Технологический процесс производства газобетонных блоков — статьи завода «ЭКО», в Москве
06.02.2018
Производство блоков газобетона раньше было доступно только крупным компаниям. С появлением новых технологий этот процесс значительно упростился, поэтому сегодня этот строительный материал производят и небольшие фирмы.
Основные виды применяемого оборудования — полуавтоматические линии (производительность обычно не превышает 2,9 м³ в смену) и более сложные полностью автоматизированные производственные линии (производительность достигает 1200 м³ в день).
Технология подразумевает работу в несколько этапов:
- подготовка (монтаж и смазка) форм и бетонной смеси;
- заполнение емкостей и вызревание готовой смеси;
- нарезка сырого бетона;
- твердение в автоклавах;
- упаковка продукции.
Подготовительный этап
Газобетонные блоки отличаются от прочих видов продукции своей ячеистой структурой. Пузырьки газа занимают в материале до 85% общего объема, благодаря чему обеспечивается легкость продуктов. Компоненты для состава размешивают в газобетоносмесителе в течение примерно 4-5 минут, затем добавляют алюминиевую пудру, вступающую в химическую реакцию с известью. Продукт этой реакции — водород. Именно он образует в готовой массе пузырьки, равномерно пронизывающие ее.
Заполнение форм и нарезка
После добавления алюминиевой пудры раствор переливают в металлические емкости — вспучивание происходит в них. Для ускорения процесса состав на этой стадии подвергают вибрационным нагрузкам — это позволяет бетону быстрее схватиться и затвердеть. По достижении стадии созревания излишки материала обрезают с помощью проволочных струн — это необходимо для устранения неровностей. Оставшуюся массу нарезают на блоки равного размера.
Автоклавная обработка
Прогревание — важнейший производственный этап. Он позволяет значительно улучшить свойства. Сформированные и заранее нарезанный на блоки газобетон помещают в камеры автоклава, где они подвергаются воздействию насыщенного пара и повышенного давления. Температура в камерах достигает 190°С.
В некоторых случаях бетон производится неавтоклавным методом — затвердевание происходит естественным путем. Однако получаемый таким образом бетон менее прочен. Автоклавный бетон считается более надежным материалом и применяется чаще. Блоки из газобетона, произведенные автоклавным методом, отличает более однородная структура, лучшие показатели звуко- и теплоизоляции. В российских климатических условиях с применением этого материала можно возводить однорядные стены без дополнительного утепления. Кроме того, ячеистый бетон может использоваться в многоэтажном строительстве домов в качестве заполнителя.
Упаковка
На финишном этапе готовая продукция пакуется в термоусадочную пленку, затем блоки транспортируют к месту назначения на специальных деревянных поддонах.
youtube.com/embed/RsR7RXSjTBs»>Технология производства газобетонных блоков | Полезная информация о газобетоне завода ДСК Грас
В 60-х годах прошлого века, когда развивалось производство автоклавных бетонов, существовали разные способы их изготовления. Одни из них подразумевали использование цементных, другие — известковых, третьи — смешанных вяжущих составов. В те годы был распространён термин «газосиликатный бетон», который применяется и в наши дни — но уже ошибочно: силикатные ячеистые бетоны ушли в прошлое как класс. Промышленность XXI века не выпускает чистых газосиликатов — сегодня распространены более долговечные бетоны на цементном и смешанном вяжущем составе. Поэтому те, кто в наши дни говорят «газосиликат», в большинстве случаев имеют в виду автоклавный ячеистый газобетон.
За последние 15 лет среднегодовой ввод жилья в России вырос в 2,5 раза. Выпуск автоклавного газобетона за этот же период увеличилось в 12 раз. Он стал самым массовым материалом для возведения стен, применяемым в строительстве.
В последние годы растёт популярность газобетонных блоков — в частности, марок низких плотностей, например, D350. Стоит отметить, что сегодня в России ежегодно выпускается более 1,5 млн м3 блоков низких плотностей. Всё чаще звучит вопрос: как производится этот материал? Развёрнутый ответ на него — в этой статье.
