шнека (мм) | 45 | 63 | 75 | 90 |
Толщина листа (мм) | 0,4-10 | 0,4-10 | 0,4-10 | 0,4-10 |
Производительность не более (кг/час) | 60 | 150 | 200 | 300 |
Скорость протягивания изделий, м/мин | 6 | 8 | 8 | 8 |
Мощность основного двигателя (кВт) | 30 | 55 | 75 | 110 |
youtube.com/embed/mQBssaQ-5_8″ allowfullscreen=»»/>
Линии для производства листа применяются для изготовления листовых материалов из из полиэтилена высокого и низкого давления, полистирола, полипропилена, АБС-пластика, поливинилхлорида и других типов полимеров. Компания «Полимермаш-сервис» предлагает продажу оборудования под ключ – от подбора комплектации для конкретного предприятия, проводит пусконаладочных работы и техническое обслуживание. Состав линии для производства листа: загрузчик автоматический, бункер-сушилка сырья, экструдер одношнековый, система охлаждения, фильтр шиберный, головка экструзионная плоскощелевая. каландр, устройство тянущее, термостат, устройство обрезки кромок, поперечной резки листового материала, приёмное или намоточное.Особенности предлагаемого «Полимермаш-сервис» оборудования
- Равномерное качество получаемого листового материала, обеспечивающее стабильное качество изготавливаемых из него изделий;
- Линии имеют трех валковую установку проката листов, с системой автономной настройки температуры каждого вала: это дает возможность для производства продукции достойного качества;
- Инверторное управление обеспечивает простую регулировку скорости производственного комплекса.
Состав линии
Экструзионные линии для производства труб
Экструзионная линия для производства труб представляет собой особенный вид промышленных автоматизированных конвейеров, специально предназначенных для изготовления трубчатых изделий и полимерных плит разнообразного назначения и любых размеров. Данные приборы дают возможность изготавливать изоляционные оболочки для проводов и трубы, которые применяются в системах водо- и газоснабжения, водосточных и дренажных комплексах. Главными преимуществами экструзионных линий является простота в обращении, высокая производительность, позволяющая оперативно, в зависимости от внутренних запросов предприятия или спроса, изменять объемы выпускаемой продукции.
Несмотря на несколько существующих классификаций экструзионных линий для производства труб, основным и главным фактором разделения на категории этих приборов служит фильера — деталь, которая формирует трубную головку.
Экструзионная линия для производства полимерных труб в зависимости от назначения состоит из разнообразных узлов, но при этом каждая из них обязательно содержит несколько основных секций: экструдер, фильеры, калибратор, шестеренчатый насос расплава, охлаждающая ванна, измерительный прибор, протяжное устройство, укладчик или намотчик, нарезчик.
Технические характеристики экструзионных линий для производства гладких труб из ПВХ (PVC)
Модель | GF63 | GF110 | GF200 | GF400 | GF630 | GF800 |
Диаметр трубы, мм | 16-63 | 16-110 | 32-200 | 160-400 | 315-630 | 450-800 |
Число траков, шт | 2 | 3 | 6 | 6 | 9 | 12 |
Усилие отводов, кН | 6 | 8 | 11 | 30 | 40 | 50 |
Скорость отвода, м/с | 15 | 12 | 8 | 4 | 2 | 2 |
Общая мощность оборудования, кВт | 14 | 14 | 14 | 41 | 56 | 64 |
Также возможна нестандартная комплектация линий GF-250 и GF-500.
Изготовление труб посредством экструзионного оборудования — это сложный, многоступенчатый процесс. На первом этапе через воронку загрузочного бункера подается гранулированное сырье в нагревательный цилиндр, где происходит его расплавление и тщательное перемешивание.
На следующем этапе шестеренчатый насос с заранее заданной скоростью подает к головке фильеры порции расплавленной массы, где происходит формовка продукции. По принципу «непринудительной экструзии» изготавливаются трубки малого диаметра ( до 10 мм): сырье проходя через формующую головку приобретает вид конечного изделия. Изготовление труб большего диаметра происходит при помощи использования специального устройства — калибратора, которое расположено непосредственно сразу за фильерой и задает габариты заготовки будущей трубы. И именно в калибраторе изделие подвергается охлаждению и приобретает итоговый размер и форму.
Толщина стенки трубы зависит от количества экструдеров, их производительности и скоростью устройства протяжки. Количество слоев готового изделия зависит от количества экструдеров. На толщину изделия влияет скорость движения через протяжку: чем быстрее движется масса, тем тоньше будут слои изделия, и как следствие, сама труба на выходе из экструзионной линии.
Измерительный датчик контролирует диаметр трубы. Датчики могут быть представлены как ультразвуковым, так и лазерным устройством. Лазерные приборы принято считать более точными, они также регулируют в режиме реального времени толщину изделия. Более высокой показатель допустимой погрешности имеют ультразвуковые измерители. Данные измерители дешевле лазерных, поэтому их устанавливают обычно на экструзионных линиях бюджетного сегмента.
Для производства гофрированных труб и шлангов экструзионные линии оснащают специальным инструментом — гофратором. Монтируется он непосредственно за формующей головкой и занимается выполнением сразу двух функций: калибровкой изделия и придания ему волнообразного рельефа.
Экструзионные линии производства шлангов из ПВХ, силикона, полиуретана
powertech. [email protected]
POWERTECH
MACHINERY
Производитель экструзионного оборудования из Циндао Китай
Главная
Экструзионные линии шланга
Наши продукты
Экструзионные линия для производства шлангов и рукавов из ПВХ, силикона, полиуретана которые применяются для различной транспортировки материалов: воды, масла, воздуха, сыпучих материалов, нефтепродуктов, грязи, сточных вод и других материалов. В зависимости от экструзионной линии шланги могут быть однослойные, многослойные, спиральновитые шланги ПВХ+ПВХ, армированные спиральной стальной проволокой, поливочные многослойные шланги ПВХ армированные нитью, напорные многослойные шланги с армировкой нитью обмоточным способом или вязальным.

В большинстве случаев экструзионная линия включает в себя:
Одношнековые экструдеры серии SJ, который наиболее подходит для производства необходимых размеров. Толщины слоев и диаметров могут регулироваться.
Экструзионную голову , подходящую для необходимых шлангов или рукавов.
Ванны охлаждения, которые служат для охлаждения шланга, оснащены водяным насосом для подачи воды,
регулировкой по X (горизонту) и по Y (высоте).
Армирующее устройство, которое подбирается исходя из способов армировки.

Тянущее устройство, роликовое, валковое или ленточное.
Линия может комплектоваться различными устройствами, в зависимости от потребностей производства.
Это могут быть: Намотчик, лазерный принтер для маркировки, планетарное тянущее устройство, дополнительный формующий инструмент, чиллер.
CONTACT INFORMATION
Mob/Whatsapp: +79158165038
Mob/Whatsapp: +79378497822
Mob/Whatsapp: +8615192681981
Email: [email protected]
Email: [email protected]
Address: No. 58, Pingcheng East road Jiaoxi Industrial Park
Jiaozhou city, Qingdao, China, 266300
Copyright © 2021 Qingdao Powertech Machinery Co.,Ltd. All rights reserved.
Автоматические линии для производства и сборки коллекторных электродвигателей
Изготовление КД с применением ручного труда не позволяет достигать их высокого качества и однообразия электромеханических параметров, что важно при массовом производстве. Технологический процесс производства КД должен соответствовать уровню современной технологии, который, прежде всего, обеспечивается необходимыми технологическим оборудованием и оснасткой (рис 1).
К достоинствам коллекторных двигателей можно отнести: компактные размеры, большой пусковой момент, быстроходность и отсутствие привязки к частоте сети, возможность планового регулирования оборотов в очень широком диапазоне: от 0 до номинального значения при изменении питающего напряжения, а также возможность их работы как на постоянном, так и на переменном токе. К недостаткам – наличие коллекторно-щёточного узла (КЩУ), из-за которого КД имеют относительно малую надёжность (срок службы), искрение, возникающее между щётками и коллектором из-за коммутации, высокий уровень шума, большое число деталей двигателя.
Даже в исправном двигателе между щётками и коллектором может возникать искрение, которое довольно сильно нагревает его ламели. А при стачивании щёток до предела и из-за их плохого прижима к коллектору искрение порой достигает кульминационного момента, представляющего собой электрическую дугу. В этом случае ламели коллектора сильно перегреваются и иногда отслаиваются от изолятора, образуя неровность, после чего даже при замене изношенных щёток двигатель будет работать с сильным искрением, выходя из строя. Для решения этой проблемы необходима тщательная конструкторская проработка КЩУ и всего КД с использованием 3D-проектирования, «know how», а также современных материалов.
В КД может возникать межвитковое замыкание обмотки ротора (рис 2, 3) или статора (это происходит нечасто), что также проявляется в сильном искрении КЩУ (из-за повышенного тока) или ослаблении магнитного поля двигателя, при котором ротор двигателя не развивает полноценный крутящий момент. Установлено, что 85–95 % отказов КД в работе происходит из-за повреждений изоляции обмоток, распределяемых следующим образом: 90 % межвитковых замыканий и 10 % повреждений и пробоев изоляции на корпус. Кроме того, происходит износ подшипников, деформация стали ротора или статора и изгиб вала. Поэтому при изготовлении КД необходимо подбирать качественные материалы для его деталей и узлов.
Надёжность коллекторного двигателя во много зависит от того, насколько грамотно производители подходят к технологическому процессу его изготовления и сборки. На многих предприятиях России используют ручную сборку КД, в том числе ручную намотку полюсов ротора, ручную прокладку изоляции пазов якоря, проточку коллекторов после намотки и сварки коллекторов. При этом качество КД оставляет желать лучшего: имеется существенный разброс параметров, не достигаются требуемые объёмы производства. А в силу большого количества деталей и узлов КД, а также высоких требований по точности сборки и допускам изготовления отдельных деталей технологический процесс их производства является довольно сложным.
