Литье пластмасс в домашних условиях – изготовление матриц и пресс форм
В настоящее время популярными стали изделия из пластмассы. Пользоваться ими удобно и практично. Литье пластмассы в домашних условиях – это хорошая идея для открытия своего бизнеса или просто для свободного времяпрепровождения. Хорошо сделанные изделия элегантно и интересно смотрятся, а также их просто содержать в порядке.
Помимо этого, они обладают необходимой прочностью. Чтобы наладить производство такого рода на территории частного владения, необходимо усвоить пару простых правил.
Подготовка материала
В первую очередь необходимо найти пластиковый лом, для изготовления будущего изделия. Это не проблема, так как такого сырья в современном мире огромное количество сломанных вещей, бутылок и другого лома из пластика.
Лом пластиковых ящиков
Однако, необходимо учесть тот факт, что каждый вид пластмассы отличается своим температурным режимом плавления.
Именно поэтому для литья конкретного изделия необходим один вид лома. Смешение нескольких разновидностей изделий из пластмассы даже при изучении его температуры плавления, при отливе часто провоцирует появление пузырьков в продукции.
Лучшим вариантом в таком случае является купить жидкую пластмассу в магазине или заменить ее на диоксидную смолу, это позволит получить качественное изделие, которое прослужит долго. А также дополнительно понадобится ряд вспомогательных средств:
- емкость для плавки;
- силикон;
- литол.
Пары пластмассы ядовиты, они обладают высокой токсичностью. Необходимо соблюдать осторожность при изготовлении изделий в домашних условиях.
Форма
Для приготовления изделия в домашних условиях, прежде всего, необходимо соорудить модель. В первую очередь следует определиться с материалом для изготовления пресс формы. Для этого подойдут следующие материалы:
- дерево;
- пластилин;
- гипс и другие.
Затем следует пройти изготовление матриц для литья, которые и будут непосредственно использоваться для отлива. Форму необходимо обмазать литолом или любой другой смазкой.
Если выбор пал на силиконовые формы, то необходимо учесть, что это вещество работает с коэффициентом более 200%. А также необходимо обратить внимание на его вязкость, чем она меньше, тем точнее получится пресс форма.
Форма для литья силиконовая
Заливка детали
Литье пластиков своими руками напрямую зависит от того материала, который мастера выбрали для изготовления будущей конструкции.
Смолы и жидкие пластмассы хорошо подойдут для приготовления, но они обладают различной степенью вязкость у них, поэтому прослужат они разное время. Все параметры следует изучить в инструкции при покупке.
Существуют рецепты приготовления пасты в домашних условиях, они требуют от мастера щепетильности и скрупулезности во время формирования состава сырья. Для изготовления материала, следует смешать 5 частей мелких опилок с 2 частями талька. Залить массу столярным клеем (его консистенция обязана отвечать состоянию сметаны).
Все тщательно перемешивается для получения теста одной консистенции.
Есть еще один хитрый ход: следует добавить 0,5 части алюминиевых квасцов, они предотвратят появление плесени на тесте, а пластичность при этом увеличивается в несколько раз.
Процесс приготовления теста для литья своими руками трудоемкий, он требует отличных знаний по этой теме. Именно поэтому многие начинающие заливщики, отдают свое предпочтение готовым смесям.
Литье пластмассы в домашних условиях
Ход работы
Отливка происходит в несколько этапов:
- Необходимо взять пресс-форму и тщательно ее очистить. После предварительной подготовки она обязана быть полностью очищенной и высушенной. Все остатки материала после подготовительных мероприятий необходимо убрать.
- Если необходимо придать будущему изделию оттенок, необходимо добавить в состав для литья пару капель краски.
Водяные краски для этого не подходят.
- Подготовительная дегазация смеси не требуется. Все дело в том, что в домашних условиях продолжительность функционирования невелика. А чтобы удалить лишние пузырьки воздуха из небольших изделий, придется приложить силу давлением и убрать их самостоятельно.
- Аккуратно перемешайте состав для заливки и заполните пресс-форму шаблона.
- Заливается все медленно небольшой струйкой.
- Смесь заливается до полного заполнения объема, задевая небольшой участок доли канала для литья. Дело в том, что после дегазации, объем материала уменьшится и станет необходимый для литья.
- Заключительный этап – охлаждение будущей конструкции.
Пластик заливается в форму после чего ему нужно дать постепенно остыть
Для получения качественного изделия шаблон необходимо остужать постепенно.
Бизнес-идеи
Если мелкий производитель решил выйти на широкий масштаб производства, стоит задуматься об открытии собственного дела.
Попробовав свои силы на дому, следует составить бизнес-план, зарегистрироваться, как индивидуальный предприниматель и начать воплощение своей мечты в реальность.
