Технологический процесс производства газобетонных блоков
Сегодня технология производства газобетонных блоков интересует всех, кто планирует строить загородный дом или открывать бизнес по производству ячеистых бетонов. Ведь этот строительный материал является очень удачным выбором в плане прочностных и теплоизоляционных характеристик, и к тому же изготовление газобетона может быть достаточно выгодным бизнес-проектом.
Что нужно знать о ячеистом бетоне?
Газобетон представляет собой искусственный камень с микроскопическими воздушными порами. Еще одно его название — автоклавный ячеистый бетон, и оно само по себе говорит о технологии его производства. Газоблоки обладают прекрасными энергосберегающими характеристиками именно благодаря своей пористой структуре. Кроме того, они отличаются относительно небольшим весом, в том числе по сравнению с кирпичом и другими видами строительной керамики.
Газобетонные блоки — это строительный материал, который может использоваться как для возведения внутренних перегородок, так и для несущих конструкций. Он не подойдет для высотных зданий или промышленных объектов, но в индивидуальном строительстве он прекрасно себя зарекомендовал. Относительно легкие газоблоки не оказывают большой нагрузки на фундамент, что позволяет сократить расходы на устройство основания. Кроме того, они обладают большими размерами, и это позволяет ускорить процесс строительства.
Состав газобетонных блоков
Все перечисленные преимущества этого строительного материала обусловлены его составом. Все, из чего состоит газобетон, — это цемент, кварцевый песок и газообразователь, в роли которого выступает алюминиевая пудра. Некоторые производители добавляют в состав гипс, известь, золу, другие ингредиенты.
Таким образом, газобетон делается на основе сухих компонентов, которые размешиваются с водой. Для этих целей подходит любая техническая чистая вода, соответствующая требованиям ГОСТа 23732-79. При этом важна температура воды. Желательно, чтобы она была не ниже 45°С, поскольку это ускорит твердение блоков, повысит их прочность, а для предприятия это выгодно тем, что увеличится производительность линии в целом. Таким образом, многие производители подогревают воду, поскольку более высокая температура означает лучшее качество материала. А еще это помогает уменьшить количество используемого цемента, поскольку нагрев воды стимулирует активность сухих компонентов смеси.
Производство газобетона требует довольно серьезного подхода к выбору песка. Теоретически для этих целей подойдет как карьерный, так и речной песок, но важно, чтобы в нем содержалось как можно меньше илистых или глиняных частиц. Также важно выбрать размер зерен — не более 2 мм. Технология производства газобетона автоклавным способом позволяет заменить песок шлаком или золой, полученным от металлургических производств. Золы ТЭС помогают получить газобетон с меньшей плотностью. Это помогает дополнительно сократить расходы на производство материала.
Для изготовления газобетонных блоков необходим портландцемент марок М400 и М500. Лучше всего, чтобы портландцемент соответствовал требованиям ГОСТа 10178-85. А вот алюминиевая пудра должна быть марок ПАП-1 или ПАП-2 — она и выполняет роль газообразователя. Иногда для тех же целей применяется специальная паста. Это может быть и суспензия, поскольку пылевидный алюминий не так удобен при замешивании раствора. Могут применяться и суспензии на его основе.
На чем основано действие алюминиевого порошка? Он вступает в реакцию с цементным или известковым раствором, обладающим свойствами щелочи, и в ходе этого химического процесса образуются соли (алюминаты) кальция и газообразный водород, обеспечивающий формирование пор.
Для производства газобетона очень важно сделать правильный расчет расхода по каждому компоненту исходного сырья. Существуют стандартные рекомендации для автоклавных газоблоков. Исходя из такой рецептуры, на весь объем смеси берут 50-70% цемента, 0,04-0,09% алюминиевого порошка и до 20-40% песка. Кроме того, понадобятся вода (0,25-0,8%) и известь (1-5%). Таким образом, для того чтобы получить 1 кубометр газобетона, нужно взять до 90 кг цемента, до 300 л воды, извести — 35 кг, песка — 375 кг, алюминиевого порошка — 0,5 кг. Но это количество может быть скорректировано уже в условиях конкретного производства в зависимости от качественных характеристик самого сырья.
Какое оборудование понадобится?
Технология изготовления газобетона относительно проста. Тем не менее кустарными методами здесь обойтись не получится. Нужно приобрести специальное оборудование, которое обычно заказывают в комплексе у производителя или его официального представителя, — это наиболее выгодный вариант. Это не одна какая-то установка, это целый автоматизированный мини-завод. Иногда производитель даже предоставляет услуги специалиста, который проконсультирует относительно монтажа такой линии, поможет ее наладить и подобрать оптимальный состав для смеси, используемой для такого оборудования.
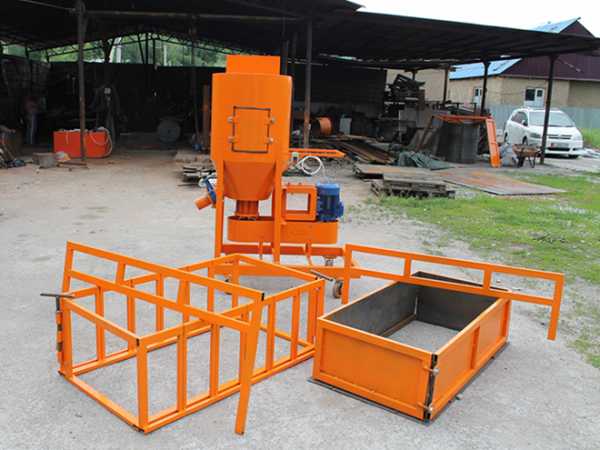
Мини-завод по производству неавтоклавного газобетона
В линию входят различные устройства, и теоретически каждое из них можно купить по отдельности, если по каким-то причинам одно выйдет из строя. Речь идет о таких вещах, как формы и предназначенные для их транспортировки передвижные поддоны, устройства для резки готовых блоков, смесители для газобетона, дозаторы для сыпучих материалов и т.д. Но главное — это печь-автоклав, ведь речь идет именно о производстве автоклавных газоблоков, отличающихся наиболее высокими качественными характеристиками.
Оборудование для производства газобетона делится на несколько типов. Выбор конкретного варианта зависит от требуемой суточной производительности, от того, сколько работников планирует нанимать предприниматель, и как будут организованы смены. Возможны следующие варианты:
- Стационарные линии обладают суточной производительностью до 60 кубометров готовой продукции. Как правило, для них нужны складские и производственные помещения площадью не менее 500 м². Главной особенностью таких линий является то, что формы подъезжают к стационарно установленному смесителю и там заполняются раствором, после чего выполняются все остальные технологические этапы. Это очень простая технология, для того чтобы обслуживать такую линию, достаточно нанять одного дополнительного работника.
- Конвейерные линии нужны там, где требуется большая производительность — до 75-150 м³ в сутки. Здесь производство осуществляется более быстрыми темпами (конечно, сроки созревания изделия не меняются, от линии это не зависит). Однако конвейерные линии требуют больших по площади производственных помещений, а для их обслуживания понадобится не менее 8 человек, хотя большинство технологических процессов здесь происходит в автоматическом режиме.
- Мини-линии не могут похвастаться высокой производительностью, до 15 кубометров готовых блоков в сутки. Отличием от стационарных линий является то, что движется в них смеситель, а формы установлены стационарно. Главное преимущество — им не нужны большие производственные площади, достаточно 140-160 м², так что в качестве стартового варианта они пользуются популярностью.
В частном строительстве часто используют мобильные установки, которые нужны для самостоятельного изготовления газоблоков. Это окупается, причем по расчетам специалистов расходы на строительство снижаются примерно на 30%. Мобильные установки поставляются в комплекте с компрессором. Работают они даже от бытовой электросети.
Этапы производства
Газобетон бывает двух видов — автоклавный или неавтоклавный. Последний вариант стоит дешевле, хотя полученный материал и отличается более низкой прочностью. Тем не менее из-за того, что себестоимость его изготовления ниже (не нужно покупать автоклав, содержать его, платить дополнительно за энергию), он является довольно популярным вариантом, поэтому его стоит рассмотреть подробнее. Если предприниматель намерен выпускать неавтоклавный газобетон, технология производства для него должна сводиться к следующим основным этапам:
- Точная дозировка всех описанных выше компонентов, а затем тщательное их перемешивание. При наличии соответствующего оборудования этот этап отнимает не более 10 минут.
- Подготовленную массу с помощью специального оборудования выгружают в специальные формы (их заполняют только наполовину, поскольку смесь будет увеличиваться в объеме в процессе газообразования). Этот процесс будет протекать в течение 4-х часов. За это время смесь заполняет отведенный ей в форме объем, а иногда даже его ей бывает мало. Тогда через 2 часа излишки можно будет убрать.
- Процесс выдержки изделий занимает около 16 часов, и по истечении этого срока происходит их распалубка и перегрузка на поддоны, где они будут набирать так называемую отпускную прочность. Этот этап отнимает еще 2-3 дня. После этого изделия можно отправлять на склад, но продавать их еще рано, поскольку свою марочную прочность они наберут только на 28-е сутки.
