3D-принтер для чайников: как перестать бояться и начать печатать
Технологии 3D-печати, еще несколько лет назад казавшиеся дорогими и недоступными, с каждым днем становятся все ближе к нам. Сейчас на рынке представлено большое количество моделей 3D-принтеров, простых в управлении и доступных по цене. Выбрать 3D-принтер для начинающих теперь стало гораздо проще.
Источник: https://www.brooklinelibrary.org
Присутствуют даже модели, которыми могут пользоваться дети. Как начать печатать 3D-модели с нуля? Мы расскажем об этом подробно.
Суть технологии 3D-печати
3D-печать – это технология, при которой 3D-принтер создает материальный трехмерный объект по компьютерной модели, разработанной в программе 3D-моделирования или на основе 3D-скана. 3D-принтер – это устройство с программным управлением, которое использует данные компьютерной трехмерной модели для послойного создания физического объекта.
Источник: https://www.solvay.com
Существует много распространенных и хорошо себя зарекомендовавших технологий 3D-печати, и специалисты продолжают работать над их усовершенствованием. Однако лидерство прочно удерживают несколько наиболее удобных в применении технологий – это FDM (fused deposition modeling – моделирование методом наплавления) и стереолитография — SLA (laser stereolithography – лазерная стереолитография) и ее аналог DLP.
Как начать печатать в 3D быстро и легко
Итак, вы решили приобрести 3D-принтер – с чего начать? Прежде всего нужно разобраться в их видах. Принтеры различаются технологиями, по которым они работают – FDM, SLA или DLP, и техническими параметрами. Разберем, какие характеристики имеют эти устройства и на что нужно ориентироваться, выбирая принтер для начала печати.
Характеристики 3D-принтера
Присматриваясь к FDM-моделям принтеров, кроме цены, обращайте внимание на такие параметры:
- Область печати – это габариты или объем той фигуры, которую можно напечатать на данном устройстве. Указывается в см3 или соотношении длины, ширины и высоты готового изделия. Рекомендуемые габариты для начинающих печатников – от 200 х 200 х 200 мм.
- Доступная скорость печати (от 40 до 150 мм/сек и даже выше).
- Разрешение печати или толщина слоя. Они напрямую связаны с внешним видом готового изделия. Начинающему пользователю стоит выбирать принтер с разрешением 50-100 мкм. Чем ниже разрешение, тем грубее выглядит готовая деталь.
- Экструдер – деталь принтера, через которую подается расплавленный материал для печати. Существуют экструдеры для печати несколькими материалами и принтеры с несколькими экструдерами, это позволяет использовать разные материалы и цвета.
Источник: https://all3dp.com
Перед началом печати на 3D-принтере следует определиться с целями, для которых будет использоваться принтер — от них будут зависеть конструктивные особенности аппарата; определитесь с размерами изделий – от них будет зависеть рабочий объем будущего принтера; всё это повлияет на цену.
Материалы
Два наиболее популярных материала для 3D-печати по технологии FDM, с которыми начинают работать новички – это пластики ABS и PLA. ABS – прочный и долговечный материал, широко распространенный и популярный, устойчив к ударам. Из ABS делаются, например, детали интерьера в авто и конструкторы LEGO, как и многое другое. PLA – биоразлагаемый нетоксичный полимер на основе молочной кислоты, получаемой из кукурузы и сахарного тростника — экологичная замена ABS. Материал хорошо держит форму, выдерживает трение, подходит для создания подвижных деталей.
Большинство принтеров поддерживают работу с несколькими видами пластика.
Источник: filamentguide.net
Если вы планируете начать работу с SLA или DLP-принтером, то важными параметрами будут рабочий объем, точность печати, которая в случае с SLA-технологией намного выше, чем у FDM-моделей, цена расходных материалов и самого устройства.
Источник: all3dp.com
Подготовка к 3D-печати
Разработка модели
Начинать печатать в 3D лучше с простых моделей — геометрических фигур несложной конструкции. Модели можно разработать самостоятельно, с помощью специальных компьютерных программ. Наиболее легкие и часто используемые:
- OpenSCAD;
- AutoCad;
- FreeCad;
- GoogleSketchUp;
- Ble
Технология 3D-печати в промышленности — Мanufactory-Industry-Design
Аддитивное производство за последние 7 лет получило невероятный толчок развития. Возможность создавать изделия сложных геометрических конфигураций открыло перед трехмерной печатью дорогу в промышленные и научные сферы. Модели, построенные по цифровым аналогам, не уступают по качеству традиционным деталям. Стоит ли утверждать, что за такой инновационной технологией стоит будущее? Попробуем проанализировать все факты и разобраться о перспективах технологии 3D-печати.
В этой статье будет рассказано о том, где и как применяется 3D-печать в промышленной сфере. Сумеет ли она заменить традиционные механические способы обработки или останется полем для тестирования? Прочитайте статью до конца и получите ответы на эти вопросы.
Какие принципы лежат в основе работы 3D-притнера?
Работа промышленного 3D-принтера строится на обработке трехмерных графических файлов с геометрическими параметрами будущего объекта. Создаются они инженерами вручную на компьютере или путем сканирования реальных прототипов.
Устройство обрабатывает данные с файлов и формирует структуру из слоев жидкого, порошкообразного или листового материала. Будущая деталь образуется последовательным соединением слоев через поперечные сечения. Каждый микрон поверхности соответствует виртуальным параметрам графической модели и сплавляется воедино в цельную модель готовой формы.
В каких отраслях применяется трехмерное производство?
Технология 3D-печати стала противоположностью привычным фрезеровальным и режущим станкам. В стандартном производстве детали формируется путем удаления лишних слоев. В 3D-принтерах ситуация строится противоположным способом. Здесь отсутствуют отходы материалов и достигается максимальная точность изготовления. Именно это позволяет коммерческим предприятиям и заводам обращать все большее внимание на экономически выгодную технологию производства.
Трехмерная печать успешно закрепились в 5 отраслях:
- строительной;
- автомобильной;
- аэрокосмической;
- медицинской;
- военной.
Связанно это с тем, что методика позволяет создавать геометрические формы неограниченной сложности. Таких результатов невозможно достичь с ограниченностью стандартного производственного оборудования. Перед инженерами и конструкторами открываются новые возможности и перспективы развития революционных технологий. Но какие материалы получается обрабатывать?
Из каких материалов делаются изделия на 3D-принтерах?
К 2017 году для аддитивного производства в промышленной сфере доступно больше 10 методов. Отличаются они технологией формирования слоев и обрабатываемых материалов. Каждый отдельный способ открывает возможности создания моделей из термопластиков или даже титановых сплавов.
Рассмотрим детально 5 основных методик:
- Моделирование методом послойного наплавления. Экструзионная методика позволяет использовать для работы термопластики, включая полилактиды.
- Моделирование форм методом электронно-лучевой плавки . Проволочный и порошковый методы дают возможность создавать изделия из большинства стандартных сплавов металла.
- Прямое лазерное спекание металлов. Технология порошкового метода позволяет создавать титановые сплавы, которые отличаются высочайшей прочностью и свойствами
- Выборочная лазерная плавка. Кроме титановых изделий можно создавать объекты из сплавов кобальт-хрома, нержавеющей стали и алюминия. Изделия отличаются высокой плотностью и не уступают механически обработанным аналогам.
- Выборочное лазерное спекание. Методика вместе с металлами позволяет изготавливать модели из полистирола, армированного стекловолокна, полиамидов и армированного углеволокна.
С 3D-технологией промышленное производство получило возможности значительно ускорить рабочие процессы, а затраты на реализацию готового изделия снизить в разы.
Перспективы и инновационные разработки на 3D-принтерах
В 2015 году General Electric успешно запустило производство сопел для ракетных двигателей. Крупногабаритные принтеры выпускают инновационную продукцию для двигателей нового поколения из композитного углеродного волокна и композитов с керамической матрицей (CMC). Этапы тестирований уже доказали, что полученные сопла в 5 раз прочнее предшественников. Достигается это за счет того, что конструкция имеет цельную монолитную форму. Больше не требуется собирать детали из 30 отдельных частей и постоянно добавлять сварные швы и припои.
Британская компания Rolls-Royce использует 3D-технологию для создания авиадвигателей, наравне с другими авиастроителями. С помощью инновационных методик запущен процесс создания отдельных элементов и деталей для двигателей. Руководители проектов видят перспективы и говорят о возможностях экспериментировать с параметрами изготавливаемых конструкций. Принтеры позволяют легко изменить геометрические параметры деталей, не меняя при этом всю производственную линию.
Аналогичным образом используют аддитивные технологии трехмерной печати компании NASA и AirBus. Если последняя использует принтеры для изготовления авиационных деталей, то космический гигант нацелен на покорение космоса. В 2016 году был запущен проект Sinterhab, который позволит «печатать» базы прямо на поверхности луны. В качестве строительного материала будет использоваться лунный реголит, из которого будут создавать цельные строительные блоки. NASA также рассматривает перспективы автономной печати ремонтных частей и деталей прямо с орбиты корабля. В будущем на этом планируется сэкономить миллиарды вместо затратных транспортировок грузовых шатлов.
Будущее уже наступило. Применение 3D-принтеров в коммерческой сфере
Самое главное – технология трехмерной печати уже доступна обычным коммерческим предприятиям. Если раньше позволить себе крупногабаритный 3D-принтер могли только крупные компании, то сейчас стоимость оборудования доступна и обычным фабрикам. Средняя цена промышленного принтера находится в диапазоне от 5000 до 15000$.
На рынке промышленного оборудования в свободном доступе уже представлены свыше 100 моделей. Основные отличия заключаются в размерах печатных изделий, материалах для изготовления, скорости создания и технологии нанесения слоев.
- 3D-принтеры BetAbram и WinSun. Используются в строительных компаниях для создания настоящих полноразмерных домов. Проекты пользуются большой популярностью в Европе и Америке. Он создает отдельные элементы для каркасных домов со сложной архитектурной формой.
- 3D-принтер Concept Laser X-Line 2000R. Позволяет плавить металл и создавать из него промышленные компоненты для деталей машиностроения. Полученные изделия ничем не отличаются по свойствам от деталей, сделанных на обычных станках. При этом скорость производства увеличивается на 35%.