Итальянская компания TEAM S.r.l – успешный европейский производитель автоматических и полуавтоматических линий. Основана в 1998 году в Италии в городе Поджибонси (Poggibonci). TEAM предлагает большой выбор машин и линий для производства и сборки коллекторных и асинхронных электродвигателей.
ТEAM поставляет свои автоматические производственные линии в компании автомобильной промышленности, производителям «белой техники» (холодильники, стиральные машины и т. д.), в компании, производящие электро- и пневмоинструменты.
Среди покупателей продукции компании Brose, Technik fur Automobile, Johnson Electric, Valeo, Crouzet, ELECTROLUX, FESTOOL, BOSCH, STANLEY, Black&Decker, HILTI и многие другие. За последние несколько лет TEAM поставила в Россию четыре большие автоматические производственные линии для изготовления электродвигателей: две линии в Тольятти (рис 4) и две в Калугу.
Сборка КД на автоматических производственных линиях в силу однородности и оптимизации технологического процесса позволяет избежать перечисленных недостатков. Однако стоимость таких линий довольно высока. Подобные капиталовложения можно оправдать только при массовом производстве уровня 350 тыс. – 1 млн двигателей в год. Линии объединяют ряд машин, управляемых с помощью компьютера, для их эксплуатации требуется, как правило, не более 2–3 рабочих. Если технологический процесс отлажен, то эффективность работы линии может достигать 95–100 %, она может эксплуатироваться в 2–3 рабочие смены.
К сожалению, наша промышленность еще не освоила производство таких линий. На предприятиях, в основном, используют отдельные машины для последующей комплектации из них полуавтоматических линий, что ведет к снижению качества готовой продукции. Например, проблема одного из наших заказчиков заключалась в невозможности достижения требуемых допусков при обработке коллекторов роторов КД на существующем оборудовании. По техническому заданию максимальный перепад между ламелями коллектора не должен был превышать 5 микрон, но заказчик не мог обеспечить величину данного параметра ниже 10–12 микрон и обратился к нам за помощью в подборе нового оборудования.
ООО «Остек-ЭТК» для решения таких задач своих заказчиков сотрудничает с итальянской компанией TEAM, которая разрабатывает и производит автоматические линии по производству различных типов электродвигателей, в том числе и коллекторных.
Как уже отмечалось, при массовом производстве КД требования к точности изготовления его элементов и узлов многократно возрастают. Например, для обеспечения высокой повторяемости и точности намотки полюсов ротора КД, сварки выводов полюсов ротора с элементами коллектора ротора согласно электрической диаграмме, последующей проточке и шлифовке коллектора ротора до требуемого в ТЗ размера с точностью до нескольких мкм, балансировки и тестирования готового ротора требуется автоматическая компьютеризированная линия.
Одна из проблем при производстве КД – обеспечение диаметра обработанного коллектора и перепад между ламелями коллектора с точностью до 3–5 мкм. Как правило, такую точность, заложенную в ТЗ, не удаётся обеспечить с помощью полуавтоматических машин, объединённых в линию. По результатам тестовых испытаний готовых роторов КД, изготовленных на автоматических линиях компании TEAM, требуемая точность обеспечивается практически в 100 % случаев.
Для примера приведем состав линии производства компании TEAM для изготовления роторов коллекторных двигателей для исполнительного механизма рулевой колонки автомобилей. На линии изготавливают два типа роторов в широком диапазоне размеров. Переналадка линии занимает всего несколько десятков минут, производительность составляет до 2000 роторов в смену.
Таблица 1 Значения пределов размеров роторов, которые могут изготавливаться на рассматриваемой линии TEAM
Значение |
Минимальное, мм |
Максимальное, мм |
A |
45 |
270 |
B |
15 |
- |
C |
8 |
70 |
D |
22 |
- |
E |
7 |
- |
F |
8 |
- |
G |
8 |
45 |
H |
6 |
- |
I |
3 |
15 |
L |
3 |
15 |
M |
8 |
45 |
N |
15 |
85 |
Линия выполняет следующие операции:
- сборку вала ротора с пакетом пластин якоря;
- установку конечных листов изоляции якоря;
- укладку пазов изоляции якоря;
- установку коллектора на вал ротора;
- намотку полюсов якоря и сварки его выводов с коллектором ротора;
- финишную обработку коллектора;
- балансировку ротора;
- тестирование готовых роторов.
Рамы машин, входящих в линию, изготовлены из высококачественной стали (электроплавка стали, упрочняющая прокатка швеллеров в вальцах).
Сегодня в ООО «Остек-ЭТК » поступает много запросов на поставку высококачественного оборудования для изготовления коллекторных двигателей. При необходимом объёме выпуска электродвигателей на уровне 350 тыс. – 1 млн двигателей в год – а такие объёмы реально востребованы нашей промышленностью – не существует другой альтернативы, кроме автоматических производственных линий, которые способны выпускать продукцию самого высокого качества с однородными электромагнитными и механическими параметрами. Наш партнер, компания TEAM, разрабатывает и изготавливает такие линии, обеспечивая качество оборудования и продукции, удовлетворяющее самые высокие требованиям заказчиков.
Линии для производства стрейч-пленки
Группа компаний «Апрель» имеет большой опыт в установке линий для производства стрейч-пленки. Наши линии комплектуются фильерами отличного качества от известного производителя JC-Times, все оборудование проходит проверку перед отгрузкой с завода. Наши сервисные инженеры запустят приобретенное оборудование и проконсультируют вас по всем интересующим вопросам. Для того чтобы подобрать модель линии, необходимо определиться с требуемыми техническими характеристиками: ширина производимой пленки (стандартно от 500 мм до 3*500 мм) и количество слоев (стандартно от 1 до 5, для работы с вторичным материалом желательно минимум 3 слоя).
Преимущества наших линий для производства стрейч-пленки:
- Высокопрочные шнеки из азотированной стали 38CrMoAl
- Двигатели Siemens
- Частотные преобразователи Holip
- Фильеры JC-Times, изготовленные из стали 5CrNiMo
- В базовую комплектацию входят капсулятор, периферийное оборудование, чиллер, пневмовалы
- Гибкая система выбора комплектации
- Возможность установить распределитель слоев (A/B/A или A/B/C/B/A, в зависимости от комплектации)
- Русифицированная документация
Производство и применение стрейч-пленки
Стрейч-пленка широко применяется для упаковки грузов, продуктов питания, защиты продукции от влаги при перевозке и хранении. Приобретая оборудование для производства стрейч-пленки, вы сокращаете затраты на покупку этого расходного материала.
Изготовление стрейч-пленки – прибыльный вид бизнеса, т.к. стрейч универсален по своей сути, и применяется на большинстве промышленных и торговых предприятий. Упаковочные материалы из стрейча используются повсеместно. Линия для производства стрейч-пленки требует лишь приобретения соответствующего сырья.
Производство стрейч-пленки – технологически несложный процесс, доступный даже малым предприятиям. Для получения качественного материала нужен надёжный станок для производства стрейч-пленки. Широкое распространение получила стрейч-пленка, изготовленная методом экструзии.
Отличительные особенности стрейч-пленки:
- высокая растяжимость до 500%;
- стойкость к проколам, которой позавидуют полиэтиленовые пленки;
- двусторонняя липкость.
Наше оборудование производит плёнку высокой эластичности, с повышенной устойчивостью к повреждениям и нужной прозрачностью. Звоните! Наши специалисты помогут Вам в подборе и поставке этого оборудования.
Наиболее популярные конфигурации стрейч-линий:
TL-70 — 1000 | TL-55 — 70-1000 | TL-55-70 — 55-1000 | TL-65-90 — 65-1500 | |
Количество слоев | 1 | 2 | 3 | 3 |
Ширина пленки | 2*500 / 1000 мм | 2*500 / 1000 мм | 2*500 / 1000 мм | 3*500 / 1500 мм |
Толщина пленки | 0.01 — 0.05 мм | 0.01 — 0.05 мм | 0.![]() | 0.01 — 0.05 мм |
Мощность двигателей | 22 кВт/ч | 15 + 22 кВт/ч | 15 + 30 + 15 кВт/ч | 18,5 + 45 + 18,5 кВт |
Произв-ность до | 100 кг/ч | 110 кг/ч | 110 кг/ч | 150 — 200 кг/ч |
Дополнительно к линии поставляются перемотчики рулонной стретч пленки с функцией резки.
Автоматический перемотчик стрейч-плёнки ARW-500
Автоматический перемотчик стрейч-пленки с функцией продольной резки.
Используется для перемотки пленки со шпули большего диаметра на шпули меньшего диаметра. Например, с помощью него можно перемотать стрейч-пленку на одну шпулю диаметром 500 мм, либо на две по 250 мм, и т. п.
Преимущества автоматического перемотчика стрейч-плёнки ARW-500:
- Функция продольной резки
- Надежность
- Стабильность работы
Модель | ARW-500 |
Ширина материала | 250mm~500mm |
Диаметр втулки на размотке | ∮76.2mm |
Напряжение | 220v/ 380v |
Двигатель | 4.5 кВт |
Скорость намотки | 0-1000m/min |
Пневматика | 0.4~0.6Mpa |
Оборудование для пищевой промышленности — «Стандартпродмаш»
Пищевая промышленность в настоящее время является одним из локомотивов российской экономики. Регулярно открываются новые предприятия, старые заводы проходят комплексную модернизацию, приобретая современное оборудование для пищевого производства. Только таким образом можно выиграть сегодня в конкурентной борьбе и успешно развиваться.
Промышленные линии розлива в ПЭТ для бизнеса
Группа компаний «Стандартпродмаш» предлагает разнообразное технологическое оборудование для пищевой промышленности в Северо-Западном федеральном округе. У нас вы можете:
- купить линию розлива воды, газированных напитков, пива, кваса, растительного масла или других жидкостей;
- оборудование для укупорки бутылок и наклейки этикеток;
- купить автомат выдува ПЭТ бутылок;
- и другую подобную продукцию.
