этапы производства и сборки (фото и видео)
Строя дом для своей семьи, мы стараемся выбирать для него качественные материалы. Предпочтение отдается натуральным, но вместе с тем, произведенным с учетом современных требований к долговечности, надежности, внешнему дизайну продуктам. Появившаяся сравнительно недавно технология производства клееного бруса возобновила интерес к строительству деревянных домов, от которых раньше многие отказывались в пользу кирпичных, каменных или блочных.
Безусловно, все перечисленные выше материалы обладают своими достоинствами и идеально подходят для строительства прочных, красивых и современных домов. Но, все же, они не могут сравниться с деревом по тому уровню комфорта и уюта, которое испытываешь, находясь в деревянном строении.
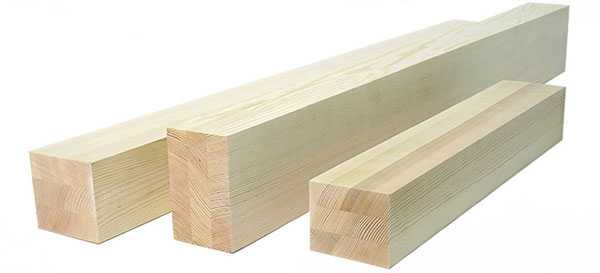
Фрагмент сруба из клееного бруса
Можно ли считать клееный брус натуральным материалом? Как он производится, чем отличается от обычного, и почему стал так популярен среди строителей и тех, кто мечтает о собственном доме?
Производство клееного бруса
Предпосылки появления технологии
Для начала разберемся, как и почему вообще появилась технология клееного бруса, чем этот материал отличается от аналогичного изделия, просто вырезанного из цельной древесины.
Всем хорошо известно свойство дерева усыхать и деформироваться в процессе эксплуатации. Построенные из него дома в результате этого процесса дают серьезную усадку, иногда достигающую 15-18% от первоначальной высоты. Усадка в свою очередь приводит к деформации всего строения и его конструктивных элементов, например, оконных и дверных блоков.
Кроме того, со временем на древесине появляются внешние дефекты – трещины, выпавшие сучки, синева, что требует проведения защитных и профилактических мероприятий.
Клееный брус лишен всех этих недостатков. Его появление возродило деревянное зодчество, а технология сборки дома из клееного бруса позволила упростить сам процесс строительства, сократить его сроки и продлить жизнь деревянным домам. Достичь этого удалось благодаря разработке целого комплекса последовательных мероприятий по обработке натуральной древесины. (см. также статью Какими преимуществами отличается клееный брус из кедра)
Этапы производства
Следует отметить, что для выпуска клееного бруса требуется сложное высококачественное оборудование – создать его своими руками в кустарных условиях просто невозможно.
Процесс состоит из нескольких технологических этапов:
- Сортировка древесины. На этом этапе происходит тщательный отбор исходного сырья: его разделяют по породам, сортам, размерам и другим важным параметрам.
Для справки. Сортировка сырья регламентируется нормативными документами.
В частности, ГОСТ 8486-86.
- Сушка. Древесину помещают в специальные сушильные камеры, оснащенные современным оборудованием. В них под непрерывным контролем пиломатериалы просушиваются до заданных значений влажности. (см. также статью Сухой профилированный брус: виды и применение)
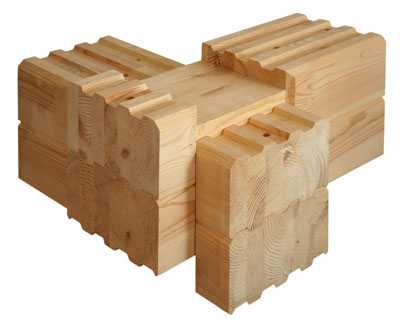
Подача древесины на сушку
- Изготовление заготовок. Этот процесс состоит из двух этапов. Сначала высушенная древесина направляется на станки, которые аккуратно вырезают из неё все дефекты, поврежденные участки. После чего она нарезается на ламели, которые сращиваются по длине.
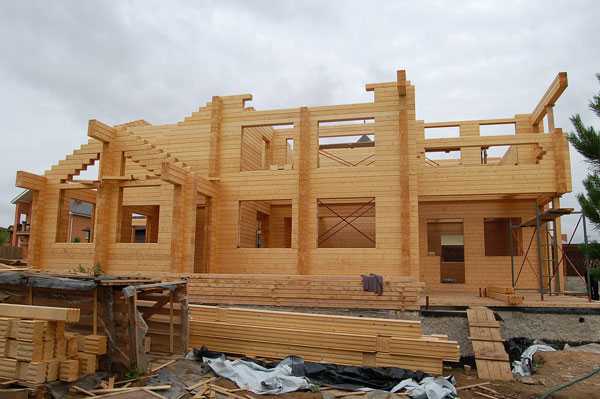
Заготовка для бруса
- Склеивание. Смазанные экологически чистым клеем заготовки соединяются и помещаются под мощный пресс. Клей под давлением проникает во все поры дерева, прочно скрепляя ламели друг с другом. Количество ламелей в брусе зависит от его проектной толщины.
Обратите внимание. Чаще всего клееный брус полностью состоит из одной породы дерева.
Но существуют сорта с одной или двумя внешними ламелями из более дорогой древесины.
Соответственно, их цена также будет выше.

Срез бруса с лицевыми поверхностями из кедра
- Профилирование. На этом этапе заготовки бруса нарезаются по длине и строгаются, а затем направляются на специальные станки, которые вырезают в теле заготовки замковые соединения – точно выверенные по размерам пазы. Технология сборки сруба из клееного бруса благодаря наличию этих идеально подходящих друг к другу пазов и шипов позволяет обходиться без применения уплотнительных материалов в швах между венцами.

На фото хорошо видна система шипов и пазов
- Упаковка. Готовый брус перед отправкой на склад или в торговую сеть упаковывают, чтобы предотвратить механические повреждения и загрязнение поверхности.
