Процессы и способы переработки угля
Угольная промышленность в Российской Федерации всегда являлась довольно важной отраслью, поскольку уголь применялся во различных отраслях промышленности. Он издавна считался крайне перспективным сырьем для получения энергии и множества химических продуктов. Да и сегодня уголь не утратил популярности. В этой статье мы рассмотрим различные процессы переработки угля.
Самым первым и самым крупным потребителем угля с 19 века являлся транспорт. Чуть позже его начали применять для производства электроэнергии, металлургического кокса, создания в процессе химической переработки различных соединений, углеграфитовых конструкционных материалов, пластмасс, горного воска, синтетического, жидкого и газообразного высококалорийного топлива, высокоазотистых кислот для удобрения. Существуют различные способы переработки угля.
Пиролиз
Этот же процесс называют коксованием. Он появился XVIII столетии. Во время этой реакции каменный уголь подвергается нагреванию в специальных коксовых печах, без доступа воздуха. Эта реакция происходит с образованием нескольких продуктов:
- пористое, твердое вещество – кокс и летучие вещества, из которых в процессе охлаждения образуется аммиачная вода
- каменноугольная смола
- газообразные соединения.
Каменноугольную смолу в дальнейшем также подвергают перегонке, вследствие чего получают легкое масло, в составе которого присутствуют ароматические углеводороды, к примеру, бензол, толуол, среднее масло (фенолы) и тяжелое масло (нафталин).
Переработка угля методом коксования включает такие этапы:
- подготовка к коксованию
- собственно коксование
- улавливание и переработка летучих соединений.
Во время подготовительной стадии осуществляется обогащение, чтобы удалить минеральные примеси, низкосернистых, малозольных, коксующихся углей. Сырье измельчается до зёрен размером примерно 0,3 мм, разные сорта угля смешиваются между собой. После этого происходит сушка полученной «шихты».
Нагрев продолжается на протяжении 14-16 часов. Весь процесс реализуется при температуре от 900 до 1050 °C. Конечным продуктом является кокс (75-78 % от объема исходного угля) в форме «коксового пирога» (спёкшейся в пласт массы) — выталкивается особыми устройствами («коксовыталкивателями») в железнодорожные вагоны. Там происходит охлаждение («тушение») водой или газом (азотом).
В условиях температуры 250 градусов Цельсия из угля происходит испарение воды, улетучивается угарный газ и углекислый газ. Когда температура поднимается до 350 градусов улетучиваются углеводороды, продукты азота и фосфора. При 500 градусах сырье спекается с образованием полукокса, а когда температура поднимается до 700 градусов и выше улетучивается водород и получается кокс.
Смесь паров и газов, которые выделяются в реакции и составляют около 25 % от массы угля, отводится по газосборнику для улавливания и дальнейшей переработки. Чтобы разделить летучие продукты их охлаждают при помощи впрыскивания распыленной воды (от 70 °C до 80 °C). Во время этой реакции выделяется больше половины объема смол, а последующее охлаждение парогазовой смеси осуществляется в кожухотрубчатых холодильниках (до 25-35 °C). Конденсаты соединяют вместе. Далее после их отстаивания образуется надсмольная вода и каменноугольная смола. После этого начинается очищение сырого коксового газа от Nh4 и h3S, промывание поглотительным маслом (чтобы выделить сырой бензол и фенол), серной кислотой (чтобы выделить пиридиновые основания). После очистки коксовый газ, составляющий 14-15 % от объема угля, используют как топливо для обогрева батареи коксовых печей, а также для других целей.
Каменноугольная смола, которая составляет примерно 3-4 % от массы угля. В составе смолы присутствует много органических веществ. На сегодняшний день ученым удалось идентифицировать лишь 60 % компонентов смолы, а это свыше 500 веществ. При помощи ректификации смолу разделяют на фракции: нафталиновую, поглотительную, антраценовую и каменноугольный пёк. После ректификации из полученных продуктов выделяют:
- нафталин
- антрацен
- фенантрен
- фенолы
- каменноугольные масла.
Коксохимические заводы являются одним из крупнейших потребителей каменного угля — до ¼ мировой добычи.
Низкотемпературный пиролиз или полукоксование
Переработка каменного угля методом низкотемпературного пиролиза осуществляется в условиях температуры 500°С. Таким образом получают искусственное жидкое и газообразное топливо.
Главные продукты полукоксования:
- полукокс – от 55 до 70%
- первичный газ – от 80 до 100 м3/т
- первичная смола – от 10 до 40%.
Горючее, полученное таким методом имеет более высокую ценность, чем твердое. Полученное топливо называют горючим газом, который служит топливом с более высокой теплотой сгорания, а также сырьем для реакций органического синтеза. Кроме газа в процессе реакции образуется смола, из которой создают моторное топливо и растворители. Третьим соединением по этой реакции является полукокс, служащий местным топливом. Для осуществления полукоксования применяется низкосортный уголь, в котором высокое содержание золы.
В 18 веке часто использовали процесс полукоксования бурого угля для получения осветительного масла. Промышленными масштабами полукоксование начали осуществлять в начале 19 века. Однако в конце 19 века об этой реакции стали забывать, и лишь в 30-х годах 20 века вследствие возникшей необходимости получения бездымного топлива в Великобритании, а после и в Германии. В это время фиксируется возобновление промышленного производства полукокса из каменных углей.
Процесс полукоксования проводится в две стадии:
- при 320-480°С происходит интенсивное выделение паров смолы, газа с образованием пластической массы
- при 480-550°С осуществляется деструкция твёрдых остатков, а также образуются и выделяются жидкие и газообразные продукты, а также образуется твёрдый полукокс.
В процессе полукоксования углей применяется несколько видов печей (реакторов), которые отличаются главным образом по типу теплоносителя (газовый, твёрдый) и системе обогрева (внутренний, внешний). Все эти системы и аппараты обеспечивают максимальный выход смолы, равномерный по показателям полукокс, высокую производительность в условиях минимального расхода тепла на процесс.
Другие способы переработки угля
Кроме таких известных методов, как коксование и полукоксование, сегодня для переработки угля часто применяют метод гидрирования. В результате такой реакции получают жидкое топливо, которое используется как моторное.
Еще одним методом является газификация, в процессе которой образуются горючие газы.
Однако наиболее высокой перспективой обладают плазмохимические процессы переработки каменного угля. Реализация таких процессов проводится в полностью автоматическом режиме, который помогает предотвратить вредные выбросы в окружающую среду золы, таких опасных веществ, как сера и прочие вредные вещества. Стоит отметить, что еще одни достоинством данного метода является использование оборудования небольших размеров.
Катализатор* |
Способ |
Конверсия угля, % |
Выход газов, % |
Выход жидких продуктов, % | |
---|---|---|---|---|---|
до 180 °С |
>180 °С |
||||
1 |
2 |
3 |
4 |
5 |
6 |
Отсутствует |
– |
28 |
11,6 |
6,3 |
38,0 |
Гематит |
Отсутствует |
45 |
11,4 |
6,5 |
41,5 |
Активирован |
92 |
11,0 |
7,1 |
66,8 |
|
Магнетит |
Отсутствует |
21 |
11,5 |
6,1 |
38,3 |
Активирован |
88 |
10,8 |
8,5 |
62,9 |
|
Пирротин |
Отсутствует |
23 |
11,8 |
10,0 |
29,5 |
Активирован |
92 |
12,1 |
10,0 |
67,9 |
|
Пирит |
Отсутствует |
34 |
11,5 |
9,8 |
40,8 |
Активирован |
91 |
12,4 |
10,1 |
67,1 |
|
* содержит 1 вес. % активированных образцов и 2 вес. % для неактивированных; ** механическая обработка в смеси с элементарной серой (0,8 вес. %) в воде |
mining-prom.ru
Как сделать угольные брикеты для отопления
Обычные опилки и древесные щепки можно жечь в изготовленных для этого котлах, а вот с угольной пылью не все так просто.Те, кто уже пробовал топить свой котел таким топливом, понял – половина его просто пропадает, проваливаясь между прутами колосников в золу, вторая же половина спекается в камень и не дает прогоревшему топливу попасть в золу. Все эти причины приводят к снижению качества горения, а значит и теплоотдачи.
Но с другой стороны выкидывать угольную пыль, по меньшей мере, глупо, в ней содержится большое количество энергии. И тут проблему способно решить превращение угля в брикеты, о чем мы и поговорим ниже.