Изготовление газобетонных блоков с применением автоклава на первых этапах практически ничем не отличается от описанной выше технологии. Сначала нужно отмерить необходимое количество всех компонентов (желательно, чтобы это было сделано с помощью дозаторов, это поможет повысить точность). Затем всю эту массу загружают в смеситель и тщательно перемешивают. Иногда специалисты для этих целей предлагают использовать бетономешалку. Затем вводят газообразователь — это происходит через 10-15 минут перемешивания исходных ингредиентов. Алюминиевый порошок в любом случае вступает в реакцию с раствором, для этого ему не нужно автоклавирование.
Полуфабрикат разливают по формам, выдерживают положенные 4-6 часов, после чего производится нарезка газоблоков. До набора прочности они должны полежать еще 10-18 часов.
Но самое важное — знать, как делают автоклавирование после всех описанных выше процедур. Сформированные блоки перегружают в специальную печь, в герметичную камеру, где при высокой температуре каждый блок обрабатывают насыщенным водяным паром. Давление при этом также должно быть высоким — до 12 кг/см².
Неавтоклавный бетон сушат в естественных условиях, но для автоклавных изделий этого не нужно. Тем не менее и их нужно держать около 28-30 суток на складе, где они будут набирать марочную прочность.
Мало знать, как делать газобетон, нужно еще суметь доставить его потребителю. Для этого газоблоки пакуют в специальную термоусадочную пленку и транспортируют на деревянных поддонах.
kamedom.ru
Газобетон своими руками в домашних условиях: технология
Газобетон – это универсальный материал, который обладает отменными прочностными характеристиками и является простым в монтаже. Поэтому материал широко применяется в строительстве. Для экономии денежных средств на этом процессе рекомендовано изготовление газобетона своими руками в домашних условиях.
Что такое газобетон и каковы его характеристики
Перед применением газобетона для возведения домов и других построек на участке, рекомендовано предварительно определить его характеристики.
Основные свойства и качества
Соответственно мировым стандартам качества и ГОСТу материал должен обладать перечнем определенных качеств. Качественный материал должен выдерживать 35-100 циклов заморозки и разморозки. Показатель теплопроводности газобетона составляет 0,09-0,38. Плотность материала составляет Д300-Д1200. Средний показатель паропроницаемости – 0,2. Усадка газобетона составляет 0,3 миллиметра на квадратный метр.
Виды материала и изделий из него
Соответственно характеристикам газобетона его разделяют на: теплоизоляционный, конструкционный, конструкционно-теплоизоляционный.
Теплоизоляционный газобетон имеет плотность от 300 до 400. Он имеет низкую теплопроводность и характеризуется незначитекльным весом. Применение материала рекомендуется для теплоизоляции помещений.
Конструкционный газобетон обладает отменными прочностными характеристиками и имеет плотность от 1000 до 1200. Благодаря высокому коэффициенту теплопроводности предоставляется возможность его применения в качестве утеплителя.
Наиболее популярным является конструкционно-теплоизоляционный газобетон. Он характеризуется плотностью 400-900. С его применением возводятся стены и перегородки.
Сильные стороны строений возведенных из газобетона
Материал широко применяется в строительстве благодаря наличию большого количества преимуществ:
- Для производства материала используется песок, известь, цемент, алюминиевая пудра и вода, что обеспечивает экологичность материала.
- Газобетон имеет небольшой вес, что упрощает процесс его укладки.
- Благодаря большим размерам газоблоков ускоряется процесс возведения газобетона.
- Материал характеризуется высоким уровнем стойкости к возгоранию.
- Газобетон является стойким к морозам, что позволяет его применять в суровых климатических условиях.
- Благодаря универсальному составу материала предоставляется возможность его распиловки и шлифовки.
- Газобетон позволяет использовать разнообразные материалы для отделки зданий внутри и снаружи.
- Такие показатели, как прочность и теплопроводность, являются оптимальными.
- Производство материала осуществляется различными компаниями, что позволяет клиенту выбрать наиболее приемлемый вариант для себя.
- Материал обладает паропроницаемыми свойствами, что позволяет обеспечить оптимальный микроклимат в помещении.
- Газобетон обладает хорошими звукоизоляционными свойствами, что обеспечивает комфортное пребывание в помещении.
Газобетонный дом имеет высокие эксплуатационные характеристики, что объясняется большим количеством преимуществ материала.
Недостатки изделий и их устранение
Перед тем, как сделать газобетон в домашних условиях, рекомендовано определить его недостатки. Материал является гигроскопичным, что приводит к усиленному водопоглощению. При отрицательных температурах накопленная в блоках влага кристаллизируется, что приводит к их разрушению.
Для того чтобы решить эту проблему нужно стены из газобетонных блоков облицовывать. С этой целью используется кирпич, металлопрофиль, дерево и другие отделочные материалы.
Производство газоблока своими руками
Технология производства газобетона в домашних условиях требует от мастера придерживаться определенных правил. Этот процесс состоит из нескольких этапов.
Необходимый набор оборудования и материалов
Перед тем, как изготавливать газобетон, нужно подготовить материалы и инструменты. Бетон делается из смеси таких материалов:
- Песок. Рекомендуется отдавать предпочтение кварцевому песку, который предварительно проходит процесс промывки и высушивания.
- Цемент. Высокопрочный материал получается при использовании цемента, который имеет марку более 400.
- Чистой воды.
- Негашеной извести.
- Алюминиевой пудры, каустической соды, сульфата натрия.
Формы
Перед тем, как делают газобетон, подготавливают формы. В строительных магазинах можно купить готовые изделия. Для экономии денежных средств их создают самостоятельно. Изначально изготавливают пенал из деревянных досок. В него вставляют перемычки, с помощью которых обеспечивается разделение каркаса на отсеки. Изготовление форм может проводиться из влагонепроницаемой фанеры. Для того чтобы зафиксировать доски, в них предварительно нужно сделать пропилы.
Размеры ячеек должны совпадать с размерами, которые в соответствии с проектом должен иметь готовый блок. Для того чтобы ускорить производственный процесс, рекомендовано провести одновременное сооружение нескольких форм. Для того чтобы исключить возможность прилипания раствора к формам, их нужно предварительно смазать специальным средством. В домашних условиях рекомендовано применение отработанного машинного масла, которое разводится водой в соотношении 1:3.
Для того чтобы ускорить изготовление газобетона можно использовать мобильные установки, которые состоят из компрессора, смесителя и соединительных рукавов. Предварительно подготавливаются приспособления, с помощью которых удаляются излишки бетона.
Приготовление раствора
Процесс изготовления газобетона в домашних условиях начинается с приготовления раствора. Количество используемых компонентов зависит от того, какой плотности материал пользователь хочет получить. Рассмотри вариант приготовления раствора для газобетона, плотностью 1600 килограмм на метр кубический. Для этого понадобится 1100 килограмм песка и 400 килограмм цемента. Компоненты тщательно перемешиваются. К ним нужно добавить 5 кг извести. Также в раствор добавляются такие добавки, как каустическая сода, алюминиевая пудра и сульфат натрия.
После тщательного перемешивания всех сухих компонентов, они заливаются 189 литрами воды. После перемешивания состава до однородности его можно использовать для заливки.
Заливка
После смазывания форм специальным составом, в них заливается раствор. При этом нужно следить, чтобы формы не заливались до краев, так как при застывании смесь вспучивается и излишки будут вылизать наружу. Формы нужно заливать до половины. После заливки материала наблюдается появление процесса газообразования. На следующем этапе проводится удаление излишков смеси с применением металлических струн. Процедура проводиться по истечению 5-6 часов после заливки.
Спустя 18 часов после заливки можно проводить распалубку изделий. Для того чтобы газобетонные блоки лучше отходили, нужно немного постучать по формам. По истечению месяца газобетон обретет техническую прочность. Затвердевание блоков наблюдается не только в помещениях, но и на открытых площадках.
Сравнение изделий самостоятельного и заводского выпуска
При производстве газобетонных блоков своими руками они затвердевают гидратационно, а на производстве – автоклавно. Эти материалы отличаются между собой по техническим и физическим параметрам. На производстве изготавливаются блоки стационарным и конвейерным способом. При использовании второго варианта снижается необходимость в участии человека к минимуму. В домашнем производстве материала человек принимает постоянное и непосредственное участие.
Рентабельность производства
На рентабельность изготовления блоков влияют разнообразные факторы. Она зависит от:
- Стоимости сырья;
- Вложений на покупку оборудования;
- Количества производственных отходов;
- Желаемого объема;
- Цели производства.
Специалисты провели расчеты в соответствии с показателями, в соответствии с которыми было установлено, что сделать газобетонные блоки своими руками дороже, чем приобрести готовый материал. Кроме того, этот процесс требует затрат сил и времени.
Газобетонные блоки – это универсальный строительный материал, который широко применяется для возведения зданий. Приобрести его можно на заводах и в строительных магазинах. Также можно провести изготовление блоков своими руками, предварительно рассчитав рентабельность этого процесса.
1beton.info
Необходимое оборудование для производства газобетона

Мини-завод по производству неавтоклавного газобетона
Раньше изготовление газобетонных изделий было только на заводах. Теперь оборудование для производства газобетона может устанавливаться на небольших площадках или даже во дворе собственного дома.
В зависимости от количества необходимых блоков можно приобрести оборудование в виде мини-завода, поставить мобильную установку для получения блоков различной плотности.