- 3D-принтер Stratasys Rortus 900mc. С его помощью компании создают сверхточные детали, инструменты и прототипы для других заводов. Методика позволяет изготавливать сверхточные шаблоны для литейного производства, запчасти и прототипы многих устройств.
Если обобщить информацию, то появляется смелый вывод. 3D-печать нашла активное применение в промышленности. Технология была доступна еще 30 лет назад, но высокая себестоимость не позволяла предприятиям в полной мере использовать возможности аддитивных разработок. Результаты 2017 года говорят о том, что промышленная 3D-печать не остановиться на достигнутом, а станет революционным методом в решении сложных инженерных задач.
www.tehnohacker.ru
3D-печать металлами — технологии и принтеры / Top 3D Shop corporate blog / Habr
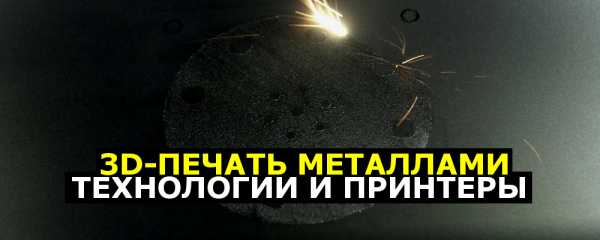
3D-печать металлом становится все более популярной. И это не удивляет: каждый металлический материал для печати предлагает уникальное сочетание практических и эстетических свойств для того, чтобы удовлетворить требования предъявляемые к различным продуктам, будь то прототипы, миниатюры, украшения, функциональные детали или даже кухонные принадлежности.
Причины печатать металлами настолько веские, что 3D-печать металлами уже внедряется в серийное производство. На самом деле, некоторые 3D-печатные детали уже догнали, а какие-то и превзошли своими свойствами те, что производятся традиционными методами.
Традиционное производство из металлов и пластиков очень расточительно — в авиапромышленности, например, до 90% материалов уходит в отходы. Выход продукции, в некоторых отраслях, составляет не более 30% от использованного материала.
3D-печать металлами потребляет меньше энергии и сокращает количество отходов до минимума. Кроме того, готовое 3D-печатное изделие может быть до 60% легче, по сравнению с фрезерованной или литой деталью. Одна лишь авиационная промышленность сэкономит миллиарды долларов на топливе — за счет снижения веса конструкций. А ведь прочность и легкость нужны и в других отраслях. Да и экономичность тоже.
3D-печать металлом дома
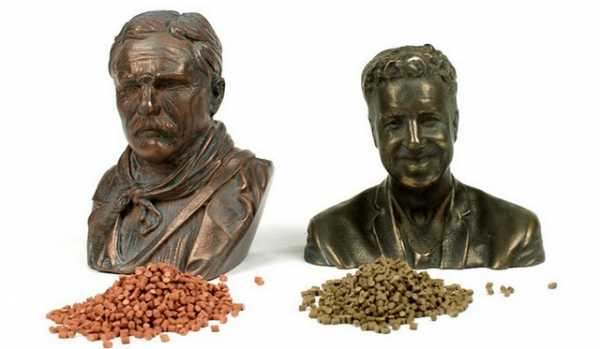
Что можно сделать, если появилось желание попробовать 3D-печать металлом в домашних условиях? Для печати металлом необходимы чрезвычайно высокие температуры, вряд ли вы сможете использовать обычный FDM 3D-принтер для этого, по крайней мере пока. Ситуация может измениться через несколько лет, но сейчас домашней 3D-технике это недоступно.
Если вы хотите сделать выглядящие металлическими распечатки у себя дома, лучший вариант — использование пластика содержащего частицы металла.
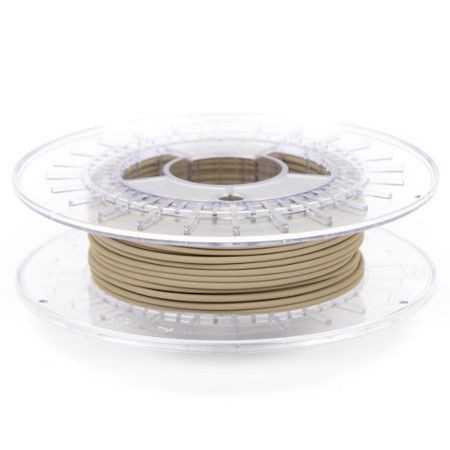
Такого например, как Colorfabb Bronzefill или Bestfilament Bronze.
Эти филаменты содержат значительный процент металлических порошков, но и достаточно пластика — для печати при низкой температуре любым 3D-принтером. В то же время, они содержат достаточное количество металла, чтобы соответственно выглядеть, ощущаться и иметь вес близкий к весу металлического предмета.
Изделия из филамента содержащего железо даже покрываются ржавчиной в определенных условиях, что добавляет правдоподобности, а вот проржаветь насквозь и испортиться от этого не смогут — и в этом их преимущество перед настоящими металлическими предметами.
Плюсы таких материалов:
- Уникальный внешний вид распечаток
- Идеально подходит для бижутерии, статуэток, предметов домашнего обихода и декора
- Высокая прочность
- Очень малая усадка во время охлаждения
- Подогреваемый стол не обязателен
Минусы:
- Низкая гибкость изделий, зависит от конструкции распечатки
- Не считается безопасным при контакте с пищей
- Требует тонкой настройки температуры сопла и скорости подачи филамента
- Необходима постобработка изделий — шлифовка, полировка
- Быстрый износ сопла экструдера — филамент с металлом очень абразивен, по сравнению с обычными материалами
Общий температурный диапазон печати обычно составляет 195°C — 220°C.
3D-печать металлом в промышленности

Если вы хотите приобрести 3D-принтер печатающий настоящим металлом, для использования на предприятии, то тут для вас две новости — хорошая и плохая.
Хорошая новость состоит в том, что их ассортимент достаточно широк и продолжает расширяться — можно будет выбрать такой аппарат, который соответствует любым техническим требованиям. Далее в статье можно убедиться в этом.
Плохая же новость одна — цены. Стоимость профессиональных печатающих металлом принтеров начинается где-то от $200000 и растет до бесконечности. Кроме того, даже если вы выберете и приобретете самый недорогой из них, отдельным ударом станет покупка расходников, плановое обслуживание с заменой узлов, ремонт. Не забываем и о персонале, и расходах на постобработку изделий. А на стадии подготовки к печати понадобится специальное ПО и умеющие обращаться с ним люди.
Если вы готовы ко всем этим тратам и трудностям — читайте дальше, мы представим несколько очень интересных образцов.
https://youtu.be/20R9nItDmPY
3D-печать металлом — применение
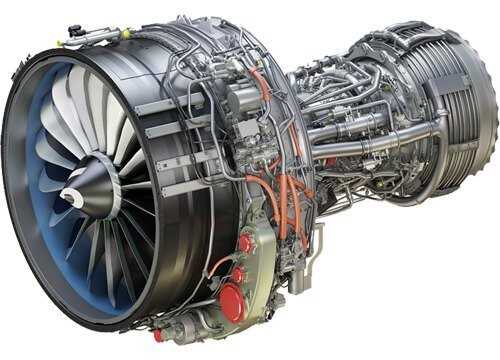
В некоторых промышленных секторах уже используют металлические 3D-принтеры, они стали неотъемлемой частью производственного процесса, о чем обычный потребитель может и не подозревать:
Наиболее распространенным примером являются медицинские импланты и стоматологические коронки, мосты, протезы, которые уже считаются наиболее оптимальным вариантом для пациентов. Причина: Они могут быть быстрее и дешевле изготовлены на 3D-принтере и адаптированы к индивидуальным потребностям каждого пациента.
Второй, столь же часто встречающийся пример: ювелирное дело. Большинство крупных производителей постепенно переходит от 3D-печати форм и восковок к непосредственной 3D-печати металлом, а печать из титана позволяет ювелирам создавать изделия невозможного ранее дизайна.

Кроме того, аэрокосмическая промышленность становится все более и более зависима от 3D-печатных металлических изделий. Ge-AvioAero в Италии — первая в мире полностью 3D-печатная фабрика, которая выпускает компоненты для реактивных двигателей LEAP.
Следующая отрасль использующая 3D-принтеры по металлу — автопром. BMW, Audi, FCA уже серьезно рассматривают применение технологии в серийном производстве, а не только в прототипировании, где они используют 3D-печать уже многие годы.
Казалось бы — зачем изобретать велосипед? Но и здесь 3D-печать металлом нашла применение. Уже несколько лет производители велосипедных компонентов и рам применяют 3D печать. Не только в мире, но и в России это получило распространение. Производитель эксклюзивных велосипедов Triton заканчивает проект с 3D-печатным элементом титановой рамы, это позволило снизить ее вес без ущерба прочности.

Но прежде, чем 3D-печать металлами действительно захватит мир, необходимо будет преодолеть несколько серьезных проблем. В первую очередь — это высокая стоимость и низкая скорость производства больших серий этим методом.
3D-печать металлом — технологии
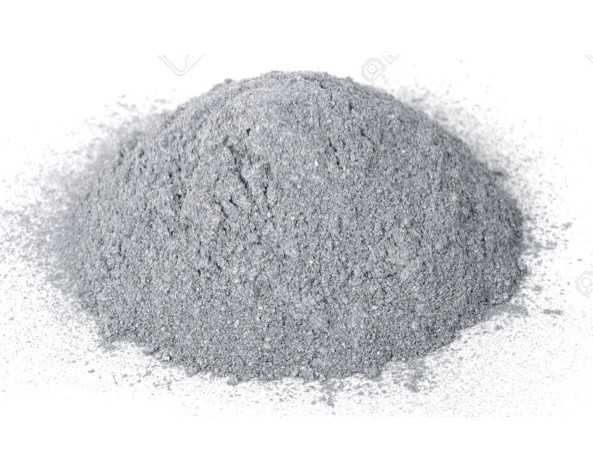
Многое можно сказать о применении печатающих металлом 3D-принтеров. Есть своя специфика, но основные вопросы такие же, как и с любыми другими 3D-принтерами: программное обеспечение и аппаратные ограничения, оптимизация материалов и печать несколькими материалами. Мы не будем говорить о программном обеспечении много, упомянем лишь, что наиболее крупные издатели, такие как Autodesk, SolidWorks и SolidThinking — все разрабатывают программные продукты для использования в объемной печати металлами, чтобы пользователи могли воплотить в жизнь изделие любой вообразимой формы.