Подробнее о технологии брикетирования
Для классификации топливных брикетов применяется ряд параметров:- материал, из которого делают брикет;
- форма;
- защищенность;
- экологичность;
- тип упаковки.
Можно, конечно же, сжечь такую пыль, предварительно растопив котел дровами, и уже на них насыпать мелкую фракцию. Но такой подход не является выходом, это очень хлопотно, ведь насыпать пыль из угля нужно понемногу, а значит часто.
Если же вы положите на дрова сразу большое количество угольной пыли, она все-таки просыплется в колосники и таким образом, проблема частичного сгорания топлива никуда не денется, к тому же остальная пыль провалится между дровами, перекроет приток воздуху и горение значительно ослабнет.
Чтобы обойти все вышеперечисленные неудобства, нужно прессовать угольную пыль в брикеты, которые в таком виде будут превосходно гореть, отдавая всю свою энергию.
Узнать о том, что предпочтительней использовать для отопления опилки или дрова, можно здесь: https://teplo.guru/kotly/toplivnyie-briketyi-ili-drova.html
Российские разработки
Решение по прессованию мелкой фракции топлива было изобретено еще в начале прошлого столетия, Российским исследователем А.П. Вешняковым.Его идея и до сих пор используется в промышленности и быту. Суть идеи заключается в прессовании древесного порошка в твердые элементы, способные гореть и отдавать тепло ни чем не хуже самого угля.
Не говоря о подробной технологии изготовления топливных брикетов и не перечисляя их типы, можно отметить, что они бывают двух основных типов:
- с применением связующих компонентов, производственное сжигание;
- без них, для домашнего использования.
Важно знать: брикеты, изготовленные по технологии, предусматривающей использование согласующих элементов, в быту использовать категорически нельзя. При их горении выделяется множество токсичных веществ, которые в производстве удаляет специальное оборудование.
Мы говорим о технологии изготовления брикетов без применения связующих компонентов. Производство проходит следующим образом:
- изначально угольная пыль и мелкие камешки измельчаются, самая большая частичка на выходе не должна быть больше 6 мм;
- далее смесь сушат до влажности в 15%. Для этого используют сушилки парового и газового типа;
- далее пыль охлаждается и передается к прессу. Его воздействие на мелкую фракцию происходит с давлением от 100 до 150 Мпа, в специальном прессе штемпельного типа;
- после чего готовая продукция подается на хранение.
Требования к размеру частичек и давлению прессовки может меняться в зависимости от применяемого оборудования и назначения топлива. К примеру, производственная линия компании ЮНИТЕК работает с частичками до 0.25 мм и их влажностью от 6 до 16%.
В результате мы получаем продукт с зольностью 15—20%, способный выдерживать давление в – 3 кг/см, а при падении с двухметровой высоты, потеря массы от удара будет незначительной. Энергоемкость брикетов будет зависеть, непосредственно, от угольной пыли, из которой их делают.
Промышленное производство
Для производства брикетов промышленного типа применяют такие связующие вещества:- нефтебитумная смесь;
- цемент;
- лигносульфонатные добавки;
- жидкое стекло;
- меласса.
Для переработки мелких частиц кокса и некоторых других сортов угля, часто используют цемент, а так же жидкое стекло. Такие материалы используют в основном в металлургии, там, где применение этих веществ допускается.
Каменноугольная смола с нефтебитумом так же применяют для изготовления промышленных угольных брикетов. Топить жилые дома ими нельзя, так как происходит выделение большого количества бензопирена и прочих токсичных элементов, запрещенных СЭС.
Изготовить топливные брикеты самостоятельно поможет данная статья: https://teplo.guru/kotly/toplivnye-briketyi-svoimi-rukami.html
Производство дома
Для того чтобы сделать угольные брикеты своими руками, нужно иметь саму пыль угля и глину, безопасный связующий элемент. Добавляя немного воды, пыль и глину смешивают 10:1, таким образом, раствор приобретает нужную консистенцию. Очень важно тщательно смешать вещества.Для создания брикетов можно использовать как обычный строительный миксер, так и специальное оборудование, например торговой марки Weber. Если вы решили изготовить брикеты вручную, можно использовать в роли формы любые емкости, ящики, кастрюли и т.д. В конце изготовления топливные брикеты нужно высушить.
Обратите внимание: применение оборудования для создания брикетов в домашних условиях будет нерентабельным.
Естественно, что брикет, изготовленные дома не идеальны. Их прочность не так велика, как у промышленных аналогов, имеют разную влажность, и теплоотдачу.
Но как бы там ни было, в котле они горят отлично, гораздо лучше спекающейся и проваливающейся угольной пыли. Да и себестоимость их непременно порадует. Оставленные положительные отзывы, о данной технологии, говорят сами за себя.
Большую популярность в последнее время приобретают котлы, способные работать на двух видах топлива. Подробнее о комбинированном оборудовании здесь: https://teplo.guru/kotly/combi/kombinirovannye-kotly-gaz-drova.html
Как производят угольные брикеты, смотрите в следующем видео:
teplo.guru
Обработка угля
Настоящее изобретение относится к обработке угля.
Более конкретно, настоящее изобретение предлагает способ обработки угля посредством удаления влаги и летучих веществ из угля для изготовления топливного продукта, в котором отсутствуют нежелательные загрязняющие вещества, которые выделяются в процессе горения угля. Любые выбросы в атмосферу от горения топливного продукта согласно настоящему изобретению будут чище, чем в случае необработанного угля, и можно не применять технологии дожигания или очистки, которые, как правило, требуются для очистки выбросов от угольной горелки. Настоящее изобретение предлагает менее дорогостоящее решение проблемы грязных выбросов, чем существующие в настоящее время решения.
Настоящее изобретение также предлагает изготавливать из угля новый продукт, который может служить как исходный материал, имеющий высокое содержание углерода, для промышленного производства активированного угля и угольных электродов. Исходный материал согласно настоящему изобретению может также служить как идеальный материал для пылеугольного вдувания (PCI) в доменные печи в черной металлургии.
Уровень техники, к которой относится изобретение
Предшествующие способы обработки угля включают удаление влаги и нежелательных летучих веществ, которые содержит уголь (как правило, низкосортный уголь и лигнит) для изготовления угля повышенного качества, обеспечивающего большее выделение теплоты в расчете на единицу массы топлива. Например, патенты США № 6447559 и № 7879117 описывают способы изготовления чистого угольное топливо, которое имеет более высокую теплотворную способность в расчете на единицу массы угля по сравнению с неочищенным углем.
Однако эти предшествующие способы не предназначаются для полного удаления всех летучих веществ. Небольшая часть летучих веществ остается, чтобы обеспечивать устойчивое горение обработанного продукта в угольных бойлерах.
По сравнению с битуминозным углем антрацитовый уголь является относительно редким, и его сжигание является более дорогостоящим. До настоящего времени никто не разработал способ его использования в качестве топлива, тем более в качестве чистого топлива. Антрацитовый уголь представляет собой ценный сорт угля, который отличается своим низким содержанием летучих веществ и низким влагосодержанием. Благодаря своим свойствам, он является идеально приспособленным для производства кокса и стали. Вследствие своих уникальных свойств, относительной редкости и некоторых других факторов, антрацитовый уголь в настоящее время продается по высоким ценам, которые многократно превосходят цены других сортов угля. Следовательно, несмотря на то, что его выбросы являются намного чище, чем выбросы, которые образует битуминозный или, как его обычно называют, бурый или паровичный уголь, ни в настоящее время, ни в обозримом будущем не предполагается вероятность использования антрацитового угля в качестве топлива для промышленных бойлеров.
Таким образом, существует неудовлетворенная потребность повышения качества низкосортного угля и придания ему некоторых из основных характеристик высокосортного антрацитового угля в сочетании с решением проблемы устойчивого горения. Задача настоящее изобретение заключается в том, чтобы удовлетворить эту потребность.
Сущность изобретения
Согласно одному аспекту, предлагается способ изготовления обработанного угля, у которого химические свойства являются аналогичными химическим свойствам антрацитового угля, из любого сорта бурого или паровичного угля, включая лигнит. Получаемый в результате обработанный уголь (иногда называемый в настоящем документе Pristine-SA (SA означает синтетический антрацит)), изготовленный способом согласно настоящему изобретению, составляют, в основном, углерод и водород, и он горит так же чисто, как природный газ.