Технология получения газобетона
Газобетон относится к разряду ячеистых бетонов. Состоит он из смеси нескольких компонентов:
- песок — 20-40%;
- известь — 1-5%;
- цемент — 50-70%;
- вода чистая — 0,25-0,8%;
- пудра алюминиевая — 0,04-0,09%.
Песок используется просеянный, его фракции не превышают 2,1 мм. Глины в нем должно содержаться не больше 7%. Цемент нужен качественный — марки М400 или М500. Алюминиевая пудра применяется в качестве газообразователя. В состав могут включаться еще некоторые компоненты: пластификаторы, ускорители твердения. Для изменения свойств газоблоков в смесь добавляют шлак, гипс или опилки. Этими добавками можно изменить плотность блоков. Ведь материал для изготовления фундамента должен быть прочнее, чем для перегородок. Теплоизоляционные блоки желательно делать более легкими и пористыми. Для этого можно полностью исключить из его состава песок.
Производство газобетонных изделий бывает автоклавное и неавтоклавное. Второй вариант производится гораздо проще, но имеет низкую прочность, недостаточную точность геометрических размеров. Автоклавные изделия бывают обычно более однородной структуры и низкой теплоемкости. Такие блоки используются в условиях России для возведения стен толщиной до 400 мм.
Изготовление блоков
Для производства газоблоков не требуются особо сложные установки. Нужно лишь точное выполнение технологических циклов. Изготовление может выполняться в следующем порядке:
- подготовка компонентов;
- введение газообразователя;
- укладка раствора в формы;
- разрезание блоков;
- созревание изделий;
- автоклавирование.
Все необходимые компоненты взвешиваются и всыпаются для перемешивания в смеситель. Минут через 10-15 к ним добавляют алюминиевую пудру, которая сразу же вступает в химическую реакцию с находящейся в смеси известью. В результате реакции смесь наполняется газом в виде пузырьков по всему объему. Это является сигналом к выкладке раствора в формы для газобетона или на специальный лоток толстым слоем. На лотке производят разрезку массы на блоки особыми пилами. Созревают полуготовые блоки в течение 10-18 часов. После этого блоки помещаются в автоклав. Это особая печь, состоящая из герметичной камеры с температурой 190°C. В ней материал обрабатывается горячим паром под высоким давлением. Далее готовый материал вынимается из автоклава и раскладывается для просушки.
Неавтоклавный строительный материал просушивается в течение 3-7 суток естественным образом. Далее блоки складируются в помещение для набора полной прочности. Происходит это обычно 30 суток. Только по истечении этого срока можно перевозить газобетон к потребителю, упаковав его в специальную термоусадочную пленку.
Оборудование для изготовления блоков
Для газобетонных блоков обычно комплектуется технологическая линия, состоящая из:
- смесителя;
- активатора;
- дозатора;
- режущего приспособления;
- автоклава;
- форм.
Все это оборудование бывает разной мощности. Она обычно варьируется в пределах 10-150 м³ в сутки. Самое дорогое в этом наборе — автоклав. От него и зависит стоимость готового продукта. В домашних условиях это производство чаще всего становится нерентабельным.
Оборудование можно разделить на такие виды:
- стационарная линия;
- конвейерная линия;
- мини-линия;
- мини-завод;
- мобильная линия.
Стационарная линия оборудования для газобетона может производить от 60 м³ продукции в сутки. Для ее складирования требуется примерно 500 м² площади. С управлением линией вполне справятся 2 человека.
Конвейерная линия может выпускать за сутки 75-150 м³ готовой продукции. Размещения оборудования для производства газобетонного блока требует площади более 600 м². Обслуживают его 8 человек.
Мини-линия рассчитана на суточный выпуск около 15 м³ изделий. В состав линии входит смеситель и формы. Для организации производства и установки оборудования требуется 2 человека и 140-160 м² площади.
Установка мини-завода гарантирует выпуск готовых блоков от 25 м³ в сутки. Это немного больше, чем с помощью мини-линии. Отличает мини-завод лишь наличием в его составе поддонов, бака с водой, оборудования для разрезания газобетона.
Мобильные линии часто используются при строительстве личных домов. Они позволяют снизить расходы на треть. Для получения качественного газобетона оборудование подключается к розетке 220 В. В составе линии может быть:
- неподвижный смеситель;
- передвижные формы для заливки раствора;
- установка для разрезания блоков.
Производительность линии достигает 100 м³ в сутки.
Заключение по теме
На протяжении многих тысячелетий человек строит для себя жилье. За эти годы значительно изменились технологии и материалы для строительства. В наше время актуальным стало строительство с использованием газобетона в виде блоков. Раньше блоки выпускались только на заводах, сегодня их производство можно наладить дома. Для этого нужно иметь желание, приобрести оборудование и установить все это на подготовленной площадке. Для выпуска газобетона нужно иметь чистую теплую воду, кварцевый песок, алюминиевую пудру марки ПАП-1, известь, портландцемент М400 или М500 и еще несколько добавок для улучшения качества продукции. Получив все это, можно начинать собственный бизнес по выпуску стройматериалов, имеющих большой спрос. При строительстве собственного дома материал сократит расходы примерно на треть.
Для собственного производства лучше всего приобрести небольшую стационарную линию, с помощью которой можно делать неавтоклавный газобетон. Обслуживать установку могут 2 человека. При таких силах можно ежесуточно выпускать около 60 м³ отличных блоков. Каждый такой искусственный камень весит примерно 30 кг и заменяет собой около 30 стандартных кирпичей. Газоблок весит в несколько раз легче кирпича, поэтому не требует строительства капитального фундамента и использования грузоподъемной техники. Материал отлично обрабатывается ручными инструментами: пилой, стамеской, сверлом. В наше время газобетон занимает ведущее место среди других строительных материалов.
kamedom.ru
процесс домашнего/промышленного изготовления + оборудование
Мир строительных материалов совершенствуется каждый год. На свет появляются гибридные продукты, обладающими высокими техническими характеристиками, которые не только продлевают срок службы построек, но и экономят деньги потребителя. Одной из таких новаций является производство газобетона.
Сегодня мы подробно расскажем технологию изготовления этого стройматериала и чем он выделяется на фоне конкурентов вообще.
Что такое газобетон?
Все мы знаем о бетоне – без данного материала не обходится ни одно строительство. В основном, его применение происходит в качестве связующего компонента, но в комбинации с наполнителями (песок, щебень и так далее) можно получить качественные блоки, являющимися альтернативой кирпичу и ракушке.
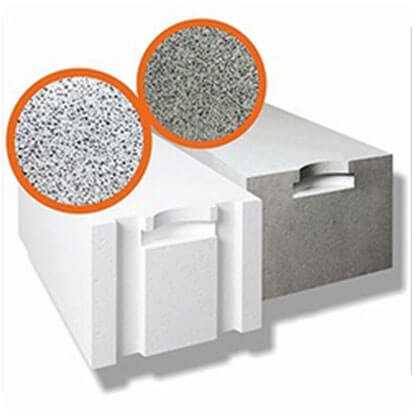
Газобетон – один из видов ячеистого бетона. Отличительная черта – пористость, получаемая путем химических реакций при производстве материала.
Классификаций газобетона много. Они зависят от оборудования, на котором происходило его производство, и вспомогательных добавок.
Преимущества газобетона:
- благодаря пористости, газобетон снижает нагрузку для фундамента постройки;
- производство газобетона можно осуществлять в домашних условиях без специального оборудования;
- пористый бетон очень гибок в плане геометрии поведения – придавать форму блокам очень легко и для этого подойдет оборудование, доступное в каждом доме;
- высокие значения прочности + защита от низких температур;
- благодаря высокой теплопроводимости газобетон рационально использовать при утеплении зданий в качестве изоляционного материала;
- экологически чистый продукт;
- пористый бетон – это огнеупорный материал, не поддающийся тлению и воспламенению.
Как и везде, без минусов здесь также не обойтись. Однако главная особенность этого материала заключается в том, что эти недостатки можно нивелировать. Для этого просто придерживайтесь элементарных норм эксплуатации и используйте газобетон лишь по его целевому применению.
Недостатки газобетона:
- большая чувствительность к влаге – пористый бетон обладает высоким показателем водопоглощения, что заставляет при строительстве использовать защитное покрытие поверх самого газобетона;
- для фиксации требуется закупка специальных крепежей вместо стандартных метизов;
- усадка влияет на структуру стен, иногда могут появляться небольшие трещины;
- из-за пористости с проникновением влаги внутрь газобетона появляется риск разрушения материала кристаллами воды при воздействии низких температур.
Производство газобетона – очень популярное направление, которое приобрело распространение не только в промышленности, но и как «кустарное» изготовление в домашних условиях. Благо, технология довольно проста и оборудование для этих целей достать очень легко.
Главная опасность для бизнеса – снижение общей репутации пористого бетона из-за частных производителей, которые продают низкокачественный товар своим потребителям.
Выделяют два типа газобетона по методу изготовления – автоклавный и неавтоклавный. Структура и первого, и второго аналогична, но ключевое отличие кроется в технологическом аспекте и оборудовании, необходимом для реализации производства.