В последнее время появились примеры того, что 3D-детали напечатанные металлом могут быть столь же прочными, как традиционно производимые металлические компоненты, а в некоторых случаях и превосходят их. Созданные с помощью DMLS, изделия имеют механические свойства такие же, как у цельнолитых аналогов.
Посмотрим же на имеющиеся металлические технологии 3D-печати:
Процесс # 1: Послойное сплавление порошка
Процесс 3D-печати металлами, которым наиболее крупные компании пользуются в наши дни, известен как сплавление или спекание порошкового слоя. Это означает, что лазерный или другой высокоэнергетический луч сплавляет в единое целое частицы равномерно распределенного металлического порошка, создавая слои изделия, один за другим.
В мире есть восемь основных производителей 3D-принтеров для печати металлом, большинство из них расположены в Германии. Их технологии идут под аббревиатурой SLM (выборочное лазерное плавление) или DMLS (прямое спекание металла лазером).
Процесс # 2: Binder Jetting
Еще один профессиональный метод с послойным соединением — склеивание частиц металла для последующего обжига в высокотемпературной печи, где частицы сплавляются под давлением, составляя единое металлическое целое. Печатная головка наносит соединительный раствор на порошковую подложку послойно, как обычный принтер на листы бумаги, после чего изделие отправляется в обжиг.
Еще одна похожая, но отличающаяся технология, в основе которой лежит FDM печать — замешивание металлического порошка в металлическую пасту. С помощью пневматической экструзии, 3D-принтер выдавливает ее, подобно тому, как строительный 3D-принтер делает это с цементом, чтобы сформировать 3D-объекты. После того, как нужная форма напечатана, объекты также спекают в печи. Эту технологию использует Mini Metal Maker — возможно, единственный более-менее доступный 3D-принтер для печати металлом ($1600). Прибавьте стоимость небольшой печки для обжига.
Процесс # 3: Наплавление
Можно подумать, что среди технологий печатью металлом отсутствует похожая на обычную FDM, однако, это не совсем так. Вы не сможете плавить металлическую нить в хот-энде своего 3D-принтера, а вот крупные производители владеют такой технологией и пользуются ею. Есть два основных способа печатать цельнометаллическим материалом.
Один из них называется DED (Directed Energy Deposition), или лазерная наплавка. Он использует лазерный луч для сплавления металлического порошка, который медленно высвобождается и осаждается из экструдера, формируя слои объекта с помощью промышленного манипулятора.
Обычно это делается внутри закрытой камеры, однако, на примере компании MX3D, мы видим возможность реализации подобной технологии в сооружении настоящего полноразмерного моста, который должен быть распечатан в 2017 году в Амстердаме.
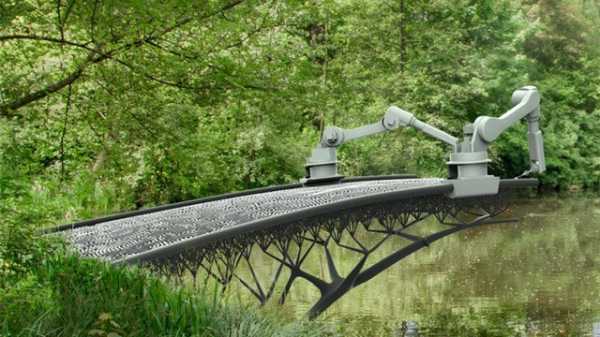
Другой называется EBM (Electron Beam Manufacturing — производство электронным лучом), это технология формирования слоев из металлического сырья под воздействием мощного электронного луча, с ее помощью создают крупные и очень крупные конструкции. Если вы не работаете в оборонном комплексе РФ или США, то вряд ли увидите эту технологию живьем.
Еще парочка новых, едва появившихся технологий, используемых пока только их создателями, представлена ниже — в разделе о принтерах.
Используемые металлы
Ti — Титан
Чистый титан (Ti64 или TiAl4V) является одним из наиболее часто используемых металлов для 3D-печати, и безусловно — одним из самых универсальных, так как он является одновременно прочным и легким. Он используется как в медицинской промышленности (в персонализированом протезировании), так и в аэрокосмической и автомобильной отрасли (для изготовления деталей и прототипов), и в других областях. Единственная загвоздка — он обладает высокой реакционной способностью, что означает — он может легко взорваться, когда находится в форме порошка, и обязательно должен применяться для печати лишь в среде инертного газа Аргона.
SS — Нержавеющая сталь
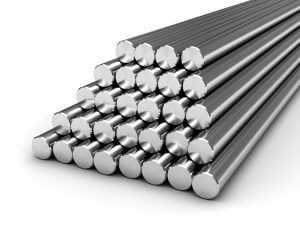
Нержавеющая сталь является одним из самых доступных металлов для 3D-печати. В то же время, она очень прочна и может быть использована в широком спектре промышленных и художественных производств. Этот тип стального сплава, содержащий кобальт и никель, обладает высокой упругостью и прочностью на разрыв. 3D-печать нержавейкой используется, в основном, лишь в тяжелой промышленности.
Inconel — Инконель
Инконель — современный суперсплав. Он производится компанией Special Metals Corporation и является запатентованным товарным знаком. Состоит, по большей части, из никеля и хрома, имеет высокую жаропрочность. Используется в нефтяной, химической и аэрокосмической промышленности (например: для создания распределительных форсунок, бортовых “черных ящиков”).
Al — Алюминий
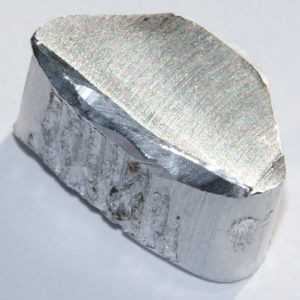
Из-за присущей ему легкости и универсальности, алюминий является очень популярным металлом для применения в 3D-печати. Он используется обычно в виде различных сплавов, составляя их основу. Порошок алюминия взрывоопасен и применяется в печати в среде инертного газа Аргона.
CoCr — Кобальт-хром
Этот металлический сплав имеет очень высокую удельную прочность. Используется как в стоматологии — для 3D-печати зубных коронок, мостов и бюгельных протезов, так и в других областях.
Cu — Медь
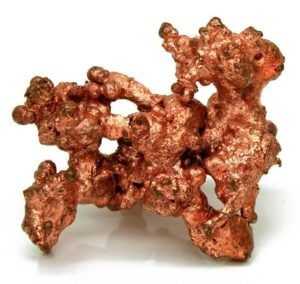
За редким исключением, медь и ее сплавы — бронза, латунь — используются для литья с использованием выжигаемых моделей, а не для прямой печати металлом. Это потому, что их свойства далеко не идеальны для применения в промышленной 3D-печати, они чаще используются в декоративно-прикладном искусстве. С большим успехом они добавляются в пластиковый филамент — для 3D-печати на обычных 3D-принтерах.
Fe — Железо
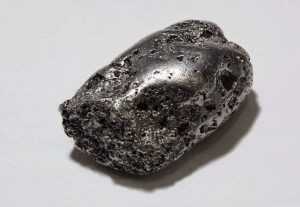
Железо и магнитный железняк также, в основном, используются в качестве добавки к PLA-филаменту. В крупной промышленности чистое железо редко находит применение, а о стали мы написали выше.
Au, Ag — Золото, серебро и другие драгоценные металлы
Большинство сплавляющих слои порошка 3D-принтеров могут работать с драгоценными металлами, такими как золото, серебро и платина. Главная задача при работе с ними — убедиться в оптимальном расходе дорогостоящего материала. Драгоценные металлы применяются в 3D-печати ювелирных и медицинских изделий, а также при производстве электроники.
3D принтеры печатающие металлом
# 1: Sciaky EBAM 300 — титановый прут
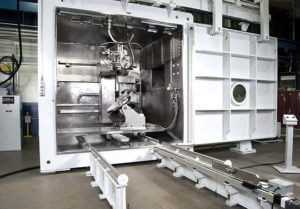
Для печати действительно больших металлических конструкций лучшим выбором будет EBAM от Sciaky. Этот аппарат может быть любого размера, на заказ. Он используется, в основном, в аэрокосмической и оборонной промышленности США.
Как серийную модель, Sciaky продает EBAM 300. Он имеет размер рабочей области со сторонами 5791 х 1219 х 1219 мм.
Компания утверждает, что EBAM 300 является одним из самых быстрых коммерчески доступных промышленных 3D-принтеров. Конструкционные элементы самолетов, производство которых, по традиционным технологиям, могло занимать до полугода, теперь печатаются в течение 48 часов.
Уникальная технология Sciaky использует электронно-лучевую пушку высокой мощности для плавки титанового филамента толщиной 3мм, со стандартной скоростью осаждения около 3-9 кг/час.
# 2: Fabrisonic UAM — ультразвуковой
Другой способ 3D-печати больших металлических деталей — Ultrasound Additive Manufacturing Technology (UAM — технология ультразвукового аддитивного производства) от Fabrisonic. Детище Fabrisonic является трехосевым ЧПУ-станком, имеющим дополнительную сварочную головку. Металлические слои сначала разрезают, а затем сваривают друг с другом с помощью ультразвука. Крупнейший 3D-принтер Fabrisonic — “7200”, имеет объем сборки 2 х 2 х 1,5 м.
# 3: Laser XLine 1000 — металлический порошок
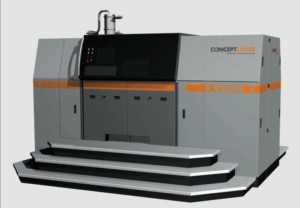
Одним из самых крупных, на рынке 3D-принтеров печатающих с помощью металлического порошка, долго являлся XLine 1000 производства Concept Laser. Он имеет область сборки размером 630 х 400 х 500 мм, а места занимает как небольшой дом.
Изготовившая его немецкая компания, которая является одним из поставщиков 3D-принтеров для аэрокосмических компаний-гигантов, таких как Airbus, недавно представила новый принтер — XLine 2000.
2000 имеет два лазера и еще больший объем сборки — 800 х 400 х 500 мм. Эта машина, которая использует патентованную технологию LaserCUSING (тип селективного лазерного плавления), может создавать объекты из сплавов стали, алюминия, никеля, титана, драгоценных металлов и из некоторых чистых материалов (титана и сортовых сталей.)