Некоторые производители помимо самого бруса производят изготовленные аналогичным способом детали, облегчающие стыковку стен в углах, монтаж перекрытий, установку дверных и оконных блоков.
Преимущества клееного бруса
Помимо перечисленных выше, клееный брус обладает и другими достоинствами, делающими его очень востребованным на строительном рынке.
- Хорошо высушенная и нарезанная на ламели древесина, являющаяся сырьем для производства, прекрасно впитывает в себя защитные средства, предохраняющие её от гниения и препятствующие возгоранию.
- Технология производства клееного и профилированного бруса позволяет создавать изделия с точно выверенными геометрическими параметрами и обеспечивать их плотное соединение друг с другом без зазоров и щелей, что благоприятно сказывается на внешнем виде и сохранении тепла в домах, помогает экономить на их отоплении.

Соединение венцов
- Вместе с тем эта технология не нарушает природную структуру дерева, сохраняя его способность регулировать уровень содержания кислорода в доме, комфортную влажность и температуру.
- При строительстве домов из клееного бруса может не соблюдаться инструкция, требующая сделать перерыв для естественной усадки до того, как приступить к отделочным работам. Поэтому здание можно возвести и сдать в эксплуатацию очень быстро.
- Наконец, гладкая и ровная поверхность позволяет вообще обойтись без отделки, оставив стены в первозданном виде.
Заключение
Современные технологии подарили людям возможность строить дома из качественных и долговечных, и вместе с тем натуральных материалов. К ним относится и клееный брус, обладающий всеми преимуществами цельного дерева, но отличающийся постоянством геометрических размеров, отсутствием дефектов и высоким качеством лицевой поверхности. (см. также статью Как создаются проекты домов и коттеджей из бруса)
Если вы хотите узнать больше об этом материале, видео в этой статье предоставит интересные сведения.
1brus.ru
Технология производства клееного бруса
Зачем человеку нужен комфорт? Ответ прост – так жить намного приятнее. Дом, который зимой отлично удерживает тепло, а летом спасает от изнуряющей жары – это комфортный дом. И построить его можно из клеевого бруса. Этот материал обладает прекрасными свойствами, которые он получает в процессе изготовления. Все этапы производства должны неукоснительно соблюдаться. Мы собрали для вас интересную информацию. Уделите чтению несколько минут и вы поймете, как делают качественный клееный брус.
Основные этапы производства
Производство клееного бруса – это сложный комплекс работ. Для его осуществления нужны:
- современное оборудование;
- профессиональные работники;
- качественная древесина;
- точное соблюдение всех технологических процессов;
- надежный контроль на каждом этапе изготовления.
Обеспечение этих условий приводит к позитивному результату. Сам технологический процесс производства клееного бруса можно разбить на такие основные этапы:
- Распиловка древесины на доски.
- Отбор полученного материала (ламелей).
- Сушка в специальных камерах.
- Строгание и повторная сортировка.
- Выторцовывание и маркировка ламелей.
- Фрезерование профиля.
- Торцевание по длине.
- Склеивание и прессование.
- Окончательная обработка (фрезерование и строгание).
Давайте подробнее рассмотрим все основные технологические операции по порядку.
1. Распиловка – с нее начинается производство
Продольная распиловка бревен – это первый этап производства. Из округлого бревна получают ламели — доски прямоугольной формы, которые в дальнейшем используются для производства бруса. Необрезные доски и горбыли, которые также образуются в процессе распиловки, отбраковываются.
2. Отбор – контроль очень важен
После распиловки производят отбор ламелей по длине. Характеристики клееного бруса зависят от качества древесины. Поэтому на этом этапе производится внешний осмотр и разделение ламелей по сортам и партиям. У добросовестных производителей брус одной партии всегда идентичен по своим физическим и визуальным параметрам.
3. Сушка – зачем она нужна
Высушивание ламелей производится в специальных камерах. В зависимости от типа производимого бруса и вида применяемого клея, остаточная влажность высушенных заготовок может составлять от 8 до 12%. Качественное выполнение этого этапа производства позволяет в будущем избежать усушки готового бруса после строительства дома.
4. Строгание ламелей и их сортировка – определяем прочность
После просушивания выполняют строгание ламелей. Им придают окончательную форму и производят повторную сортировку. Повторный отбор делают для определения прочности заготовок. Существует специальный стандарт DIN 4074-S10, который должен строго соблюдаться.
5. Выторцовывание и маркировка — долой бракованные участки
Древесина – это натуральный материал. Поэтому внутри любого бревна могут находится скрытые участки, которые подлежат удалению в процессе производства бруса. К таким дефектам относятся:
- трещины;
- большие сучки;
- неровности кромок;
- откосы.
При их выявлении производят выторцовывание и маркировку бракованных участков.
6. Фрезеровка профиля – зачем ее производят
В процессе производства заготовки (ламели) имеют различную длину. А в готовом виде профиль клееного бруса имеет строго определенные стандарты. Для того, чтобы получить ламели нужного размера, выполняют фрезерование профиля – на торцах ламелей вырезают зубцы нужной конфигурации.
7. Торцовка ламелей по длине – стандарты должны быть едиными
Длина клееного бруса зависит от стандартов производства. В отличие от обычного аналога, при изготовлении клеевого бруса возможно получить изделия любых размеров. Для получения необходимой длины проводят торцовку – склеивание ламелей по длине.
8. Склеивание и прессование клееного бруса – финиш уже близко
Нанесение клея производят на специальных машинах. Тончайший слой клея (до 1% от объема готового бруса) обеспечивает прочное соединение ламелей в единое изделие.
Клей для клееного бруса бывает:
- меламиновым;
- резорциновым;
- полиуретановым.
Прессование позволяет получить заготовки различных размеров.
Наиболее часто встречается клееный брус сечением:
- 200х200 мм;
- 150х150 мм;
- 100х100 мм.
9. Строгание и фрезерование готового бруса – окончательная отделка завершена
Последним этапом производства является финишная отделка готовых изделий. После окончательного высыхания производят строгание и фрезерование. Шлифовка клееного бруса завершает технологический процесс.