Сравнительную характеристику двух видов газобетона мы подали в таблице ниже:
Характеристика | Автоклавный газобетон | Неавтоклавный газобетон |
---|---|---|
Затвердевание | Обрабатывается на последней стадии изготовления в автоклаве. Воздействие высокого давления и температуры дает свои результаты. Готовый продукт можно получить за 24 часа. | Достигает марочной прочности в естественных условиях. Иногда его слегка подогревают в специальных печах до невысокой температуры, не превышающей 100 градусов. Так процесс происходит быстрее. Техническая зрелость таких изделий наступает спустя 28 дней. |
Внешние характеристики | Белый цвет + четкие границы формы | Серый. Иногда углы газобетона могут осыпаться |
Прочность/плотность | Более прочный материал. Прочность и плотность имеют оптимальные показатели для возведения стен. | Менее прочный газобетон. Чтобы уравнять показатели с автоклавным, при возведении теплоизоляционной стены необходимо увеличение толщины кладки на 18-20 сантиметров. |
Хрупкость, долговечность, геометрия | Автоклавный газобетон может прослужить до 200 лет, а благодаря улучшенной геометрии, количество дополнительных затрат при строительстве значительно уменьшается. | Газобетон гидратационного твердения более хрупкий. Долговечность его может достигать 50 лет. |
Сложность производства | Автоклавный газобетон выпускается, как правило, с использованием высокотехнологичных конвейерных установок. Как следствие, скорость изготовления больше, продуктивность – выше. | Производство неавтоклавного газобетона занимает значительно больше времени, а при выпуске изделий своими руками трудозатраты крайне велики. |
Производство газобетона неавтоклавным путем может производится в домашних условиях, так как нет необходимости закупать полномасштабное оборудование, которое работает по принципу конвейера.
Автоклавный газобетон можно изготовить только промышленным путем. Для этих целей закупаются полноценные автоматические линии производства + это все дополняется другим специализированным оборудованием, сводящим процесс изготовления газобетона в рамки 18-24 часов.
Классификация газобетона на основании плотности:
- Теплоизоляционный пористый бетон – вспомогательный материал для утепления стен. Не может использоваться в качестве строительной основы из-за низкой прочности – до 380 кг/м3.
- Теплоизоляционно-конструкционный. Прочность достигает 880 кг/м3 при высоком показателе теплопроводимости, что делает его наиболее универсальным решением при строительстве частных домов, а также при возведении несущих стен.
- Конструкционный пористый бетон. Обладает высоким запасом прочности – до 1300 кг/м3, но его теплопроводимость составляет 0.4+, что не годится для качественной изоляции помещений извне.
Если вы хотите производить газобетон по ГОСТу, придется указывать категорию вашей продукции, которая распространяется уже на сами блоки, что получаются на конечном этапе производства пористого бетона.
Производство брусчатки: подробно об аспектах организации
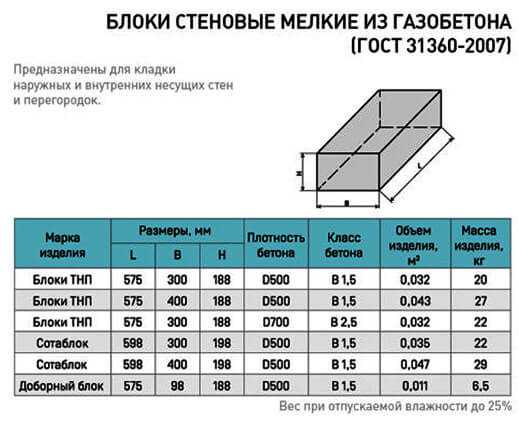
На рисунке выше представлена полная классификация блоков из газобетона на основании их геометрии и технических характеристик стройматериала.
Если производство газобетона происходит на ручном оборудовании в домашних условиях, придерживаться всех требований будет весьма затруднительно. Однако, чем выше качество газобетона, тем дороже товар уйдет на рынке. А это дает возможность к дальнейшему расширению идеи и переходу на промышленный вариант изготовления пористого бетона.
Какие технологические моменты производства газобетона?
В этом разделе мы вплотную разберемся в вопросе – как изготовить газобетон. Рассмотрим технологические моменты производства как в домашних условиях, так и промышленных + предоставим список наиболее актуального оборудования для этих целей в 2018 году.
Вариант 1. Технология производства газобетона в домашних условиях.
Для производства газобетона в домашних условиях не требуется дорогостоящего оборудования, большинство технологических процессов можно выполнить самостоятельно + экономия для конечного потребителя составит около 40% от рыночной стоимости пористого бетона.
Почему изготавливать блоки дома выгодно:
- Цена конечного продукта. Этот пункт мы уже описали выше – экономия на самом товаре до 30%+ не забываем о транспортировке, которая также съест от 5 до 15% ваших денег на закупку.
- Не требуется закупать газобетон с запасом. При строительстве человек делает кладку стык в стык, потому предугадать точное количество блоков очень проблематично. Таким образом, происходит переплата на 10-15%. Но, если вы наладили производство газобетона у себя дома, эти проценты останутся в вашем кармане, а не уйдут продавцу.
- Хоть ассортимент блоков из газобетона и довольно широк, очень трудно подобрать идеальный размер именно для ваших целей. При производстве газобетона в домашних условиях вы сами настраиваете оборудование и делаете формы по собственным замерам, что очень удобно.
Газобетон домашнего производства можно использовать для строительства 1-2 этажных зданий, а сам процесс изготовления должен осуществляться при температуре не менее 5+ градусов по Цельсию, иначе нормально просохнуть пористый бетон попросту не сможет.
Оборудование для производства газобетона в домашних условиях:
Бетономешалка.
Ручной замес раствора как вариант даже не стоит и рассматривать, так как обеспечить качественное смешивание реагентов и добиться равномерной пористости не удастся.
Формы для заливки.
Если нет возможности купить готовые, соорудить данное оборудование самому особых усилий не составит. Достаточно иметь дома станок по резке листового металла, аппарат по сварке и клепки для скрепления элементов.
Допускаются формы и из дерева, но для их производства потребуются уже столярное оборудование.
Стальная проволока.
Необходима для срезки верхней бугристой части газобетона после наполнения смесью форм заготовки.
В качестве исходного сырья для производства газобетона используют бетон Д20 -400, песок из кварца и добавки – такие, как каустическая сода и сульфат натрия.
Для получения пористого бетона необходимо вступление в химическую реакцию 2-х компонентов – негашеной извести и пудры из алюминия. Все компоненты смешиваются и заливаются проточной водой.
Технология изготовления газобетона в домашних условиях:
Смешение сухих компонентов.
Исходное сырье засыпается в нужных пропорциях в смеситель, коим выступает бетономешалка. Всё оставляют на 5-10 минут. Полученная сухая смесь должна иметь однородный цвет.Добавление жидкости.
Заливается вода и процесс смешивания газобетона продолжается, пока раствор не при
biznesprost.com
12 лучших производителей газобетонных блоков
Обновлено: 18.09.2019 22:30:16
Эксперт: Давид Вайнберг
*Обзор лучших по мнению редакции expertology.ru. О критериях отбора. Данный материал носит субъективный характер, не является рекламой и не служит руководством к покупке. Перед покупкой необходима консультация со специалистом.
Газобетонные блоки стали в последние годы очень популярным строительным материалом. Российские потребители по достоинству оценили его высокие эксплуатационные свойства, экономию времени и финансов при строительстве. Область применения газобетона продолжает расширяться, а спрос подхлестывает производителей к расширению ассортимента. Сегодня на отечественном рынке наблюдается многообразие этой продукции, что затрудняет выбор неискушенному покупателю. Советы наших экспертов помогут разобраться с основными параметрами газобетонных блоков.
Как выбрать газобетонный блок
- Технология производства. Для изготовления газобетона требуются такие природные материалы, как песок, цемент, известь, гипс. Газообразование происходит за счет добавления алюминиевой пыли, которая начинает реагировать при добавлении воды с цементом и известью. А вот для затвердения массы производители используют два способа.
- Автоклавная технология подразумевает обработку сформированного блока насыщенным паром, который подается при высоком давлении. Такой газобетон отличается высокой прочностью, но стоит дороже. Он рекомендуется для возведения стен.
- Неавтоклавная технология заключается в термической обработке полуфабриката, иногда сушка происходит на открытом воздухе. Газобетон получается дешевле, но применять его следует для устройства перегородок.
- Марка газобетона. Определяющей характеристикой газобетонных блоков является плотность. Она изменяется в кг/куб. м, а численное выражение становится обозначением марки после литеры D. Диапазон плотностей колеблется от D200 до D1200. Самые тяжелые блоки используются для устройства несущих конструкций многоэтажек, марки D500…D600 оптимально подходят для частного домостроения. А самые пористые и легкие изделия (D200…D350) применяются для теплоизоляции зданий или создания внутренних перегородок.
- Прочность на сжатие. Плотность газобетона напрямую влияет еще на один важный параметр, который называется прочность на сжатие. Для обозначения принято использовать соответствующий коэффициент в МПа. Например, популярный блок B2,5 обладает прочностью на сжатие 2,5 МПа, а плотность его находится в пределах 700-800 кг/куб. м. Для сравнения у кирпича этот показатель достигает 15-20 МПа, поэтому для многоэтажного строительства газобетонные блоки не применяются.