Но покупка оборудования не обойдет предпринимателя стороной. Да и тяжело отливать формы для производства массы изделий собственноручно. Необходимо готовить первые изделия и продавать их, а на полученные средства купить определенный станок для литья пластмасс, пресс.
Как сделать процесс литья пластмассы прибыльным в своем регионе? Семь простых правил отливки позволят приготовить качественное изделие, которое будет интересно смотреться, а также радовать глаз. А со временем предприниматели смогут задаться вопросом о расширении своих навыков и обустройстве личного бизнеса.
Видео: Литье пластмассы в домашних условиях
Как сделать экструдер для переплавки пластмассы из пистолета для герметика
Многие виды пластика являются полезным сырьем для вторичной переработки.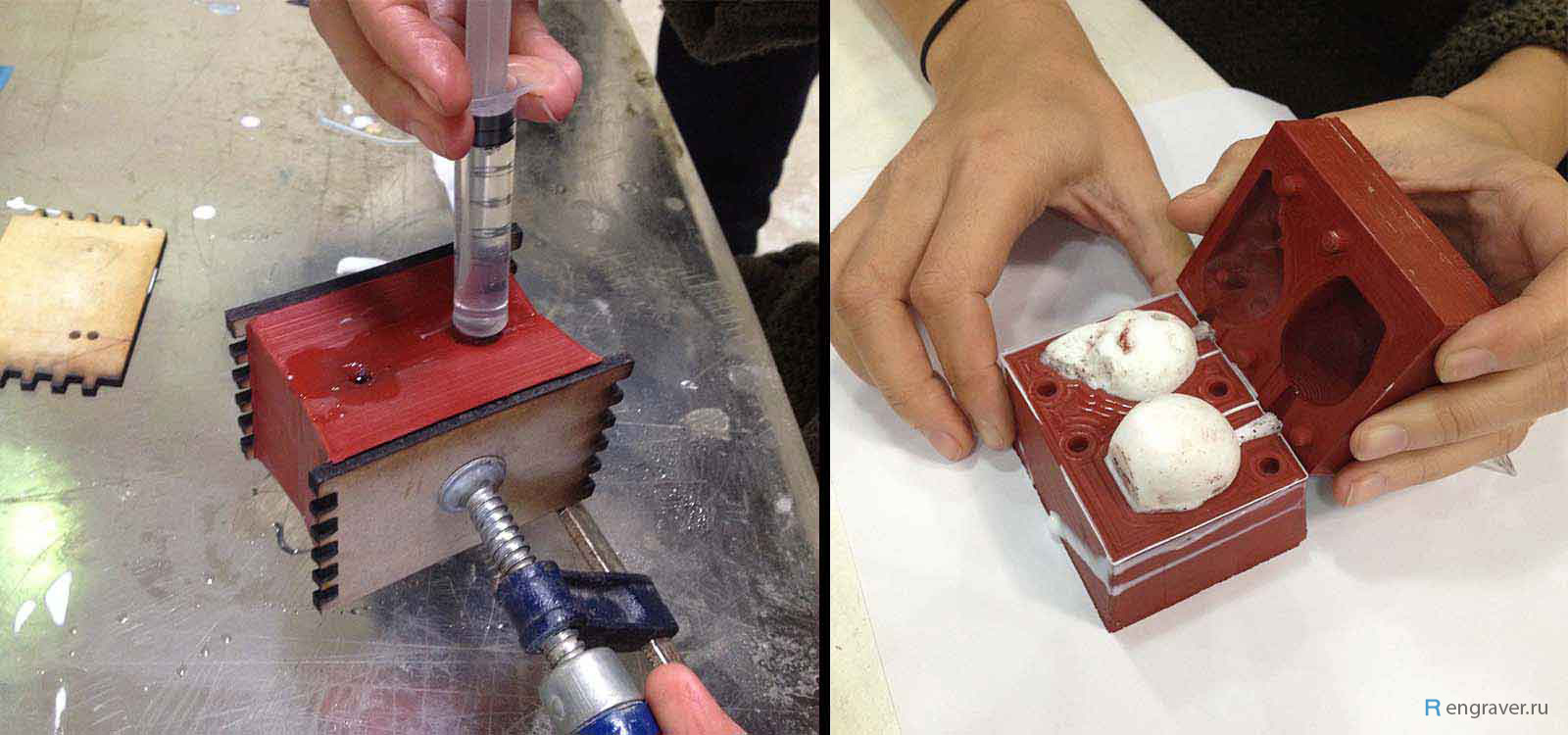
Материалы:
- пистолет для герметиков;
- стальная трубка;
- асбестовый шнур;
- нихромовая нить;
- провод с вилкой;
- механический терморегулятор от электродуховки;
- пластиковая бутылка от моющего средства;
- скотч;
- песок;
- гипсовая штукатурка.