Подготовка сырья
Для изготовления блоков из ячеистого бетона используется смесь цемента, гипса, песка, извести и воды. В неё в небольших объёмах добавляется алюминиевая паста. За точное дозирование всех компонентов отвечает автоматизированная установка.
Формование
Из миксера сырьё поступает в формы большого объёма. Здесь смесь находится несколько часов при температуре, составляющей приблизительно 50º С. Идёт реакция, и массив поднимается, напоминая дрожжевое тесто. Возникает огромное количество ячеек (пор), которые и дают стройматериалу его название. После того, как массив приобрёл требуемый объём, нужно еще некоторое время, чтобы он предварительно отвердел. Далее он кантуется на 90º и в вертикальном положении помещается на поддон для автоклава. Здесь массив остаётся в ходе резки, обработки в автоклаве и разделения.
По окончании процесса смесь подаётся на участок резки.
Резка на блоки
На очередной стадии массив, сохраняя вертикальное положение, движется по участку резки. Здесь с применением ножей и струн он режется по заранее заданным размерам.
Интересный факт
Отходы материала, образующиеся при резке, вновь поступают в производство. Технологический процесс выпуска ячеистого бетона, таким образом, становится безотходным.
Обработка в автоклаве
Нарезанные блоки помещаются в автоклав — камеру с температурой 180-190ºС, давлением около 12 бар и насыщенным паром. Здесь будущий стройматериал выдерживается в течение 12 часов. За это время в блоках формируется кристаллическая структура, выгодно отличающая автоклавный газобетон от других материалов и придающая ему достойные практические свойства.
После обработки в автоклаве готовый стройматериал с применением крана-делителя выкладывается для остывания.
Упаковывание
На последнем этапе блоки из ячеистого бетона — например, марки D300 — аккуратно запаковываются в перфорированную термоусадочную пленку с помощью автоматического оборудования.
Упакованные газобетонные блоки транспортируются на склад с помощью вилочных погрузчиков. С этого момента они готовы к реализации.
Отличительные особенности применяемого оборудования
Для производства автоклавного ячеистого газобетона на нашем заводе применяется оборудование марки HESS AAC Systems B.V., отвечающее самым строгим международным стандартам.
Система подачи сыпучих материалов. В ней используется запатентованная технология Lahti Precision, реализованная только в линиях HESS, в основе которой — псевдоожижение (флюидизация) материалов. Система разгружает силоса и дозирует подачу сыпучих материалов в псевдоожиженном состоянии, создаваемом с помощью воздуха. Шнеки и другие механические части не используются, поэтому нет необходимости чистить и заменять детали. Самое важное — то, что система позволяет дозировать сыпучие материалы с точность до 100 грамм. Это даёт возможность максимально точно и гибко адаптировать рецептуру.
Устройство кантования массива. Массив перед резкой кантуется в форме в вертикальное положение, после чего корпус формы удаляется. Массив не подвергается механическому захвату манипулятором, что положительно влияет на качество конечного продукта. Предотвращается появление трещин, исключается деформация массива, сохраняются прочностные и геометрические характеристики блоков.
Устройство вертикальной, предварительной и окончательной боковой резки. Обрезает материал по трём измерениям, позволяет регулировать толщину снимаемого слоя или выравнивать поверхность массива после предварительной резки. Линия оснащена системой, следящей за обрывом струн. Обрезки массива отбрасываются в шлам-канал, промываемый водой. Отсюда они поступают в ёмкость с размалывающим устройством и мешалкой, расположенную под линией резки. Из ёмкости шлам транспортируется в шламбассейн для дальнейшего использования. Такое решение даёт экономию сырья и служит частью концепции «Безотходное производство».