Подобные машины есть у всех основных игроков на рынке 3D-печати металлом: у EOS, SLM, Renishaw, Realizer и 3D Systems, а также у Shining 3D — стремительно развивающейся компании из Китая.
# 4: M Line Factory — модульная 3D-фабрика
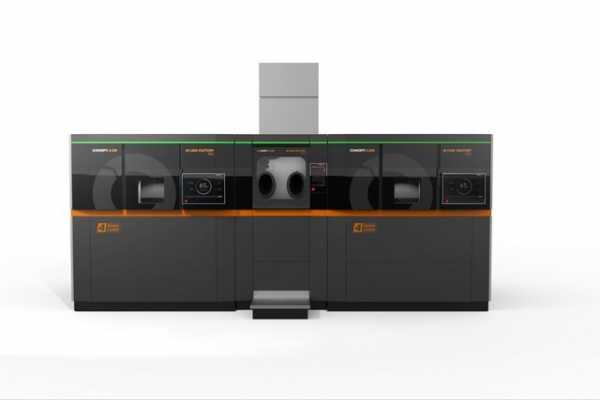
Рабочий объем: 398,78 х 398,78 х 424,18 мм
От 1 до 4 лазеров, 400 — 1000 Вт мощности каждый.
Концепция M Line Factory основана на принципах автоматизации и взаимодействия.
M Line Factory, от той же Concept Laser, и работающий по той же технологии, делает акцент не на размере рабочей области, а на удобстве производства — он представляет собой аппарат модульной архитектуры, который разделяет производство на отдельные процессы таким образом, что эти процессы могут происходить одновременно, а не последовательно.
Эта новая архитектура состоит из 2 независимых узлов машины:
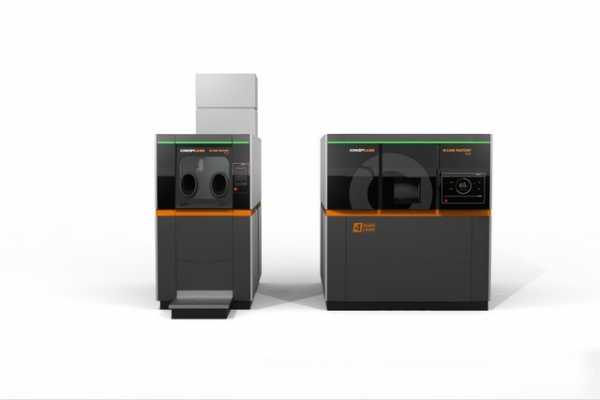
M Line Factory PRD (Production Unit — производственная единица)
Production Unit состоит из 3-х типов модулей: модуль дозирования, печатный модуль и модуль переполнения (лоток для готовой продукции). Все они могут быть индивидуально активированы и не образуют одну непрерывную единицу аппаратуры. Эти модули транспортируются через систему туннелей внутри машины. Например, когда новый порошок подается, пустой модуль хранения порошка может быть автоматически заменен на новый, без прерывания процесса печати. Готовые детали могут быть перемещены за пределы машины и немедленно автоматически заменяются следующими заданиями.
M Line Factory PCG (Processing Unit — процессинговая единица)
Это независимый блок обработки данных, который имеет встроенную станцию просеивания и подготовки порошка. Распаковка, подготовка к следующему заданию печати и просеивание происходят в замкнутой системе, без участия оператора.
# 5: ORLAS CREATOR — 3D-принтер готовый к работе
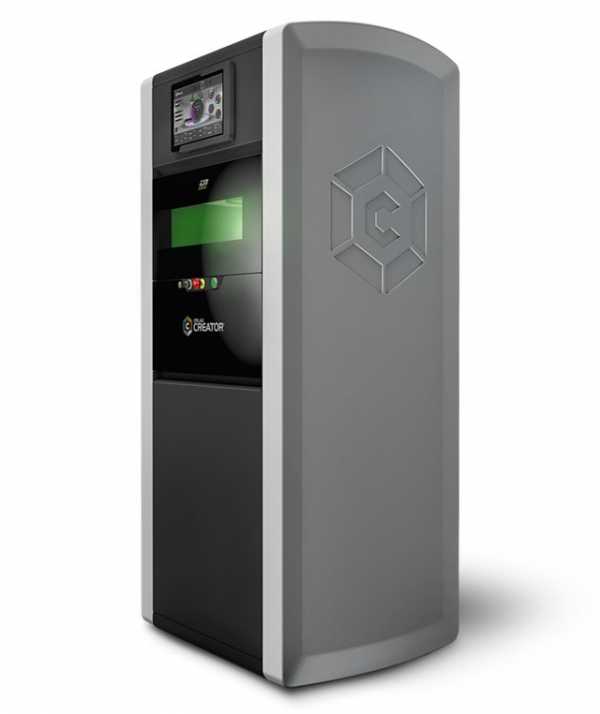
Создатели ORLAS CREATOR позиционируют этот 3D-принтер как максимально доступный, простой в обращении и готовый к работе, не требующий установки никаких дополнительных комплектующих и программ сторонних производителей, способный печатать прямо из файла комплектной CAD/CAM их собственной разработки.
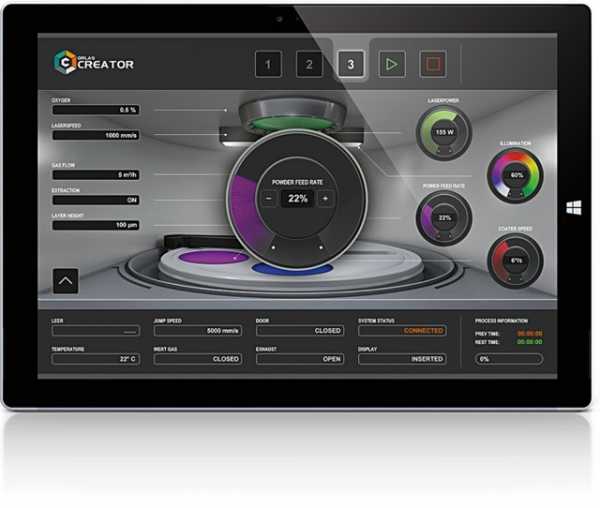
Все необходимые компоненты установлены в относительно компактном корпусе, которому необходимо пространство 90х90х200 см. Много места он не займет, хоть и выглядит внушительно, да и весит 350 кг.
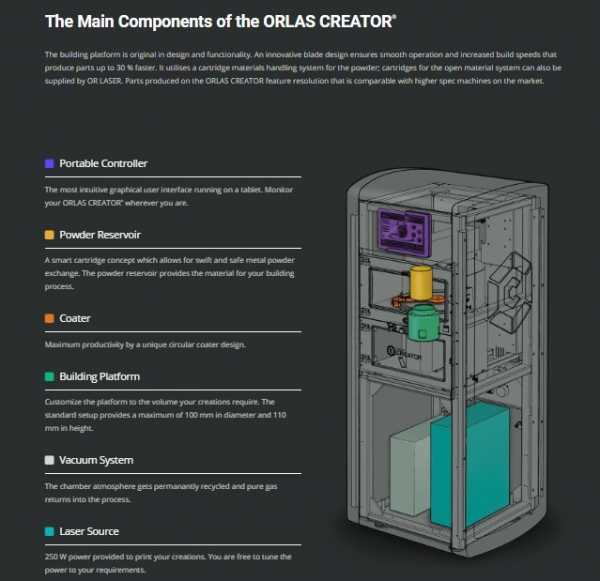
Как можно понять из приведенной производителем таблицы, металлический порошок спекается вращающейся лазерной системой, слоями 20-100 мкм толщиной и с размером “пикселя” всего в 40 мкм, в атмосфере азота или аргона. Подключить его можно к обычной бытовой электросети, если ваша проводка выдержит нагрузку в 10 ампер. Что, впрочем, не превышает требований средней стиральной машины.

Мощность лазера — 250 Ватт. Рабочая область составляет цилиндр 100 мм в диаметре и 110 в высоту.
# 6: FormUp 350 — Powder Machine Part Method (PMPM)
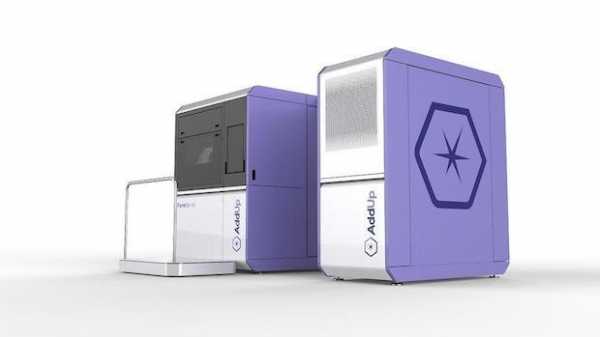
FormUp 350, работающий в системе Powder Machine Part Method (PMPM), создан компанией AddUp — совместным проектом Fives и Michelin. Это новейший аппарат для 3D-печати металлами, впервые представленный в ноябре на Formnext2016.
Принцип работы у этого 3D-принтера тот же, что и у приведенных выше коллег, но его главная особенность в другом — она заключается в его включенности в PMPM.
Принтер предназначен именно для промышленного использования, в режиме 24/7, и рассчитан именно на такой темп работы. Система PMPM включает в себя контроль качества всех комплектующих и материалов, на всех стадиях их производства и распространения, что должно гарантировать стабильно высокие показатели качества работы, в чем у Мишлена огромный многолетний опыт.
# 7: XJET — NanoParticle Jetting — струйная печать металлом
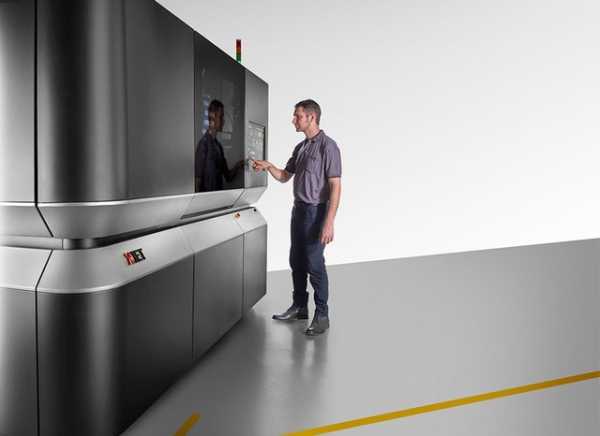
Технология впрыска наночастиц предполагает использование специальных герметичных катриджей с раствором, в котором находится взвесь наночастиц металла.