Согласно еще одному аспекту предлагается обработанный уголь, который составляют, в основном, углерод и водород, и из которого удалены влага и летучие вещества для изготовления топливного продукта, в котором отсутствуют нежелательные загрязняющие вещества.
Согласно следующему аспекту, предлагается уплотненный продукт, такой как брикет, в котором сочетаются обработанный уголь согласно настоящему изобретению (Pristine-SA) и биомасса. Мелкие частицы Pristine-SA уплотняются вместе с обожженной биомассой (причем обожженная биомасса изготавливается в таких же реакторах, как Pristine-SA, но работающих параллельно), и получается твердое топливо, которое можно вводить непосредственно в использующие битуминозный уголь бойлеры. Пропорции биомассы и Pristine-SA тщательно регулируются, чтобы обеспечивалось оптимальное горение и устойчивость пламени при минимальном загрязнении бойлера. В некоторых случаях может потребоваться небольшой дополнительный поток горючего газа, чтобы поддерживать горение.
Согласно следующему аспекту, настоящее изобретение предлагает способ сжигания обработанного угля согласно настоящему изобретению с горючим газом посредством введения спутного потока горючего газа, например, такого как природный газ, газ из органических отходов или другой подходящий газ, вдоль обработанного угля в достаточном количестве, чтобы поддерживать устойчивое горение в существующем промышленном бойлере, предназначенном для сжигания битуминозного угля.
Подробное описание изобретения
Согласно первому аспекту настоящего изобретения, предлагается способ обработки неочищенного угля, позволяющий удалить из него внутреннюю и поверхностную влагу с последующим удалением летучих веществ. Этот процесс осуществляется посредством ступенчатого нагревание в условиях определенной температуры и атмосферного давления. В результате этого процесса получается продукт, который можно сжигать в бойлерах, предназначенных для сжигания битуминозного угля, при том условии, что обработанный уголь смешивается со вспомогательным топливом, таким как встречающееся в природе топливо, которое может поддерживать горение обработанного угля, за счет увеличения содержания водорода по отношению к углероду в смеси двух видов топлива.
Примеры вспомогательного топлива, имеющего высокое содержание водорода, представляют собой газ из органических отходов и природный газ, хотя можно также использовать и чистый водород, при том условии, что его производство является экономически целесообразным. Смешанное топливо, которое составляют обработанный уголь согласно настоящему изобретению и вспомогательное топливо, не производит токсичных выбросов в атмосферу, и эти выбросы предпочтительно имеют пониженное содержание углерода.
Поскольку использующие битуминозный уголь бойлеры, как правило, не оборудованы для одновременного сжигания двух видов топлива, могут потребоваться некоторые модификации, чтобы обеспечить решение этой задачи. Такие модификации включают, например, двойные топливные впуски, регуляторы скорости подачи и оптимальное расположение впусков топлива в целях поддерживания горения с максимальной эффективностью.
В США и других странах существуют многочисленные бойлеры комбинированного цикла или многотопливные бойлеры, которые способны сжигать раздельно уголь и природный газ. Обработанный уголь согласно настоящему изобретению является идеально пригодным для использования в сочетании с этими бойлерами. Таким образом, настоящее изобретение делает более ценными битуминозный и суббитуминозный уголь, а также снижает стоимость соблюдения экологических стандартов при сжигании угля этих сортов вследствие уменьшения соответствующих выбросов.
В прошлом, когда цена природного газа была относительно высокой, совместное сжигание угля и природного газа для улучшения горения было экономически нецелесообразным. В настоящее время, несмотря на обнаружение природного газа в сланцевых месторождениях США, существуют прогнозы, согласно которым будет продолжаться постепенное увеличение цены природного газа с течением времени. Это объясняется тем, что увеличение поставок природного газа уже увеличило по сравнению с предложением спрос на него со стороны многочисленных предприятий, которые переключились на использование газовых бойлеров.
Следовательно, столь ожидаемое падение цены природного газа может оказаться непродолжительным, и в результате этого произойдет замедление преобразования угольных бойлеров в использующие природный газ бойлеры. Использование угля в целях сжигания будет продолжаться, согласно ожиданиям или прогнозам авторитетных американских и международных энергетических учреждений. Для такого применения в целях сжигания обработанный уголь согласно настоящему изобретению, который за счет удаления летучих веществ представляет собой чистый уголь, имеющий низкое содержание летучих веществ, можно сжигать совместно со вспомогательным топливом, таким как природный газ или биогаз, что представляет собой экологически превосходную и экономически целесообразную альтернативу по отношению к раздельному сжиганию неочищенного угля, природного газа или биомассы.
Новизной отличается идея, заключающаяся в том, чтобы совместно сжигать в угольных бойлерах обработанный уголь согласно настоящему изобретению (т.е. уголь, имеющий близкое к нулевому содержание летучих вещества) и вспомогательное топливо, такое как природный газ. Настоящее изобретение является идеально пригодным для использования в бойлерах комбинированного цикла или многотопливных бойлерах, которые способны раздельно или одновременно сжигать топливо нескольких видов. Хотя существуют многочисленные бойлеры комбинированного цикла или многотопливные бойлеры, при обычном применении эти бойлеры предназначаются только для переключения с одного топлива на другое.
В отличие от существующих способов удаления летучих веществ из угля (включая способы коксования), настоящее изобретение предлагает способ, в котором используется многоступенчатое нагревание, как правило, двухступенчатое нагревание, в процессе которого осуществляется разложение угля и полное удаление из него влаги и летучих веществ в газообразной форме. В процессе нагревания используются температуры в интервале от 900 до 2500°F (от 482 до 1371°C). Эти температуры являются выше, чем температуры, которые используются в обычных способах удаления влаги и летучих веществ из угля. На первой ступени температура повышается до уровня в интервале от 900 до 1500°F (от 482 до 816°C), и на второй ступени температура повышается до уровня в интервале от 1500 до 2500°F (от 816 до 1371°C).
Влага и летучие вещества в газовой фазе охлаждаются и конденсируются в ступенчатом режиме, образуя раздельные потоки, в которых содержатся вода и жидкие углеводородные побочные продукты, и при этом сохраняется структурная целостность исходного угля, из которого изготавливается обработанный уголь согласно настоящему изобретению. Образующиеся в данном процессе углеводородные побочные продукты представляют собой жидкости, в том числе каменноугольные смолы и другие тяжелые летучие вещества, а также метан, бутан и легкие ароматические соединения. Экономическая ценность этих жидкостей представляет собой значительное достижение настоящего изобретения и обуславливает значительное повышение экономической целесообразности изобретенного способа.
Период времени (время выдерживания), в течение которого уголь подвергается ступенчатой термической обработке, является более продолжительным, чем в предшествующих способах. Таким образом, для способа изготовления Pristine-SA согласно настоящему изобретению требуется время выдерживания, составляющее от 15 до 45 минут, чтобы удалить из угля все содержащиеся в нем летучие вещества. Как правило, время выдерживания для первой ступени составляет приблизительно от 15 до20 минут, а время выдерживания для второй ступени дополнительно составляет от 20 до 25 минут.
Конечный продукт, изготовленный предшествующими способами, согласно которым из угля удаляются влага и летучие вещества, также отличается от продукта Pristine-SA, изготовленного способом согласно настоящему изобретению. Предшествующие способы позволяют изготавливать твердое чисто горящее топливо, которое способно поддерживать свое собственное горение, в то время как, согласно способу изготовления Pristine-SA, получается чисто горящее твердое топливо, в сочетании с которым используются горючие газы. Эти газы включают имеющие низкую теплотворную способность газы, которые производят и бесполезно сжигают нефтеперерабатывающие заводы и другие промышленные предприятия, а также газы из биомассы.
Согласно следующему варианту осуществления настоящего изобретения, получается продукт Pristine-SA, совместно с которым уплотняется обожженная биомасса, такая как, например, обожженная древесина или другой подвергнутый обжигу возобновляемый источник энергии с нейтральным показателем высвобождения углерода, причем он имеет удельную энергоемкость, которая превышает удельную энергоемкость древесины и приближается к удельной энергоемкости угля, и данный уплотненный продукт получается в форме брикетов. Хотя этот уплотненный продукт может поддерживать свое собственное горение, он отличается от продуктов, изготовленных согласно предшествующим способам, тем, что он производит уменьшенные выбросы диоксида углерода вследствие использования биомассы, которая производит нулевые выбросы диоксида углерода. В данном отношении следует отметить, что горение биомассы по определению считается производящим нулевые выбросы диоксида углерода, поскольку такое выбросы нейтрализуются поглощением диоксида углерода в процессе роста растений.