Система разделения массива. В ней реализована уникальная технология разделения «зелёного» массива, позволяющая расслаивать его непосредственно после резки — до автоклавирования. Массив подается в автоклав разделённым на слои. Благодаря этому пропаривание выполняется максимально равномерно и качественно, и газобетон приобретает предельно возможную прочность. В отличие от традиционных технологий, подразумевающих резку вертикально стоящего массива и разделение «белого» продукта, слипания слоёв при пропаривании не происходит. Поэтому не требуется и дополнительного разделения блоков после автоклавирования. Благодаря этому сохраняется привлекательный вид блоков, исключается появление сколов, отверстий и трещин, обеспечивается идеальная геометрия конечного продукта.
ПАЗОБЕТОН И ЕГО СВОЙСТВА
🕑 Время чтения: 1 минута
Газобетон изготавливается путем введения воздуха или газа в суспензию, состоящую из портландцемента или извести и мелкоизмельченного кремнистого наполнителя, так что, когда смесь схватывается и затвердевает, образуется однородная формируется клеточная структура. Хотя он и называется газобетоном, на самом деле это не бетон в правильном смысле этого слова. Как описано выше, это смесь воды, цемента и мелкоизмельченного песка. Газобетон также называют газобетоном, пенобетоном, ячеистым бетоном. В Индии в настоящее время у нас есть несколько заводов по производству газобетона.
Распространенным продуктом из ячеистого бетона в Индии является Siporex.
Производство газобетонаСуществует несколько способов производства газобетона.
(a) Путем образования газа в результате химической реакции внутри массы в жидком или пластическом состоянии.
(b) Путем смешивания предварительно сформированной стабильной пены с суспензией.
(c) Путем использования тонкоизмельченного металла (обычно алюминиевого порошка) с суспензией, который вступает в реакцию с гидроксидом кальция, выделяющимся в процессе гидратации, с выделением большого количества газообразного водорода. Этот газообразный водород, когда он содержится в смеси шлама, дает ячеистую структуру.
Вместо алюминиевой пудры можно добавлять цинковый порошок. Вместо металлического порошка также использовались перекись водорода и хлорная известь. Но в настоящее время эта практика не получила широкого распространения.
При втором способе предварительно сформированная стабильная пена смешивается с цементом и дробленым песчаным раствором, что создает ячеистую структуру, когда она схватывается и затвердевает. В качестве незначительной модификации некоторые пенообразователи также смешивают и тщательно взбивают или взбивают (так же, как при приготовлении пены с яичным белком) для получения эффекта пены в бетоне. Аналогичным образом можно использовать большое количество воздухововлекающих добавок и тщательно смешивать их для придания ячеистой аэрируемой структуре бетона. Однако этот метод не может быть использован для снижения плотности бетона сверх определенной точки, и поэтому использование воздухововлечения для изготовления газобетона не часто практикуется.
Метод газификации является одним из наиболее широко распространенных методов с использованием алюминиевого порошка или другого подобного материала. Этот метод применяется при крупносерийном производстве ячеистого бетона на заводе, где весь процесс механизирован, а изделие подвергается обработке паром под высоким давлением, т. е., другими словами, изделия обрабатываются в автоклаве. Такие продукты не будут страдать ни снижением прочности, ни нестабильностью размеров.
Практика использования предварительно сформованной пены с суспензией ограничивается мелкосерийным производством и работами на месте, где допускается небольшое изменение размерной стабильности. Но преимущество в том, что этим методом можно добиться любой желаемой плотности на месте.
Свойства газобетона Использование пенобетона приобрело популярность не только из-за низкой плотности, но и из-за других свойств, в первую очередь теплоизоляционных свойств. Газобетон производится в диапазоне плотности от 300 кг/м3 до примерно 800 кг/м3. Марки с более низкой плотностью используются для целей изоляции, в то время как марки со средней плотностью используются для изготовления строительных блоков или несущих стен, а марки со сравнительно более высокой плотностью используются в производстве сборных элементов конструкции в сочетании со стальной арматурой.