Что такое утепленный клееный брус?
Теплопроводность клееного бруса крайне низка. Поэтому этот материал прекрасно подходит для строительства домов. Но на рынке встречается и утепленный клееный брус. Он значительно отличается от натурального аналога, потому что содержит вставки (блоки) из синтетических материалов и является, по сути, многослойной панелью.
Изготовление клееного бруса – довольно сложный и дорогостоящий технологический процесс. Осуществлять его грамотно могут лишь немногие предприятия. Поэтому при покупке клееного бруса особое внимание обращайте на производителя.
Следующее видео наглядно демонстрирует этапы производства клееного бруса:
derevo-s.ru
технология производства, домокомплекты, размеры, за и против, а также как изготовить своими руками
Клееный брус относится к современным видам пиломатериалов. При строительстве деревянных домов он выступает альтернативой оцилиндрованному бревну и профилированному брусу. Сложная технология производства приводит к удорожанию материала, однако взамен покупатели получают высочайшее качество и отличные эксплуатационные характеристики брусового дома.

Что это такое?
Клееный брус представляет собой комбинированный строительный материал. Его основой выступают пиленые доски, которые склеиваются между собой при помощи клеевых составов по специальной технологии. Для изготовления используются ламели, лишенные дефектов и сучков.
Клееный брус подвергается профилированию – это позволяет создать нужную геометрию среза для быстрого и эффективного возведения конструкций.
Также он лишен недостатков, присущих натуральному дереву, – горючести, склонности к деформациям и значительной усадке. Но благодаря современному подходу и использованию клеевых смесей материал приобретает дополнительные полезные свойства – высокую прочность, теплопроводность и стабильность размеров.
Дом из этого материала получается долговечным, теплым, уютным, с характерным микроклиматом натуральной древесины. И возвести его удается в максимально сжатые сроки.
Что лучше – обычный брус или клееный?
Делая выбор между традиционным профилированным брусом и клеевой разновидностью пиломатериала, следует остановиться на положительных свойствах первого.
К достоинствам профилированного бруса можно отнести тот факт, что он представляет собой цельный массив дерева. Это полностью натуральный стройматериал, обладающий высокой экологичностью. Он может обрабатываться растворами, препятствующими гниению и возгоранию, но вредных испарений и запахов они не издают.

Еще один плюс профилированного материала – низкая стоимость в сравнении с клееным видом. Последний обойдется примерно на 30% дороже.
К тому же в классическом брусе присутствует естественный воздухообмен, создающий в жилище особый микроклимат.
Но профилированный уступает клееному по вариативности размеров, уровням влажности и усадки, вероятности деформаций и частичной утрате свойств в ходе эксплуатации. Зачастую он требует отделочных работ для повышения эстетичности и периодической конопатки возникающих трещин.
Классификация
В строительстве применяется несколько разновидностей материала в зависимости от целевого назначения и конфигурации профиля.
Виды материала по назначению:
- Оконный и дверной. Производится из минимум 4 ламелей, используется на участках монтажа оконных и дверных проемов.
- Стеновой. Количество ламелей достигает 2-3, его используют для возведения стен в одноэтажных домах и постройках с мансардой.
- Опорный. Вид с наибольшей несущей способностью. С его помощью конструируют каркасы зданий, балки перекрытия и несущие опоры.
Наиболее востребованные для строительства параметры стенового бруса – 100-160*180 и 180-270*260 мм.
Стеновой брус может изготавливаться с использованием теплоизоляционного слоя или без него.
Виды по типу профиля:
- гребенка – оснащен мелкими зубьями, нарезанными по бокам изделия;
- финский профиль – образует соединение “шип-паз”, его поверхность практически плоская;
- немецкий профиль – имеет от 4 до 8 соединительных пазов, образует самый крепкий модуль.
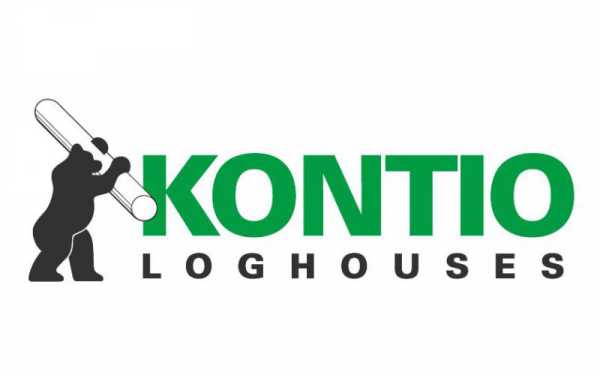
Домокомплекты от производителя
Домокомплект из бруса – это строительный набор, состоящий из нескольких сотен элементов, предназначенных для возведения постройки. По сути это готовые дома в разобранном виде.
Важно! Установка домокомплекта из клееного бруса производится только на устоявшийся фундамент.
Все детали комплекта имеют строго выверенные размеры, выполненные в соответствии с архитектурным проектом. Элементы подогнаны друг к другу, что значительно упрощает и ускоряет строительство.
В сборку входят:
- окладной венец;
- межэтажные перекрытия;
- основание под кровлю;
- стропильная система с обрешеткой;
- столбы, лаги, балки;
- наружные и внутренние стены;
- чистовой и черновой пол.
В набор входит сборочная документация с подробной схемой сборки. Каждая деталь должна быть пронумерована и упакована.
Производство клееных брусьев

Сейчас современные клееные пиломатериалы изготавливаются по всему миру серийно.
Полученное изделие обработано и полностью готово к использованию.
Сырье для изготовления
Производители предпочитают использовать хвойные породы деревьев по причине их доступности и низкой стоимости. В работу идут стволы сосны, ели и лиственницы, за рубежом применяется древесина кедра и пихты. Из-за высокой стоимости сырья брус из дуба и ясеня может изготавливаться только под заказ.
В производстве многослойного бруса часто комбинируют натуральные материалы. Для наружных слоев используются ель и сосна – структура их древесины более однородная. Для внутренних вставок применяются лиственница и кедр – они характеризуются высокой прочностью.