Большие производственные мощности, современное оснащение, квалифицированные сотрудники, многолетний опыт работы, использование наиболее передовых материалов и технологий позволяет нам выпускать качественную, эффективную и экономичную продукцию, которая превосходно зарекомендовала себя в наших условиях и пользуется большим спросом.
Продажа оборудование для пищевой промышленности
Продажа пищевого оборудования – приоритетное, но не единственное направление деятельности нашей компании. В отличие от подавляющего числа конкурентов, наша задача – не просто предложить вам купить оборудование для ПЭТ бутылок, моноблок розлива воды и аппарат для укупорки бутылок, но помочь вам в организации прибыльного бизнеса.
Мы можем:
- провести анализ вашего предприятия, выявить наиболее слабые его места и выполнить модернизацию производства, чтобы существенно повысить производительность и снизить себестоимость продукции;
- подобрать оптимальное оборудование в соответствие с имеющимися производственными площадями, организовать его поставку, монтаж и настройку;
- организовать обучение персонала работе на нашем оборудовании;
- обеспечить его гарантийное и постгарантийное техническое обслуживание.
Все еще не можете решить, следует ли купить оборудование для розлива воды или нет? Тогда позвоните нам – мы обязательно предложим вам такие условия сотрудничества, от которых вы не сможете отказаться!
Читать полностьюЧто такое производственная линия?
отправлено Джоном Спейси, 7 февраля 2017 г.

Производственная линия — это заводская конфигурация, которая включает ряд этапов производства. Предметы перетекают от шага к шагу, приближаясь с каждым шагом к тому, чтобы стать готовым продуктом, частью или компонентом.
Сравнение серийного производства и массового производства
Производственные линии используются как в серийном, так и в массовом производстве. Серийное производство включает в себя перемещение набора элементов на каждом этапе вместе в виде партии.Например, пекарня может обрабатывать 1200 пончиков шаг за шагом, перемещая пончики вместе с рабочей станции на рабочую станцию. После этого производственную линию можно перенастроить для партии печенья. В массовом производстве все этапы производственного процесса выполняются одновременно. Например, если автомобили производятся в 28-этапном процессе, производственная линия может всегда иметь по одной машине на каждом этапе.Производство
Это полный список статей, которые мы написали о производстве.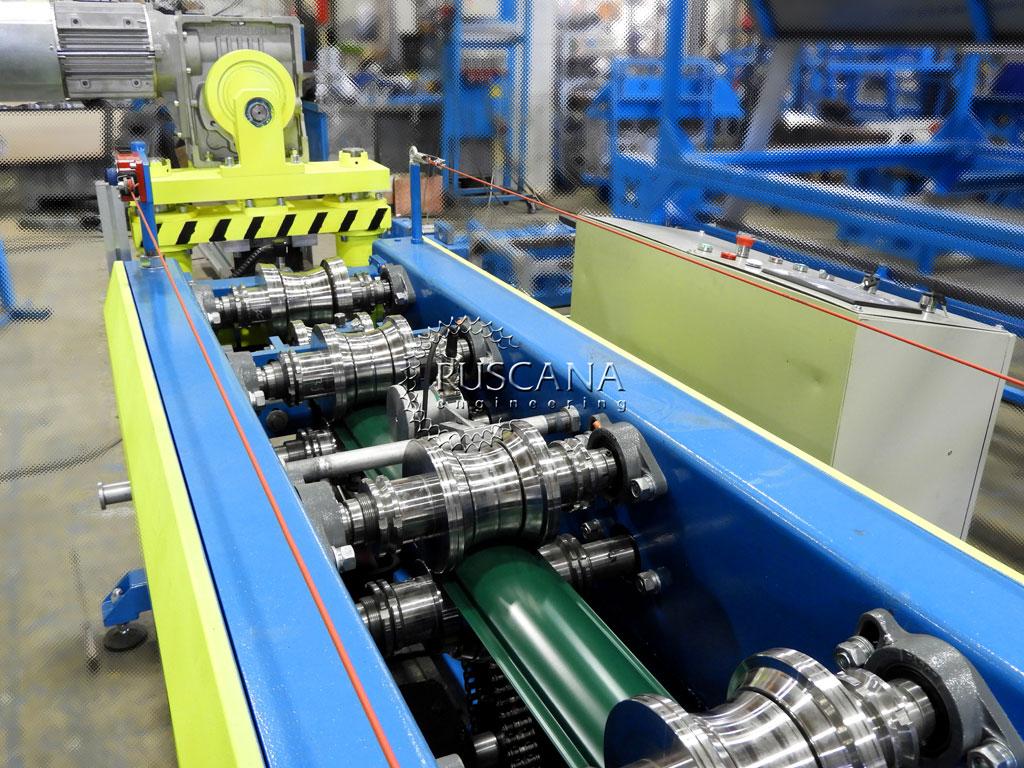
Если вам понравилась эта страница, добавьте в закладки Simplicable.
Обзор времени такта с формулой расчета и примером.
Справочник по изготовлению.
Разница между серийным и массовым производством.
Определение непрерывного процесса с примерами.
Определение «сделать на складе» с примерами.
Распространенные виды производственного процесса.
Определение производственного цикла с примерами.
Определение непрерывного производства с примерами.
Определение производства клеток с примерами.
Список распространенных бизнес-моделей.
Стратегия розничной торговли, сочетающая физические местоположения с сильным присутствием в электронной торговле.
Определение дополнительных товаров с несколькими примерами.
Организация, представляющая предприятия или профессионалов, у которых есть что-то общее.
Деловая разница между продуктами и услугами.
Несколько примеров распространенных бизнес-моделей.
Определение бизнес-модели.
Определение масштабируемой бизнес-модели с несколькими примерами.
Определение двустороннего рынка с примерами.
Самые популярные статьи о Simplicable за последний день.
Последние сообщения или обновления на Simplicable.
Три рабочие производственные линии | PROCESS EXPO 2021
- Home
- Три рабочие производственные линии
Только на PROCESS EXPO!
Обратите внимание на неизменно популярные интерактивные полнофункциональные производственные линии на выставочном зале. Ни одна другая выставка не предлагает такого уникального опыта, чтобы увидеть технологии в действии — от создания до конечной упаковки продукта. Представлены три различных сектора промышленности. Оставайтесь с нами для получения дополнительной информации.
Линия по производству мяса
PROCESS EXPO 2021 будет включать в себя автоматизированную линию по производству фрикаделек, которая начинается с измельчения, формовки, обработки, варки, замораживания и проверки сырого продукта перед его упаковкой для потребителя. Эта линейка фрикаделек будет включать в себя последние инновации от самых разных производителей оборудования, которые собираются вместе, чтобы продемонстрировать участникам PROCESS EXPO новейшие технологии.
Prepared Foods Line
Белки растительного происхождения — один из самых популярных продуктов в современной пищевой промышленности.Экспоненты PROCESS EXPO объединяют усилия, чтобы собрать куриный наггетс на растительной основе, который будет проходить несколько раз в день, и познакомить посетителей с процессом создания этого популярного продукта. Используя некоторые из крупнейших производителей оборудования в отрасли, мы проведем слушателей через производственный процесс во время ежедневных демонстраций, чтобы помочь вам понять сложность каждого этапа.
Bakery Line
Не пропустите третью производственную линию на PROCESS EXPO, поскольку мы производим обеденные булочки без глютена.Эта инновационная линия начнется с нашего миксера и внедрения наших безглютеновых ингредиентов и будет проходить до финальной упаковки. Эта автоматизированная линия будет включать новейшие технологии смешивания, укладки, выпечки, замораживания, проверки и упаковки. Учитывая проблемы, связанные с работой с рецептурами без глютена, эта демонстрация поможет переработчикам лучше понять инструменты, имеющиеся в их распоряжении для производства этого популярного продукта.
Посмотрите короткое видео о том, как поставщики работают вместе, чтобы проводить живые демонстрации с полностью работающими производственными линиями прямо на выставочной площадке — доступно ТОЛЬКО на PROCESS EXPO.
youtube.com/embed/1NY8GjR9DFI» allowfullscreen=»»/>
Что такое производственная линия?
Что такое производственная линия?НАЖМИТЕ ЗДЕСЬ ДЛЯ УКАЗАТЕЛЬНОЙ СТРАНИЦЫ
ЧТО ТАКОЕ ПРОИЗВОДСТВЕННАЯ ЛИНИЯ?
В. Райан 2009
ФАЙЛ PDF — НАЖМИТЕ ЗДЕСЬ ДЛЯ ПЕЧАТИ РАБОЧЕЙ ТАБЛИЦЫ | |
Многие продукты
изготовлены и собраны на производственной линии.Перед введением
Линии компьютерного управления и производства роботов обслуживались людьми.
Каждый человек будет выполнять ограниченное количество задач или даже одну
задача, и продукт будет передан по производственной линии
следующий человек. Это будет продолжаться до тех пор, пока продукт не будет полностью
собран.![]() Некоторые современные производственные линии все еще работают в том же в то время как другие полагаются на роботов и компьютерное управление или комбинацию люди и машины. | |
Пример производственной линии приведенное ниже было упрощено. Эта производственная линия предназначена для сборки велосипеда (см. выше). Когда рама велосипеда движется по производственная линия у каждого человека на рабочем месте есть определенная задача выполнить (см. ниже). | |
ПРЕИМУЩЕСТВА: Производственная линия
это очень эффективный способ изготовления и сборки продукта.![]() НЕДОСТАТКИ: Однако рабочие на производственных линиях часто жалуются этот небольшой навык или обучение требуется, чтобы завершить их индивидуальный задач и что работа на производственной линии чрезвычайно скучна и невыполнение.Работники часто считают свою задачу не очень важной, поскольку они просто производят одну маленькую часть большого продукта, состоящего из тысячи компонентов. | |
По приведенной ниже ссылке можно перейти к пятиминутному видео, показывающему, как производится Tesla Model S.
| |
НАЖМИТЕ ЗДЕСЬ, ЧТОБЫ СЛЕДУЕТ ПРОДУКЦИЯ СТРАНИЦА | |
НАЖМИТЕ ЗДЕСЬ, чтобы увидеть УКАЗАТЕЛЬ ДИЗАЙНА ПРОДУКЦИИ, СТРАНИЦА | |
Полное руководство по производственным линиям автомобилей
Сборочная линия — одно из величайших изобретений 20-го века. Часто упоминаемый в числе первых подрывных практик, он настолько потряс мир, что производители, не сумевшие к нему приспособиться, закрыли свой бизнес.