Линия по производству автоклавных газобетонных блоков от китайского производителя
Подготовка сырья → Цемент → Известь → Гипс → Добавка → Песок → Дозирование сырья → Смешивание и заливка → Используется для добавления стальных стержней в газобетонные плиты (опционально) → Предварительно отверждение → Поворотный кран переворачивает форму и начинает извлекать форму → Подготовка тележки для резки → Машина для резки разрезает формованный материал по горизонтали и вертикали → удаляется нижняя часть формованного материала → Сгруппируйте тележку для отверждения и отправьте полуфабрикаты в автоклавы → Выдерживание → Выгрузка готовых блоков из автоклавов → Кубирование → Упаковка под погрузку → Транспортировка готовой продукции →
1. Обработка сырья
Линия по производству газобетонных блоков должна измельчать кремнеземистые материалы, такие как песок, летучая зола и т. д. В зависимости от сырья и характеристик процесса процесс измельчения можно разделить на: сухое измельчение в порошок, мокрое измельчение с водой в суспензию и смешанное измельчение с известью.
Процесс подготовки сырья — это процесс подготовки ингредиента, который должен соответствовать технологическим требованиям, а обработка сырья и процесс хранения перед завершением ингредиентов для всего производства могут выполняться плавно, качество продукта может соответствовать требованиям большинство основных аспектов процесса имеют непосредственное влияние.
Для получения материала, соответствующего технологическим требованиям газобетонных блоков, в основном известняковые и кремнистые материалы необходимо измельчать. Перед входом в мельницу некоторые сыпучие материалы должны быть сначала измельчены, чтобы достичь размера подачи, необходимого для входа во вторичный помол шаровой мельницы.
а. Принцип работы
Во время работы двигатель через ременный привод приводит во вращение эксцентриковый вал, так что подвижная челюсть периодически закрывается и покидает неподвижную челюсть, и, таким образом, материалы сжимаются, растираются, измельчаются, так что материалы становятся меньше, постепенно падают от разгрузочного порта.
Дробилка имеет такие характеристики, как: большой коэффициент дробления, высокая производительность, однородный размер частиц, простая конструкция, надежная работа, простота обслуживания, экономичность и т. д.
г. Основные технические характеристики
Модель | Максимальный диаметр загружаемого материала (мм) | Размер разгрузки (см) 9 0074 | Производительность (т/ч) | Мощность ( кВт) | Вес (т) | Размеры основной рамы (Д×Ш×В) (мм) |
PEX-150×750 | 125 | 10-40 | 10-40 | 15 | 3,5 | 9 0002 1430×1635×1108 |
PEX-250×750 | 210 | 25-60 | 15-30 | 22 | 4,5 | 1667×1545×1020 |
PEX-250×1000 | 210 | 25-60 | 20-52 | 30-37 | 6,5 9000 3 | 1580×1964×1380 |
PEX-250×1200 | 210 | 25-60 | 25-60 | 37 | 7,7 90 003 | 1580×2164×1430 |
PEX-300×1300 | 250 | 20-80 | 30-90 | 55 | 9 0002 11 | 1750×2320×1730 |
(2)ковшовый элеватор
Ковшовый элеватор является незаменимым оборудованием на линии по производству газобетона.
а. Принцип работы
Ковшовый элеватор NE состоит из рабочих частей (ковша и тягового ремня), верхней части с передающим барабаном, нижней части с натяжным роликом, среднего корпуса, исполнительного устройства, тормозного устройства и т. д. Он используется для транспортировки порошка с сыпучей плотностью. материал (ρ < 1,5 т / м³), твердые частицы или блоки, такие как уголь, песок, ветер, цемент и битая руда и т. д.
б. Основные характеристики
NE Ковшовый элеватор использует проточный способ подачи. Материал будет транспортироваться наверх по цепи Plate-Link, а затем выгружаться под действием силы тяжести. Наши лифты мультистандартны, имеют высокую производительность и низкое энергопотребление. Он спроектирован как полностью закрытый с медленно работающей цепью, что позволяет избежать возврата материала, поэтому мощность не тратится впустую.