Больше всего ценится сырье из северной древесины – у нее высший класс прочности.
Виды клея
Для изготовления клееных брусьев используется несколько видов клея. Они отличаются классами водостойкости, эксплуатации и экологической безопасности.
- Меламиновый. Прозрачный клей, применяется в российском и европейском производстве для строительства большепролетных конструкций.
- Резорциновый. Темный состав с повышенной влагостойкостью, им склеивают наружные части бруса для эксплуатации в условиях повышенной влажности. Этот вид материала применяется изготовителями США в судостроении, возведении мостов и открытых конструкций.
- EPI-система. Прозрачный клеевой состав, применяется в малоэтажном строительстве Японии и России.
- Полиуретановый. Имеет прозрачную структуру, быстро затвердевает. Подходит для склеивания оконных и дверных брусьев.
Стандарты качества
Производство клееного бруса не требует подготовки лицензии. Но продукция должна соответствовать стандартам качества, подтвержденным соответствующими сертификатами.
Государственные стандарты на клееный брус:
- ГОСТ 20850-84 “Конструкции деревянные клееные. Общие технические условия”;
- ГОСТ 16588-91 “Пилопродукция и деревянные детали. Методы определения влажности”;
- ГОСТ 19414-90 “Древесина клееная массивная. Общие требования”;
- ГОСТ 25884-83 “Конструкции деревянные клееные. Метод определения прочности клеевых соединений при послойном скалывании”;
- ГОСТ 15613.4-78 “Древесина клееная массивная. Методы определения предела прочности зубчатых клеевых соединений при статическом изгибе”.
Технология изготовления
- Подготовка сырья. Невысушенную и необрезанную доску сортируют, распиливают на заготовки по заданным параметрам, очищают от коры и отправляют на просушивание в камеры. Финишная влажность доски не должна превышать 8-12%.
- Удаление дефектов и калибровка. Каждую доску обрабатывают на четырехсторонних станках. Это позволяет устранить остатки обзола, сучки, трещины и прочие дефекты.
- Шлифовка. Проводят чистовую обработку ламелей с обеспечением геометрической точности и плотности прилегания заготовок.
- Склеивание. Клеенаносящая машина подает клей на поверхность широкой стороны заготовки равномерным слоем. Затем ламели прессуют в цельный брус под давлением от 15 кг/м2 в течение 30 минут.
- Профилирование. На сторонах бруса производятся надпилы в виде шипов, гребней, пазов в соответствии с запланированной конфигурацией.
- Обработка защитными составами. Готовые изделия пропитывают смесями, которые препятствуют горению и гниению клееного бруса.

Готовая продукция проходит проверку на качество и упаковывается для отгрузки или хранения.
Зачем изготавливать своими руками?
При наличии нужного инструментария можно самостоятельно изготовить брус клееного типа. Это позволяет получить материал нестандартных габаритов, которые в продаже не встречаются.
Изготовление своими руками поможет отрегулировать слои бруса по прочности, податливости, длине, ширине, типу поверхности. Его можно использовать для отделочных работ, реставрации мебели и прочих мелких работ, где закупка больших партий клееного бруса нецелесообразна.
Обратите вниманиеДля изготовления подойдут обычные доски или рейки из строительного супермаркета.
Для более тщательной и точной обработки применяются фрезерные станки и шлифовальные машины, но в домашних условиях можно обойтись ножовкой по дереву и рубанком. Особенно тщательно обрабатывают поверхности, подлежащие склейке – их шлифуют, убирают пыль и обезжиривают.
Склеивание проводят при помощи готового клея, который можно купить в торговых точках. Необходимо строго следовать инструкции по нанесению и просушке клея.
Для фиксации и сжатия склеенных деталей используют струбцины. После просушивания готовый брус окончательно обстругивают и шлифуют.
Что такое финский клееный брус?
К финским типам профиля относят срезы со сложной конфигурацией и утеплением. Нижний край такого бруса оснащен соединительными шипами, а на верхнем крае располагаются пазы, соответствующие шипам по размерам. Расположенная между шипами ступенчатая канавка в середине глубже, по краям – мельче.
По краям канавки размещают уплотнительный материал, а в центр помещают теплоизоляционную синтетическую ленту. С боков канавка прикрывается скошенными кромками верхнего бруса. Такое исполнение позволяет добиться высокого уровня теплоизоляции, избежать попадания влаги и продувания конструкции.
Данный вид утепления является трудоемким и дорогостоящим. Упрощенные и бюджетные варианты предполагают уплотнение только по центру или только по бокам. Это тоже позволяет добиться хороших показателей непродуваемости.
Преимущества и недостатки материала
Востребованность клееного бруса растет с каждым днем. Это объясняется многочисленными положительными свойствами и достоинствами материала:
- Минимальный процент усадки, что позволяет не дожидаться усадки дома, а сразу же сдавать его в эксплуатацию.
- Отличные теплоизолирующие свойства, зачастую не уступающие кирпичу.
- Не требует отделки – поверхность бруса ровная и гладкая, не имеет трещин и дефектов.
- Брус не подвержен горению, гниению, червоточинам и грибковым поражениям.
- Сохраняет геометрические пропорции, не деформируется и не меняет форму.
- Клееный брус прост в монтаже, что в разы сокращает процесс возведения постройки.
- При условии грамотного монтажа обеспечивается высокая влагонепроницаемость и устойчивость к проникновению ветра.
- Не имеет ограничений по длине, а толщина изделия может включать до десяти ламелей.
- Небольшой вес изделий не требует задействования специальной строительной техники.