- Морозостойкость. Важнейшим показателем газобетона для суровых климатических условий России является морозостойкость. Она определяется количеством циклов замораживания и оттаивания, которые выдерживает материал без ухудшения эксплуатационных характеристик. Диапазон морозостойкости колеблется в диапазоне F15…F100. Строители рекомендуют для возведения наружных стен использовать блоки с морозостойкостью выше F50.
- Разновидности газоблоков. На отечественном рынке представлено несколько разновидностей, отличающихся по форме и размерам. Классикой жанра считается прямоугольные конструкции, эксперты выделяют в этой группе несколько типов.
- Кладочные или стеновые газобетонные блоки выпускаются для возведения несущих стен. Иногда их используют и для устройства перегородок. При стандартной высоте (200 мм) и длине (600 мм) они отличаются шириной (200…500 мм).
- Специальные блоки для перегородок при тех же параметрах длины и высоты имеют ширину 75…150 мм.
- Для создания перемычек можно встретить в продаже блоки длиной 500 мм, высотой 200 мм и шириной 250…400 мм.
В наш обзор попали 12 лучших производителей газобетонных блоков. Их можно купить в разных регионах нашей страны. При распределении мест в рейтинге учитывалось мнение экспертов и отзывы потребителей.
Что лучше газобетон или пенобетон
Тип блоков |
Достоинства |
Недостатки |
Газобетон |
+ высокая прочность и надежность + морозостойкость + экологичность + отсутствует усадка + стабильные геометрические размеры |
— сильно поглощают влагу — высокая цена |
Пенобетон |
+ низкое водопоглощение + экологичность + низкая теплопроводность + низкая цена |
— склонность к образованию трещин из-за усадки — неточная геометрия |
Рейтинг лучших производителей газобетонных блоков
Aeroc
Рейтинг: 4.9
Крупнейшим производителем газобетонных блоков в России является компания «Аэрок СПб». Основано оно в 2004 г, все оборудование, установленное на предприятии, сделано немецкой фирмой Wehrhahn. Продукция поставляется на отечественный рынок под торговой маркой Aeroc. С момента запуска первой линии предприятие задает тон российским производителям. В 2005 г с конвейера сошел первый газобетонный блок с прочностью В2,5 и начался массовый выпуск продукции с плотностью D400 кг/куб м. В настоящее время Aeroc является единственным предприятием в России, где производятся блоки D300 (прочность В2,0). Эксперты отдали бренду первое место в нашем рейтинге за образцовую тепловую защиту.
Пользователи широко используют в строительстве питерские газоблоки, отмечая идеальную геометрию, легкость, экологичность и прочность.
Достоинства
- легкость;
- низкая теплопроводность;
- прочность;
- экологичность.
Недостатки
- не обнаружены.
XELLA
Рейтинг: 4.9
Немецкий производитель газобетонных блоков XELLA славится высочайшим качеством продукции. Спрос на газоблоки в нашей стране подтолкнул владельцев компании к строительству российского филиала. В 2007 г на территории Московской области заработал крупнейший завод по выпуску ячеистых блоков. Но экспертов особенно заинтересовало стремление производителя к обучению отечественных архитекторов и строителей. Разработаны даже программы повышения квалификации. Газобетонные блоки поставляются на отечественный рынок в самых разных исполнениях.
Пользователи отмечают большие размеры блока (600х300х200 мм), благодаря чему ускоряется возведение стен. А вот к минусам материала строители относят необходимость утепления и обязательную защиту от влаги. Производитель занимает второе место в рейтинге.
Достоинства
- удобство в работе;
- ровная геометрия;
- экологичность;
- простота обработки.
Недостатки
- низкая влагостойкость.
UDK
Рейтинг: 4.8
Крупнейшим производителем газобетонных блоков в Украине является компания UDK. Предприятие ориентируется на выпуск продукции премиум-класса. Производитель изготавливает строительные блоки по технологии автоклавного газобетона. В заводских цехах установлено оборудование фирмы Masa AG, что положительно сказывается на геометрии. Основной сырьевой базой являются такие природные материалы, как портландцемент, измельченный кварцевый песок, негашеная известь. Отличительной чертой бренда является стипендиальная программа для студентов, поддерживающая финансово отличников учебы.
Производитель занимает третью строчку рейтинга за точную геометрию, ценовую доступность и заботу о подрастающем поколении. К минусам пользователи относят большой отход и низкую прочность.
Достоинства
- приемлемая цена;
- точные размеры;
- экологичность;
- поддержка одаренной молодежи.
Недостатки
- низкая прочность;
- много отходов.
ЛСР
Рейтинг: 4.8
Одним из крупнейших производителей строительных материалов является «Группа ЛСР». Российская компания производит керамический и пористый кирпич, тротуарный и фасадный клинкер, перегородочные и стеновые блоки. В состав концерна входит 4 предприятия, одно из них построено на территории Московской области, еще 3 работают в Санкт-Петербурге. Все производственные площадки оснащены высокопроизводительным оборудованием. Популярностью у потребителей пользуются утепленные пористые блоки, этот строительный материал используется в частном и многоэтажном домостроении. Эксперты отдали производителю четвертое место в рейтинге. Подняться выше бренду не позволил скромный ассортимент газоблоков.
Достоинства
- собственные разработки;
- инновационное оборудование;
- высокое качество продукции;
- стойкость к воздействию атмосферы.
Недостатки
- скромный ассортимент газоблоков.
ЕвроАэроБетон
Рейтинг: 4.8
Еще один производитель газобетона из северной столицы России попал в наш рейтинг. ООО ЕвроАэроБетон занимается выпуском автоклавного ячеистого бетона с 2008 г. Продукция отвечает всем экологическим требованиям, она производится на современном европейском оборудовании. Под брендом ЕвроАэроБетон поставляется в продажу широкий спектр материалов. Это газобетонные блоки для стен, перегородок, U-образные конструкции, крошка, клей инструмент. Эксперты отдали производителю пятое место в нашем рейтинге.
Пользователи лестно отзываются о хорошей геометрии блоков, простоте использования, они легко режутся ножовкой. Не понравилась потребителям структура материала, напоминающая пенобетон.
Достоинства
- хорошая геометрия;
- широкий ассортимент блоков;
- современное европейское оборудование;
- легкость укладки.
Недостатки
- пористая структура.
Ytong
Рейтинг: 4.7
Родоначальником автоклавного газобетона считается немецкая компания Ytong. В 2003 г произошло слияние предприятия с двумя другими производителями из Германии, в результате чего появился концерн XELLA. Ячеистый бетон продолжает поставляться под торговой маркой Ytong. На территории Московской области построено предприятие, на котором выпускаются газобетонные блоки по самым современным технологиям. Газоблоки изготавливаются из натуральных компонентов, что делает конечную продукцию экологически чистой и нетоксичной. В ассортименте представлены стеновые, U-образные, армированные, перегородочные, дугообразные блоки.
Пользователи отмечают простоту обработки, экологичность, экономичный расход. К недостаткам следует отнести нестабильное качество продукции.
Достоинства
- передовые разработки;
- европейские технологии;
- натуральное сырье;
- широкий ассортимент.
Недостатки
- нестабильное качество.
Стоунлайт
Рейтинг: 4.7
Газобетонные блоки Стоунлайт выпускаются в г. Бровары Киевской области. Предприятие оснащено автоматизированными линиями, которые изготовлены известной немецкой компанией Хеттен. Украинский производитель тщательно контролирует качество поставляемого сырья. Проверка соблюдения технологии осуществляется на каждой промежуточной операции. Благодаря такому подходу удается своевременно выявлять брак, не допуская попадание его в торговую сеть. Эксперты по достоинству оценили высокое качество газоблоков, за что бренд попадает в наш рейтинг.
Пользователям понравилась легкость, доступность, экономичность материала. Некоторые потребители сообщают о таких недостатках, как неточные размеры и крохкость газобетонных блоков.
Достоинства
- автоматизированное немецкое оборудование;
- тщательный отбор сырья;
- контроль на каждой стадии изготовления.
Недостатки
- неточная геометрия;
- крохкость.
Липецкий силикатный завод
Рейтинг: 4.7
Крупным поставщиком строительных материалов на рынок Центрального региона России является Липецкий силикатный завод. Предприятие основано в 1938 г, с тех пор были освоены новые виды продукции. Сегодня производитель предлагает отечественному потребителю силикатный кирпич и перегородочные плиты, стеновые блоки из ячеистого бетона. В 2015 г было запущено новое производство высокопрочного кирпича на немецких прессах LASCO, а через год с конвейера сошел цветной силикатный кирпич. Завод попал в рейтинг 100 лучших предприятий России, работающих в строительной отрасли.
Пользователей устраивает прочность, многофункциональность и доступность липецкой продукции. Недовольство вызывает непостоянство качества от партии к партии, в сезон активного строительства попадается брак.
Достоинства
- прочность;
- многофункциональность;
- приемлемая точность;
- доступная цена.
Недостатки
- непостоянство качества;
- попадается брак.
Главновосибирскстрой (Сибит)
Рейтинг: 4.6
Лидером в строительном комплексе Сибири является предприятие Главновосибирскстрой. Компания предлагает комплексный подход к строительству домов, внедряя инновационные решения и передовые технологии. Завод работает с 1963 г, последние десятилетия продукция поставляется в торговую сеть под брендом СИБИТ. В 2007 г на предприятии была введена в эксплуатацию вторая очередь по изготовлению газобетонных блоков. Увеличение объема продаж позволило удовлетворить спрос на блоки в регионе.