г. Основные технические характеристики
Модель | Производительность конвейера (м³/ч) | Скорость подъема (м/с) ) | Частота вращения главного вала (об/мин) | Диаметр материала (мм) | Hoperp | ||
Объем (л) | Ширина (мм) | Расстояние (мм) | |||||
NE15 | 15 | 0,5 | 15,54 | <40 | 2,5 | 250 | 203 |
NE30 | 30 | 0,5 | 16,45 | <50 | 900 02 7,8 | 300 | 305 |
(3) Ленточный конвейер , песок, известь и другое сырье, является наиболее эффективное конвейерное оборудование непрерывного действия, конвейерная лента движется по принципу фрикционного привода. Отличается большой производительностью, длинной трансмиссией, плавной транспортировкой, отсутствием относительного движения материалов и конвейера, меньшим уровнем шума, простой конструкцией, простотой обслуживания, меньшим потреблением энергии и стандартизированными компонентами.
а. Основные технические данные ленточного конвейера
Ширина ленты (мм) | Длина (м) Мощность (кВт) | Скорость (м/с) | Производительность (т/ч) | ||
500 | ≤12 / 3 | 12-20 / 4-5,5 | 9 00710,8-1,0 | 50- 191 | |
650 | ≤12 / 4 | 12-20 / 5,5 | 9 00710,8-1,60 | 80-250 |
(4)Шаровая мельница
Измельчение сырья является важным этапом производства газобетонных блоков. Известь, гипс, песок, шлак и другие материалы могут быть полностью перемешаны и взаимодействовать только после порошкового измельчения, после чего изделия получаются прочностными. Шаровая мельница является ключевым оборудованием для измельчения материала.
Шаровая мельница представляет собой горизонтальное цилиндрическое вращающееся устройство, внешнее зубчатое колесо, две кабины, шаровую мельницу решетчатого типа. Сырье равномерно подается в первую кабину через шнековый полый вал. В первой кабине есть вкладыш лестницы или гофрированный вкладыш, а также стальной шарик разного размера. Когда шаровая мельница работает, кабина создает центробежную силу и поднимает шар на определенную высоту, падает, толкает и измельчает материалы. После грубого помола в первой камере сырье через однокамерную тарелку поступает во вторую камеру. Во второй кабине есть плоская футеровка и стальной шар, и отец будет измельчать сырье. Наконец, порошок будет выгружен через разгрузочную решетку для завершения операции измельчения.
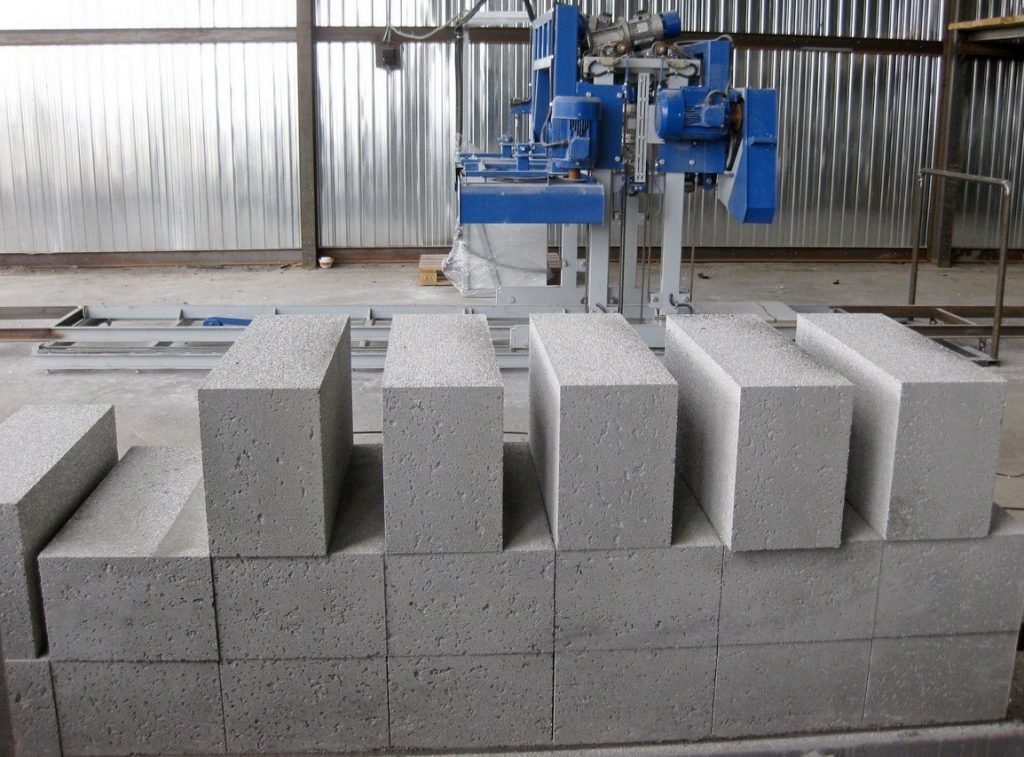
б. Основные характеристики