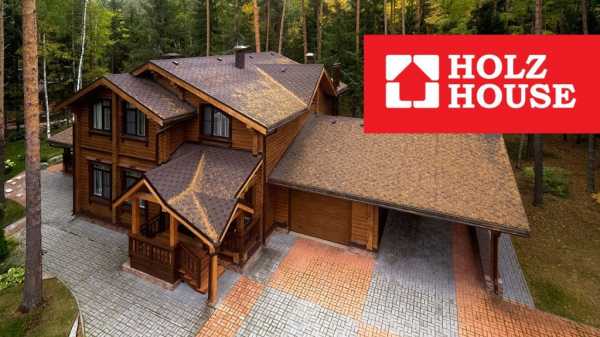
Недостатки клееного бруса:
- Высокая стоимость пиломатериала по сравнению с оцилиндрованным бревном и профилированным брусом.
- Необходимость поддержания в жилище определенного уровня влажности при отсутствии перепадов температур.
- Низкая воздухопроницаемость конструкций.
- Потребность в дополнительной теплоизоляции в процессе строительства.
Некоторые производители используют для склеивания синтетические составы низкого качества, что значительно снижает экологичность изделий из бруса.
Полезные видео
Характеристика и особенности материала, советы и рекомендации специалиста, смотрим:
Посмотрите все этапы производства клееного бруса — от распиловки леса и сушки заготовок до зарезки угловых соединений и покрытия защитными составами:
На видео ниже — достоинства и недостатки домов из клееного бруса, особенности сборки:
Существенные преимущества клееного бруса делают его популярным и эффективным стройматериалом для возведения долговечных строений. Высокая цена окупается красивым внешним видом постройки снаружи, комфортной и уютной атмосферой внутри.
domavlad.ru
технология изготовления клееного бруса от GoodWood
Клееный брус, в отличие от других материалов, является высокотехнологичным продуктом. Соответственно, для производства качественного клееного бруса необходимо строгое соблюдение технологии. Наша компания пришла к тому, что без собственного производства клееного бруса нам не обойтись. Только в этом случае мы можем гарантировать, что брус соответствует техническим условиям, т.е. со временем не треснет, не потемнеет и его теплоизоляция будет на должном уровне. На сегодняшний день производственные мощности компании GOOD WOOD насчитывают 2 собственных завода в Зеленограде общей площадью 10 000 кв. м.
Технология производства клееного бруса поэтапно:
- Первая торцовка
- Распиливание бревна (бревно — доски)
- Сушка
- Вскрытие дефектов (первое строгание)
- Оптимизация (доски — ламели)
- Сращивание (ламели — плети)
- Второе строгание (рейсмусование)
- Нанесение клея
- Прессование (плети — клееный брус)
- Профилирование (клееный брус — клееный профилированный брус)
- Торцовка
- Зарезание чашек (пазов)
Спрос на эту продукцию в последнее время сильно возрос, и, как обычно у нас происходит, появилась целая индустрия по выпуску некачественных материалов. Их использование резко снижает эффект от вложенных средств.
В активе компании новейшее оборудование от ведущих европейских производителей, сушильные камеры MuhlbockVanichek, производственные линии от лидеров — Hundegger и SMB, мы также используем при изготовлении немецкое и американское оборудование Weinig и Leademac. Качество обработки и точность у этих станков не может сравниться с лучшими немецкими станками. Для того чтобы при изготовлении бруса на дешевых станках обеспечить вхождение шипов в пазы, необходимо увеличивать зазоры, что ведет к ухудшению теплоизоляционных свойств.
Завод по производству клееного бруса GOOD WOOD полностью автоматизирован, на каждой стадии происходит автоматический контроль качества. Это позволяет свести процент брака к минимуму. Мы сушим древесину с использованием мягких режимов сушки при влажности 8–10 %.
Строгие стандарты качества и технические условия, прин
www.gwd.ru
Как это сделано? Производство клееного бруса для деревянных окон
Наш завод работает с крупнейшим в России поставщиком оконного клееного бруса. Сейчас мы вам подробно расскажем и покажем (см. видео в конце этой статьи!) как организован весь процесс производства! Рассказ начнём с того, что предприятие занимает 17Га площади и основной своей продукцией считает именно многослойный оконный брус с использованием ламелей радиального распила. В качестве основного материала используются Ангарская сосна и Сибирская лиственница.
95% продукции поставляется на Европейский и Скандинавский рынки, а 5% идёт на Российский рынок. Так что можно сказать, что Чехия, Италия, Германия, Австрия, Швейцария, Бельгия, Норвегия, Швеция, Франция использует ровно такой же оконный брус при изготовлении окон, что и наш завод поставщик в Санкт-Петербурге (Пушкине). В 2009 году, первыми в России, производством был получен сертификат IFT Немецкого института оконных технологий (г. Rosenheim, Бавария). Можно утверждать, что этот институт является гарантом качества продукции и полученный сертификат подтверждает, что продукция предприятия соответствует требованиям европейской директивы «Деревянные слоистые профили для оконных рам. − Требования и контроль»
Сортировка круглого леса
Весь пиловочник поставляется железной дорогой и буквально «с колес» отправляется на сортировку круглого леса. Отсортированный лес хранится на складе примерно в объёме месячного запаса.
Цех радиального распила
Далее круглый лес поступает на участок радиального распила. Все оборудование для этих целей (подача в цех, сортировка досок, удаление отходов + дополнительное оборудование) было полностью спроектировано и установлено немецкой компанией EWD.
Управление простое. Как в компьютерной игре 🙂 Пиу. Пиу.
Сырая сортировка
Пока распиленные сырые доски не попали в сушильный комплекс, их необходимо правильно отсортировать. С этой целью в лесопильном цехе установлена автоматическая линия для сортировки и штабелирования сырой доски. На этом же этапе осуществляется разбор досок и по размерам и по сортам качества: А, В и С.
Сушильно-котельный комплекс
В сушильном комлпексе 24 камеры (4 блока по 6 камер) фирмы Muehlboeck Vanicek. В каждую камеру загружается до 130 м3 пиломатериалов. Всем управляет умное програмное обеспечение, в котором содержится больше 200 программ сушки для разных пород дерева: от привычной сосны, до экзотических пород древесины.