Когда используются сорта угля, которые имеют высокое влагосодержание, способом согласно настоящему изобретению изготавливается топливо, у которого теплотворная способность (CV) является выше, чем теплотворная способность необработанного угля. Повышение теплотворной способности происходит прямо пропорционально влагосодержанию угля.
Помимо своего использования в качестве топлива для более чистого горения, обработанный уголь согласно настоящему изобретению (синтетический антрацитовый уголь) представляет собой экономически привлекательную альтернативу по отношению к нефтяному коксу и другим аналогичным исходным материалам для различных отраслей промышленности, включая активированный уголь и угольные электроды для алюминиевой промышленности, а также углеродные добавки для сталелитейной промышленности. Еще одно применение обработанного угля Pristine-SA согласно настоящему изобретению представляет собой пылеугольное вдувание (PCI) в доменные печи. В данном отношении продукт Pristine-SA может функционировать в качестве предпочтительного источника углерода в целях ускорения восстановления железной руды в доменной печи в процессе производства расплавленного железа и позволяет сократить потребность в коксе.
Антрацитовый уголь в качестве топлива для промышленных бойлеров используется лишь в минимальной степени вследствие своей высокой стоимости, ограниченной доступности и проблем, связанных с поддержанием его горения. Обработанный уголь согласно настоящему изобретению представляет собой практически чистое сочетание углерода и водорода и преодолевает недостатки, отмеченные выше. Таким образом, настоящее изобретение предлагает подобный антрациту уголь, который можно продавать по менее высоким ценам, чем природный антрацит, и, следовательно, он может оказаться экономически целесообразным в качестве топлива.
Согласно важному аспекту настоящего изобретения, предлагается введение спутного потока вспомогательного топлива, такого как природный газ или другой горючий газ (например, биогаз, газ из органических отходов, дизельное топливо и т.д.), который представляет собой сонаправленный поток вдоль обработанного угля в промышленном бойлере. Вспомогательное топливо, такое как природный газ, обеспечивает требуемое соотношение углерода и водорода в топливе, чтобы поддерживать горение обработанного угля согласно настоящему изобретению. В таком сочетании обработанный уголь согласно настоящему изобретению и горючий газ обеспечивают устойчивое горение, в процессе которого уменьшается требуемого количества горючего газа по сравнению с количеством, которое потребовалось бы в случае работы бойлера только с использованием газа.
Горючие газы также включают газы, которые производят промышленные предприятия, нефтеперерабатывающие заводы и химические производственные предприятия, и у которых теплотворная способность является чрезмерно низкой для экономичного сжигания для производства тепловой/электрической энергии. Следовательно, эти газы, как правило, сжигаются в факелах, и при этом бесполезно расходуется их энергосодержание. Эти горючие газы обеспечивают требуемое содержание водорода, чтобы поддерживать горение обработанного угля согласно настоящему изобретению.
Такой способ не только повышает качество угля низких сортов, но также производит выбросы, которые являются в более значительной степени сокращенными и очищенными, чем выбросы, которые производят в результате своего горения необработанные битуминозные и суббитуминозные паровичные угли. Кроме того, посредством использования обработанного угля согласно настоящему изобретению, может быть устранена очистка выбросов вследствие того, что они имеют близкое к нулю содержание веществ, присутствие которых в выбросах является нежелательным. Помимо этого, согласно данному способу, образуются углеводородные побочные продукты, которые представляют собой важный фактор, положительно влияющий на экономическую целесообразность способа. Удаление влаги из исходного угля повышает теплотворную способность угля, превращая его в более эффективное топливо, чем необработанный уголь.
Хотя настоящее изобретение описывается в связи с тем, что в настоящее время рассматривается как наиболее практичный и предпочтительный вариант осуществления, следует понимать, что настоящее изобретение не должно ограничиваться описанным вариантом осуществления, но, напротив, предназначается для распространения на разнообразные модификации и эквивалентные конфигурации, которые соответствуют идее и находятся в пределах объема прилагаемой формулы изобретения.
edrid.ru
Каменный уголь — переработка вчера, сегодня и завтра
Когда-то Менделеев сказал, что топить нефтью — все равно что кидать в печь ассигнации. То же самое можно сказать и про каменный уголь. Переработка позволяет снизить нагрузку на экологию и практически избавляет уголь от серосодержащих вредных примесей. Рассмотрим же основные способы и процессы переработки угля, а также результат и полученные из него продукты.
Угольное прошлое
С углем как топливом человечество знакомо еще со времен Древней Греции. Но как самостоятельная отрасль угольная промышленность выделилась лишь в 18 веке. В начале 19 века уголь стали использовать весьма активно — топливо для транспорта, производство электричества, металлургия, химическая промышленность, автомобиле- и кораблестроение и др. Потребовалось более качественное сырье.
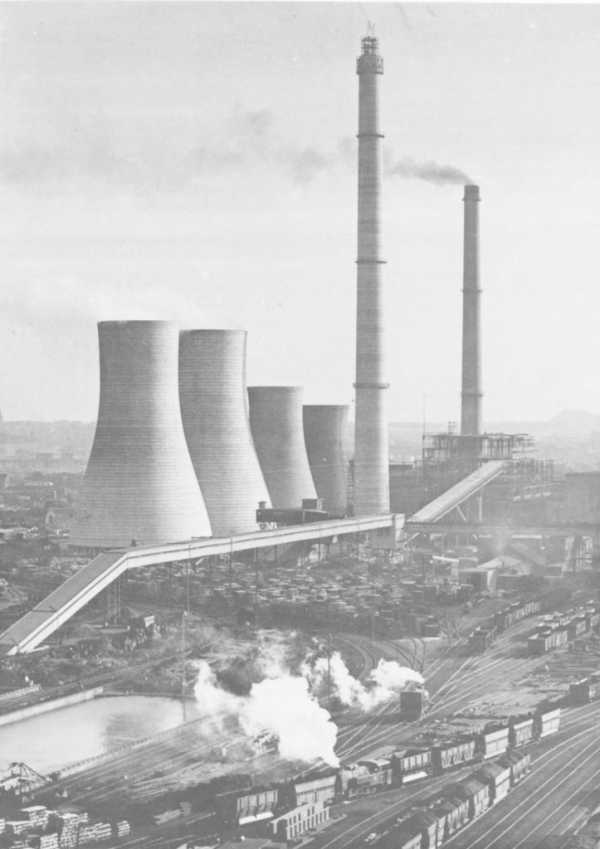
Разработаны были в 20 веке способы переработки угля, чтобы качество добытого сырья было выше. Они были с недостатками, такими как низкий выход продуктов, жесткие рамки осуществления процесса. Но с введением в процесс различных катализаторов выход продукта стал более высоким, а значит, и более дешевым, да и прохождение процесса уже не требовало жесткого соблюдения всех условий.
На сегодняшний день добыча и переработка угля — это шаг в будущее. Осуществляется она пятью способами. Выбор метода зависит от того, какой конечный продукт необходим.
Пиролиз
Этот способ переработки каменного угля используется уже давно. Еще в конце 90-х гг. 19 столетия уголь умели нагревать без доступа воздуха, чтобы вызвать разрушение полимерных молекул, с последующим их превращением. Продукты термохимической обработки бывают в твердом, жидком и газообразном состоянии.
Современное коксование (еще одно название пиролиза) проводится при температуре от 900 до 1100 °C. Продуктом процесса является кокс, который используют в металлургической промышленности как черной, так и цветной, а также побочный продукт в виде смеси газов и паров.