Машина состоит из подающей части, разгрузочной части, поворотной части и приводной части (редуктор, малая трансмиссия, двигатели, электрическое управление) и других основных компонентов. В этой машине используется внешняя шестерня, опора полого вала. Полый вал выполнен из стального литья, съемная гильза, токарная обработка зубчатого колеса выполнена с использованием литья под давлением, износостойкие гильзы встроены в цилиндр (есть два вида гильз: резиновая гильза и стальная гильза, резиновая гильза легкая, малошумная, износостойкая, хорошая уплотнение, как правило, предпочтительнее.) Эта машина имеет хорошую износостойкость, а также плавный и надежный ход.
г. Основные технические характеристики шаровой шлифовальной машины
Модель | Φ1,5×5,7 | Φ1,83×7 900 03 | Φ2,2×7 | Φ2,4×8 |
Производительность (т/ч) | 3,5-4 | 8-12 | 90 002 15-17 | 19-22 |
Максимальный диаметр Подача материала (мм) | ≤25 | ≤25 | ≤25 | ≤25 9007 4 |
Загрузка (Т) | 11 | 21 | 30 | 40 |
Мощность (кВт) | 130 | 245 900 03 | 380 | 475 |
Вес (т) | 23 | 36 | 49 | 9 0071
(5) Смесительный бак для отходов (перед шаровой мельницей)
Смесительный бак для отходов состоит из крепежной платформы, лестницы, ограждения, смесителя и бака. Обычно отработанный навоз из перегонной тележки и все другие отработанные материалы следует смешивать с водой в резервуаре. Смешанный материал будет переработан вместе с исходным навозом.
(6) Силос для извести, цемента
Силос используется для хранения материалов, с воздушной подушкой или вибрационным двигателем; по объему технические характеристики: 100м³, 200м³, 300м³. Их можно настроить в соответствии с требованиями выбранных линий.
2. Дозирование и розлив
Дозирование – это оборудование, которое взвешивает готовые дозирующие материалы и все сырье, регулирует температуру, концентрацию и добавляет материал, а затем, в соответствии с требованиями процесса, подает материал в смеситель при один раз. Дозирование является ключевым звеном процесса газобетона, связанного с сырьем, между процентным содержанием активных ингредиентов, относительно текучести и вязкости раствора, подходит ли алюминиевый порошок для нормального твердения газа и сырого тела.
Процесс заливки – это уникальный процесс производства газобетона, который отличается от других видов бетона. Процесс заливки — это процесс дозирования после измерения и необходимой регулировки, помещаемой в смеситель для смешивания материалов, предназначенных для обработки оговоренного времени, температуры, плотности суспензии, через заливное отверстие смесителя, заливаемого в форму. Суспензия вступает в ряд физических и химических реакций в форме и образует пузыри, а пузырьки делают суспензию надутой, загущенной и затвердевшей. Процесс заливки является важным процессом для воздействия на структуру пор; процесс дозирования и процесс заливки составляют основную часть производственного процесса газобетонных блоков.