Изготовление экструдера
На отрезок стальной трубы равной по длине тубу для герметиков наматывается асбестовый шнур. Важно, чтобы торец трубы был заварен и имел небольшое центральное отверстие.
Поверх асбеста наматывается нихромовая нить. Ее можно получить из выровненной спирали от электроплиты.
Затем спираль закрывается новой обмоткой из асбестового шнура.
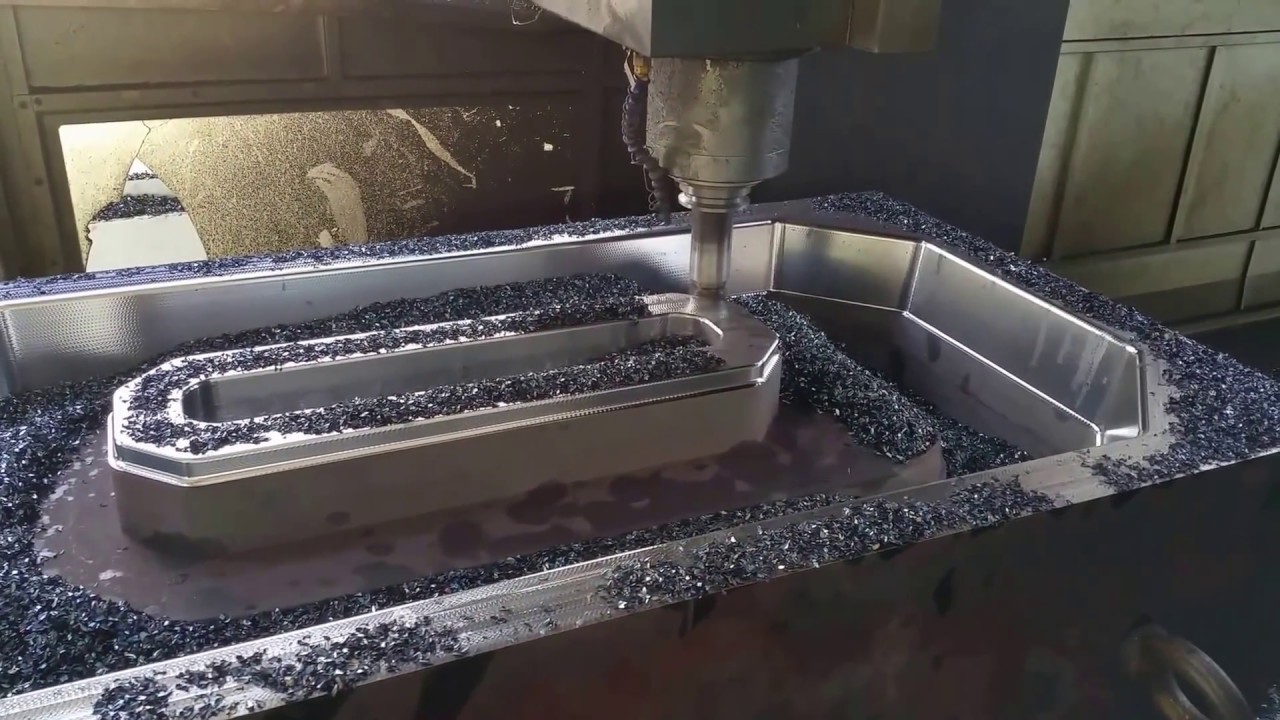
На пистолет от герметиков закрепляется механический терморегулятор от духовки. Его нужно закрепить так, чтобы ручка регулировки располагалась с тыльной стороны пистолета.
Из пластиковой бутылки от моющего средства изготавливается форма для литья в виде трубы. Для этого у нее срезается дно и горловина, после чего она распускается вдоль.
С одной стороны заготовка подгибается, и на изгибе вырезаются зазубрины. Полученный лист наматывается на любую трубку диаметром около 5 см. Затем заготовка закрепляется скотчем. Зазубрины при этом формируют ее дно. Сбоку полученной формы нужно сделать небольшое отверстие равное диаметру термодатчика. В него требуется вставить трубку из свернутого листового пластика.
Затем в форму из бутылки помещается стальная трубка с обмоткой из нихромовой нити и асбестового шнура. С одной стороны она фиксируется вырезанными зазубринами. Боковая трубка прижимается вплотную к обмотке. Концы нихромовой нити выводятся в отверстия по краям формы.