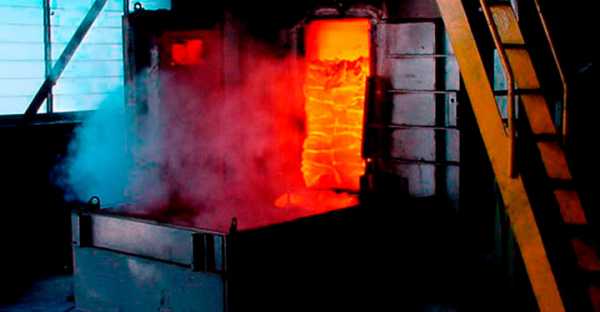
Из смеси, получившейся после коксования под высокой температурой, позже извлекают около 250 химических веществ, в том числе бензол, нафталин, фенолы, аммиак и гетероциклические соединения. Введение в процесс катализатора поспособствовало формированию кокса с мелкозернистой внутренней структурой — более ценный вид товарного кокса.
Полукоксование
Для того чтобы получить из угля переработкой топливо (жидкое или газообразное), используется низкотемпературное коксование при 500 °C. Процесс также не новаторский, известен давно. Раньше целью было получить из бурого угля твердое топливо, более ценное энергетически. Сегодня процесс переработки угля методом полукоксования с применением катализатора окисления увеличил экологичность конечного продукта, в нем уменьшена концентрация канцерогенов и вредных веществ. Из полученной смолы производят растворители и топливо.
Деструктивная гидрогенизация
Этот способ переработки каменного угля направлен на преобразование твердого топлива в «синтетическую нефть» при температуре 400-500 °C и под действием водорода. Идея такой переработки появилась еще в 20-е годы прошлого столетия. В 30-40-е годы построены первые промышленные предприятия на территории Германии и Великобритании, а вот в СССР процесс в промышленных масштабах стали использовать лишь в 50-х.
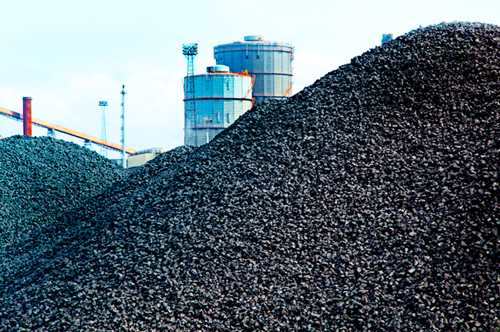
В качестве катализаторов при нефтепереработке используется смесь из алюминия, молибдена и кобальта. Изначально и для угля использовали ее же, но, как оказалось, процесс можно сделать значительно дешевле, без потери эффективности, применив в качестве катализатора широко распространенную железосодержащую руду — магнетит, пирит или пирротит. Такой результат легко было просчитать, если знать, что катализ идет опосредованно. Уголь переходит в жидкую фазу не под действием молекул водорода, а через перенос атомов водорода от молекул органического растворителя к молекулам составляющей угля. Катализатор нужен лишь для восстановления растворителем свойств, потерянных во время отщепления атомов водорода.
Газификация
Под действием высоких температур, но в воздушной среде, где присутствует кислород, водород, углекислый газ и пар, твердый уголь переходит в газообразное состояние. В этом заключается вся суть процесса. Существует около 20 технологий. Не будем подробно останавливаться на каждой из них, а рассмотрим, чем может помочь введение катализатора.
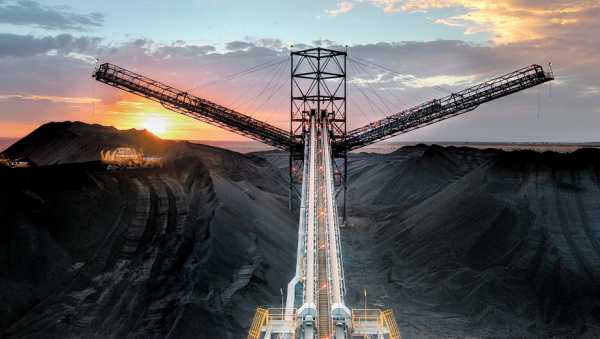
Кроме повышения эффективности, с катализатором появляется возможность понизить температуру с сохранением скорости на прежнем уровне, регулировать конечный продукт газификации тоже можно. Самыми распространенными являются щелочные и щелочноземельные металлы, а также железо, никель и кобальт.
Плазмохимическая переработка
Один из самых перспективных, так как кроме жидкого топлива из каменного и бурого угля при переработке извлекаются такие ценнейшие соединения, как ферросилиций, технический кремний и другие кремнийсодержащие вещества, которые при других способах просто выбрасывались вместе с золой.
А что завтра
Учитывая, как быстро опустошаются залежи нефти и газа на земле, топливный вопрос скоро встанет достаточно остро. И одним из простейших решений будет добыча угля. Ученые ведут свои изыскательские работы, в поисках новых процессов переработки — более результативных, недорогих, но при этом экологически чистых.
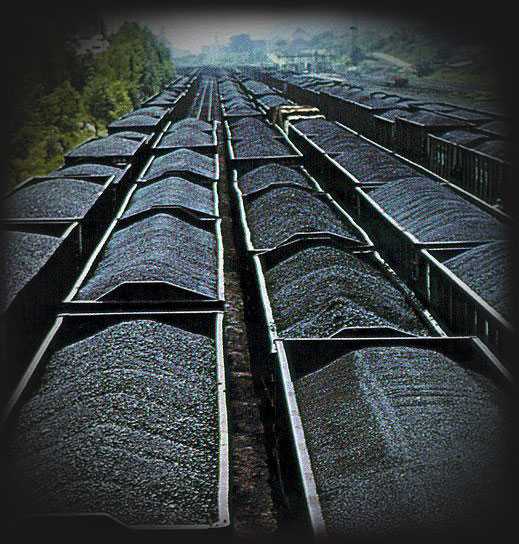
Ведутся работы и по получению «синтетической нефти». В Красноярске, например, прошла апробация получения ее из смеси угля и воды в равных пропорциях. Синтез велся под высоким давлением, обработка велась механическая, электромагнитная и кавитационная. Энергозатраты невелики — всего 5 кВт на тонну нефти. По своему химическому составу полученная фракция близка к природной.
Так что не спешите утилизировать своего железного коня, кормить будет чем. И еще одна хорошая новость — уголь восполняется, а значит, еще долго прослужит человечеству.
fb.ru
Переработка древесного угля
ТЕХНОЛОГИЯ И ОБОРУДОВАНИЕ ЛЕСОХИМИЧЕСКИХ ПРОИЗВОДСТВ
Из многочисленных способов переработки древесного угля приведены только некоторые, представляющие наибольший интерес для лесохимической промышленности.
Брикетирование древесного угля. Древесный уголь, особенно древесно-угольная мелочь,— малотранспортабельный материал; при транспортировке и перевалках уголь сильно измельчается и распыляется. Эти недостатки древесного угля устраняются при его брикетировании с применением связующих веществ. В качестве связующих могут быть применены растворимые в воде продукты (растворимая смола, технические лигносуль — фонаты и др.) и нерастворимые (отстойная смола, древесно — смоляной пек в смеси со смолой, битум и др.)-
Брикетированный уголь в Украине и производство древесно-угольных брикетов состоит в приготовлении брикетной смеси, прессовании сырых брикетов и сушки или прокаливания их. Например, древесно-угольную мелочь растирают 30 мин на бегунах с техническими лигносульфо — натами (полученными при производстве целлюлозы с варочной кислотой на аммониевом основании) и получают брикетную смесь, содержащую 77—78 % угля, 11 —12% лигносульфонатов (в расчете на сухое вещество) и 10—11 % воды. Смесь прессуют на вальцово-ручейном прессе под давлением 15—20 МПа. Сырые брикеты высушивают при 100—120 °С в течение 2 ч или прокаливают при 500 °С. Плотность готовых брикетов до 0,75 г/см3, прочность на сжатие около 6 МПа. Теплота сгорания 1 кг брикетов примерно такая же, как у исходного угля, однако ввиду большей плотности брикетов теплота сгорания единицы объема их гораздо выше.
Брикеты используются в кузнечном и литейном производствах, в сфере общественного питания, туризма и др.
Существуют также способы окусковывания (склеивания) древесно-угольной мелочи без прессования под давлением.
Производство карбюризатора. Карбюризатор — это березовый древесный уголь, покрытый пленкой углекислого бария. Он применяется для цементации стальных изделий, т. е. для обогащения их поверхностного слоя углеродом с целью придания особой твердости.
Технологический процесс производства карбюризатора состоит из следующих основных операций: дробления и сортировки угля-сырца, обмазки угля углекислым барием, сушки и охлаждения сырого карбюризатора. Уголь-сырец измельчают на дробильных валках в три ступени, с промежуточным рассевом, сначала на куски размером 25—35 мм, затем до 15 мм и окончательно на куски 3,5—10 мм.