Процесс предварительного отверждения — это в основном процесс после заливки суспензии для дальнейшего сгущения и затвердевания.
(1)Система взвешивания
Сырье для газобетона имеет следующие физические состояния: жидкое, жидкое, порошкообразное, алюминиевый порошок и кусковой алюминий. Различные материалы имеют разные весы, такие как весы для извести, бункер для взвешивания цемента, резервуар для взвешивания шлама и т. Д. Материал будет точно измерен автоматической измерительной системой.
а. Бункер для взвешивания извести и цемента
Используется для взвешивания цемента и извести, а затем подачи их в заливочный смеситель.
Объем | Годовая производительность |
1,2 м³ | 900 71|
2.0м³ | ﹥150000м³ |
б. Емкость для взвешивания навозной жижи
Используется для взвешивания суспензии, а затем помещается в смеситель для заливки.
Объем | Годовая производительность |
2,5 м³ | 900 71|
4,5 м³ | ≤150000 м³ |
в. Измерительный бак для воды
Измерение воды и автоматическая подача воды в смеситель для навозной жижи.
Диапазон измерения | Годовая производительность |
250 кг | ≤150000м ³ |
500 кг | ﹥150000 м³ |
(2) алюминиевый порошок Смеситель
Состоит из цилиндра, кронштейна и пневматической дроссельной заслонки (устройство двойного вывода сигнала). Он используется для смешивания алюминиевой пудры.
(3) Заливочный смеситель
Заливочный смеситель состоит из смесительного барабана, смесительного вала, трансмиссионного механизма, отводного устройства, соплового устройства и т. д., что является основным оборудованием газобетонного завода. Смеситель для заливки используется для смешивания цементного раствора, цемента, извести, гипса и алюминиевого порошка в определенной пропорции, после равномерного и полного смешивания смеси, а затем своевременно заливает смешанный раствор в раму формы.
Модель | Диаметр барабана (мм) | Диаметр лопасти (мм) | Скорость перемешивания (об/мин) | Мощность (k Вт) | Годовая производительность (м³/год) |
4,2 м | 1700 | 570 | 566 | 37 | ≤150000 |
4,8 м | 1900 | 600 | 590 | 37 9007 4 | 200000-250000 |
6м | 2000 | 640 | 650 | 45 | 300000 |
(4) Переливочная тележка
Po Паромная тележка является основным оборудованием автоклавной секции линии по производству газобетонных блоков, предназначенной для перетаскивания. Он состоит из рамы тележки, привода и механизма позиционирования. Рама тележки сварена из профильной стали. Привод состоит из редуктора, муфты, вала, ведущего колеса и ведомого колеса. Паромная тележка имеет характеристики сильной силы при перетаскивании, толкании и остановке. при быстром перемещении он может точно позиционироваться и подключаться, а также может работать с низкой частотой при полной загрузке, а также может работать с высокой частотой при пустой загрузке.
Технические характеристики паровоза (м) | Загрузка (т) | Скорость/частота ходьбы (м/мин) | 9 0071Мощность (кВт) | Годовая мощность (м³/год) | |||||||||||||||||||||||||||||||||||||||||||||||||||||||||||||||||||||||||||||||||||||||||||||||||||||||||||||||||||||||||||||||||||||||||||
4,2 | 6 | 9000 2 0 ~20 | 3620 | 7,5 | ≤150000 | ||||||||||||||||||||||||||||||||||||||||||||||||||||||||||||||||||||||||||||||||||||||||||||||||||||||||||||||||||||||||||||||||||||||||||
4,8 | 8 | 4220 9 0074 | 9 | 20-250000 | |||||||||||||||||||||||||||||||||||||||||||||||||||||||||||||||||||||||||||||||||||||||||||||||||||||||||||||||||||||||||||||||||||||||||||
6 | 10 | 4970 M Формы линии по производству газобетонных блоков разделены на раму пресс-формы и боковую пластину, которая является важным оборудованием для формования продукта.
|