Сборочная линия была больше, чем просто изобретением, которое ускорило производственные процессы — это была идея, методология, направленная на повышение эффективности и производительности. Практически каждая отрасль быстро приняла и адаптировала ее в соответствии со своими потребностями, и она продолжает развиваться и процветать по сей день.
Сегодня наиболее широко используемый термин среди производителей — это бережливое производство — сборочная линия, на которой работает оптимально, без задержек и проблем, с минимальными отходами и максимальной производительностью. Сегодня эти объекты являются целью любого бизнеса, а не только производственного.
Первая часть этого руководства описывает сборочную линию от ее скромного начала и первых прототипов, главного прорыва Генри Форда, до вклада Toyota в сборочную линию и бережливое производство. Затем руководство переходит к современным тенденциям, их организационному аспекту, новым технологиям, интеграции ИИ и машинного обучения, а также другим разрушительным методам, которые штурмом захватывают мир.
Сегодня мы видим, что каждый бизнес принял организационные методы, используемые современными сборочными линиями.
Они применимы практически к любой существующей компании, и даже к нашей личной повседневной организации задач.
Для того, чтобы компания действительно преуспела в сегодняшнем быстро меняющемся мире, она должна работать безупречно — с минимальными отходами и максимальной эффективностью.
Вот как сборочные линии сделали это возможным.
История линий производства автомобилей Когда в разговоре упоминается термин «производство автомобилей», большинство людей сразу же думают о Генри Форде и его революционных сборочных линиях, но на самом деле все гораздо сложнее.Во-первых, сборочная линия была запатентована не Фордом, а другим гигантом автомобильной промышленности, которому приписывают создание современной автомобильной промышленности в том виде, в каком мы ее знаем, но не нарицательным.
В этой главе мы перечислим, как появились линии по производству автомобилей, какими мы их знаем, и как к ним привело постоянное стремление к эффективности и повышению качества продукции в различных отраслях. В этой главе будет рассмотрена их история, а важность разделения труда, взаимозаменяемые части и аналогичные концепции из других отраслей сыграли важную роль в их развитии.
Разделение труда
Эффективные и рентабельные линии по производству автомобилей также обязаны своим существованием древней социальной концепции: разделению труда. На протяжении всей истории концепция разделения труда изучалась, анализировалась и применялась во многих отраслях, начиная с Шумерской империи около 3000 г. до н. Э. В модели разделения труда каждый работник выполняет одну задачу, которая со временем становится его второй натурой. Конструкция отдельных частей единообразна, что способствует повышению эффективности и сокращению общих производственных затрат.
Ранние сторонники разделения труда, однако, также осознавали его подводные камни, наиболее значительными из которых являются снижение удовлетворенности работников в долгосрочной перспективе и меньшие возможности для продвижения по службе. Тем не менее, разделение труда не обязательно по способностям или навыкам, а с акцентом на одну задачу для каждого рабочего, нашло свое применение во всех отраслях, от судостроения до общего производства и производства автомобилей.
Теоретики разделения труда
Одним из первых теоретиков, взявшихся за концепцию разделения труда, был Платон , который постулировал в своей «Республике», что «неравенство человечества… воплощается в разделении труда.Греческий философ, как и многие теоретики, которые пойдут по его стопам, рекламировал бесчисленные преимущества разделения труда как на политическом, так и на экономическом уровне.
Например, ученый и философ 17-го века сэр Уильям Петти наблюдал, как разделение труда привело к повышению производительности голландских судостроительных верфей. Петти с радикальными идеями, которые предшествовали промышленной революции примерно на 100 лет, считается первым современным философом, который предположил, что разделение труда имеет многочисленные социальные преимущества. В своей книге «Политическая арифметика» Петти из первых рук изложил свои наблюдения о разделении труда в судостроительной отрасли. По словам Петти, изначально голландцы строили свои корабли по одному, что считалось долгим и кропотливым процессом. Петти заметил, что, когда труд был разделен таким образом, что определенные рабочие выполняли определенную задачу на каждом построенном корабле, процесс занимал меньше времени.
Десять лет спустя экономист Адам Смит расширил идеи Петти, продвигая идею о том, что разделение труда равносильно экономической зависимости страны.Его публикация 1776 года «Богатство народов» сегодня считается одной из самых влиятельных книг по экономической науке. Некоторые идеи Смита в то время считались радикальными и новаторскими, в том числе идея о том, что выбранный человеком вид работы вызван разделением труда и способствует ему. Он подчеркнул важность сочетания навыков с оборудованием для повышения производительности и экономического процветания.
Идеи Смита были квалифицированы и расширены более века спустя французским социологом Эмилем Дюркгеймом , автором книги 1893 года «Разделение труда в обществе».”
Благодаря вкладам первых ученых, таких как Дюркгейм, Петти и Смит, а также пионерам обрабатывающей промышленности в судостроительной отрасли, разделение труда стало самой эффективной производственной системой в мире.
Ранние концепции в других отраслях
В годы, предшествовавшие промышленной революции, общество действительно функционировало так же, как то, что предлагал Платон: будь то сапожники, строители или ткачи, один человек создавал единичный предмет на каждом этапе его пути.Источник «торговли», этот метод производства требовал значительных навыков, на освоение которых могли уйти годы. Кроме того, для овладения определенным ремеслом может потребоваться целая жизнь тренировок и практики. Сегодня ремесленное производство — это специализированная отрасль, стоимость которой многие производители считают непомерно высокой.
Самое раннее свидетельство использования производственной линии и массового производства сменных компонентов относится к 12 веку Китай . Многие государственные монополии страны заказывали и осуществляли массовое производство различных металлических компонентов.
Европа приняла массовое производство еще в 1104 году в водном городке Венеции, Италия. В том же году началось строительство крупнейшего промышленного комплекса на континенте: The Venetian Arsenal . Конгломерат оружейных складов и верфей, Арсенал в конечном итоге охватил 15 процентов Венеции по площади, в общей сложности 110 акров, и нанял более 16 000 рабочих. За столетия до того, как Генри Форд усовершенствовал движущуюся сборочную линию, Венецианский арсенал предложил такую возможность, но на каналах, а не на механических ремнях — детали производились массово и устанавливались на корабли, когда они плыли по каналу.На пике производства, в середине 1500-х годов, весь корабль можно было собрать за один день.
Промышленная революция
По мнению многих теоретиков, капитализм в том виде, в каком мы его знаем, родился в результате промышленной революции. Промышленная революция, обозначенная как период между 1760 и 1840 годами, привела к тому, что «инновационные» изобретения и достижения в производстве распространились со скоростью лесного пожара. Разделение труда было важным компонентом промышленной революции, способствуя прорыву в методах производства, в том числе в процессах сборочных конвейеров и погрузочно-разгрузочных работах, во множестве отраслей, требующих модернизации.
Наиболее важные концепции производственных линий во время промышленной революции
Поскольку мукомольная промышленность играла важную роль в поддержании питания населения, она была в авангарде механических и производственных инноваций во время промышленной революции. Многие эксперты считают, что современные методы обработки сыпучих материалов были созданы Оливером Эвансом, который автоматизировал мукомольную мельницу.
- Оливер Эванс и его автоматическая мукомольная мельница — Первый автоматизированный процесс сыпучих материалов.
- В 1700-х годах помол муки был трудоемким и длительным процессом с множеством этапов, включая измельчение и просеивание.
- Эванс, работая на заводе своей семьи в Ньюпорте, штат Делавэр, отметил, что весь процесс, помимо того, что он длительный, часто приводил к получению некачественного продукта.
- После открытия мельницы в 1785 году Эванс искал альтернативы.
- В отличие от большинства производителей того времени, мыслитель-новатор рассматривал производственный процесс как непрерывное целое.
- Он считается одним из первых, кто рассматривает производственный процесс как нечто большее, чем просто сумму его отдельных частей.
- На своей семейной мельнице Эванс использовал древнеримскую ленточную ковшовую систему вместе с брезентовыми конвейерами для транспортировки муки и автоматизации процесса.
- Его методы были приняты на ряде пивоваренных заводов и заводов как в колониальных США, так и в Великобритании.
- The Portsmouth Block Mills, Хэмпшир, Англия — Самый ранний промышленный пример непрерывного линейного процесса сборки.
- Построенный с 1801 по 1803 год, завод в основном производил детали для Королевского флота.
- Всего в Портсмуте было произведено 22 различных типа станков, которые оставались открытыми до 1960-х годов.
- Bridgewater Foundry, England — Современные фабрики по-прежнему устроены таким же образом.
- Литейный завод специализировался на производстве локомотивов и станков, и его здание было построено в линию с отдельными участками для погрузочно-разгрузочных работ и производства.
- Рабочие использовали краны для подъема тяжелых материалов и предметов, а железная дорога, соединенная напрямую с фабрикой, обеспечивала удобство транспортировки.
- Завод Leiston Works — Самая первая поточная сборочная линия.
- Еще до того, как возникла идея о личных автомобилях, транспортная отрасль была лидером в обрабатывающей промышленности.