Пользователи отмечают улучшение качества продукции, стремление производителя заинтересовать потенциального покупателя. Место в рейтинге объясняется использованием административного ресурса в регионе.
Достоинства
- сотрудничество с немецкими компаниями;
- современные автоматизированные линии;
- комплексный подход к строительству.
Недостатки
- недобросовестная конкуренция.
Саратовский завод стройматериалов
Рейтинг: 4.5
Современные газобетонные блоки выпускает Саратовский завод стройматериалов. Этот крупный концерн состоит из двух заводов, есть у него и собственный песчаный карьер. Производитель добывает качественное сырье, что в сочетании с голландским оборудованием позволяет выпускать конкурентоспособную продукцию. Объем производства превышает 900 тысяч кубометров газобетона в год. Газоблоки поставляются в 15 регионов России. Потребителю предлагается широкий ассортимент блоков с марками D300…D700 и прочностью В1,5…В5,0.
Эксперты включили бренд ГРАС в наш рейтинг за точность геометрии и приемлемые цены. А вот к прочности продукции есть претензии, т. к. при транспортировке образуется много битых блоков в нижних рядах.
Достоинства
- широкий ассортимент;
- доступные цены;
- точная геометрия;
- собственное сырье.
Недостатки
- образуется много боя при перевозке.
Костромской силикатный завод
Рейтинг: 4.4
Производство строительного кирпича на Костромском силикатном заводе началось в 1930 г. Предприятие одно из первых стало заниматься этим перспективным направлением. Сегодня компания может похвастаться широким ассортиментом, при этом проводятся работы по улучшению качества продукции. Кроме кирпича и газоблоков завод производит тротуарную плитку, бордюрный камень, железобетонные кольца. Благодаря налаженной товаропроводящей сети поставки кирпича и газобетона осуществляются в разные регионы страны. Эксперты отмечают высокую прочность, морозостойкость и долговечность газобетонных блоков.
Бренд занимает место во второй десятке нашего рейтинга из-за высокой цены на свою продукцию. А вот обслуживание клиентов на заводе организовано на высшем уровне.
Достоинства
- быстрое оформление и погрузка;
- прочность;
- морозостойкость;
- широкий ассортимент.
Казанский завод силикатных стеновых материалов
Рейтинг: 4.3
Большими объемами выпуска стройматериалов может похвастаться Казанский завод силикатных стеновых материалов. В год с производственных линий выходит около 230 млн. шт кирпича и 100 тысяч кубометров автоклавного газобетона. Предприятие поставляет свою продукцию на рынки Татарстана и Поволжья. Потребители ценят газобетонные блоки за высокую прочность и морозостойкость. Продукция выпускается в соответствие с государственными стандартами качества. С протоколами испытаний каждой марки можно ознакомиться на официальном сайте.
Место в рейтинге объясняется скромным присутствием бренда в других регионах страны. К качеству блоков у пользователей претензий нет.
Достоинства
- большой годовой объем выпуска;
- качественное изготовление;
- экологичность;
- богатый ассортимент.
Недостатки
- дефицит в торговой сети других регионов.
Внимание! Данный рейтинг носит субъективный характер, не является рекламой и не служит руководством к покупке. Перед покупкой необходима консультация со специалистом.
expertology.ru
Газобетон — Википедия
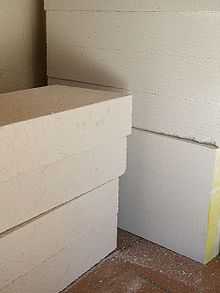
Газобето́н — лёгкий, ячеистый бетон с равномерно распределёнными по всему объёму замкнутыми порами[1] диаметром 1—3 мм. По технологии окончательной обработки различают автоклавный и «неавтоклавный» газобетон.
При производстве этого материала используются цемент, кварцевый песок и специализированные газообразователи, также в состав смеси при его изготовлении иногда добавляют гипс, известь, промышленные отходы, к примеру, зола и шлаки металлургических производств.
Газообразование в замешенной на воде смеси обусловлено взаимодействием газообразователя, обычно мелкодисперсного металлического алюминия с сильнощелочным цементным или известковым раствором, в результате химической реакции образуются газообразный водород, вспенивающий цементный раствор, и алюминаты кальция.
Пылевидный алюминий неудобен для применения при замешивании раствора, так как сильно пылит. Поэтому в качестве специализированных газообразователей используются алюминиевые пасты и суспензии.
Типичный цикл производства газобетона: Перемешанные сухие ингредиенты смешиваются с водой, раствор заливается в форму. Происходит реакция щелочного водного раствора гидроксида кальция и газообразователя, приводящая к выделению водорода, который и «вспучивает» смесь. Смесь увеличивает объём и вспучивается как тесто. После предварительного схватывания цементного раствора, монолит извлекают из формы и разрезают на заготовки блоков, плит, панелей. После этого разрезанные заготовки подвергают обработке водяным паром в автоклаве для придания им окончательной прочности, либо высушиваются в электроподогреваемых сушильных камерах.
Газобетон легко обрабатывается: пилится, сверлится, строгается обычными стальными инструментами, даже без твердосплавных напаек. В него легко забиваются гвозди, скобы, установочные изделия. Со временем в процессе карбонизации прочность может уменьшаться на 20-30% [источник не указан 153 дня].Так как пористость, а соответственно газо- и паропроницаемость современных блоков выше, то и карбонизация и старение происходит значительно быстрее указанных 15-20 лет, чем это описано в исследовании Е.С. Силаенкова. Не горюч, так как состоит только из минеральных компонентов.
Имеет меньшую естественную радиоактивность по сравнению с обычным бетоном, так как в его состав не входит гранитный щебень, слюды, — составная часть природных гранитов, которые имеют повышенную естественную радиоактивность из-за концентрации в этих минералах тория и урана.
Газобетон применяется в жилищном, коммерческом и промышленном строительстве. Основной объем потребления занимают строительные (стеновые и перегородочные блоки), также применяются армированные изделия (перемычки и плиты перекрытия).
- По назначению:
- конструкционные.
- конструкционно-теплоизоляционные.
- теплоизоляционные[2].
- По условиям твердения:
- автоклавные (синтезного твердения) — твердеющие в среде насыщенного пара при давлении выше атмосферного;
- неавтоклавные (гидратационного твердения) — твердеющие в естественных условиях, при электропрогреве или в среде насыщенного пара при атмосферном давлении.
- По виду вяжущих и кремнеземистых компонентов подразделяют:
- по виду основного вяжущего:
- на известковых вяжущих, состоящих из извести-кипелки более 50 % по массе, шлака и гипса или добавки цемента до 15 % по массе;
- на цементных вяжущих, в которых содержание портландцемента 50 % и более по массе;
- на смешанных вяжущих, состоящих из портландцемента от 15 до 50 % по массе, извести или шлака, или шлако-известковой смеси;
- на шлаковых вяжущих, состоящих из шлака более 50 % по массе в сочетании с известью, гипсом или щелочью;
- на зольных вяжущих, в которых содержание высокоосновных зол 50 % и более по массе;
- по виду кремнеземистого компонента:
- на природных материалах — тонкомолотом кварцевом и других песках;
- на вторичных продуктах промышленности — золе-унос ТЭС, золе гидроудаления, вторичных продуктах обогащения различных руд, отходах ферросплавов и других.
- по виду основного вяжущего:
Теплопроводность — одна из основных характеристик газобетона. Благодаря малой плотности и низкой теплопроводности, газобетон применяется в теплоизолирующих конструкциях (несущие и перегородочные стены зданий и сооружений). Теплопроводность газобетона марки D500 в сухом виде равна 0,12 Вт/м°C, в 4 раза ниже, чем у полнотелого кирпича (0,45-0,55 Вт/м°C), и несколько ниже теплопроводности дерева (0,15 Вт/м°C). Наличие влаги существенно влияет на теплопроводность газобетона, поэтому в характеристиках обычно указываются две величины — теплопроводность газобетона в сухом состоянии (обозначается λ(α)), и теплопроводность при влажности 4% — λ(β). Теплопроводность также существенно зависит от плотности газобетона: чем выше плотность, тем выше теплопроводность (так, теплопроводность газобетона марки D1000 уже 0,29 Вт/м°C), но также и прочность.
Коэффициент теплопроводности, Вт/м*°C | ||||
---|---|---|---|---|
Плотность | D300 | D400 | D500 | D600 |
Сухой газобетон | 0,072 | 0,096 | 0,112 | 0,141 |
Газобетон при влажности 5% | 0,088 | 0,117 | 0,147 | 0,183 |
История появления технологии производства автоклавного газобетона[править | править код]
Для придания бетону пористой структуры чех Гоффман добавил в цементные и гипсовые растворы кислоты, углекислые и хлористые соли. Соли, взаимодействуя с растворами, выделяли газ, который и делал бетон пористым. За изобретённый газобетон Гоффман в 1889 году получил патент, но дальше этого у него дело не пошло.
Замысел Гоффмана развили американцы Аулсворт и Дайер. В качестве газообразователя в 1914 году они использовали порошки алюминия и цинка. В процессе химической реакции этих порошков с гашеной известью выделялся водород, который и способствовал образованию в бетоне пористой структуры. Это изобретение оказалось столь значимым, что его и поныне считают отправной точкой технологии изготовления газобетона.