В больших объёмах здесь сушат и лиственницу, известную не только своей прочностью и долговечностью, но и сложностью обработки, капризностью. Если проявить неаккуратность в технологии сушки лиственницы, то могут появиться трещины на торцах, коробление и проч. Кроме того, лиственница и сохнет дольше чем сосна.
Кстати сказать, топливом для собственной котельной, которая отвечает за тепло для сушильных камер является неизмельченная кора из лесопильного цеха.
Коры столько, что её вполне достаточно для получения тепловой энергии всему предприятию. Таким образом, опилки и щепа являются самым настоящим товаром и вполне себе реализуются на внутреннем рынке в качестве топлива.
Оптимизация древесины
После сушильных камер пиломатериалы так называемыми пакетами (типа как паллетами, но не паллетами :)) доставляются в так называемый буферный склад для дальнейшей деревообработки. За 2–3 дня нахождения на буферном складе древесина равномерно распределяет влажность и выравнивает температуру по отношению к окружающей среде.
Дальше начинается кропотливый труд по оптимизации древесины, который включает в себя предварительную острожку и вырезание глазков дефектных зон. Для этого система автоматической загрузки самостоятельно разбирает штабели и поштучно выдает доски на систему контроля влажности Brookhuis. Слишком влажные материалы снова отправляются на досушку, а подходящие материалы проходят четырёхстороннюю острожку на станке Hydromat 22B. Скорость обработки достигает 120 погонных метров в минуту!
Деревянное око
После 4-х сторонней обработки пиломатериалы поступают на оптический супер-мега-гига сканер WoodEye, который на невероятной для человеческого глаза скорости, сканирует весь входящий древесный материал на предмет дефектов и пороков. На основании собранных данных осуществляется разметка ламели и информация передаётся дальше на торцовочный станок OptiCut 350, где пороки вырезаются, сбрасываются на транспортёрную ленту и поступают в дробилку, а готовые заготовки без сучков и пороков продолжают свой путь в сторону клееного бруса.
Чистые ламели нарезаются на определенную длину (так называемые мерные длины), а также на более короткие заготовки (коротье) и поступают на транспортеры, где в зависимости от размера и сорта заготовки раздаются по соответствующим накопительным столам. Вся эта цепочка работает на очень приличной скорости и создаётся ощущение, что станки буквально стреляют заготовками.
Сращивание
Дальше всё собирается на десяти сортировочных столах и прямиком на участок сращивания GreСon. Сращивание оконного бруса осуществляется на вертикальный минишип.
Заготовки укладываются вручную с дополнительным контролем качества. Все остальные операции (клеенанесение, прессование) выполняются автоматом. Максимальная длина сращенной ламели может достигать 6,3 м.
Склеивание оконного бруса происходит на двух линиях Dimter:
- ContiPress 4500, с длиной прессования 4,5 м, на которой клеится брус 1 категории (две цельные ламели снаружи и средние сращенные)
- ContiPress 6300, с длиной прессования 6,3 м на которой клеится брус 3 категории (все ламели сращенные)
Доверяй, но проверяй. Несмотря на полностью автоматизированные и компьютеризированные процессы, вся клееная продукция проверяется визуально и при помощи люминисцентых карандашей отмечаются некачественные склейки, и тут же безжалостно выпиливаются: Ламели идут на переклейку.
Ламели для мебельного щита, сращиваются по длине на горизонтальный или вертикальный минишип на тех же участках цеха. Сложенные в пакет сращенные по длине ламели погрузчиком транспортируются на складские буферные зоны, где как минимум сутки выдерживаются для стабилизации клеевых соединений.
Мебельный щит производится на линии прессования ProfiPress PP 5500.
После склеивания щиты сортируются, штабелируются и передаются на линию торцовки и шлифования для окончательной обработки и придания товарного вида. Готовые мебельные щиты упаковывается в пленку и отправляются на склад.
Безусловно, при предприятии есть своя лаборатория, где анализу подвергаются не только сама древесина, но и качество склеивания шиповых соединений, проверяется уровень напряжений между ламелями и т.д.
Складирование готовой продукции
Ассортимент готовых изделий не заканчивается оконным брусом. На складе готоы к отгрузке уже упоминавшийся нами клееный щит, а также разнообразный профилированный погонаж, террасная доска (для солнечной Франции например), мелкореечный клееный брус, стеновой брус для строительство загородных домиков, экзотическая хагара (строганая доска из склеенного мелкореечного бруса) и другие продукты.
Большое спасибо, что дочитали до конца! Вот вам в награду обещанное видео:
oknasmart.ru
крупнейший завод по производству клееного бруса в России, изготовление домокомплектов из клееного бруса от производителя
Более 13 лет одна из крупнейших компаний Московской области и России «АПС ДСК» строит дома из профилированного клееного бруса.
Собственное деревообрабатывающее производство позволяет сделать жилье для наших клиентов доступнее.
Мы самостоятельно изготавливаем качественный клееный брус, используя оборудование от ведущих производителей
Германии, Италии, Финляндии и Швеции. Прочность и долговечность наших деревянных домов напрямую зависят от качества стройматериала, поэтому особое внимание мы уделяем технологии производства клееного бруса.
Узнайте, из каких технологических стадий состоит производство «АПС ДСК», и почему мы не боимся предоставлять гарантию более 10 лет.
СТадия №1 Подбор сырья для изготовления пиломатериалов
Наша компания не покупает пиломатериал у сторонних изготовителей, это приводит к удорожанию, не выгодно для клиентов и не гарантирует надлежащего качества сырья. Мы получаем древесину с собственных лесных делянок. При отборе сырья происходит тщательная проверка качества пиломатериалов с помощью силовых и акустических установок.
Далее отбираются внешне чистые ламели, которые подлежат дальнейшему склеиванию. Также на этом этапе отмечается вся древесина с пороками строения, вплоть до малейших трещин. Все дефекты, которые влияют на прочность ламелей, удаляются на высокоточных станках.
На каждом этапе изготовления профилированного клееного бруса в нашей компании действует независимый технический контроль. На этой стадии сотрудники ОТК передают в клееный только качественное сырье, соответствующее требованиям ГОСТ 24454-80, 26214-84, 8486-86.