- Первая поточная сборочная линия использовалась на заводе Leiston Works Factory, который строил портативные паровые двигатели, начиная с 1840-х годов: в 1852 году производство паровых двигателей началось в «Длинном цехе», названном из-за его формы.
- Машиностроение началось на одном конце длинного помещения, и детали были прикреплены по мере того, как он «продвигался» по комнате.
- Некоторые детали были построены на уровне балкона завода, а затем опущены на двигатель.
- К тому времени, как паровой двигатель прошел через всю комнату, он был готов.
В то время как промышленная революция принесла огромные изменения в обрабатывающую промышленность и произвела первые версии сборочной линии, это было еще не все. Взаимозаменяемые (или предварительно изготовленные) детали еще больше изменят производственную отрасль к лучшему.
Взаимозаменяемые детали: огромный прорыв
Мало кто может отрицать превосходное мастерство изготовления индивидуального изделия, будь то пара кожаных ботинок или привлекательный автомобиль. Однако изготовление на заказ — это трудоемкий процесс; тот, который может негативно повлиять на эффективность и прибыль компании. Благодаря использованию сменных деталей в производстве различных товаров, от оружия до автомобилей, массовое производство становится реальностью.Кроме того, заменить или отремонтировать предмет намного проще.
Система Грибоваля
Хотя использование сменных деталей в производстве является обычным явлением в современном мире, это был настоящий прорыв, который восходит к Франции 18 века. Оружие было первыми предметами массового производства со сменными частями, начиная с пушек и снарядов.
Французский инженер и офицер артиллерии генерал-лейтенант Жан-Батист Вакет де Грибоуаль приписывают содействие повсеместному внедрению стандартизированного оружия, называемого системой Грибоуаль.Система изменила процесс сверления при производстве пушек, используя стандартизированную систему сверления, которая позволила сделать стенки более тонкими и уменьшить общую длину без ущерба для дальности и точности.
Реализованная по королевскому приказу в 1765 году, тезка Грибоваля была продолжена его соотечественником и покровителем Оноре Бланом. Конструктор огнестрельного оружия считал, что систему Грибоваля можно использовать в производстве мушкетов. Хотя идея Бланка провалилась во Франции в то время, серийные ружья сыграли важную роль в обеспечении французских побед в наполеоновских войнах, которые велись с 1803 по 1815 годы.Ни Грибоваль, ни Блан, умершие в 1789 и 1801 годах соответственно, не дожили до того, чтобы их концепция стала широко распространенной реальностью в их родной стране.
Производство стандартного оружия Эли Уитни
По другую сторону Атлантики идеи Блана привлекли внимание тогдашнего посла во Франции Томаса Джефферсона. После нескольких лет прислушивания к предложениям Джефферсона относительно стандартизированного производства оружия новое правительство США одобрило испытание этой идеи.Сам президент Джордж Вашингтон наградил изобретателя Эли Уитни грантом на производство 12 000 предварительно изготовленных мушкетов.
Уитни, прославившаяся в 1794 году как изобретатель хлопкоочистительной машины, не смогла уложиться в срок, установленный Конгрессом. Они приказали Уитни явиться на сборку, на которой он успешно продемонстрировал, как взаимозаменяемые детали могут произвести революцию в оружейной промышленности. До широкого использования сменных частей сломанное огнестрельное оружие должно было ремонтироваться оружейным мастером на индивидуальной основе.Готовые детали упростили процесс ремонта оружия, навсегда изменив отрасль.
Рэнсом Эли Олдс: отец концепции сборочной линии
На рубеже 20-го века личные автомобили только начинали завоевывать мир, соединяя его таким образом, который раньше был невозможен. И прорывы в методах производства сборочных линий сыграли важную роль в этой игре. Несмотря на распространенное заблуждение, что Генри Форд был мозгом сборочной линии, на самом деле это был один из соперников Форда, который изобрел и запатентовал «инновационный» метод производства — Ransom Olds .
Olds Motor Vehicle Company — там, где все начиналось
Олдс, производитель автомобилей из Детройта, основал компанию, которая носит его имя по сей день, — Oldsmobile, — которой приписывают начало правления Детройта как автомобильной столицы мира. На момент основания в 1901 году компания Olds была известна как Olds Motor Vehicle Company. С самого начала завод Oldsmobile использовал конвейер в качестве основного средства производства.
Концепция сразу же имела успех: за первый год работы завода с конвейера сошло 425 автомобилей.В следующем, 1902 году, было произведено 2500 автомобилей Olds Motor Company.
Рэнсом сделал еще один шаг вперед в своем «инновационном» видении производства, внедрив модель массового производства, которая изменила производственный ландшафт как самого Детройта, так и автомобильной промышленности в целом. Как и первые производители оружия, первые производители автомобилей изначально создавали автомобили индивидуально, без стандартного шаблона. Таким образом, каждый автомобиль отличался от других. Французский Benz Velo был первым стандартизированным автомобилем: в течение 1894 года выпуска было выпущено 134 идентичных автомобиля.
Модель Oldsmobile Curved Dash 1901 года вошла в историю как первый серийный автомобиль в США . К 1904 году было продано около 5000 моделей Curved Dash.
Генри Форд усовершенствовал сборочную линию
Несмотря на успех, достигнутый Рэнсомом Олдсом и его одноименной компанией, именно Генри Форд оставил свое имя на протяжении всей истории как виртуальный отец автомобильной промышленности. Движущаяся сборочная линия Ford произвела революцию в автомобильном производстве и внесла свой вклад в улучшение условий труда в 20 веке.
Ford получил идею от пищевой промышленности
Идея движущейся сборочной линии родилась после посещения Фордом скотобойни Swift & Company в Чикаго. Это событие даже задокументировано в музее Генри Форда: находясь на мясокомбинате, Форд восхищался конвейерной системой компании, по которой мясо доставлялось рабочим. Впоследствии Форд спроектировал и построил аналогичную сборочную линию с движущимися платформами и приводными конвейерными лентами на своем заводе в Хайленд-Парке.На мясокомбинате Swift & Co Форд также воочию убедился в преимуществах разделения труда. Рабочим были поручены специализированные задания, что обеспечило высокую эффективность рабочих мест.
Первый автомобиль Moving Assembly Line: Ford Model T
После посещения бойни Форд собрал команду для разработки движущейся сборочной линии для автомобильной промышленности. Группа опытных специалистов, в том числе инструментальщик К. Гарольд Уиллис и начальник завода Питер Э.Мартин адаптировал концепцию девятого воплощения Ford Model T. После длительного периода проб и ошибок, 1 октября 1908 года, первая модель T, собранная за 93 минуты, сошла с конвейера в Детройте. До внедрения движущейся конвейерной ленты среднее время производства Ford Model T составляло около 12 часов.
Полная модель T состояла из более чем 3000 деталей, от шин до клапанов и бензобаков, все из которых стали единообразными, начиная с 1913 года.Быстрый и организованный производственный процесс был разбит на 84 этапа, при этом один рабочий выполнял одну и ту же задачу для каждого автомобиля. Рабочие сборочного конвейера были специально обучены, чтобы стать виртуальными экспертами в этой единственной конкретной задаче, выполняемой с трехминутными интервалами.
За счет сочетания взаимозаменяемых деталей, движущейся сборочной линии и особенно подготовленных рабочих время, необходимое для сборки транспортного средства, значительно сократилось. Меньшее количество рабочей силы привело к снижению общих производственных затрат, а экономия была передана клиентам Ford.При цене менее 300 долларов , что значительно меньше, чем в прошлом году 850 долларов (около 18 000 долларов в сегодняшней стоимости), Ford Model T принес в массы личные автомобили . Впервые средний класс в целом мог позволить себе качественный личный автомобиль.
Через год после запуска движущейся сборочной линии Ford значительно превзошел всех остальных автопроизводителей. В 1914 году с заводов Ford сошло чуть более 308 000 автомобилей. А к 1927 году во всем мире было продано более 15 миллионов автомобилей Ford модели T.
Условия труда улучшены благодаря производственным линиям
Несколько неожиданных, но желанных побочных эффектов движущейся сборочной линии были более безопасные фабрики, более короткая рабочая неделя и улучшенные условия труда. Поскольку у рабочих были унифицированные, статические задачи и назначенная должность, случаи блуждания рабочих по рабочему месту были исключены, что снизило уровень травм и при этом удерживало сотрудников на задании.
Повышенная заработная плата и гарантированная оплата
Ford также привнес человеческое сострадание в автомобильную промышленность.Хотя этот акт мог быть жестом доброй воли и щедрости, он также помог улучшить моральный дух сотрудников и снизить текучесть кадров. Улучшения условий труда Ford включали введение 5-долларового рабочего дня, «значительной для того времени заработной платы», с гарантированной оплатой. Повышение заработной платы сопровождалось и другими льготами: рабочим больше не разрешалось поднимать тяжести, наклоняться или останавливаться на работе, и никакой специальной подготовки не требовалось. Эти новые стандарты рабочего места означали, что больше людей могло работать, так как почти любой мог выполнять задачи.Иммигранты также имели право на работу.
Поскольку производство товаров было таким длительным специализированным процессом, первые производители искали способы сэкономить время и повысить эффективность. Без вклада вольнодумцев, таких как Эванс, Олдс и Форд, автомобильная промышленность была бы совсем другим зверьком. Вместо того, чтобы сидеть в тени своих предшественников, современные автомобильные компании смотрят в будущее, постоянно совершенствуя свои методы и привнося совершенно новую динамику в ландшафт автомобильных производственных линий.
С самого начала автомобилестроения движущиеся сборочные линии и их взаимозаменяемые части играли решающую роль. С момента своего появления они создавались, чтобы производить автомобили быстрее и эффективнее, чем ручной труд. Сам их дизайн остается отличительной чертой совместных усилий множества производителей, а не одной компании. Десятки компаний-производителей автомобилей работали вместе, чтобы усовершенствовать конвейер в том виде, в котором мы его знаем сегодня.