Далее в пустое пространство между пластиковой оболочкой и стальной сердцевиной заливается термостойкий раствор, приготовленный из песка и гипсовой штукатурки.
После застывания раствора верхняя трубка из обрезанной бутылки удаляется.
В боковое отверстие свободное от раствора устанавливается термодатчик, который закрепляется хомутом. Концы нихромовой нити подключаются к электрокабелю с вилкой. Внутрь стальной трубы засыпается пластиковая крошка. Это может быть HDPE пластик из мелко нарезанных крышечек от ПЭТ бутылок, или ABS пластик, который можно получить из корпусов старой бытовой техники.
Далее заправленная пластиком труба устанавливается в пистолет для герметиков. В нее запускается шток пистолета с тарелкой. Если тарелка окажется большой, то ее нужно предварительно обточить. Теперь включив вилку в розетку и отрегулировав температуру можно разогреть массу. Затем привычными движениями рычага пистолета ее следует выдавить.
Полученный экструдер можно использовать по-разному.

Смотрите видео
Переплавка пластиковых бутылок в домашних условиях — как расплавить пластмассу и зачем
В этом руководстве я расскажу вам, как плавить пластмассу в домашних условиях. Переплавка пластиковых бутылок из полиэтилена высокой плотности (HDPE) и изготовление из них блоков, которые можно использовать разными способами.
Каждый день мы используем и выбрасываем много пластиковых бутылок… Давайте изменим это!
Дэйв Хаккенс удивительный парень, который сделал много видео об утилизации пластика. Он показывает, как собирать, расплавлять и обрабатывать пластиковые предметы, чтобы создавать новые вещи.
Шаг 1: Материалы и инструменты
МАТЕРИАЛЫ:
- Бутылки из полиэтилена высокой плотности (HDPE)
- Деревянные дощечки (для изготовления формы)
ИНСТРУМЕНТЫ:
- зажимы
- бумага для выпечки
- перчатки с термозащитой
- ножницы/нож
Шаг 2: Форма
Нет необходимости делать очень сложную форму для плавки пластика.
Поскольку мы собираемся расплавить пластик и получить обычный блок, нам нужна простая коробка. Чем точнее и аккуратнее будет собрана коробка, тем точнее и аккуратнее будет блок.
Как вы можете видеть из приведенных выше рисунков, я использовал деревянные доски, которые лежали в моей мастерской, так же я накрыл каждую внутреннюю поверхность коробки бумагой для выпечки. Это будет важно позднее, когда будем извлекать блок из формы. Древесина — пористый материал, а расплавленный пластик — очень липкий, так что не стоит им соприкасаться.
Шаг 3: Как разрезать бутылки
Прежде всего, HDPE, что это такое? Как можно отличить его от всех других видов пластика?
HDPE — полиэтилен высокой плотности. Это довольно распространенный материал, используемый специально для производства пластиковых бутылок и коррозионностойких трубопроводов.
Как вы можете видеть на рисунке №1, его легко отличить от другого типа пластика благодаря цифре «2» в качестве идентификационного кода смолы.
После удаления этикеток и мытья бутылок нам нужно разрезать их на мелкие кусочки. Чем меньше, тем лучше, так как потребуется меньше времени для плавления. Используйте нож или крепкие ножницы.
Обычно я начинаю с ножа, отрезаю горлышко (фото № 2), которое является более жесткой частью, затем отрезаю основание и, наконец, ручку.
После этого вы можете использовать ножницы, чтобы сделать из больших кусков более мелкие (фото № 4).
Шаг 4: Плавление
Каждый тип пластика имеет разную температуру плавления.
Дэйв Хаккенс отлично изучил каждый тип, чтобы индивидуализировать правильную точку плавления (здесь вы можете увидеть его работу).
Я узнал, что в моей печи HDPE обычно плавится при температуре около 180°C.
В то время пока нагревается духовка, положите кусок бумаги для выпечки на противень и расположите на ней кусочки пластика. Наконец поместите противень в духовку и проверяйте его каждые 10 минут.
Шаг 5: Эффект мрамора
Первый раскрас, который я покажу вам, мой любимый: эффект мрамора.
Через 10/15 минут, если вы видите, что пластик выглядит липким, вы можете вытащить его из духовки. Оденьте жаростойкие перчатки и скрутите пластик (фото № 2/3).
Действуйте быстро (пластик остывает), но имейте ввиду, что он очень горячий и липкий.
Как только у вас получится что-то вроде того, что вы можете увидеть на фото №4, вы можете положить обратно в духовку.
ПРЕДУПРЕЖДЕНИЕ: Используйте перчатки! Если пластик попал на вашу кожу, немедленно промойте пораженное место холодной водой, чтобы уменьшить боль.