Наночастицы осаждаются и образуют собой материал печатаемого изделия.
Учитывая заявленные особенности технологии (применение металлических частиц наноразмера), несложно поверить создателям аппарата, когда они утверждают о его беспрецедентных точности и разрешении печати.
# 8: VADER Mk1 — MagnetoJet — струйная печать металлом
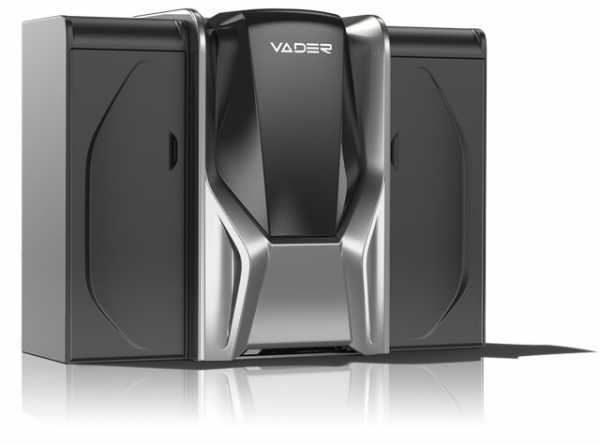
Технология Зака Вейдера MagnetoJet основана на изучении магнитной гидродинамики, а конкретнее — возможности управлять расплавленным металлом с помощью магнитных полей. Суть разработки в том, что из расплавленного алюминия формируется капля строго контролируемого размера, этими каплями и осуществляется печать.
Размер такой капельки — от 200 до 500 микрон, печать происходит со скоростью 1000 капель в секунду. Рабочая область принтера: 300 мм х 300 мм х 300 мм
Рабочий материал: Алюминий и его сплавы (4043, 6061, 7075). И, пусть пока это только алюминий, но принтер в 2 раза быстрее порошковых и до 10 раз дешевле.
В 2018 году планируется выпуск Mk2, он будет оснащен 10 печатающими головками, что должно дать прирост скорости печати в 30 раз.
# 9: METAL X — ADAM — атомная диффузия
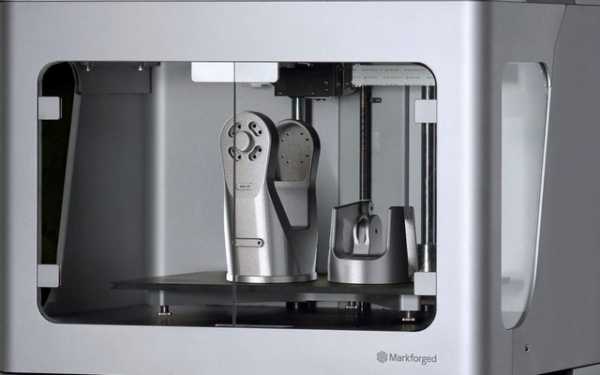
Компания Markforged представила новую технологию 3D-печати металлом — ADAM, и 3D-принтер работающий по этой технологии — Metal X.
ADAM (Atomic Diffusion Additive Manufacturing) — технология атомной диффузии. Печать производится металлическим порошком, где частицы металла покрыты синтетическим связующим веществом, которое удаляется после печати, позволяя металлу соединиться в единое целое.
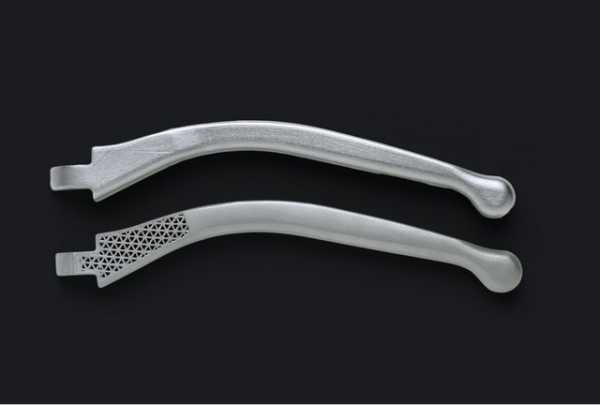
Главное преимущество технологии — отсутствие необходимости применения сверхвысоких температур непосредственно в процессе печати, а значит — отсутствие ограничений по тугоплавкости используемых для печати материалов. Теоретически, принтер может создавать 3D-модели из сверхпрочных инструментальных сталей — сейчас он уже печатает нержавейкой, а в разработке титан, Инконель и стали D2 и A2.

Технология позволяет создавать детали со сложной внутренней структурой, такой как в пчелиных сотах или в пористых тканях костей, что затруднительно при других технологиях 3D-печати, даже для DMLS.
Размер изделий: до 250мм х 220мм х 200мм. Высота слоя — 50 микрон.
Того гляди, скоро можно будет распечатать высококачественный нож — с нуля, за пару часов, придав ему любой самый замысловатый дизайн.
Хотите больше интересных новостей из мира 3D-технологий?
Подписывайтесь на нас в соц. сетях:
habr.com
3D-принтер для печати мелких деталей
Введение
Точное воспроизведение мелких деталей — одно из свойств, за которое 3D-печать и ценится как полезная технология. В статье будет рассказано о точной печати на 3D-принтерах, областях ее применения и связанных с ним преимуществах, необходимом оборудовании.
Источник: all3dp.com
Содержание
Области применения
3D-принтеры уже несколько лет применяются в областях, где требуется точность и высокий уровень детальности изделий:
- архитектурное макетирование и прототипирование;
- миниатюрные изделия;
- стоматология;
- ювелирная промышленность.
Подробнее, с примерами, читайте дальше.
Источник: vulcanjewelry.tumblr.com
Есть несколько причин использовать 3D-принтеры для производства мелких деталей:
- свобода реализации дизайнерских решений,
- экономия временных и трудовых затрат на производство,
- возможность выбора технологии 3D-печати, отвечающей потребностям — декоративное или функциональное применение печатаемых изделий.
Источник: flashforge-eu.com
Далее рассмотрим названные области применения чуть подробнее.
Архитектурное макетирование
В архитектурном макетировании 3D-печать применяется как средство, позволяющее на порядок сократить расходы. Производство макетов устаревшими методами может занимать месяцы и требовать высоких трудозатрат (из-за необходимости ручной сборки). 3D-печать позволяет воссоздавать миниатюрные копии строений и их элементов за считаные часы и с очень высокой детализацией.
Источник: ultimaker.com
Миниатюрные изделия высокой точности
3D-печать может применяться в производстве всевозможных мелких объектов — от фигурок для настольных игр до миниатюрных электромеханических устройств.
Источник: all3dp.com
Мелкие детали, напечатанные на 3D-принтерах — хороший индикатор возможностей оборудования.
Источник: blog.prusaprinters.org
Источник: all3dp.com
Это миниатюрное устройство, напечатанное Лэнсом Абернети из Новой Зеландии, является самой маленькой (15 мм) функционирующей циркулярной пилой в мире. Устройство напечатано на Ultimaker 2 и работает за счёт мотора, питающегося от батарейки для слухового аппарата.
Источник: all3dp.com
Башни были созданы для иллюстрации возможностей высокоточного DLP-принтера Solus 3D. Самая маленькая башня на фото имеет высоту 3 мм.
Источник: 3dlink.me
Куб 2,5 мм был напечатан на SLA-принтере Unirapid 3, особенностью которого является способность производить крайне мелкие и при этом высококачественные элементы. В качестве материала использовалась смола ProtoGen18420.
Образец напечатанный на усовершенствованной, последней модели Юнирапид — Unirapid VI.
Стоматология
3D-печать широко применяется в стоматологии при производстве зубных кап, коронок и имплантатов, так как предлагает множество преимуществ по сравнению с технологиями прошлого. Производители 3D-принтеров реагируют на подобный спрос. Так, Formlabs выпускает мощные SLA-аппараты и широкий ряд стоматологических материалов для 3D-печати. Stratasys производит специализированные промышленные стоматологические 3D-принтеры.
Align Technology Inc. (Invisalign®) и CC Ortho Technology Limited (ClearCaps™) — лидеры рынка, применяющие 3D-принтеры для создания «невидимых» элайнеров и ночных кап.
Источник: angel.co
В производстве элайнеров ClearCaps используются 3D-принтеры Structo (технология MSLA).
Читайте также: «Производство и применение элайнеров на личном опыте — плюсы и минусы»
Источник: Core3dcentres Asia Pacific на YouTube
Align Technology Inc. также является производителем известных 3D-сканеров iTero.
Ювелирные украшения
3D-печать идёт бок о бок с ювелирной промышленностью. В производстве ювелирных изделий применяются специализированные 3D-принтеры и соответствующее программное обеспечение. Многие ювелиры позволяют покупателям принимать участие в разработке индивидуального дизайна украшений. Такие услуги доступны и в частных ювелирных мастерских, и в компаниях покрупнее.
Литьё по выплавляемым моделям
Самый распространённый способ производства ювелирных украшений, в котором применяется 3D-печать — литьё по выплавляемым моделям.
Источник: all3dp.com
3D-модель будущего изделия печатается в воске. Для этого в основном используются методы SLA и DLP, реже — DOD («капельная печать»). Возможна печать множества моделей за один проход.
Источник: 3dbazaar.in
Источник: 3dhubs.com
Полученная восковка заключается в гипс, откуда затем выжигается при высоких температурах. Расплавленный драгоценный металл заливается в образовавшуюся полость — так получается отлитая модель, которая позже подвергается финишной обработке.
Источник: Dezeen на YouTube
Печать металлом
Куда менее распространённый способ производства ювелирных украшений на 3D-принтере — прямая печать металлом.
Источник: timothyruffner на flickr.com
Изделия (или их части) производятся на DMLS-оборудовании и нуждаются в минимальной финишной обработке.
Источник: timothyruffner на flickr.com
Примеры применения 3D-принтеров для точной печати: преимущества и выгода
Ниже описывается несколько случаев успешного применения 3D-печати: кому и какую проблему удалось решить, какие принтеры применялись, в чём заключается выгода.
Студент выровнял себе зубы за $60 при помощи DIY-элайнеров, напечатанных на 3D-принтере
Эймос Дадли — студент Технологического института Нью-Джерси — выровнял себе зубы, используя доступные технологии 3D-сканирования и 3D-печати.