Свой вклад в дело совершенствования газобетона (газосиликата) внёс шведский архитектор и ученый Юхан Аксель Эрикссон. В своих исследованиях он пытался вспучивать раствор извести, кремнезёмистых компонентов и цемента за счёт взаимодействия этого раствора с алюминиевым порошком. Этот подход увенчался успехом. В 1929 году в местечке Иксхульт фирмой «Итонг» (Ytong) был начат промышленный выпуск газобетона. Инженерами этой фирмы за основу была взята технология тепловлажностного воздействия в автоклавах на известково-кремнезёмистые компоненты, запатентованная в 1880 году немецким профессором В. Михаэлисом. Только за первый год работы этим предприятием было произведено 14 тысяч м³ газобетона (газосиликата). Следует заметить, что фирмой «Итонг» цемент не применялся вообще.
Несколько иной метод производства газобетона внедрила в жизнь в 1934 году шведская фирма «Сипорекс» (Siporex). Он основывается на применении смеси из портландцемента и кремнезёмистого компонента. Известь в данном случае не применялась. Авторы этого метода — инженеры финн Леннарт Форсэн и швед Ивар Эклунд. Научные и практические достижения вышеперечисленных инженеров и стали впоследствии основой промышленного производства как газосиликатов, так и газобетонов во многих странах мира.
История производства ячеистых бетонов в СССР[править | править код]
Производство ячеистых бетонов в СССР стало активно развиваться в 1930-е годы. Автоклавные ячеистые бетоны (АЯБ) с газовой поризацией появились в промышленных масштабах к 1950-м годам. К 1960-м годам производство АЯБ стало самостоятельным развивающимся научным направлением, во многом опережающим европейские наработки в этой области.
К концу 1980-х годов в СССР из ячеистых бетонов было построено более 250 млн м² зданий различного назначения (жилых, общественных, производственных, животноводческих). При этом, несмотря на высокий уровень отечественных научных разработок, ориентиром для советской промышленности служили западно-европейские достижения (понижение плотности панелей и блоков вплоть до 300 кг/м³), основанные, в первую очередь, на стабильном сырье и оборудовании, обеспечивающем высокую однородность материала.
В 1987 г. с принятием очередной жилищной программы СССР основным средством её реализации стала научно-производственно-техническая программа «Система эффективного строительства жилых и общественных зданий из ячеистых бетонов», которая предполагала строительство около 250 новых заводов по производству АЯБ с доведением общего его выпуска к 1995 г. до 40-45 млн м³/год.
Планы по этой программе предусматривали не только механическое наращивание объёмов выпуска автоклавных бетонов. Важной задачей было также и снижение средней плотности выпускаемой продукции (для блоков она составляла 600—700 кг/м³). В программе говорилось: «Таким образом, семикратное увеличение производства ячеистых бетонов в нашей стране следует сопровождать двукратным снижением их объёмной массы».
К 2011 году производство ячеистого бетона в России составило более 3,2 млн м³/год, количество заводов-производителей АЯБ — более 80, до 2015 года планируется к запуску 10.
- ГОСТ 25485-89 «Бетоны ячеистые»
- ГОСТ 21520-89 «Блоки из ячеистых бетонов стеновые мелкие»
- СН 277-80 «Инструкция по изготовлению изделий из ячеистого бетона»
- ГОСТ 31359-2007 «Бетоны ячеистые автоклавного твердения. Технические условия»
- ГОСТ 31360-2007 «Изделия стеновые неармированные из ячеистого бетона автоклавного твердения»
ru.wikipedia.org
Производство газобетона: оборудование, организация мини-завода
Современная строительная индустрия отличается совмещением традиционных методов строительства с новейшими технологиями возведения построек. Применение ячеистых бетонов существенно повысило эффективность гражданского строительства и улучшило качество строительных работ. Широко развернутое производство газобетона для нужд частного домостроения подчеркивает возросшую популярность среди застройщиков бюджетных вариантов стеновых материалов с достаточно высокими прочностными и теплоизоляционными свойствами.
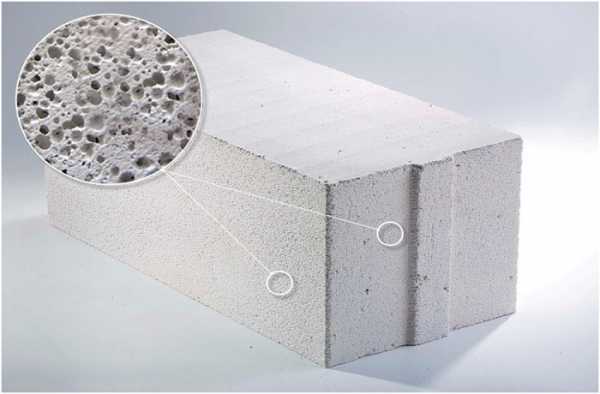
Газобетон
Физико-механические свойства газобетонных изделий
Одним из таких востребованных строительных стеновых материалов является газобетон, используемый при возведении малоэтажных жилых домов и хозяйственных построек. Из-за своей пористой структуры он является ячеистым бетоном и представляет собой искусственное пористое камнеподобное образование.
Производители газобетона выпускают газобетонные изделия в виде блоков различной конфигурации, соответствующих требованиям следующих стандартов:
- ГОСТ 31359-2007, устанавливающего требования к ячеистым бетонам, предназначенным для производства стеновых блоков и панелей, плит, перемычек и других строительных элементов;
- ГОСТ 31360-2007, регламентирующего требования к стеновым изделиям, изготовленным из ячеистого бетона.
ГОСТ 31359-2007 определяет газобетонные материалы как разновидность ячеистых бетонов, отличающуюся от других ячеистых материалов способом порообразования (п.4.2). По своей структуре газобетонное изделие напоминает своеобразную бетонную «губку», состоящую из мелких пузырьков-ячеек диаметром не более 3 мм.
Благодаря мелкопористой структуре, блочные изделия, которые способно выпускать современное оборудование для производства газоблоков, обладают физико-механическими свойствами, выгодно отличающими их от аналогичных изделий из других бетонных материалов:
- малым удельным весом;
- низкой теплопроводностью;
- огнестойкостью;
- устойчивостью к воздействию грибков и плесени;
- простотой механической обработки;
- технологичностью изготовления и применения.
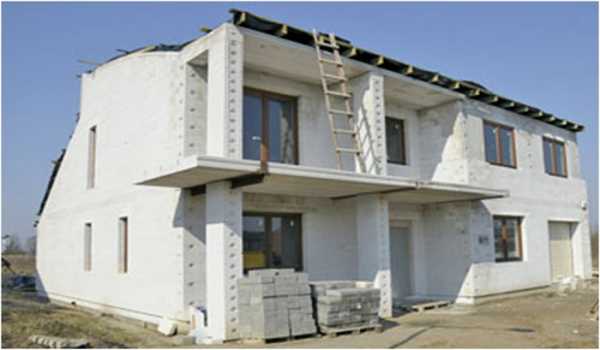
Завод по производству газобетона
Преимущества
В качестве технико-экономических достоинств газобетонных материалов отмечают следующие аспекты:
- Вес строительных газобетонных блоков в несколько раз меньше веса аналогичных изделий из кирпича или бетона. Газоблок стандартных габаритов 300х250х600 мм весит всего лишь 30 кг, что более, чем в 3 раза меньше веса такого же объема кирпичей размерами 60х125х250 мм.
- Простота обработки изделий обычными механическими инструментами допускает подгонку блоков в процессе возведения построек для улучшения качества сборки.
- Высокие тепло- и шумоизоляционные качества стен из газобетонных блоков обеспечивают комфортное проживание в жилых постройках.
- Надежная огнестойкость по отношению к открытому пламени обеспечивает пожаробезопасность строения.
- Высокая технологичность строительства при использовании газоблоков повышает эффективность и качество работ.
- Доступная стоимость газоблоков обеспечивает им должную конкурентоспособность на рынке стройматериалов.
- Возможность организации изготовления газоблочной продукции как частного бизнеса, поскольку реальная цена производства газобетона, мини-завод или оборудование линии конвейерного типа сравнительно доступны. Технологичность производства газобетонных материалов создает предпосылки для ведения бизнеса с высокой рентабельностью.
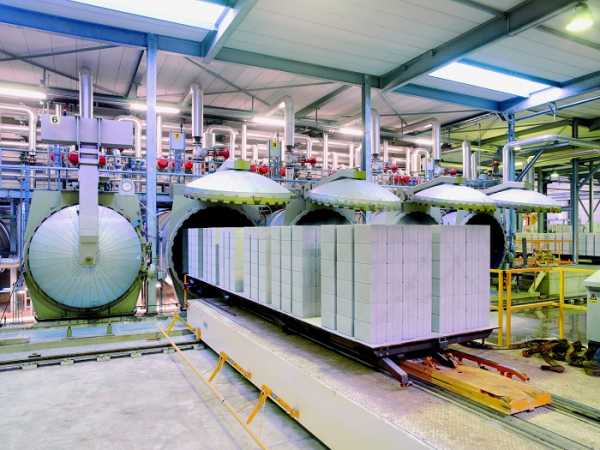
Производство газобетона
Технология изготовления газобетона
Исходными компонентами, которые применяют производители газобетонных блоков при изготовлении ячеистого газобетонного материала, являются:
- Портландцемент в пропорциях 50 — 70% от объема подготавливаемой смеси;
- Известь – не более 5% от объема смеси;
- кварцевый песок фракции, не превышающей 2,1мм, пропорции в смеси – 20-40%;
- вода – 0,8-1,0%;
- комплексные газообразующие добавки в пределах от 0,04 до 0,09%.