После отсева от мелочи, пыли и охлаждения уголь поступает в обмазочный аппарат типа бетономешалки. Для обмазки готовят суспензию углекислого бария в водном растворе крахмала. Затем карбюризатор сушат в горизонтальных вращающихся барабанах с помощью дымовых газов, температуру которых на входе в барабаны поддерживают в пределах 600— 700 °С. Готовый карбюризатор аналогично древесному углю охлаждают воздухом в тонком слое на конвейере, что стабилизирует продукт и предотвращает его самовозгорание.
Расход крахмала на 1 т карбюризатора равен 10 кг, углекислого бария — 215 кг. Углекислый барий — вещество 1-го класса опасности, ПДК его аэрозоля в воздухе рабочей зоны 0,5 мг/м3.
Согласно ГОСТ 2407—83 карбюризатор должен содержать, %: 20±2 углекислого бария, не более 2 углекислого кальция, до 0,04 общей серы, до 0,2 двуокиси кремния, не более 8 летучих веществ и 4 влаги. Не менее 92 % карбюризатора должно при рассеве оставаться между ситами с полотном № 35 и № 100, масса крупных частиц не должна превышать 2 %, а мелочи на поддоне 6 %.
Производство активного угля. Активным или активированным древесным углем называется продукт, получаемый путем специальной обработки древесного угля-сырца, в результате, которой во много раз увеличивается его пористость за счет удаления остатков летучих веществ и выгорания смолистых пленок. Активация угля производится в активационных печах путем воздействия на него перегретого водяного пара или топочных газов при температуре 750—1000 °С. Степень обгара, т. е. потеря массы древесного угля при его активации, в зависимости от требуемых свойств готового продукта равна 40—80 %.
В древесном угле-сырце имеются в основном макропоры, размер которых превышает 100 нм (1 нм=10-9 м). В активном древесном угле поры гораздо мельче: микропоры размером 1— .. 2 нм и переходные, или мезопоры, размером до 50 нм, т. е. они соизмеримы с величиной молекул различных веществ. Удельная поверхность пор достигает огромной величины, исчисляемой сотнями квадратных метров на 1 г активного древесного угля, вследствие чего поглотительная способность его во много раз больше, чем у исходного угля-сырца.
Поэтому активный уголь широко применяется для обесцвечивания жидкостей в сахарорафинадном и других производствах, для поглощения паров органических растворителей из воздуха производственных помещений, является обязательной составной частью противогазов и др.
В лесохимической промышленности вырабатывается активный уголь марки ДАК — Сырьем для его производства служит угольная мелочь (отход карбюризаторного производства), при необходимости добавляется кусковой уголь. Печь активации представляет собой стальной цилиндр, футерованный жароупорным кирпичом. Уголь прокаливают 45—60 мин под воздействием парогазовой смеси, состоящей из продуктов сгорания дизельного топлива и перегретого водяного пара; температура смеси 800—950 °С. Активирующим началом является химически связанный кислород, в результате взаимодействия с которым смолистые вещества угля образуют твердый углерод и газообразные соединения. Охлаждение готового активного угля ведется в стальном охлаждающем барабане, орошаемом снаружи водой. Выход — 50 % от исходного угля.
Активный уголь марки ДАК имеет активность по йоду не менее 30, пористость по воде не менее 1,4 см3/г, содержание золы до 6% и влаги до 10%. Применяется для обезмаслива — ния парового конденсата на теплоэлектростанциях.
Активный осветляющий уголь высокого качества можно получать из отработанной щепы канифольно-экстракционных за — i водов. Если для выработки активного угля использовать дре
Весный уголь, полученный при пиролизе древесины с катализаторами, то выход активного угля в расчете на исходную древесину повышается примерно в 1,5 раза.
Производство окисленного древесного угля. Древесный уголь дробят, сортируют и окисляют при повышенной температуре кислородом воздуха. В некоторых случаях окисленный уголь подвергают термообработке и повторному окислению.
В результате на поверхности угля образуются различные функциональные группы — карбоксильные, фенольные, спиртовые и др. Меняя условия окисления, можно добиться преобладания тех или иных групп и придания продукту окисления различных свойств — ионообменных, комплексообразующих, каталитических и др.
Древесный окисленный уголь марки ДОУ-1—полифункциональный катионит, способный заменить более дорогие и токсичные катиониты на основе синтетических смол. ДОУ-2 имеет высокую избирательность к ионам тяжелых металлов и применяется для глубокой очистки химических реактивов от примесей железа, меди, никеля и др. ДОУ-Зс предназначен для глубокой очистки неорганических реактивов от примесей щелочноземельных металлов и используется, в частности, при получении фторидов калия и натрия особой чистоты. Уголь ДОУ-4с обладает высокой каталитической активностью, например, в процессах этерификации и переэтерификации смесей низкомолекулярных жирных кислот и их эфиров.
Древесные окисленные угли отличаются высокой термостойкостью (до 300 °С), химической и радиационной устойчивостью, легко регенерируются, могут выпускаться в виде гранул.
Пожаро- и взрывобезопасность производства. Большинство технологических процессов пиролизного производства пожароопасны, а некоторые из них пожаро — и взрывоопасны. В сушилках не исключено самовозгорание древесины, поэтому горизонтальные сушилки должны иметь подвод острого пара; в случае загорания останавливают дымосос и подают в сушильную камеру пар. В вертикальных непрерывнодействующих сушилках опасность загорания повышается при резком увеличении подачи воздуха в топку или на разбавление теплоносителя. Поэтому сушилки должны быть оснащены устройствами, подающими сигнал при чрезмерном повышении температуры отработанного теплоносителя. Тушение загораний производится острым паром при остановленном дымососе и закрытых затворах загрузочных люков.
В тушильниках уголь выделяет горючие газы; при неполной загрузке горизонтальных тушильников вагонетками с углем концентрация газов в них достигает взрывоопасного уровня. Необходимо загружать тушильники полностью или же подавать в них инертный газ.
Вертикальная непрерывнодействующая реторта должна иметь подвод острого пара в верхнюю, среднюю и нижнюю части. Содержание кислорода в теплоносителе необходимо систематически контролировать. Во избежание подсоса воздуха и загорания угля в реторте нужно поддерживать небольшое положительное давление.
Отходящие газы от различных аппаратов лесохимических производств содержат значительное количество паров летучих веществ и подлежат очистке с целью предотвращения попадания их в атмосферу и регенерации некоторых из них. Газовые выбросы …
Количество промышленных стоков и степень их загрязненности зависят от принятой схемы технологических процессов и на различных заводах колеблются в весьма широких пределах. В частности, при экстракции уксусной кислоты из жижки …
В процессах производства лесохимических продуктов образуются различные сточные воды — отбросные воды ректификационных аппаратов, промывные, подсмольные и подскипидар — ные воды и др. Все они объединяются общим названием промышленных стоков …
msd.com.ua
Утилизация отходов углеобогащения | Добывающая промышленность
07.07.2016
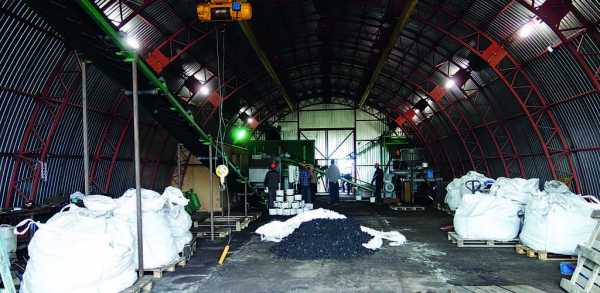
Отходы углеобогащения — техногенные залежи полезных ископаемых
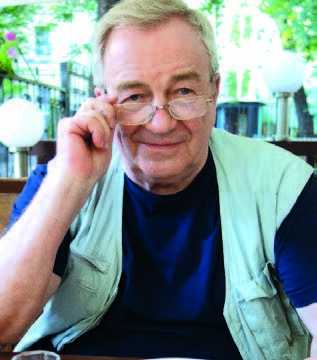
Отходы угольной промышленности РФ, находящиеся в шламоотстойниках и накопителях, превышают 260 млн Т и представляют собой крупные техногенные скопления полезных ископаемых, ежегодный прирост которых составляет 3 млн Т. Только в Печорском бассейне неиспользованных шламов более 12 млн Т.