Шаг 6: Закрепляем форму
Через 10 минут извлеките пластик из духовки и положите его в форму. Зажмите его так сильно, как можете, и каждые 5 минут, затягивайте зажимы сильнее. HDPE сжимается, когда он остывает, поэтому, чтобы получить плоский блок, вы должны часто затягивать зажимы.
Шаг 7: Мраморный блок
Это результат после 2 часов охлаждения.
Как видно из фото, благодаря технике крутильно-вращательного движения, которую мы использовали, получился прекрасный эффект мрамора. Мне очень нравится этот метод, потому что вы можете видеть все используемые цвета.
Шаг 8: Эффект «Камуфляжа»
Вот еще один раскрас. Я называю его эффектом камуфляжа.
Это проще и безопаснее, чем эффект мрамора, потому что нет нужды касаться пластика руками. Как и в Шаге 5, после 10/15 минут, если вы видите, что пластик выглядит липким, вы можете извлечь его из духовки.
На этот раз мы будем использовать технику складывания. Очень аккуратно (и всегда используйте перчатки), поднимите бумагу для выпечки с одной стороны и сложите пластик на себя (фото № 2).
Повторите тоже самое с другой стороны и положите обратно в духовку.
Шаг 9: Закрепляем форму
После 10 минут плавления выньте пластик из духовки, сложите в последний раз, сделав что-то вроде яичного рулета (фото № 1) и поместите его в форму.
Как и на шаге 6, зажмите его так сильно, как можете, и возвращайтесь каждые 5 минут, чтобы затянуть зажимы. Затем оставьте его остывать на пару часов.
Шаг 10: Камуфляжный блок
Вот результат. Выглядит действительно как камуфляж.
Шаг 11: Что можно сделать из блоков?
Эти блоки невероятно прочные, простые и тяжелые. Вы можете использовать их по-разному.
На фотографии № 3 вы можете увидеть, кастет, спиннер, несколько брелков и юлу. На сайте preciousplastic вы можете найти другие способы применения HDPE, такие как, например, плитка — фото № 1.
Шаг 12: Самодельная юла
Вот пример того, что вы можете сделать с помощью единственной бутылки из-под моющего средства.
Прежде всего, я удалил этикетку, и я очень хорошо промыл бутылку, избавляясь от всех мыльных остатков. Затем я расплавил пластик в тонкий блок (по методу, показанному на предыдущих этапах), и я сплющил его до толщины 5 мм (фото № 2).
Я нарисовал юлу, состоящую из 3-х частей и приклеил шаблон к блоку. Затем, разрезал все фигуры по линиям с помощью лобзика и отшлифовал вручную все края.
Спустя 2 часа, после того как я сделал блок из бутылки, и двадцати минут работы над блоком, у меня получилась эта классная юла.
Надеюсь, вам понравилось, и вы попытаетесь переработать несколько пластиковых бутылок, сделав из них что-нибудь интересное.
Спасибо, что прочитали мое руководство!
Литье пластмасс под давлением на заказ (онлайн-предложения)
Уникальные формы, неслыханные конструкции нестандартных пластиковых деталей? Нет проблем.
Мы любим вызовы. Мы помогли некоторым из наших клиентов реализовать проекты, которых не коснулся бы ни один другой производитель пластмасс на заказ. Мы доставили готовый продукт, который поразил и порадовал клиентов, которые почти исчерпали свои возможности.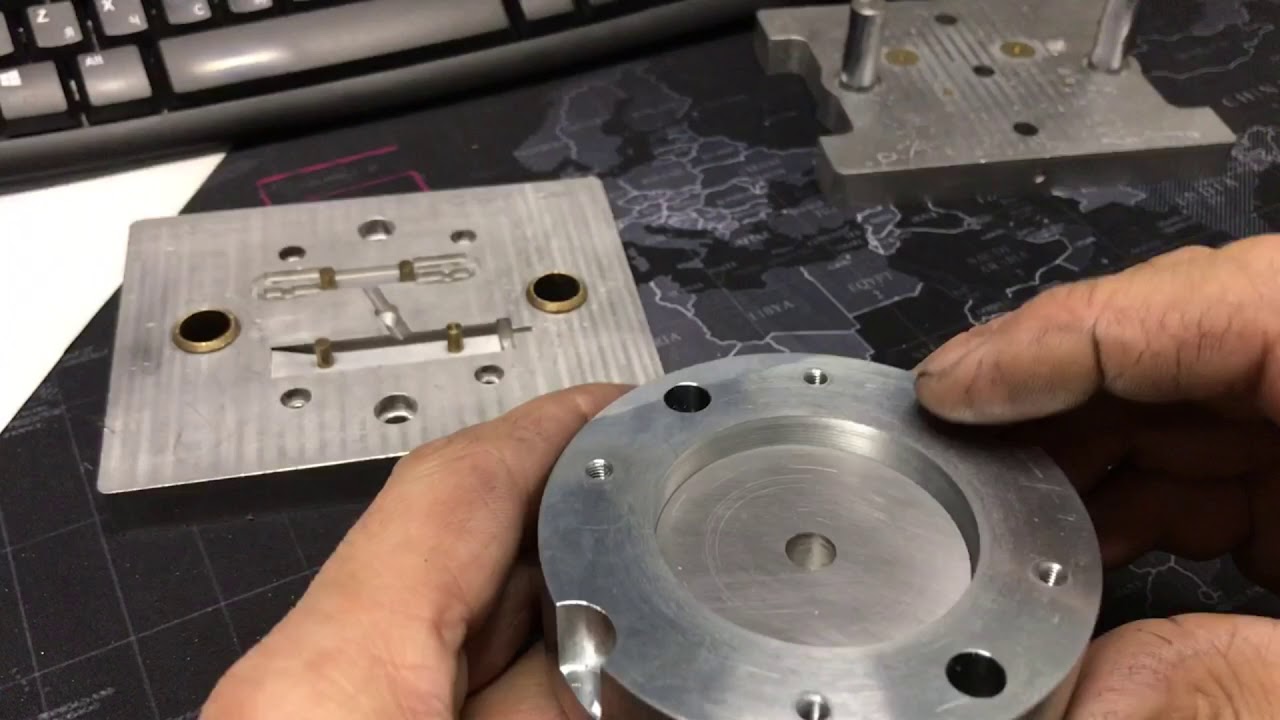