Базовая технология получения газобетона состоит из нескольких этапов:
- Этап 1 – дозирование основных компонентов – цемента, песка, извести — в соответствии с пропорциями заданного рецепта газобетонного материала.
- Этап 2 – подача основных компонентов и воды в специальный газобетоносмеситель. Тщательное перемешивание компонентов до получения высокогомогенной смеси.
- Этап 3 – добавка в приготовленную смесь газообразователя (чаще всего газообразователем является водная суспензия алюминиевой пудры). Процесс поризации смеси. Это важно! В процессе химического взаимодействия металлического алюминия, составляющего основу пудры, с известковым и цементным растворами выделяется свободный водород в виде газовых пузырьков, которые «вспучивают» цементное тесто. Оборудование для газобетона должно обеспечивать равномерное по объему смеси газовыделение, чтобы получилась однородная пористая структура.
- Твердение газобетонной смеси в специальных формах, нарезание блоков требуемой конфигурации. Форму готовым изделиям можно придать самую разнообразную – от традиционных параллелепипедов до U-образных или арочных блоков.
В зависимости от вида обработки твердеющей газобетонной массы выделяют два способа изготовления газоблоков:
- неавтоклавный способ, при котором созревание полуфабрикатов изделий до набора регламентируемой прочности протекает естественным образом без принудительного воздействия внешних факторов;
- автоклавный способ или автоклавирование, при котором изделия подвергаются воздействию давления при повышенной температуре в автоклавных камерах.
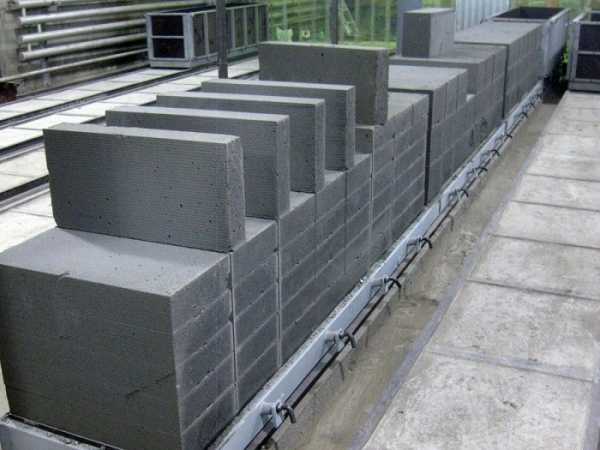
Производство газобетона
Особенности автоклавирования газобетонных блочных изделий
Если в состав оборудования, которым оснащен завод газоблоков, входит автоклавная камера, то продукция автоклавного твердения намного превосходит по показателям качества изделия, изготовленные по неавтоклавной методике. Усадка автоклавных блоков в процессе эксплуатации не превышает 0,5 мм/м, тогда как аналогичный показатель для неавтоклавных стеновых блоков доходит до 5 мм/м. Предел прочности на сжатие автоклавных газобетонных материалов достигает 3,2 МПа, для неавтоклавных материалов – не более 1,0 МПа. У газоблоков автоклавного твердения устойчивая однородная структура, что предопределило их эксплуатационные свойства как универсального строительного материала. Стеновые постройки толщиной 375-400мм, возведенные из газобетонных изделий, неплохо себя зарекомендовали в российских погодных условиях без дополнительного утепления.
Принцип автоклавирования ячеистого стройматериала заключается в размещении уже отформованных изделий в автоклаве, в котором блоки длительное время будут находиться под воздействием повышенного давления (до 1,2 МПа) и проходить обработку водяным паром при температуре 190-191 град. Ц. Подобные условия инициируют реакции, укрепляющие структурную плотность материала и повышают его прочность.
Техническое оснащение газобетонного производства
Для запуска производственной деятельности по изготовлению газобетонных изделий комплектуется технологическая линия по производству газобетона, в состав которой входят следующие функциональные элементы:
- дозаторы компонентов газобетонной смеси;
- газобетоносмеситель (миксер-активатор) для приготовления газобетонной вспененной смеси;
- формы под заливку вспененной газобетонной смеси и последующего твердения;
- устройства для резки газоблоков;
- тележки для перемещения готовой продукции на складирование.
Для работ по автоклавной технологии линия оснащается автоклавной камерой и системой автоматического управления и регулирования режимов работы автоклава.
До того, как организовать мини-завод производства газоблоков или иной газобетонной продукции, необходимо определиться с производительностью технологической линии. От этого зависит техническое оснащение производственного участка или завода и степень автоматизации регламентируемых технологических операций. Для выпуска строительной продукции в промышленных масштабах потребуется совершенно иное оборудование, чем для малого производства или под изготовление газоблоков в кустарных условиях. Производственно-технологические линии по выпуску газобетонной продукции подразделяют на три категории.
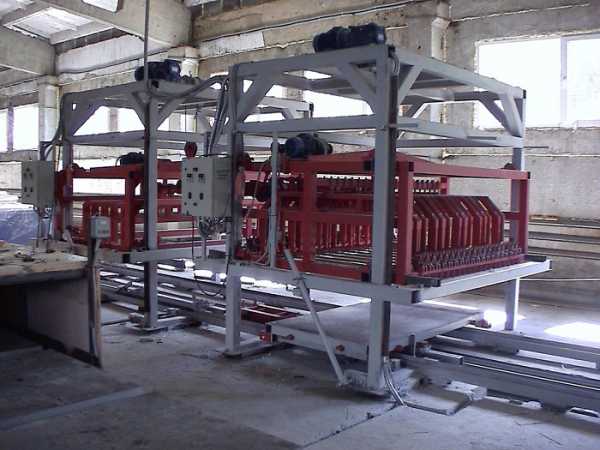
Производство газобетона
Мини-линии
1. Мини-линии, представляющие собой мини-заводы производственной мощностью 15-25 куб. м/сутки газобетонной продукции. У них низкая степень автоматизации техпроцессов. Обслуживанием исполнительных механизмов занимаются 2-3 работника. Производственные площади мини-заводов не превышают 140-160 кв. метров. В состав основного оборудования входят:
- газобетоносмеситель;
- устройства для резки твердеющей смеси;
- формы, лотки для созревания газоблоков;
- рельсовые пути и тележки для транспортировки готовой продукции.
В мини-заводах используются смесители передвижного типа, которые после замеса газобетонной смеси подкатывают к неподвижным стационарным формам для заполнения их приготовленной смесью.
Цена оборудования для производства газобетонных блоков на таких линиях может существенно возрасти при оснащении ее дополнительными опциями, например, компрессором для подачи воздуха в целях более качественного размешивания бетонной смеси или автоматизированными дозаторами.
Линии стационарного типа
2. Линии стационарного типа производственной мощностью от 30 до 60 куб. метров/сутки. Завод газобетона такого типа оснащен стационарным газобетоносмесителем, к которому передвижные формы-тележки подъезжают для заполнения вспененной газобетонной массой. Уровень автоматизации производства довольно высокий, что позволяет привлекать к работе одного-двух рабочих. Производственные площади стационарных линий не превышают 500 кв. метров.
Линии конвейерного типа
3. Линии конвейерного типа производственной мощностью от 75 до 150 куб. метров/сутки. Несмотря на высокую степень автоматизации управления техпроцессами, для обслуживания комплекса требуются не менее 8 человек обслуживающего персонала. Площадь , которую занимает конвейерный завод по производству газобетонных блоков, превышает 600 кв. метров.
Организационные вопросы при открытии газобетонного производства
Открытие завода по производству газобетона потребует оформления ряда документов, связанных со спецификой изготовления и реализации газоблоков. Если используется оборудование для производства газобетона в кустарных домашних условиях без применения автоклава, то никаких разрешительных документов на такие работы не потребуется. В постановлениях Правительства РФ от 13.08.97 за №1013 и Госстандарта РФ от 08.10.2001 г., определяющих перечни продукции, подлежащей обязательной сертификации, блоки из ячеистого бетона и оборудование для их изготовления отсутствуют. Однако в случае применения автоклавной технологии производителю необходимо получить разрешение от органов Госгортехнадзора, эксплуатация оборудования проводится при повышенном давлении. Отдельно необходимо получать разрешения от пожарной службы, поскольку электрическая мощность автоклавного агрегата составляет 5-10 кВт. Свои замечания может дать горСЭС, поскольку использование алюминиевой пудры должно предусматривать возможность утилизации газообразующей суспензии на ее основе.
Еще не так давно производить газобетон и другие ячеистые бетоны могли только крупные специализированные предприятия, располагающие дорогостоящим оборудованием.
Внедрение новых техпроцессов значительно упростило изготовление столь востребованных материалов, что дало толчок к развитию производства газобетонных изделий силами малого и среднего бизнеса.
Если вы нашли ошибку, пожалуйста, выделите фрагмент текста и нажмите Ctrl+Enter.
biztolk.ru