Стадия №2 Сушка древесины — залог прочности и долговечности пиломатериала
От процесса сушки зависит насколько прочной и долговечной будет заготовка. Мы не применяем агрессивные методы сушки, вследствие которых пиломатериал высыхает только снаружи, образуя трещины и производственный брак.
На нашем производстве используются автоматические сушильные камеры INCOPLAN, которые проводят мягкую сушку древесины и дальнейшее кондиционирование ламелей. К дальнейшему обработке подвергаются только те экземпляры, которые достигли уровня влажности 8-12%.
Такие заготовки не растрескиваются и сохраняют целостность. Специалисты ОТК проводят проверку уровня влажности с помощью контрольных функций автоматических сушильных аппаратов, что гарантирует точность показателей.
Сушильные камеры для клееного бруса на заводе АПС ДСК
Стадия №3 Склеивание ламелей
На этой стадии необходимо правильно подобрать клеевой состав. Мы не экономим на клее для бруса, поэтому используем самый безопасный и качественный клей KIILTO. Такой состав обеспечивает надежную фиксацию древесины и полную безопасность бруса. Он не содержит агрессивных и вредных смол. Многочисленные сертификаты качества KIILTO подтверждают его безопасность для здоровья взрослого человека и детей.
На этой стадии служба ОТК уделяет внимание расположению ламелей относительно расположению годовых колец. Чтобы максимально уменьшить напряжение в готовом изделии, элементы должны располагаться симметрично. Далее материал проходит специальные испытания и ультразвуковое обследование по всей длине бруса для выявления некачественной склейки. Не прошедшие испытания элементы, не попадают на следующую стадию в цехе производства клееного бруса.
Грамотно склеенные ламели становятся надежным и долговечным строительным материалом. Он отличается экологичностью и устойчивостью к короблению. По сравнению с цельным брусом, клееный не меняет своих пропорций во время эксплуатации, дает минимальную усадку и создает полностью монолитную стену.
Стадия №4 Проверка качества профилирования заготовки
Для создания монолитной стены и полного исключения продувания венцов, необходимо точное профилирование примыкающих сторон бруса. Служба ОТК проверяет верность нахождения пазогребневых шипов. Главное отличие стройматериала АПС ДСК от других российских производств — самая большая высота шипа. Она обеспечивает надежное антипродувание и защиту от попадания влаги во внутренние пазы.
Дом из такого деревянного стройматериала возможно возвести за минимальное количество времени, так как на строительный объект поступает готовый стеновой комплект, который собирается словно конструктор LEGO. Правильное профилирование увеличивает прочность стен. Брус способен выдерживать большие нагрузки, так как разнонаправленные волокна ламелей уменьшают риск разрыва заготовки без механического вмешательства.
Стадия №5 Подготовка замков клееного бруса в соответствии с выбранным проектом
Для каждого проекта используются цельные заготовки с заранее заготовленными чашками (замками) для их соединения. Таким образом, на объекте нет необходимости подгонять материал “в размер”, отпиливать лишние метры или подбирать недостающие части бруса. Это значительно сокращает время строительства и увеличивает качество построенного объекта.
Нарезка чашек из клееного бруса по проекту на заводе АПС ДСК
Наше предприятие по производству домокомплектов из клееного бруса в заводских условиях производит нарезку замков и торцовку. Создаем замки по типу теплый угол, которое надежно защищает углы от промерзания. Зарезка на современных станках отличается точностью размеров и 100% соответствием требованиям утвержденного проекта. Надежная фиксация чашек соединения обеспечивает сохранность тепла в доме, не допуская промерзания или попадания влаги. Современный чашкорез позволяет получить максимально точный распил без применения ручного труда. Каждый элемент заготовки нумеруется в строгом соответствии с планом проекта дома.
Заключительный этап изготовления клееного бруса

Сотрудники ОТК тщательно осматривают всю партию клееного бруса.

Торцы стенового комплекта обрабатываются эпоксидным воском, что обеспечивает их защиту от растрескивания

Готовые стеновые комплекты упаковываются в защитную пленку и маркируются. Все это мы делаем бесплатно, чтобы вы получили клееный деревянный брус в идеальном состоянии
www.aps-dsk.ru
как изготовить клееный брус своими руками.
Самостоятельное производство клееного бруса позволяет решить множество проблем в доме, начиная с ремонта или реставрации мебели, и заканчивая крупными строительными или отделочными работами. Мне могут возразить, зачем клеить брус самому, если можно купить готовый? Отвечаю: не всегда клееный брус нужен в больших объемах, особенно при мелких работах, не всегда можно купить брус нужного размера, обычно продают брус стандартных размеров.
На самом деле почти невозможно купить брус с необходимыми параметрами. Например, если нужен крепкий брус (как конструктивный элемент), но при этом внешние поверхности бруса должны быть мягкими (например, будут подвергаться обработке: резьба по дереву, рельефная отделка и т. д.). Эта статья поможет вам научиться изготавливать клееный брус самостоятельно.
Несколько важных замечаний
1. Правильно изготовленный клееный брус по своим конструкционным, механическим и прочим параметрам превосходит цельный брус, изготовленный из того же дерева и с такими же размерами.
2. Современные клеевые составы для дерева, в случае их правильного применения, позволяют получить клеевой шов более прочный, чем само дерево. Я как-то хотел оторвать приклеенный брусок к столешнице. Дело кончилось тем, что сам брусок расщепился по длине, но в месте клеевого соединения не отстал ни на йоту.
3. Во многих случаях (в том числе в домашних условиях городской квартиры) изготовить клееный брус можно без использования специального дорогостоящего инструмента, если для его производства использовать покупные детали (половые рейки, доски).
Прежде чем перейти непосредственно к технологии изготовления клееного бруса, рассмотрим некоторые определения.