Сегодняшние сборочные линии далеки от своих первых аналогов. Те, которые используются сегодня на фабриках, отличаются оптимизированной технологией и систематическими методами, которые позволяют минимизировать отходы. Это увеличивает ценность транспортных средств без ущерба для удовлетворенности клиентов или производительности.
Этой эффективности современных сборочных линий можно в значительной степени отдать должное Japan и Toyota Industries , которые сыграли решающую роль в разработке технологии этой сборочной линии и улучшении производственных линий, которые используются до сих пор.Производственная система Toyota рассматривается многими инсайдерами отрасли как предшественник того, что сейчас известно как бережливого производства . Таким образом, и Toyota, и Япония признаны лидерами как в автомобилестроении, так и в производственной отрасли.
Обзор бережливого производства и производственной системы Toyota
Система производства Toyota , известная как TPS , представляет собой интегрированную социально-технологическую систему.Философия и практика управления TPS помогают организовать производство, логистику и взаимодействие с клиентами и поставщиками. TPS является предшественником более общего термина «бережливое производство». Основными задачами являются устранение чрезмерной нагрузки и несогласованности при минимизации отходов.
TPS стремится минимизировать или исключить восемь различных видов отходов. К ним относятся:
- Перепроизводство или крупные отходы
- Время в наличии или в ожидании
- Транспорт
- Обработка
- Наличие на складе
- Механизм
- Изготовление бракованной продукции
- Недостаточно загруженные рабочие
По самой своей конструкции TPS представляет собой основу для устранения отходов при сохранении всех ресурсов.Это эталон обрабатывающей промышленности, который сейчас копируется во всем мире, прежде всего под маркой бережливого производства.
Как Сакичи Тойода и автоматизированные ткацкие станки проложили путь к TPS
CC Public domain, через Wikimedia CommonsВ то время как кредит на бережливое производство может идти напрямую в Японию и TPS, кредит за TPS должен быть отдан его изобретателю, Sakichi Toyoda . Тойода родился в 1867 году и был основателем Toyota Industries.Даже после своей смерти в 1930 году Тойода остается известным как король изобретателей, на его имя было выдано 85 патентов. Последние, однако, были сделаны с помощью его родственников, в том числе собственных детей.
Интересно, что он был наиболее активен в области ткацких станков и добился большого прорыва в 1896 году, когда он сконструировал ткацкий станок, который автоматически прекращал работу в случае обрыва нити . В то время порванная нить представляла серьезную проблему качества в процессе ткачества.Рабочим приходилось постоянно контролировать ткацкие станки на предмет обрыва нитей. Если одна оборванная нить не будет вовремя поймана, это приведет к серьезному дефекту плетения, который повредит всю ткань.
Это был только первый метод, внедренный в производственную систему Toyota. Вот все методы, разработанные Toyota и используемые сегодня в бережливом производстве.
Тойода обнаружил и отремонтировал порванную нить, что положило начало процессу его изобретения системы, в которой машина или производственный процесс останавливался при обнаружении неисправности.Он хотел избавить машину от таких ошибок, для чего решил использовать комплексный подход под названием Jidouka. В переводе с японского это слово означает автоматизация. Тем не менее, Toyoda внесла небольшие изменения в свой написание, позволив перевести его как autonomation — автоматизация с человеческим участием .
Подход компании Toyoda «Пять причин»В своем изобретении TPS Тойода использовал то, что он назвал принципом из пяти почему , который является неотъемлемой частью TPS и является одной из его основ.Подход «пять причин» потребовал от Toyoda спросить «почему?» пять раз при возникновении проблемы с системой. Спросив пять «почему», он смог найти корень проблемы, а не просто устранить и устранить симптомы неисправности.
Ткацкий станок, ведущий на первую сборочную линиюОдно из величайших достижений Тойоды произошло в 1925 году, когда он изобрел ткацкий станок Model G . Ткацкий станок работал полностью сам по себе и вообще не требовал вмешательства человека или наблюдения.Операторам приходилось лишь изредка пополнять свои челноки пряжей для автоматического устройства смены челноков. Это был самый совершенный ткацкий станок в мире: он значительно улучшил качество и производство ткани. Благодаря его изобретению один неквалифицированный рабочий мог контролировать от 30 до 50 отдельных ткацких станков. Спрос на эти автоматизированные ткацкие станки резко вырос во всем мире, и Тойода построил свою первую сборочную линию в 1927 году, чтобы удовлетворить спрос на эти станки. Ткацкие станки автоматически перемещались от станции к станции на сборочных линиях, используемых для их создания.В 1929 году он продал патент на автоматический ткацкий станок британской компании Platt Brothers. Интересно, что продажа патента на ткацкий станок дала начальный капитал для развития автомобильной компании.
Подход JIT и основание Toyota Motor CompanyВскоре после продажи патента на свой автоматизированный ткацкий станок Тойода начал производство автомобилей в 1933 году как отдельное специализированное подразделение своего завода по производству автоматических ткацких станков Toyoda. Производство автомобилей на заводе возглавил сын Тойоды Киичиро.
К 1937 году подразделение по производству автомобилей официально отделило от подразделения компании по производству автоматизированных ткацких станков — Toyota Motor Company была официально основана .
Под руководством Киичиро Тойода она стала собственной независимой компанией. Киичиро хотел создать лучший автомобиль в мире. Самая первая его модель называлась Model A. Она имеет кузов Chrysler, раму и заднюю ось производства Ford, а также переднюю ось и двигатель производства Chevrolet.В то время TPS не походил ни на что прежде в мире.
К этому времени TPS включила еще одно теоретическое изобретение Сакичи Тойоды, концепцию автоматизации под названием Just-in-Time, или JIT. Эта концепция изначально возникла в результате инцидента, во время которого Киичиро опоздал на поезд, находясь в Англии. Поезд действительно ушел вовремя. Однако Киичиро опоздал на поезд на несколько секунд.
На основе этого, казалось бы, несущественного инцидента, Сакичи разработал концепцию, согласно которой материалы для TPS должны поступать на завод именно тогда, когда они необходимы, а не слишком рано или слишком поздно.Он представил и включил эту концепцию в TPS в 1936 году.
Тайити Оно: уменьшение размера лота и появление TPSХотя заслуга в создании TPS в значительной степени принадлежит Сакичи Тойода, его фактическое улучшение, если не фактическое рождение, следует приписать японскому промышленному инженеру и бизнесмену по имени Тайити Оно . Оно пришел в Toyota Motor Company в 1943 году, и ему сразу же было поручено возглавить цех механической обработки. В то время в этом магазине были станки, которыми управлял опытный мастер.
Под руководством Оно механический цех был преобразован в последовательность операций, в которой машины были расположены таким образом, чтобы каждый мастер отвечал за несколько станков. Это преобразование уменьшило размер лотов в магазине и позволило каждому мастеру возглавить от 5 до 10 отдельных машин.
Революция в организации производства от непрерывного производстваЕще одно изменение, приписываемое Оно, — это революция в производственной организации, которая включила в себя концепцию компании Toyoda JIT.Оно полностью реализовал эту концепцию вскоре после того, как возглавил цех механической обработки.
До его приезда фактическое производство, которое происходило в магазине, было спланировано заранее. Менеджеры и руководители должны были попытаться угадать или оценить, каким будет потребительский спрос, а затем на основе этой оценки определить, какой тип и сколько товаров производить. Затем программа производства была продвинута через производство в процессе, который был буквально известен как система выталкивания.Конечно, эта система была очень несовершенной, потому что не было реального способа предсказать, сколько и какие продукты клиенты действительно купят.
Прогнозы системы выталкивания часто были неверными, что приводило к тому, что в любой момент времени производилось слишком много или слишком мало продуктов.
Под руководством Оно было отказано от системы выталкивания в пользу отслеживания запасов и воспроизведения только того, что покупатели вытащили из запасов. Эта система называлась вытягивающей системой и была основана на той же системе, которая использовалась в то время в американских супермаркетах.
По сути, система записывала, что покупатели сняли с полок и купили. Товары, продаваемые в наибольших количествах и самыми быстрыми темпами, производились и пополнялись.
Оно полностью внедрило вытяжную систему в TPS в 1948 году.
Система КанбанСистема вытягивания давала ряд преимуществ для производства и TPS, но не без недостатков. А именно, не было возможности быстро передать информацию из супермаркета обратно на завод.На самых ранних этапах системы требовалось, чтобы кто-то записал названия продуктов и количество на листе бумаги, а затем отправил их на производственное предприятие.
Со временем бумага, на которой была записана информация, была заменена постоянными карточками с цветовой кодировкой и подробной информацией — система называется Канбан. Карты пошли по кругу. Когда покупатель снимал детали с полок супермаркета, сами карты возвращались в производство.Затем они прошли производство вместе с множеством других продуктов. В конечном итоге они снова оказались на полках супермаркетов с урезанными товарами и, таким образом, были готовы к следующему циклу.
Непрерывное совершенствованиеЭйдзи Тойода реализовал еще одну концепцию, называемую непрерывным совершенствованием, которая станет краеугольным камнем TPS. Он почерпнул эту идею из буклета Ford, который он получил и привез с собой после посещения завода Ford. В буклете изложена философия постоянного поощрения сотрудников к высказыванию своих идей по улучшению.
Вдохновленный этой идеей, Эйдзи представил TPS и Toyota Motor Company в 1950 году. Интересно, что Toyota поддержала эту идею, в то время как Ford в конце концов отказался от нее.
Линия стоп-сигнала и система освещения AndonЕще одна концепция, представленная в 1050, — остановка линии . В основе этой идеи лежал тот же принцип автоматизации, который представил и разработал Сакичи Тойода. По сути, он останавливал производство всякий раз, когда в системе обнаруживалась неисправность или дефект.