Техногенные запасы шламов — это, с одной стороны, ценное углеродосодержащее сырьё для получения тепловой и электрической энергий, с другой — источник загрязнения окружающей среды. Шламонакопители занимают большие территории вокруг угольных предприятий, выводят земли из хозяйственного оборота, загрязняют окружающую среду.
Использование шлама, после сложного процесса его сушки, в слоевых топках и бытовых печах малоэффективно из-за больших потерь этих продуктов в виде просыпа под колосники, которые увеличивают количество удаляемой золы. При этом мелкие классы при сжигании попадают в воздух в виде дыма и загрязняют атмосферу.
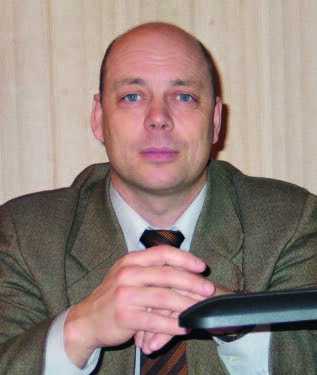
Утилизация шламов является актуальной научно–технической задачей, решение которой позволит:
— улучшить экологическую обстановку в угольных регионах, на шахтах и разрезах;
— рекультивировать земли, занятые отстойниками и накопителями;
— сократить потребление природных энергетических ресурсов за счёт переработки отходов в дешёвое топливо для промышленности, ЖКХ и бытовых нужд населения.
Разработка новых технико-технологических решений, направленных на эффективную переработку шламов с получением товарного продукта с высокими потребительскими свойствами и решением экологических проблем в угольных регионах, является актуальной научно-практической задачей, имеющей большое экологическое и прикладное коммерческое значение. Одним из прогрессивных направлений переработки отходов является брикетирование шламов без применения связующих добавок.
Теоретические основы брикетирования
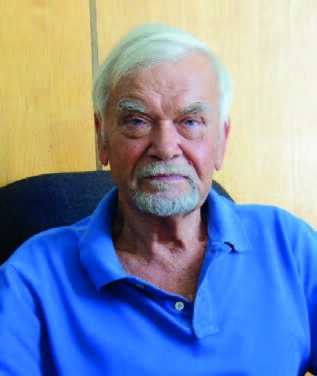
Известные штемпельные, кольцевые и вальные технологии брикетирования углеродосодержащих материалов, с высокой жёсткостью, твёрдостью и упругостью, по принципу действия и особенностям конструкции формовочных инструментов не позволяют, получать механически прочное окускованное топливо без использования связующих веществ с приемлемыми технико-экономическими показателями брикетного производства.
Мировая практика подтверждает: изготовление угольных брикетов без применения связующих добавок по традиционным технологиям требует больших производственных затрат, предусматривающих сверхтонкий помол исходного сырья для прессования, высокотемпературный нагрев брикетируемого материала до пластического состояния и сверхвысокие давления прессования.
Концептуально, с позиций существующих представлений о механизме действия молекулярных и капиллярных сил сцепления при образовании структуры окускованного углеродосодержащего материала с учётом его упруго-пластичных свойств, значительно более благоприятные условия для окускования жёстких, малопластичных веществ без связующих добавок, в сравнении с существующим технологиями прессования, могут быть реализованы только в прессовых агрегатах, обеспечивающих выполнение следующих условий:
— интенсивное развитие активной (удельной) поверхности и капиллярно-пористой структуры брикетируемой массы, а также увеличения числа и плотности контактов брикетируемых частиц в процессе их уплотнения под давлением для повышения эффективности действия молекулярных и капиллярных сил сцепления при формировании структуры окускованного топлива;
— снижение сопротивляемости брикетируемой массы в процессе её уплотнения, обусловленной твердостью частиц и силами трения между ними при их относительном перемещении в межзерновом (межпоровом) пространстве для минимизации энергозатрат на хрупкие деформации, уплотнение и увеличение доли энергии на пластические необратимые деформации, которые определяют механическую прочность структуры брикета;
— повышения активности силового поля поверхности брикетируемых частиц (повышение свободной поверхностной энергии) образования новых некомпенсированных молекулярных и электрических сил взаимодействия за счёт деформации кристаллической решётки и разрушения насыщенного окисленного слоя на поверхности частиц;
— существенное увеличение времени действия давления прессования, что способствует более глубокому сдвигу прилагаемой энергии в сторону образования пластической деформации, которые с механической точки зрения в итоге и определяют прочность образованной структуры окускованного топлива.
Технология брикетирования
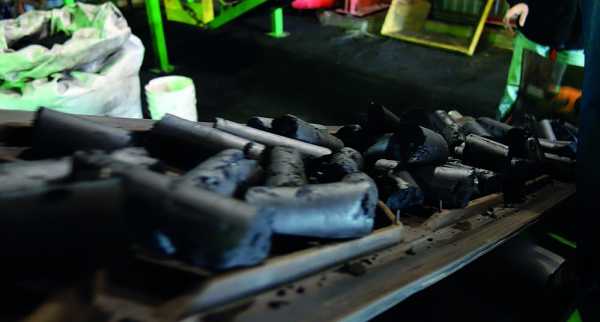
С технической стороны для выполнения условий брикетирования без использования связующих добавок в наиболее полной мере подходят шнековые экструдеры, успешно применяемые для формования высокопластичных строительных материалов и пластмасс. используя этот принцип, специалисты ИОТТ, ООО «Брик-Тек» и ООО «ИТ «Северная Русь» при содействии АО «ННЦ ГП-ИГД им. А.А. Скочинского» разработано специализированное прессовое оборудование для производства механически прочного брикетного топлива из угольных шламов без связующих добавок. Для формирования брикетов в составе технологического комплекса используется специализированное шнековое оборудование.
Разработанная технология позволяет в максимальной мере реализовать теоретические принципы брикетирования без связующих присадок за счёт создания, при окусковании шламов, в зоне прессования, комбинированного действия осевых, сдвигающих и крутящих усилий при уплотнении частиц брикетируемого под давлением материала.
По состоянию на 01.08.2016 г. в г. Воркуте при поддержке Правительства республики коми и привлечении средств инвесторов смонтирована и начала действовать модульная опытно-промышленная брикетная линия, на которой отрабатываются все технологические режимы от приготовления смеси и дозирования сырьевых компонентов, формирования и сушки брикетов, пакетирования и отгрузки готовой продукции.
Угольные брикеты обладают прочностью, необходимой для их последующей транспортировки. Сохраняют прочность при увлажнении, обладают однородностью по геометрическим и
физико-химическим параметрам. Проектная производительность брикетной линии составляет Q = 5,0 Т/ч.
Область применения брикетов
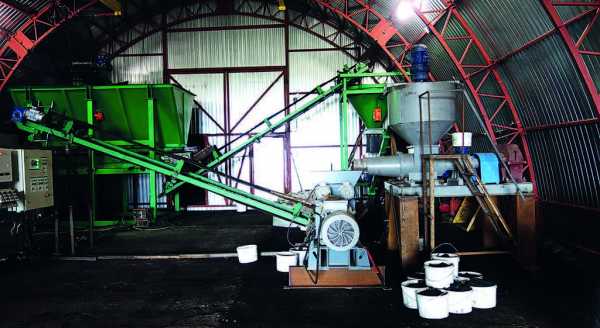
Угольные брикеты предназначены для применения в металлургической и коксохимической промышленности, на тепловых и электрических станциях, удалённых объектах Минобороны РФ, в котельных ЖКХ и железнодорожном транспорте без реконструкции действующих котлоагрегатов, а также для бытовых нужд в частном секторе.
Область применения брикетной технологии
Угольные регионы российской Федерации, угольные компании, шахты, разрезы, горно-обогатительные комбинаты и фабрики.
.
Текст: Станислав Будаев — зав. лабораторией института обогащения Твердого Топлива (ИОТТ), канд. техн. наук
Владимир Добромелов — генеральный директор ООО «ИТ «Северная Русь»
Михаил Смирнов — зам. генерального директора по научной работе — ученый секретарь,
АО «ННЦ ГП — ИГД им. А.А. Скочинского», канд. техн. наук.
dprom.online
как бизнес и в домашних условиях своими руками
Обычно, вопроса, как сделать уголь для шашлыка, не стоит. В магазинах повсеместно можно найти в продаже мешки с древесным углём. Его достаточно чтобы готовить на мангале. А для тех, кто хочет всё сделать самому можно подготовить уголь в «домашних условиях».