На рисунке ниже показаны основные детали клееного бруса и способы их соединения. На самом деле способов соединения много больше, но на рисунке указаны наиболее простые в изготовлении в домашних условиях. Важным условием для бруса является взаимное расположение годовых колец, ламели должны быть склеены таким образом, чтобы их взаимное расположение в изготавливаемом брусе было разнонаправленным у смежных ламелей. В этом случае, брус будет наименее подвержен короблению.
Технология изготовления клееного бруса в домашних условиях
Необходимые инструменты (перечень инструмента, конечно, зависит от того, какой брус вы хотите изготовить):
- Ножовка или двуручная пила
- Струбцины
- Строгальный инструмент (рубанок, электрорубанок, циркулярная пила)
- Фрезерный станок (циркулярная пила со сменяемыми фрезами), желательно, но не обязательно
- Шлифмашинка ленточная, желательно, но не обязательно
- Кисти малярные, щетки волосяные, синтетические
- Разметочные инструменты (рулетка, стальная метровая линейка, угольник и т. д.).
На фото представлен инструмент, без которого точно не обойтись (набор струбцин).
Необходимые материалы:
- Пиломатериалы (доски, брус, рейки)
- Клей по дереву или универсальный
- Растворитель 646 (ацетон) — для обезжиривания.
Технология изготовления клееного бруса будет рассмотрена на примере производства клееного бруса для изготовления оконных коробок дома.
Требования к исходному материалу. Применяемый пиломатериал должен быть сухим и здоровым. В данном случае я использовал брус из сосны и лиственницы (100 на 100 мм), который хранился под навесом, т. е. естественной сушки.
Нарезаем заготовки нужной длины, с припуском по 5 см с каждой стороны.
Отбираем три заготовки (ламели) для изготовления одного бруса. Что важно? Так как на первом этапе строгаются и фугуются только те канты (стороны) у ламелей, которые подлежат склеиванию, в которых будет выбираться паз, то необходимо заранее определить взаимное расположение ламелей таким образом, что бы рисунок годовых колец был разнонаправленным. Для соединения ламелей использовал соединение на шпонку. После острожки склеиваемых сторон, выбираем паз у крайних ламелей с одной стороны и у средней ламели два паза (по двум сторонам). По размерам пазов на циркулярной пиле делаем заготовки для шпонок.
После изготовления всех деталей будущего блока, для предварительной оценки, подгонки собираем брус на «сухую», без клея.
Подготовка склеиваемых поверхностей важная операция. В зависимости от применяемого клея порядок подготовительных действий может меняться (см. инструкцию на упаковке клея). Но основные операции, как правило, все же однотипны. Обычно необходимо:
- Сопрягаемые поверхности обработать наждачной бумагой или, что удобнее, шлифмашинкой.
- Обеспылить поверхность щёткой или пылесосом.
- Обезжирить (я использовал растворитель 646 и кисть), дать просохнуть.
- Все изготовленные детали (места стыков) обработать огнебиозащитой, за два раза с промежуточной сушкой.
После выполнения этих операций можно приступать к склеиванию бруса.
Склеивание бруса
Склеивание бруса процесс наиболее ответственный. Здесь особо важно правильно выбрать клей. Т. е в зависимости от того, где (на улице, в помещении) в каких условиях (влажность, температура) будет использоваться будущее изделие, а также в зависимости от требований к внешнему виду клеевого соединения (цвет клея) необходимо выбирать соответствующий клей. Сейчас на рынке проблем с выбором клея практически нет.
Технология склеивания зависит от выбранного клея и обычно также указывается на упаковке. Как видно на фото, клей имеет жёлтый цвет (вопрос цвета для меня не был принципиальным), клей предназначен для использования при наружных работах, по дереву, рисунок годовых колец у бруса разнонаправленный. Дефекты и сколы по краям бруса будут удалены при чистовой обработке бруса. После склеивания для сжатия и фиксации склеиваемых деталей я использовал струбцины.
Сушка клеевого соединения должна выполняться в соответствии с рекомендациями производителя клея. Как правило, необходимо соблюсти следующие условия:
- Следует избегать прямого воздействия на изделие солнца и воды (я, к примеру, сушил под навесом)
- Соединяемые детали должны быть сильно прижаты по склеиваемой плоскости
- Время сушки должно быть выдержано в соответствии с рекомендациями производителя.
Упомяну еще одну нестандартную (необязательную) операцию. С учётом того, что клееный брус создавался для изготовления оконных блоков, а силовые воздействия при выполнении конопатных работ при монтаже оконных блоков — не маленькие. Решил дополнительно усилить конструкцию бруса установкой на шканты. Шканты использовал самодельные из дуба, диаметром 22 мм, с использованием в нижней части шканта отверстия под конусный клин (шкант встаёт в распор на клин — при забивании). Сначала засверлил отверстия. Шканты и конусный клин сажал на клей. Забивал шканты кувалдочкой.
Завершающие операции при изготовлении клееного бруса
Тщательно просушив изделия, окончательно обрабатываем клееный брус. В частности, строгаем брус. При строгании нужно выдержать одинаковые размеры для всех брусьев, размеры бруса в чистоте (в сечении) — 90 на 275 мм. Далее обрабатываем склеенный брус со всех сторон огнебиозащитой, два раза.
Готовый склеенный брус представлен на фото ниже (вид с торца и вид сбоку).
Замечание
Что бы не зацикливаться на слове БРУС, нужно добавить, что данная технология вполне применима при изготовлении и других деталей. Я, например, для изготовления столешницы для компьютерного стола использовал покупную половую доску, из которой и клеил щит.
Совет: При изготовлении небольших заготовок (для ремонта мебели) или небольших конструкций (навесные полочки, ящички) когда делать пазы или четверти несподручно, или у вас нет такой возможности, часто склеивание делают на гладкую фугу. В этом случае, для более надежного склеивания и фиксации, очень поможет набор центровых маркеров. Советую купить. Купить маркеры можно в строительных магазинах, стоят они копейки, а помогают замечательно. Крупные маркеры, на фото справа, самодельные, выточенные на токарном станке, используются при более крупных работах.
Буду рад, если статья окажется вам полезной!
www.diy.ru