Источник: health.wusf.usf.edu
Проблема
У парня не было денег на услуги ортодонта. В детстве ему ставили брекеты, но он был непослушным (так он говорит) и не довёл дело до конца. Один из зубов у Эймоса стоял криво, и это портило его улыбку.
Решение
Узнав, что в университете есть всё необходимое оборудование, Эймос изучил теоретическую часть и приступил к созданию DIY-элайнеров. У него получилось.
Источник: warosu.org
Комментарий практикующего ортодонта Брента Ларсона из Школы стоматологии Университета Миннесоты:
«Такие DIY-решения всегда заманчивы, из-за возможности сэкономить деньги. Но это же не перепланировка дома, когда вы сможете вызвать профессионала, если что-то пойдёт не так. Ущерб может привести к повреждению корня, рецессии десны и, в худшем случае, к потере зубов».
Источник: warosu.org
Как это делается
Для разработки и 3D-печати прозрачных капп студенту потребовалось следующее:
- некоторые теоретические знания в ортодонтии,
- 3D-сканер,
- слепок зубов,
- CAD-приложение,
- 3D-принтер высокой точности,
- материал для ретейнера
- и вакуум-формовочная машина.
Источник: health.wusf.usf.edu
В чём выгода
Стоимость брендовых «невидимых» элайнеров (Invisalign, Damon, ClearCorrect) — от $2000 до $4000. Эймос определил, каким образом необходимо сдвинуть неровно расположенный зуб и напечатал 12 капп из нетоксичного пластика. Поскольку он заплатил лишь за материалы, это обошлось ему в $60.
Источник: wtvr.com
Применённый принтер и материалы
У Эймоса есть свой 3D-принтер, но недостаточной точности, поэтому использовался университетский Stratasys Dimension 1200es. XY-точность этого 3D-принтера близка к 0,1 мм. В своём блоге парень высказал мнение, что SLA 3D-принтер Form 2 от Formlabs, возможно, подошел бы ещё лучше.
Источник: warosu.org
В качестве пластика для ретейнера использовался Keystone Pro-Form .030”, купленный на eBay. Материал для таких целей должен быть достаточно прочным и нетоксичным.
Источник: huffpost.com
В Rietveld Architects сэкономили месяцы и улучшили обратную связь с клиентами
Rietveld Architects LLP — международная компания, известная в США и Европе своими креативными коммерческими архитектурными пространствами. Маргарет и Рийк Ритвельды узнали о 3D-печати от знакомых из NASA и увидели в технологии возможность повысить продуктивность своей компании.
Источник: rietveldarchitects.com
Проблема
Этапы типичного проекта в Rietveld Architects включали необходимость создания ряда моделей различного масштаба и уровня детализации — чтобы дать клиентам представление о разработанном компанией дизайне.
Источник: rietveldarchitects.com
Эта задача обычно требовала того, чтобы двое работников в течение двух месяцев занимались резкой, сборкой и финишной обработкой компонентов из картона, пенопласта и оргстекла. Высокие затраты на сложное изготовление и ручную сборку не позволяли порой достичь желаемого уровня детализации макета. Так что Ритвельды были заинтересованы в оптимизации этого процесса — в том числе для того, чтобы повысить качество обратной связи со своими клиентами.
Источник: rietveldarchitects.com
Решение
В Rietveld Architects внимательно изучили восемь систем 3D-печати.
Рийк Ритвельд:
«Мы были особенно впечатлены возможностями быстро производить модели высокой детализации, нуждающиеся в минимальной финишной обработке, хотя и
top3dshop.ru
Применение 3D-печати в производстве | 3D-week.ru
Большинство людей думают, что 3D-печать можно использовать только для прототипирования или макетирования, но не для производства конечных изделий. Другими словами, 3D-принтеры не все воспринимают как устройства для серийного производства деталей. И, до недавнего времени, это было верное утверждение.
Однако, есть такие ситуации, при которых наиболее предпочтительным и экономически эффективным методом производства будет именно 3D-печать (здесь и далее FDM-печать).
Из всех распространенных методов для производства пластиковых изделий, 3D-печать имеет свой собственный уникальный набор преимуществ и недостатков.
Печать на 3D-принтере позволяет максимально точно подобрать параметры изделия и отлично подходит для изготовления небольшой партии. 3D-печать позволяет делать детали со сложной геометрией и структурой, именно такие, какими они были задуманы, без оптимизаций под оснастку и каких-либо дополнительных затрат. Эта технология имеет максимальную гибкость изменения продукта после начала серийного производства, и опять же, без затрат. Только представьте, вы запустили на производстве партию изделий и в процессе изготовления выявили недостаток конструкции изделия. Традиционным способом изготовления, например, литье под давлением, потребовалось бы останавливать производство, дорабатывать всю оснастку, а затем запускать процесс по новой. Что же касается 3D-печати, то в данном случае, нужно всего лишь внести изменения в цифровую модель и тут же продолжить печать.
Все понимают, что печать единичных изделий на принтере просто незаменима ни одной из традиционных технологий. Если же рассматривать изготовление очень больших партий деталей, измеряемых сотнями или тысячами единиц, то чаша весов перевешивает в сторону традиционных способов изготовления серийной продукции, главным образом из-за экономической составляющей. Такой способ производства как литье под давлением будет экономически более выгоден при изготовлении 1000 и более изделий. Если посмотреть на диаграмму, которую мы подготовили для наглядности, то можно увидеть зависимость стоимости производимых шахматных фигур от размера партии при литье под давлением и печати на FDM-принтере.
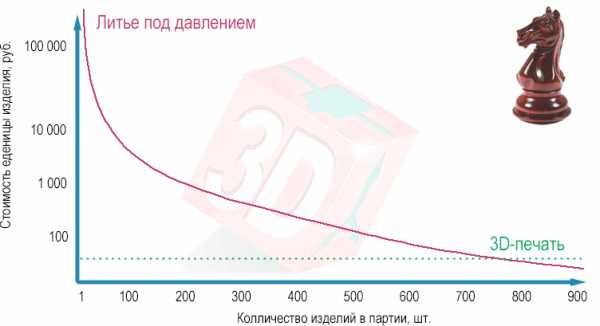
Серийная 3D-печать. Данные, приведенные в диаграмме, усредненные и не являются точным расчетом.
Как вы видите, стоимость производства деталей на 3D-принтере всегда постоянна. При литье под давлением, стоимость оснастки, закладываемая в изделие, делает единичные партии экономически не выгодными, тогда как в больших партиях себестоимость единицы продукции получается ниже, чем при FDM-печати.
Можно привести несколько примеров, когда изготовление больших партий изделий на 3D-принтере было единственно возможным решением.
В 2012 году американский предприниматель Брук Драмм создал недорогой 3D-принтер Original Printrbot и разместил свой проект на Kickstarter, что позволило ему собрать более $ 830 000 от 1 800 спонсоров. Этих средств должно было хватить на создание около 1 200 комплектов запчастей PrintrBot. При этом, каждый набор содержал всего 22 шт. пластмассовых деталей, 16 из которых являлись уникальными.
Для поставленной задачи Бруку необходимо было сделать огромное количество деталей, но традиционные способы изготовления не могли справиться с этой задачей. Если бы он использовал литье под давлением, то это потребовало бы создать большие и очень сложные формы для литья, а значит, понести большие финансовые затраты. В то же время, такая технология имеет ряд ограничений, что не позволило бы Бруку сделать некоторые очень сложные элементы.
Аналогичная ситуация с применением ЧПУ станков с высокой степенью детализации. Детали, выполненные на ЧПУ стоили бы целое состояние.
Выход был найден легко. Детали Printrbot были выполнены на 3D-принтере. Он использовал свой принтер, чтобы создать детали для 10 принтеров. Затем, собрав 10 принтеров, он использовал их одновременно для печати всей партии деталей. Такую мини фабрику он назвал «bot farm».
При цене $ 500 за один Printrbot, его мини фабрика обошлась в сумму около $ 5000. Это конечно не малая сумма для небольшого предпринимателя, но, когда он закончил их использовать для производства деталей, просто продал их.
Таким образом, использование нескольких FDM 3D-принтеров было действительно лучшим способом производства, чтобы изготовить набор деталей в промышленных объемах. Еще одним вариантом применения нескольких FDM-принтеров одновременно может быть ситуация, когда требуется ускорить печать одного большого задания, разделив его на несколько параллельно работающих машин.
Рассмотрим еще один пример применения так называемых ферм 3D-принтеров. Компания Robohand из США использует одновременно 50 FDM-принтеров Makerbot Replicator для печати изделий. Robohand создает функциональные анатомические манипуляторы, которые выступают недорогой альтернативой стандартным протезам для тех, кто остро в них нуждается.
3D-печать на нескольких FDM-принтеров идеально подходит для такого производства, поскольку позволяет сделать много деталей, сохраняя при этом способность настроить каждый элемент манипулятора под особенности конкретного пользователя.
В отечественном производстве 3D-принтеры до сих пор применяются крайне ограниченно. Причина этой проблемы в том, что в России очень мало специалистов в области аддитивных технологий. Тем не менее, в последнее время отмечается рост интереса к 3D-оборудованию со стороны промышленных предприятий. Будем надеяться, что вскоре и на наших предприятиях, по примеру запада, можно будет увидеть массовое применение 3D-принтеров в производстве серийных продуктов.
Понравилось? Покажи друзьям!
3d-week.ru
Производство 3D-принтеров в России. Обзор и интервью — PICASO 3D / Top 3D Shop corporate blog / Habr
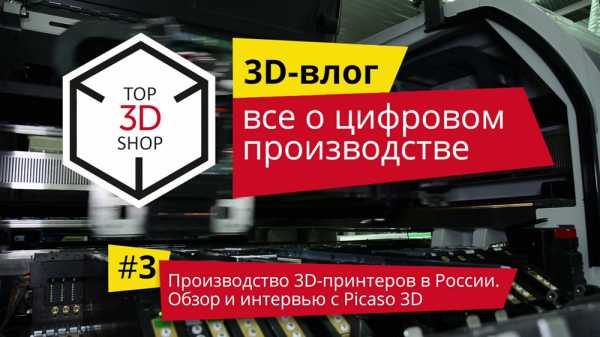
Это третий выпуск видеоблога о цифровом производстве. В этот раз мы расскажем вам о производстве 3D-принтеров в России на примере компании PICASO 3D. Вы увидите экскурсию по фабрике в Зеленограде и интервью с учредителем, узнаете, как всё начиналось и каковы планы известного российского производителя 3D-принтеров на ближайшее время.