Иногда для достижения цели превзойти своих конкурентов требуется уникальная форма или иной необычный производственный дизайн из пластика.Наши смелые и креативные дизайнеры пресс-форм будут работать с вами, чтобы помочь разработать решение, которое достигнет этого — систему производства пластиковых деталей на заказ, соответствующую вашим требованиям к продукту, бюджету и срокам.
Мы можем производить самые сложные детали — длиной до 48 дюймов — с почти неограниченным количеством слайдов и вставок. Мы разработали наши Рекомендации по проектированию литья пластмасс под давлением, чтобы вы могли легко понять, может ли пластиковая деталь быть литьевой под давлением.
Наши Гарантированный срок службы Формы спроектированы и изготовлены из высококачественной стали. Качество любой пластмассовой детали, изготовленной методом литья под давлением, зависит от точности инструмента. Бывают случаи, когда нестандартная пластиковая деталь должна точно соответствовать другим деталям, чтобы получилось законченное изделие. Становится жизненно важным, чтобы каждая пластиковая деталь была отформована из прецизионных инструментов, изготовленных в соответствии с точными производственными спецификациями пластмасс, и запускалась на соответствующих машинах для литья пластмасс под давлением. Мы с уверенностью подходим к этим проектам, потому что очень много успешно реализовали.
Гибкость. Командная работа. Находчивость.
Производитель нестандартного пластика должен быть дополнительным членом сплоченной команды. При этом важно избегать ненужных расходов из-за накладных расходов на изготовление пластика на заказ. Мы осознаем ценность сплоченных, простых отношений, в основе которых лежит четкое общение. Мы познакомимся с вами, вашим продуктом, репутацией и потребностями, чтобы мы могли работать вместе, как член вашей команды.
Выбранный вами производитель нестандартных пластиковых деталей станет важной частью производственного процесса.Компоненты, произведенные выбранным вами партнером-производителем, будут играть важную роль в повышении репутации вашей компании и повышении продаж продукции.
Мы знаем, как правильно, эффективно и экономично выполнять проекты литья пластмасс под давлением, даже в очень сложных сочетаниях конструкции, инструментов, объема, смолы и выбора оборудования.Большинство изделий из пластика на заказ можно изготавливать одним из нескольких способов. Команда экспертов ICOMold поможет вам решить, какой из них является наилучшим и наиболее экономичным.
Изоляционные материалы | Министерство энергетики
Полиуретан — это пенопластовый изоляционный материал, в ячейках которого содержится газ с низкой проводимостью. Изоляция из пенополиуретана доступна в формулах с закрытыми и открытыми ячейками. В пене с закрытыми порами ячейки с высокой плотностью закрываются и заполняются газом, который помогает пене расширяться и заполнять пространства вокруг нее. Ячейки пенопласта с открытыми порами не такие плотные и заполнены воздухом, что придает изоляции губчатую текстуру и более низкое значение R.