Немного про древесный уголь
Древесный уголь где только не использовался: в металлургии, химической промышленности и медицине. Но мы вряд ли начнём делать активированный уголь или создавать порох. Нам древесный уголь интересен как топливо. Топливо для мангалов, грилей и жаровен с уютным теплом.
Подготовка материала
Уголь не от каждой деревяшки можно использовать для приготовления пищи. Это фруктовые деревья (груша, яблоня вишня), лиственные деревья (ольха, дуб, клён) и распространённая берёза. Совсем не подходят хвойные породы. Такое сырьё содержит смолы (это испортит вкус мяса).
Строительные обрезки для изготовления угля для мангалов не используются: пропитки и клеи при сгорании оставят канцерогенные вещества в угле.
Берёза – не самый лучший вариант, но дерево распространённое. Уголь получается чуть жарче чем надо. Хотя, зная такую особенность, можно приноровиться и делать классный шашлык.
Второе требование – сухие дрова. Для пиролиза влага вредна. В промышленном производстве сырьё сушат в специальных печах газами до 150 °С, а при выжиге «для себя» нужно или дать дровам просохнуть или взять сушину.
Гнилое дерево на уголь не пережигается.
Кора ухудшает качество угля и по возможности её нужно удалить с дров.
Выжег древесного угля
Суть процесса в том, чтобы древесина сгорела не до конца.
При нагреве сырья с ограничением доступа кислорода остаётся углеродный каркас, повторяющий древесину. Такой процесс называется пиролизом. Рабочей температурой пиролиза древесины будет 350 °С. Целлюлоза при пиролизе подвергается термической деструкции, результатом которой становится образование угля и пиролизных газов.
Большое количество пор способствует быстрому горению древесного угля.
Массовая доля углерода в древесном угле составляет 50%.
Выжигайте уголь вдали от построек и лесопосадок. Соблюдайте правила пожарной безопасности.
Приготовить уголь для мангала можно несколькими способами.
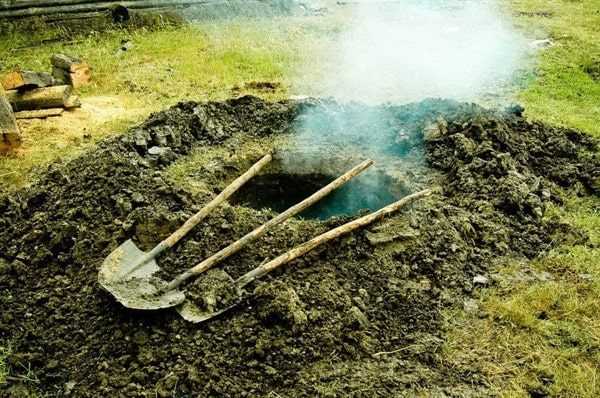
В костре
Один из простейших способов, как сделать угли для мангала в домашних условиях. Потребуется только старое ведро с крышкой, или какая другая негорючая ёмкость.
- Разожгите костёр. Не используя средств для розжига.
- Дайте прогореть.
- Крупные почти прогоревшие до углей головни кочергой или щипцами отправляйте в ведро и зарывайте крышкой. Под конец соберите угли и тоже добавьте в ведро.
- Воздуха для горения будет недостаточно и тление прекратится. Пары часов обычно достаточно.
С опытом количество непрогоревших дров в вашем угле будет меньше.
В яме
Этот способ старый, можно сказать исторический.
- Прежде всего, понадобится яма. Объём ямы определяет количество требуемого угля. Чтобы было удобно работать, дно не должно быть меньше окружности диаметром 0,8-1,0 метров. Ещё что следует учесть: делать яму в низине – плохая идея: она заполнится водой.
- Итак, яма выкопана, стенки и дно утрамбованы.
- Разожгите костёр в яме. И заполните яму на треть дровами. Дрова должны быть среднего размера.
- Когда дрова почти прогорят, заполните угольную яму дровами до самых краёв.
- Проследите чтобы все дрова занялись. И накройте яму листом железа, а щели присыпьте землёй.
- Через пару дней можно снимать крышку и доставать уголь.
Будьте осторожны на краю ямы: уголь, сделанный своими руками, не стоит риска свалиться в яму с костром.
В бочке
Делая древесный уголь в домашних условиях хочется снизить риск. И этот способ как раз из таких.
Вам не потребуется яма. Вы замените её 200 литровой бочкой.
Есть два способа: с разницей снаружи или внутри бочки разводить костёр.
В любом случае поставьте бочку на 4-6 кирпичей, так чтобы она не касалась земли.
Первый способ: костёр внутри бочки.
Чтобы в бочке горели дрова в самом низу нужно пробить несколько отверстий. Некоторые советуют закрепить штуцер для шланга и нагнетать воздух на первом этапе (например, бытовым пылесосом), но это на ваше усмотрение.

- Начать нужно с костра в бочке.
- Когда костёр разгорится заполните бочку на треть дровами и дайте прогореть.
- Заполните бочку дровами полностью. Когда все дрова займутся, закройте крышкой. Искусственный наддув, если он был, следует отключить.
- Когда бочка остынет можно доставать уголь.
Второй способ: костёр вокруг бочки.
- Бочку сразу набейте дровами и закройте крышкой.
- Под бочкой разведите огонь и поддерживайте пока пиролиз не закончится. Если есть термометр, то интенсивность огня должна обеспечивать температуру 350 °С внутри. Без термометра придётся ориентироваться на глаз.
- Следите за дымом из бочки. Сизый прозрачный дым говорит об окончании процесса. Потушите огонь и дайте бочке остыть 2 часа.
Если всё сделано правильно, то выжег дров в 200 литровой бочке займёт около 12 часов.
Когда открываете крышку берегите лицо: газы и угольная пыль могут воспламениться.
В печи
Обычная домашняя печь может помочь вам сделать уголь для шашлыка.
- Растопите печь, загрузите дрова.
- Дождитесь, когда поленья разгорятся и превратятся в красные головёшки.
- Переложите головни в керамическую или металлическую ёмкость с крышкой подходящего размера.
- Закройте крышкой и вынесете из дома.
- Когда остынет, можно проверять качество угля.
От тлеющих в закрытой ёмкости углей исходит угарный газ.
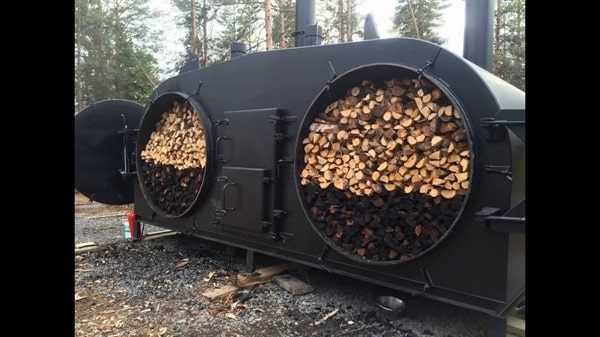
Как бизнес
Промышленное производство угля для мангала строится немного по-другому. Тут важны обрабатываемые объёмы. Нужно снижать трудоёмкость и требуется готовить сырьё (в основном сушить).
Сам процесс можно разбить на 4 стадии:
- Распил на чурки и сушка сырья при 150 °С (влажность дров будет мешать процессу).
- Нагрев при недостатке кислорода до 350 °С – пиролиз.
- Прокалка – нагрев до 500-550 °С. Выжигаются остатки смол.
- Охлаждение и фасовка.
Камера сушки и пиролизная печь совмещаются так, что газы из печи сушат сырьё для следующей закладки.
Кустарное изготовление оборудования для производства древесного угля – задача нетривиальная. Вот, например, пиролизная печь УВП-5Б, разработанная ЦНИИМЭ.
Производство древесного угля, как бизнес, — хоть и затратное, но перспективное направление. Спрос стабильно растёт и цены на уголь не падают. Некондицию и угольную крошку можно перерабатывать в топливные брикеты или сжигать при производстве новой порции угля.
Интересно узнать: вы покупаете уголь для шашлыков или делаете своими руками? Ответ можно дать в комментариях.
edanaprirode.com