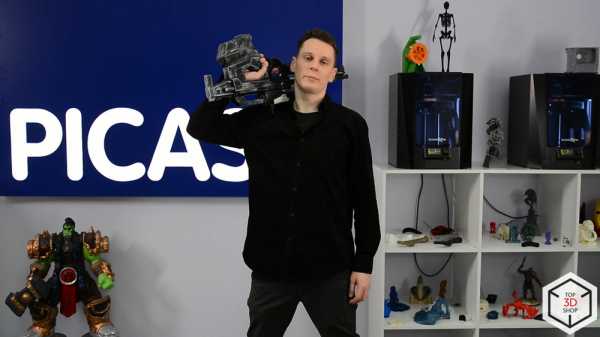
История PICASO 3D началась в 2010 году, когда два студента — Андрей Исупов и Максим Онисимов познакомились с проектом Rep-Rap и за пару месяцев напечатали и собрали в городской квартире свой первый принтер GEN X.
В 2011 они уже продали более 50 таких устройств.
Потом был PICASO 3D Builder и первый опыт серийного производства.
В 2014 стартовала серия PICASO 3D Designer, созданная в рамках которой PRO 250 пользуется популярностью, производится и продается и поныне.
Примененная в этом принтере технология быстрой двухэкструдерной печати JetSwitch перевернула представления о том, какой должна быть FDM-печать двумя материалами.
Наконец, старшая модель линейки, Designer X PRO, получившая в реинкарнацию в новом корпусе, до сих пор остается одним из лучших персональных 3D-принтеров с технологией FDM.
На производстве PICASO 3D нас встретил сооснователь и генеральный директор фирмы — Андрей Исупов.
Андрей рассказал нам о полном цикле производства оборудования, его этапах и разделении работ на конвейере. Всё это вы можете увидеть в видео.
Производство
Автоматика включена в рабочий процесс там, где требуется особая точность — при размещении элементов на печатных платах, их сборке и пайке. Большая часть работ, включая сборку узлов с многократной проверкой работоспособности и качества, производится вручную.
Главный инженер производственной площадки, Вячеслав, рассказал нам о сборке печатных плат.
“Специальные автоматические станки наносят на платы паяльную пасту по трафарету.
Размещают транзисторы и конденсаторы, прочие элементы.
Мелкие комплектующие подаются в сборочный станок на лентах с бобин.
После сборки плата проходит автоматический и визуальный контроль.
Платы проверяются сканирующей системой и сотрудниками на нескольких этапах сборки.
После сборки плата запекается при 270 градусах Цельсия — происходит расплавление припоя и прочное соединение компонентов.
В итоге мы имеем спаянную плату.
Дальше она отправляется на контроль качества, прошивку, выводной монтаж, проверки, а потом поступает в сборку.
Количество брака на производстве плат — 0,02%.”
Участок сборки принтеров разделен на секции.
В одном месте собирают отсеки электроники — в отсек электроники устанавливается печатная плата, затем отсек уходит на проверку.
В следующей секции производится сборка столов — устанавливаются валы, проверяются все размеры, жесткость, дальше стол тоже уходит в ОТК.
На сборке механики натягиваются ремни, устанавливается печатающая головка.
В секции сборки печатающих головок собирают гордость фирмы — печатающие головки с технологией JetSwitch.
Основная особенность этой печатной головки — очень быстрое переключение между материалами и высокое качество печати.
В конструкцию головы включены энкодеры, температурные и другие датчики. Конструкция выполняется с микронными допусками и содержит высококачественные компоненты, что здорово удорожает ее, но служит гарантией качества.
JetSwitch — уникальная разработка PICASO 3D, запатентованная в России, США, ЕС, Китае и Индии. На данный момент, JetSwitch обеспечивает самую быструю и качественную двухматериальную печать по технологии FDM, разработки других компаний отстают, даже таких, как Ultimaker.
Принтеры собираются на каркасе, затем переходят в отдел корпусирования, где на них монтируется внешний корпус, после чего отправляются на тестирование.
Принтеры тестируют на протяжении нескольких дней, проверяют переключение, равномерность подачи, выравнивание стола, все узлы принтера проверяются в работе.
Большинство деталей принтера, такие как каркас, корпусные элементы, платы, производится различными предприятиями в России. Направляющие делает немецкая фирма BOSCH.
В Китае сейчас заказываются шаговые моторы, блоки питания, вентиляторы и стандартные узлы, которые там уже имеют достаточно высокое качество.
Закупаются только качественные детали проверенных производителей, это выходит недешево, но помогает сделать принтер отказоустойчивым и способным работать в режиме 24/7.
Собранные, протестированные и упакованные принтеры хранятся на конечном участке производства до отправки клиентам.
Интервью
С производства мы отправились в офис PICASO 3D, для более детальной беседы.
О названии. Почему именно PICASO?
Мы очень долго выбирали название, были и другие похожие варианты, но остановились именно на этом, как самом понятном, простом и красивом, в т.ч. и для выхода на европейский рынок, на который мы сразу нацелились.
Как ваше увлечение реп-рапом вылилось в производство коммерческого продукта, как так получилось?
На тот момент на рынке было очень мало предложений принтеров, были какие-то полуфабрикаты, никакого намека на дружелюбность к пользователю и эргономичность, простоту работы. Проще говоря, не было ни одного готового к работе профессионального продукта. Мы поняли, что это хорошая свободная ниша, и у нас было представление чем мы хотим ее занять.
Были ли среди первых клиентов производственные компании?
Не так много. Больше было предпринимателей, у которых появились свободные деньги и они решили попробовать что-то новое, вроде 3D-печати на заказ.
Как изменилась целевая аудитория за это время?
Сама технология развивается, оборудование становится более профессиональным, приходит больше клиентов из бизнеса разного калибра. Рост рынка мы видим в индустриальном применении, в работе с серьезными инженерными пластиками выдерживающими экстремальные нагрузки и температурные режимы.
Что нового в материалах?
Материалы с наполнением углеродным волокном появились относительно недавно. Это направление очень интересно тем, что материалы относительно недорогие и имеют очень хорошие прочностные характеристики, а принты из них выдерживают температуры около 200 градусов Цельсия.
Вы готовите какие-то новые материалы к выпуску на рынок?
Да, мы готовим два новых материала. Оба — угленаполненные, это материалы линейки Ultran. Один из них — более индустриальный, имеющий более высокие характеристики на выходе в готовых изделиях, но более гигроскопичный и требующий перед печатью сушки при температуре около 120 градусов в течение трех часов. Если содержать его при 80 градусах или в защищенной от влаги атмосфере, он будет стабильно работать. Второй материал — дороже, дает менее прочные детали, но намного меньше впитывает влагу из воздуха. Сейчас мы как раз проводим тесты, составляем таблицы свойств и к Top 3D Expo будем иметь на руках все характеристики, которые представим на выставке вместе с самими материалами. Основное применение наших материалов — всевозможные инженерные детали. Высокая прочность, слабое трение — очень хорошо подходит для всевозможных шестеренок. Прочность на разрыв в 2-2,5 раза выше, чем у ABS.
Очень интересно. Сколько такой пластик будет стоить?
Пока не буду раскрывать порядок цен, мы назовем их когда анонсируем линейку материалов к продаже. Конечно, стоимость будет выше, чем у бытовых пластиков типа PLA, ведь это материалы целевые, предназначенные для промышленности.
Каковы успехи PICASO 3D на международном рынке?
Пока мы ездим по международным выставкам, вызываем интерес у зарубежных коллег и потенциальных клиентов. Модель X PRO мы создавали именно под международный рынок. В этом году мы начнем рассылку демонстрационных образцов зарубежным дистрибьюторам, к концу года планируем выйти на полноценные международные продажи.
Сколько принтеров вы продаете ежегодно?
Цифры варьируются от года к году, в среднем это около 1500 машин, в этом году хотим продать 2000.
Как так вышло, что у вас вообще есть какие-то конкуренты в России?
Одна компания не может занять весь рынок — существует антимонопольное законодательство. Мы и не стремимся создавать машины для закрытия всех сегментов. Есть ниши, которые пока не входят в наш круг интересов, наша главная цель — создать максимально качественные аппараты в своем сегменте, а не закрыть весь рынок абы чем. Мы с самого начала не хотели делать маленькие хоббийные принтеры — они нам просто не интересны. Мы делаем аппараты для практического промышленного применения, это совсем другая история. Создав JetSwitch и X PRO на его основе, мы подготовили себе платформу для производства новинок, которые отвечают нашим стандартам качества и входят в наш круг интересов.
Будет что-то новенькое? Когда мы узнаем об этом?
Часть мы покажем уже на Top 3D Expo 10 апреля, остальное позже, посмотрим когда.
Как ты видишь развитие аддитивных технологий и цифрового производства вообще? Считаешь ли, что персональный 3D-принтер будет на столе у каждого инженера?
Был такой лозунг “3D-принтер в каждый дом”, так вот — в него я не верю. Этот продукт не для дома. Конечно, есть увлеченные люди, которые и станки дома ставят, и для них эксплуатация 3D-принтера не будет проблемой. Но основная целевая аудитория — профессионалы, для которых это незаменимый инструмент — конструкторы, инженеры. Да, в работе конструктора — самый оптимальный вариант, когда на каждом рабочем месте есть свой персональный 3D-принтер.
Как ты видишь развитие аддитивных технологий в ближайшем будущем?
Никто не знает, какие новые технологии могут появиться на рынке в любой момент и изменить “правила игры”. Пример — технология CLIP, которая возникла внезапно, поменяла SLA-технологии. Что касается FDM, если смотреть на то, что мы имеем сейчас, скорее всего — недорогой сегмент персональных FDM-принтеров начнет меняться — машины будут постепенно дорожать, но намного быстрее увеличивать свои возможности. В первую очередь это касается печати более прочными и более конструктивными материалами.
История PICASO 3D — отличный пример того, что цифровое производство в России живет и развивается, а также прекрасная иллюстрация того, что обычные студенты могут создать свой крутой проект и он станет коммерчески успешным. Я желаю команде PICASO 3D развития на российском рынке, признания на международной арене, а также еще большего количества новинок.