Как и пенополиизо, R-значение полиуретановой изоляции с закрытыми порами может со временем упасть, поскольку часть газа с низкой проводимостью уходит, а воздух заменяет его, что называется тепловым дрейфом или старением. Наибольший тепловой дрейф происходит в течение первых двух лет после изготовления изоляционного материала, после чего значение R остается неизменным, если только пена не повреждена.
Фольга и пластиковые покрытия на жестких пенополиуретановых панелях могут помочь стабилизировать R-значение, замедляя тепловой дрейф. Светоотражающая пленка, если она установлена правильно и обращена к открытому пространству, также может действовать как лучистый барьер. В зависимости от размера и ориентации воздушного пространства это может добавить еще один R-2 к общему тепловому сопротивлению.
Полиуретановая изоляция доступна в виде вспененного жидкого вспененного материала и жесткого пенопласта. Из него также могут быть изготовлены ламинированные изоляционные панели с различными покрытиями.
Нанесение полиуретановой изоляции распылением или вспенением на месте обычно дешевле, чем установка пенопластов, и эти приложения обычно работают лучше, потому что жидкая пена формируется на всех поверхностях. Вся производимая сегодня изоляция из пенополиуретана с закрытыми порами производится с использованием газа, не содержащего ГХФУ (гидрохлорфторуглерод), в качестве вспенивающего агента.
Пенополиуретан низкой плотности с открытыми ячейками использует воздух в качестве вспенивателя и имеет значение R, которое не меняется со временем.Эти пены похожи на обычные пенополиуретаны, но более гибкие. Некоторые сорта с низкой плотностью используют в качестве пенообразователя диоксид углерода (CO2).
Пена низкой плотности распыляется в открытые полости стенок и быстро расширяется, герметизируя и заполняя полости. Также доступна медленно расширяющаяся пена, которая предназначена для полостей в существующих домах. Жидкая пена расширяется очень медленно, что снижает вероятность повреждения стены из-за чрезмерного расширения. Пена проницаема для водяного пара, остается эластичной и устойчива к впитыванию влаги.Он обеспечивает хорошую герметичность, огнестойкость и не поддерживает пламя.
Также доступны жидкие пенополиуретаны на основе сои. Эти продукты могут применяться с тем же оборудованием, что и для пенополиуретанов на нефтяной основе.
Некоторые производители используют полиуретан в качестве изоляционного материала в конструкционных изоляционных панелях (СИП). Для изготовления СИП можно использовать пенопласт или жидкую пену. Жидкая пена может быть впрыснута между двумя деревянными обшивками под значительным давлением, и после затвердевания пена создает прочную связь между пеной и обшивкой.Стеновые панели из полиуретана обычно имеют толщину 3,5 дюйма (89 мм). Толщина потолочных панелей составляет до 7,5 дюймов (190 мм). Эти панели, хотя и более дорогие, более устойчивы к возгоранию и диффузии водяного пара, чем EPS. Они также изолируют на 30-40% лучше при заданной толщине.
ИНСТРУМЕНТ: что вы можете сделать с формированием пресс-формы
В этом месяце я хотел бы обсудить накопление в полостях формы и некоторые решения для решения этой проблемы, как профилактику, так и очистку.Существует множество основных причин накопления плесени, от отсутствия вентиляции, выпадения пластика, остатков пластика, вызывающих обесцвечивание полости, и огнезащитных добавок, до разложенного материала из-за нагрева, превышающего рекомендованное, или из-за того, что пластик остается в стволе. а не продувка. Накопление может вызвать проблемы с глянцем деталей, визуальные дефекты и проблемы с прилипанием.
У меня есть опыт работы со многими материалами, но не со всеми, поэтому некоторые из вас будут знать из первых рук о проблемах накопления с другими материалами, не упомянутыми здесь.Прокомментируйте и поделитесь, если вы это сделаете.
На некоторых более дешевых сортах материалов, особенно на более дешевых поликарбонатах, со временем на поверхности полостей может образовываться неприятный густой налет, вызывающий проблемы с внешним видом и прилипанием. Эти отложения бывает очень трудно удалить. Единственное, что я обнаружил, что можно сделать с инструментами для уменьшения, а не устранения, накоплений и помощи в процессе очистки, — это нанести покрытие на полости. Я предпочитаю алмазный хром. Это обеспечивает очень твердую поверхность, которая помогает противостоять налипанию и защищает отделку поверхности полости.
У меня также были проблемы налипания с нейлонами, содержащими добавки, такие как УФ-стабилизаторы и модификаторы удара, когда наросты вызывают визуальные дефекты с непостоянным блеском на детали. Это может потребовать очень частой очистки полостей для поддержания характеристик блеска, и могут возникнуть проблемы, если не используются надлежащие методы очистки. Лучшее решение, которое я нашел с этим типом отложений, — это снова покрытие инструмента алмазным хромом, который имеет большое значение для уменьшения отложений и защиты полостей и блеска при необходимости очистки.