СамОно также применил эту систему на сборочных линиях. Он пошел еще дальше, настаивая на том, чтобы руководители спешили на помощь работнику, который обнаружил дефект или отклонение от нормы, но не смог отремонтировать или устранить его достаточно быстро в отведенное ему время. Хотя эта идея в значительной степени приписывается Toyota Motor Company и TPS, она не совсем чужда другим производителям автомобилей.
Генри Форд — концепция, аналогичная остановке линии на его собственном заводе еще в 1930 году.
Как и ожидалось, концепция изначально привела к значительному количеству остановок на конвейере и производстве. Сам процесс в то время не был достаточно стабильным, чтобы его можно было продолжать. Однако Со временем Оно улучшило систему, что позволило производственным линиям начать работать более эффективно и плавно.
Его усовершенствование произошло благодаря технологии под названием Andon light system . Эта система включала в себя загорание зеленого света, когда все было в порядке, желтого света, когда были обнаружены небольшие проблемы, и красного света, когда линия была немедленно остановлена на заводе.
Современные производственные линии автомобилей, которые используются сегодня, на самом деле не сильно отличаются от базовых систем Ford прошлых лет, если вы посмотрите на самые основы. Автомобили по-прежнему переходят от станции к станции и от рабочего к рабочему по устойчивой конвейерной линии. Все отдельные рабочие выполняют порученные им задачи на назначенных им станциях. Когда каждый рабочий завершает работу и каждая задача выполнена, с конвейера сходит новый автомобиль, готовый к работе и готовый к работе.
Последние изменения
Хотя основные процессы на конвейере более или менее одинаковы, это не означает, что они были невосприимчивы к последним инновациям.
- Стандартизация — Ключевое различие между сегодняшним днем и потом заключается в децентрализации производства : большинство деталей, используемых при производстве автомобилей, больше не производятся собственными силами. Они производятся другими поставщиками на других заводах в стране или по всему миру.Эти поставщики также используют свои собственные версии сборочных линий для производства автомобильных запчастей. Автопроизводители могут иметь собственные производственные мощности, на которых они производят собственные автомобильные детали. Производственные мощности расположены не в одном здании с автомобильным заводом. Они могут даже не находиться в том же городе, штате или стране, что и автомобильный завод. Концепция, лежащая в основе покупки или производства автомобильных запчастей на другом заводе по производству автомобилей, включает в себя стандартизацию. Стандартизация — это концепция, доведенная до совершенства компанией Ford с ее взаимозаменяемыми частями.
- Совместное использование платформы — Генри Форд говорил клиентам, продавая свой автомобиль Model T: « Вы можете иметь любой цвет, если он черный. ”На его сборочном конвейере в то время не было возможности производить автомобили любого другого цвета, кроме черного. Сегодня производители автомобилей производят автомобили самых разных цветов, марок и моделей. Благодаря инновациям, внедренным такими людьми, как Toyoda, Ohno и другими, стало гораздо больше свободы в производстве сборочных линий.Сама эта свобода основана на концепции , разделяющей платформу . Совместное использование платформы подразумевает, что автомобильная компания разрабатывает и создает автомобили для совместного использования деталей с другими марками и моделями автомобилей. Таким образом, они могут легко производить больше моделей.
- Робототехника — Сегодняшние сборочные линии обеспечивают механизацию деталей и инструментов. Во многих аспектах производством занимаются роботы, которые заняли место рабочих. На некоторых этапах сборочной линии работа выполняется за счет комбинации робота и человеческого труда .Роботы пригодились для производства автомобилей, потому что многие аспекты производства автомобилей на самом деле опасны и требуют больших физических затрат. Он включает в себя повторяющиеся движения, которые создают напряжение и стресс для человеческого тела. Роботы избавляют рабочих от этого риска. Они делают создание новых автомобилей на конвейере безопаснее и проще во многих отношениях.
- Заводской дизайн и чистота — Наконец, современные сборочные линии сегодня часто называют чистыми , светлыми и открытыми конструкциями.Это уже не те переполненные, грязные, жирные и небезопасные предприятия, какими они были на заре автомобилестроения.
Типы производственных линий
Сегодня производители автомобилей используют на своих заводах множество различных производственных линий. Тип, который используется на объекте, будет зависеть от фактических условий на заводе. Это также будет зависеть от того, какая производительность требуется на самом заводе.
I-линияСамая простая и простая сборочная линия — это I-line.Это прямая линия , которая представляет собой короткую и, в некоторых случаях, не автоматизирована. Он не имеет изгибов и обеспечивает легкий доступ как операторам, так и материалам.
Важно, чтобы линия сборки I-line была короткой; если он будет слишком длинным, это создаст препятствие, потому что переход от одной стороны I-образной линии к другой занимает слишком много времени.
Это также может увеличить отходы при надзоре за линией из-за больших расстояний ходьбы. Операторы могут контролировать только ограниченное количество процессов, которые включают как свой собственный, так и два смежных.
Линия UU-line — это тип сборочной линии, используемой сегодня в бережливом производстве. Это самый известный , который получил самые высокие оценки как лучший макет. Это лучшее решение для ручного производства. Однако даже эта линия может создать проблемы, если в U-образной форме находится более одного оператора. Фактически, операторы всегда должны находиться в пределах U-образной части линии, потому что материалы и инструменты поставляются извне.Для установки требуются различные лотки и направляющие для перемещения материалов по линии, которые катятся по линии роликами, находящимися под самой линией.
Для U-линии требуется отдельный оператор, который должен обрабатывать процессы пополнения для устройства. Основное преимущество U-line заключается в том, что все процессы находятся под рукой. Операторы могут контролировать не только свои собственные процессы, но и смежные с ними. Кроме того, они могут видеть процессы, происходящие по ту сторону U-образной линии.
U-образные линии используются, когда требуется работа с несколькими машинами. Рабочий может выполнять работу, выполняемую как в начале, так и в конце линии, благодаря тому, как линия настроена.
Его масштаб также можно отрегулировать, увеличивая или уменьшая масштаб. Руководители просто должны перемещать рабочих, чтобы увеличить или уменьшить масштабы операций на U-линии. Когда есть высокий спрос на производство, руководители могут назначить одного рабочего на каждую станцию. Когда производственные потребности низкие, на все станции может быть назначен один рабочий.
S-LineЭтот тип сборочной линии наиболее часто используется в автомобильной промышленности . Он создается с помощью нескольких I-линий, которые расположены таким образом, чтобы создать S-образную форму. При использовании на больших заводах он может легко быть длиннее мили. Благодаря такой форме логистические операции и транспортировка материалов не тратятся зря, и она намного легче вписывается в завод.
Линия LL-line — это последняя конструкция сборочной линии, используемая сегодня на заводах.L-линия обычно создается по необходимости, потому что на заводе просто не хватает места для другого типа производственной линии. Он похож по конструкции на I-line и представляет те же проблемы.
Машины ручной работы
Хотя это наиболее распространенные типы сборочных линий, которые сегодня встречаются на многих заводах по производству автомобилей, они не используются некоторыми избранными производителями автомобилей. А именно, Aston Martin и Ferrari предпочитают создавать свои автомобили вручную.
Каждый из автомобилей этих компаний изготавливается на заказ в соответствии с требованиями каждого клиента.Фактически, они даже изготовят индивидуальное сиденье водителя по точным размерам заказчика. При этом у компаний нет необходимости в сборочных линиях на своих производственных площадях.
Объединение потоков материалов в производстве
Вышеупомянутые схемы линий сегодня можно найти на множестве автомобильных заводов. Однако на других предприятиях можно встретить слияние производственных линий. В редких случаях производственные линии могут быть временно или навсегда разделены, особенно когда фабрика должна производить различную продукцию.
Основным преимуществом объединения вторичной производственной линии с основной является быстрое использование материалов . Фактически, владельцам фабрик часто не нужен склад для хранения лишних материалов, потому что они будут немедленно израсходованы во время производства.
Однако для того, чтобы эта установка работала, темп и спрос на вторичную линию должны соответствовать спросу и скорости первой. Когда обе линии идут в ногу друг с другом, инвентарь для отслеживания магазина отсутствует.
Три типа линий слияния, используемых сегодня на заводах, включают:
- Гребневая линия, которая включает в себя слияние всех второстепенных линий с одной стороны линии
- Линия корешка, которая включает линии сборки, идущие со всех сторон. Это также называется линией рыбьей кости
- Сложная линия , иногда называемая потоком создания ценности, которая включает в себя множество ветвей и сложных систем, объединяющих все типы линий в одну
Все три линии способствуют быстрому и стабильному использованию складских запасов, устраняя необходимость в дополнительном складе, что может сэкономить компании деньги.
Современное производство, окружающая среда и удовлетворенность работников
Промышленная революция привела к беспрецедентному росту производительности и производства по всему миру. Никогда прежде технологии, позволяющие заменять детали и сборочные линии, не были найдены где-либо еще.
Эта технология отвечает за удобство и богатство продуктов и услуг, которыми люди повсюду пользуются и которые в большинстве своем ежедневно воспринимают как должное.Более того, сегодняшнее глобальное процветание в значительной степени связано с изобретением, обслуживанием и постоянным совершенствованием производственных процессов.
Улучшения сборочной линии
Усовершенствования, обнаруженные на сборочных линиях сегодня, придают большее значение различным частям высокотехнологичных процессов, используемых сегодня на заводах. Сегодня производство осуществляется посредством так называемых параллельных процессов — множество параллельных операций, которые используются на заключительных этапах сборки.
Эти виды деятельности отмечены сложными коммуникациями, графиками производства и планами материальных потоков , все из которых основаны на компьютерных технологиях, которые также отслеживают системы и помогают снизить затраты на хранение и отслеживание запасов.
Современные сборочные линии также включают концепцию под названием Совместная разработка приложений или JAD . JAD объединяет людей, работающих в производственных сферах, с теми, кто работает в сфере информационных технологий или ИТ на одном производственном предприятии.Его основное преимущество заключается в значительном сокращении времени, необходимого для выполнения одного проекта.