Приглашаем вас на выставку-конференцию Top 3D Expo, которая состоится 10 апреля в Технополисе «Москва». Вход бесплатный, регистрируйтесь на сайте и приходите, предъявив паспорт.
На выставке вы сможете увидеть «живьем» 3D-принтеры PICASO 3D и напечатанные на них образцы, задать вопросы сотрудникам компании и узнать много нового и интересного.
Также в экспозиции — промышленный робот KUKA, болид Bauman Racing Team, стенд виртуальной реальности VR Concept и многое другое.
habr.com
3D-принтеры по металлу, технологии и стоимость
В этом подробном гиде мы рассмотрим основные принципы технологий 3D-печати металлами, расскажем о разнице между ними и приведем примеры применения. Прочитав эту статью, вы узнаете об их преимуществах и ограничениях. Читайте статью и смотрите видео о 3D-печати металлами.
Содержание:
SLM & DMLS: в чем разница
Как работает 3D-печать металлами
Характеристики SLM & DMLS
Параметры принтера
Адгезия между слоями
Область поддержки и ориентация деталей
Полые секции и облегченные конструкции
Расходные материалы для SLM и DMLS
Другие технологии
Осаждение материала путем направленного энергетического воздействия (Directed Energy Deposition)
Послойное нанесение связующего материала (Binder Jetting)
Постобработка
3D-принтеры для печати металлами:
Markforged
HP Metal Jet
Aurora Labs
Digital Metal
3DSLA.RU
Shining 3D
Stratasys
Промышленные 3D-принтеры для печати металлами:
Fabrisonic
Concept Laser
Sciaky
3D Systems
EOS
Своими руками: 3D-принтер по металлу для дома
Mini Metal Maker
DESKTOP METAL Studio System
Ability3D — 888
Плюсы и минусы 3D-печати металлами
Плюсы
Минусы
Выводы
SLM & DMLS: в чем разница
Выборочное лазерное плавление (SLM) и прямое лазерное спекание металлов (DMLS) являются двумя процессами аддитивного производства, которые относятся к семейству трехмерной печати порошковым слоем. Эти две технологии имеют много общих черт: обе используют лазер для спекания или выборочного плавления частиц металлического порошка, связывая их вместе и создавая слои изделия, один за другим.
Различия между SLM и DMLS сводятся к основам процесса склеивания частиц (а также к патентам): в SLM лазер расплавляет металлический порошок, а в DMLS частицы порошка нагреваются меньше и спекаются между собой, не переходя в жидкую фазу.
Основное отличие DMLS от традиционных технологий производства металлических деталей в том, что DMLS-принтер создает объекты без остаточных внутренних напряжений, которые могут снижать качество металлических компонентов изготовленных литьем и штамповкой. Это важно для деталей производимых для автомобильной и аэрокосмической отрасли, так как они должны выдерживать высокие нагрузки.
В SLM лазер расплавляет каждый слой металлического порошка, и перепады температур могут приводить к возникновению внутренних напряжений в детали, что потенциально может сказаться на ее качестве, хоть и в меньшей степени чем, например, при литье. В этом вопросе преимущество SLM перед традиционными технологиями меньше, чем преимущество DMLS. С другой стороны, спеченные по технологии DMLS детали уступают в монолитности и запасе прочности деталям напечатанным по методу SLM.
Технологии похожи до степени смешения, как по принципу действия, так и по используемым техническим решениям, потому некоторые 3D-принтеры способны печатать по обеим методикам.
Обе технологии, SLM и DMLS, используются в промышленности для создания деталей для различных областей машиностроения. В этой статье мы используем термин «3D-печать металлами» для обозначения обоих процессов в целом, и описываем их основные механизмы, что поможет инженерам и дизайнерам в понимании преимуществ и ограничений технологии.
Расскажем и о других технологиях 3D-печати металлами, менее распространенных, таких как электронно-лучевое плавление (EBM) и ультразвуковое аддитивное производство (UAM).
Процесс печати SLM / DMLS:
Более подробно о методе SLM Вы можете прочитать в нашей статье.
Как работает 3D-печать металлами
Процессы изготовления деталей по технологиям SLM и DMLS очень схожи.
Основные этапы:
-
Камеру построения сначала заполняют инертным газом (например, аргоном) для минимизации окисления металлического порошка, а затем нагревают до оптимальной температуры производства.
-
Тонкий слой металлического порошка распределяется по платформе построения, а высокомощный лазер сканирует поперечное сечение компонента, плавя или спекая вместе металлические частицы и создавая следующий слой. Вся область модели подвергается обработке, поэтому деталь сразу твердая.
-
После завершения формирования слоя, платформа построения опускается на толщину слоя и рекоутер наносит следующий слой порошка. Процесс повторяется до завершения всей детали.
Когда процесс печати завершается, детали полностью находятся в металлическом порошке. В отличие от процесса спекания полимерного порошкового слоя (такого как SLS), детали прикрепляются к платформе построения с помощью области поддержки. Области поддержки строятся с использованием того же материала, что и деталь, их необходимо использовать для избегания деформации и искажений, которые могут возникнуть из-за высоких температур обработки.
Когда камера построения остывает до комнатной температуры, неизрасходованный порошок вручную удаляется, а детали обычно подвергаются дополнительной термической обработке для снятия остаточных напряжений, затем удаляют поддержки. Детали отделяются от платформы построения и готовы к использованию или последующей обработке.
Схема принтера SLM / DMLS:
Характеристики SLM & DMLS
Параметры принтера
В SLM и DMLS почти все параметры процесса устанавливаются производителем принтера. Высота слоя, используемого в 3D-печати металлами, колеблется обычно от 20 до 50 микрон и зависит от свойств материала.
Стандартная область 3D-печати металлами варьируется около 250 x 150 x 150 мм, доступны принтеры и с большей областью печати, около 500 x 280 x 360 мм. Точность размеров, которую может достичь 3D-принтер для печати металлами, составляет приблизительно ± 0,1 мм.
Металлический порошок в SLM и DMLS используются повторно: обычно менее 5% уходит в отходы. После каждой печати неиспользованный порошок собирают, просеивают и затем смешивают с новым материалом, до состава необходимого для следующей печати.
В отходы идут, в основном, поддержки.
Небольшое серийное производство рамы велосипеда с использованием SLM. Предоставлено: Renishaw и Empire Cycles.
Адгезия между слоями
Металлические детали, изготовленные методами SLM и DMLS, имеют почти изотропные механические и термические свойства. Они твердые, с очень небольшой внутренней пористостью (менее 0,2-0,5%).
Металлические 3D-печатные детали имеют более высокую прочность и твердость и часто более гибкие, чем детали, изготовленные традиционным способом. Однако они более склонны к усталости.
Например, посмотрите в таблице ниже на механические свойства 3D-печатного сплава AlSi10Mg EOS и литого сплава A360. Эти два материала имеют очень похожий химический состав, с высоким содержанием кремния и магния. 3D-печатные детали имеют превосходные механические свойства и более высокую твердость по сравнению с литым материалом.
Из-за гранулированной формы порошка, шероховатость поверхности (Ra) металлической 3D-печатной детали составляет примерно 6-10 мкм. Эта относительно высокая шероховатость поверхности может частично объяснить более низкую усталостную прочность сплава.
Сравнение механических свойств отдельных разновидностей 3D-печатных и литых деталей:
Основные характеристики |
AlSi10Mg (3D-печатный сплав) |
A360 (Литой сплав) |
Предел текучести (деформация на 0,2%) |
XY: 230 MPa Z : 230 MPa |
165 MPa |
Прочность на растяжение |
XY: 345 MPa Z : 350 MPa |
317 MPa |
Модуль |
XY: 70 GPa Z : 60 GPa |
71 GPa |
Удлинение при разрыве |
XY: 12% Z : 11% |
3.5% |
Твердость |
119 HBW |
75 HBW |
Усталостная прочность |
97 MPa |
124 MPa |
Область поддержки и ориентация деталей
Области поддержки при 3D-печати металлами требуются всегда, из-за очень высокой температуры обработки, и они обычно строятся с использованием решетчатой структуры.
Область поддержки в 3D-печати металлами выполняет три функции:
-
Обеспечивает подходящую платформу для следующего слоя;
-
Прикрепляет деталь к платформе построения и предотвращает ее деформацию;
-
Отводит тепло от детали и позволяет ей остывать с контролируемой скоростью.
Детали часто ориентированы под углом, чтобы минимизировать вероятность деформации и максимизировать прочность в критических направлениях. Однако это увеличивает объем необходимой области поддержки, время печати, количество материала и общую стоимость.
Деформация также может быть сведена к минимуму с использованием бессистемных/случайных шаблонов сканирования, т.е. последовательности прохода лазером участков слоя. Эта стратегия сканирования предотвращает накопление остаточных напряжений в каком-либо конкретном направлении.
Поскольку стоимость 3D-печати металлами очень высока, часто используются симуляции, для прогнозирования поведения детали во время печати. Алгоритмы непрерывной оптимизации также используются не только для максимизации механических характеристик и создания легких деталей, но и для минимизации необходимой области поддержки и вероятности деформации.
Кронштейн перед снятием с области поддержки, ориентированной под углом 45 °. Предоставлено: Concept Laser.
Полые секции и облегченные конструкции
В отличие от процессов спекания полимерных порошковых слоев, таких как в SLS, большие полые секции обычно не используются в 3D-печати металлами, так как области поддержки нельзя легко удалить.
В качестве альтернативы полым сечениям, детали могут быть спроектированы с оболочкой и ядром. Оболочка и ядро обрабатываются с использованием различной мощности лазера и скорости сканирования, что приводит к различным свойствам областей детали. Использование оболочки и ядра очень полезно при изготовлении деталей с большим сплошным сечением, поскольку оно значительно сокращает время печати и вероятность деформации, а также гарантирует производство деталей с высокой стабильностью и отличным качеством поверхности.
Использование решетчатой структуры также является общей стратегией в 3D-печати металлами, для уменьшения массы детали. Алгоритмы оптимизации топологии также могут помочь в разработке органически легкой формы.
Удаление порошка вокруг деталей, изготовленных методом 3D-печати SLM:
Расходные материалы для SLM и DMLS
top3dshop.ru