Некоторые из вас, без сомнения, думают: «Это стоит денег», и да, это так. Но если проблемы с качеством деталей, временем и трудозатратами на очистку оправдывают затраты, то окупаемость есть. Если деталь имеет жесткие характеристики глянца, вызывая брак или брак, стоимость покрытия полостей минимальна в целом.
Накопление из-за недостаточной вентиляции может вызвать визуальные дефекты детали и простои из-за необходимости чистки инструмента в прессе. Методы вентиляции — это отдельная тема, поэтому я не буду вдаваться в подробности здесь.Области в полости, где такое скопление обычно является обычным, — это области конца заполнения, детали, задерживающие газ, и линии сшивки.
Некоторые материалы более склонны к газообразованию и скоплению, чем другие, особенно стеклонаполненные материалы. Но любой материал может оставить следы газообразования, если инструмент не вентилируется должным образом. Это проявится в виде коричневатых пятен на стали, что также может привести к эрозии. Этот нарост с течением времени также может проявляться в виде незаполненной области на детали, особенно в глубоких ребрах и деталях с ПК и ПК / АБС. Очистить полость от деталей бывает сложно.
Эти области не всегда легко или недорого удалить, поскольку они не находятся на поверхности линии разделения. Обычно для них требуется вставка, выталкивающий штифт или вентиляционный штифт для выхода газа, а также их очистка во время обслуживания инструмента.
Многие формовщики обрабатывают детали вокруг ожогов, что иногда является необходимостью, но создает другие проблемы, связанные с изменением скорости впрыска в процессе. Таким образом, в таких ситуациях необходимо максимально увеличить вентилирование, прежде чем использовать переработку в качестве решения.Иногда может быть тонкая грань между вспышкой и ожогами, в зависимости от навыков и знаний мастера. Бывают также случаи, когда язычок перелива необходим на некоторых крупных деталях, на которых идет стеклонаполненный материал на линиях вязания в конце заполнения. Вентиляция всегда должна быть в центре внимания при разработке инструмента, уделяя внимание используемому материалу (см. Также столбец за январь).
Другой тип отложений, который я видел, — это остатки, которые некоторые материалы оставляют по всей поверхности полости.Это обесцвечивает полость и может приобретать коричневатый оттенок. Со временем это может повлиять на блеск детали и способствовать прилипанию. Я никогда не наносил покрытия на полость, чтобы предотвратить образование такого типа, потому что для его появления могут потребоваться тысячи циклов.
Таким образом, по моему опыту, эта форма накопления обычно не является большой проблемой, и с ней можно справиться в рамках регулярного технического обслуживания инструмента. Не путайте это образование с обесцвечиванием стали в результате теплового воздействия. Мелкие стальные детали или участки с недостаточным охлаждением могут обесцвечиваться из-за сильной жары.
Обработка также может способствовать скоплению в ваших полостях. При использовании верхнего предела или выше рекомендованного диапазона для материала повышается вероятность образования побочных продуктов выделения газов, которые приведут к накоплению. Как упоминалось выше, добавки могут способствовать образованию отложений, особенно антипирены при работе при более высоких температурах или когда расплав остается в стволе. И, как многие из вас, читатели, слишком хорошо знают, что некоторые материалы очень быстро разлагаются, если их запечь в бочке.
Как упоминалось в моих предыдущих столбцах, моя цель — всегда сосредотачиваться на инструменте, чтобы предоставить большое окно процесса и решить проблемы. Но в случае образования отложений я обнаружил, что все, что я действительно могу сделать, это попытаться защитить полости с помощью покрытия и сократить интервалы очистки. Таким образом, решение проблемы отложений требует очистки и дополнительного обслуживания инструмента. Типичными методами удаления отложений являются струйная очистка (оксид алюминия, стеклянные шарики и др.), Струйная очистка сухим льдом или ручная полировка инструментальщиком или техником.
В прошлом году я также разработал и выпустил на рынок новый очиститель. Он растворяет налет (и ржавчину), не вызывает коррозии и делает возможной очистку в прессе. Он называется Zap-Ox, и вы можете узнать о нем подробнее здесь.
ОБ АВТОРЕ: РЕНДИ КЕРКСТРА
Рэнди Керкстра работает в индустрии пластмасс более 26 лет и часто занимается поиском и устранением неисправностей при литье под давлением. В настоящее время он является менеджером по оснастке в большой многопрофильной формовочной и производственной компании.
.