Фактор окружающей среды
Более того, сегодня производственные линии работают не только на то, чтобы навести порядок в самой своей архитектуре. Они также работают значительно, чтобы улучшить среду , которая окружает объекты, в которых они расположены. Хорошим примером может служить завод Subaru, расположенный в Лафайете, штат Индиана. Этот завод перерабатывает 99,8% отходов производственной деятельности.
Кроме того, многие мировые компании, в том числе производители автомобилей, теперь поощряют своих поставщиков либо забрать, либо переработать свою собственную упаковку. Переработка или возврат упаковки сокращает расходы поставщика. Это также означает, что им придется покупать меньше упаковочных материалов. Многие обнаруживают, что даже нестандартные детали, которые в противном случае были бы выброшены, можно переработать и использовать для новых целей.
Человеческий фактор
В отрасли не секрет, что рабочим автозаводов часто бывает скучно на работе.Они выполняют одни и те же задачи изо дня в день, в конечном итоге теряя интерес к тому, что они делают. Когда они теряют интерес, они ставят под угрозу цель производства и качество продукции.
Чтобы избавиться от скуки рабочих, такие компании, как Toyota, теперь предоставляют рабочим возможности для физических упражнений и отдыха. Рабочие вместе тренируются во время перерывов и имеют возможность расслабиться и пообщаться во время смены.
Им также предоставлены усовершенствованные инновации, которые делают их работу проще и интереснее.Эти новые улучшения ускоряют темпы производства продукции и снятия автомобилей с конвейера. Им нравится работать с меньшим количеством материалов, что снимает не только их скуку, но и снижает физическое и умственное напряжение, которое может возникнуть в связи с их работой.
Такие компании, как Toyota, также заинтересованы в капитале компании. Они получают выгоду через участие в прибыли , бонусы и другие финансовые стимулы . Эти денежные льготы предназначены для увеличения объемов производства и обеспечения ежедневной занятости рабочих.Чем лучше они работают, тем больше увеличивают свою зарплату.
Хотя улучшение сборочных линий и производства, возможно, не было в первую очередь сосредоточено на человеческом опыте, владельцы компаний нашли уникальный стимул для того, чтобы их сотрудники были довольны во время работы.
Качество продукции, а также темпы производства в значительной степени зависят от того, насколько хорошо рабочие на фабрике действительно любят выполнять свою работу.
Когда им предоставляются стимулы, такие как финансовые бонусы, а также новые технологии для работы, сотрудники с большей вероятностью примут участие в проекте.Они также менее склонны рисковать своей работой и здоровьем в производственном цехе.
Доказано, что способность общаться, тренироваться и чувствовать связь с остальной производственной командой повышает моральный дух рабочих. С повышением морального духа улучшаются качество и скорость работы сборочных линий. Этот аспект улучшения сборочных линий имеет не меньшее значение, чем защита окружающей среды, сокращение затрат и создание автомобилей, готовых к работе в демонстрационных залах.
Производственная линия— CEOpedia | Управление онлайн
Производственная линия представляет собой комплекс машин, собранных вместе и управляемых таким образом, что они функционируют как единое целое.Это также команда, управляемая людьми, которые устанавливаются в соответствии с порядком операций, выполняемых в рамках технологического процесса. Количество позиций в производственной линии зависит от потребностей и технических характеристик продукта. Каждый произведенный продукт должен пройти указанный этап производственного процесса в течение определенного времени, а сотрудники должны выполнить все действия, возложенные на его / ее должность. Этот набор действий называется производственным циклом. Конечный результат производственной линии может быть результатом: обработки, погрузочно-разгрузочных работ, транспортировки, упаковки и т. Д.
В литературе также используются следующие термины:
- комплекс машин
- комплект машин
- комплексная машина
- интегрированная производственная система
- рабочее оборудование
Характеристики
Рисунок 1. Модель производственной линииПроизводственная линия имеет несколько характеристик:
- Машины пространственно расположены так, чтобы образовывать линии
- производство частично или полностью автоматизировано Система первичного управления
- объединяет и объединяет работу на линии
- интеграция автономных машин для погрузочно-разгрузочных работ и транспортировки на короткие расстояния
- использование защитных компонентов безопасности на всей линии
- использование контрольно-измерительных рабочих мест, проверяющих материалы, полуфабрикаты и готовую продукцию
Типы производственных линий
Строительство производственной линии зависит от количества выпускаемых деталей.Анализируя производственные процессы, можно выделить несколько основных видов производственной деятельности:
- единичное производство (например, строительство дома),
- мелкосерийное производство — произведено ремесленных изделий, мало аналогичных изделий
- массовое производство — большие серийные серии продукции
- непрерывное производство — например, переработка нефти, производство бумаги, стали и т. д.
Список литературы
Сборочная линия | промышленное строительство
Сборочная линия , производственная компоновка машин, оборудования и рабочих для непрерывного потока заготовок при массовом производстве.
Сборочный конвейер ToyotaРоботизированная сварка на сборочном конвейере автомобилей Toyota Motor Corporation, Япония.
Предоставлено Toyota Motor CorporationПодробнее по этой теме
История организации работы: Линия сборки
Хотя прототипы сборочной линии можно проследить до глубокой древности, истинного предка этой промышленной техники можно найти в…
Дизайн сборочной линии определяется путем анализа этапов, необходимых для производства каждого компонента продукта, а также конечного продукта. Все перемещения материала упрощены, без перекрестного потока, возврата или повторяющейся процедуры. Рабочие задания, количество машин и производительность программируются таким образом, чтобы все операции на линии были совместимы.
Сборочная линия для автомобилей начинается с голого шасси. Компоненты прикрепляются последовательно по мере движения растущего агрегата по конвейеру.Детали подбираются в узлы на линиях подачи, которые пересекают основную линию, чтобы доставить внешние и внутренние детали, двигатели и другие сборки. По мере движения единиц каждый рабочий на линии выполняет определенную задачу, и каждая деталь и инструмент доставляются к месту использования синхронно с линией. На конвейере одновременно находится несколько различных узлов, но сложная система планирования и контроля гарантирует, что соответствующий тип и цвет кузова, отделка, двигатель и дополнительное оборудование прибудут вместе для создания желаемых комбинаций.
Автоматизированные сборочные линии полностью состоят из машин, управляемых машинами, без или почти без человеческого надзора. В таких непрерывных отраслях промышленности, как нефтепереработка и химическое производство, а также на многих современных заводах по производству автомобильных двигателей, сборочные линии полностью механизированы и почти полностью состоят из автоматического саморегулирующегося оборудования.
Получите подписку Britannica Premium и получите доступ к эксклюзивному контенту. Подпишитесь сейчасОднако многие изделия по-прежнему собираются вручную, потому что многие компоненты не могут быть легко обработаны машинами.Дорогие и в некоторой степени негибкие, автоматические сборочные машины экономичны только в том случае, если они обеспечивают высокую производительность. Однако развитие универсального оборудования и более широкое использование промышленных роботов повысили эффективность полностью автоматизированных сборочных операций.
Определение сборочной линии
Что такое сборочная линия?
Сборочная линия — это производственный процесс, который разбивает производство товара на этапы, которые выполняются в заранее определенной последовательности.Сборочные линии — наиболее часто используемый метод массового производства продукции. Они снижают затраты на рабочую силу, поскольку неквалифицированные рабочие обучаются выполнять определенные задачи. Вместо того, чтобы нанимать квалифицированного мастера для сборки целого предмета мебели или двигателя автомобиля, компании нанимают рабочих только для того, чтобы добавить ножку к табурету или болт к машине.
Ключевые выводы:
- Сборочная линия — это производственный процесс, при котором производство товара представляет собой последовательность шагов, выполняемых в заранее определенной последовательности.
- Сборочные линии — это наиболее часто используемый метод массового производства.
- Сборочные линии сокращают затраты на рабочую силу, поскольку неквалифицированные рабочие обучаются выполнять конкретные задачи, а не собирать целую единицу продукции.
Общие сведения о сборочных линиях
Сборочная линия — это место, где полуфабрикаты перемещаются с рабочего места на рабочее место. Детали добавляются последовательно, пока не будет произведена окончательная сборка. Сегодня автоматизированные сборочные линии работают на машинах с минимальным контролем со стороны человека.
Введение сборочной линии коренным образом изменило способ производства товаров. Кредит Генри Форду, который в 1908 году организовал сборочную линию для производства своих автомобилей Model T. Раньше рабочие собирали продукт (или большую его часть) на месте, часто один работник выполнял все задачи, связанные с созданием продукта.
На сборочных линиях, с другой стороны, рабочие (или машины) выполняют конкретную задачу по продукту, пока он идет по производственной линии, а не выполняют ряд задач.Это увеличивает эффективность за счет максимизации количества, которое рабочий может произвести по сравнению с затратами на рабочую силу.
Определение того, какие отдельные задачи должны быть выполнены, когда они должны быть выполнены и кто будет их выполнять, является решающим шагом в создании эффективной сборочной линии. Сложные изделия, такие как автомобили, необходимо разбивать на компоненты, которые машины и рабочие могут быстро собрать.
Компании используют подход «проектирование для сборки» (DFA) для анализа продукта и его конструкции с целью определения порядка сборки и выявления проблем, которые могут повлиять на выполнение каждой задачи.Затем каждая задача классифицируется как ручная, роботизированная или автоматическая, а затем назначается отдельным станциям в цехе производственного предприятия.
Особенности сборочных линий
Компании также могут проектировать продукты с учетом их сборки, что называется параллельным проектированием. Это позволяет компании производить новый продукт, который был разработан с учетом массового производства, с заранее определенными задачами, порядком задач и компоновкой сборочной линии.Это может значительно сократить время между выпуском первоначального дизайна продукта и выпуском конечного продукта.
Современные сборочные линии сочетают цифровые технологии с человеческим вкладом.