Способы производства цемента — Завод строительных смесей «ВосЦем»
Процесс производства цемента состоит из следующих основных технологических операций: добычи сырьевых материалов; приготовления сырьевой смеси, обжига сырьевой смеси и получения цементного клинкера; помола клинкера в тонкий порошок с небольшим количеством некоторых добавок.
В зависимости от способа подготовки сырья к обжигу различают мокрый, сухой и комбинированный способы производства цементного клинкера.
При мокром способе производства измельчение сырьевых материалов, их перемешивание, усреднение и корректирование сырьевой смеси осуществляется в присутствии определенного количества воды. А при сухом способе все перечисленные операции выполняются с сухими материалами. Мокрый способ приготовления сырьевой смеси применяют, когда физические свойства сырьевых компонентов (пластичной глины, известняка, мела с высокой влажностью и т.д.) не позволяют организовывать экономичный технологический процесс производства сырьевой смеси по сухому способу производства. При комбинированном способе сырьевую смесь приготовляют по мокрому способу, затем ее максимально обезвоживают (фильтруют) на специальных установках и в виде полусухой массы обжигают в печи. Каждый из перечисленных способов имеет свои достоинства и недостатки.
Способ производства цемента выбирают в зависимости от технологических и технико-экономических факторов: свойств сырья, его однородности и влажности, наличия достаточной топливной базы и др.
Мокрый способ производства цемента.
Сухой способ производства цемента.
Комбинированный способ производства цемента.
Производство цемента складывается в основном из следующий операций: добыча сырья; приготовления сырьевой смеси, состоящего из дробления и ее гомогенизации; обжига сырьевой смеси; помола обожженного продукта (клинкера) в тонкий порошок.
Существуют два основных способа производства – мокрый и сухой. При мокром способе производства сырьевую смесь измельчают и смешивают сырьевые материалы с водой. Получаемая сметанообразная жидкость – шлам – содержит 32-45% воды. По сухому способу сырьевые материалы предварительно высушивают, а затем измельчают и смешивают. Полученный тонкий порошок называют сырьевой мукой.
В зависимости от физических свойств исходных материалов и ряда других факторов при получении цемента по мокрому способу применяют разные схемы производства. Схемы эти отличаются одна от другой только способом приготовления сырьевой смеси. Приводим схему производства цемента по мокрому способу из твердого материала — известняка — и мягкого — глины.
При трехкомпонентной сырьевой смеси корректирующую добавку дробят, после чего она попадает в бункер, откуда вместе с известняком поступает в мельницу. Глину до болтушки пропускают через валковую дробилку. Сырьевые материалы дозируют перед мельницей специальными питателями.
Если при производстве по мокрому способу сырьевую смесь составляют из одних твердых материалов — известняка, мергелей и глинистых сланцев, то их дробят в дробилках без добавки воды и размалывают совместно в мельнице, куда добавляют воду. В том случае в схеме отсутствует болтушка. При изготовлении цемента из одних мягких материалов (мела, глины, мягких мергелей) сырье измельчают в болтушках, после чего размалывают в более коротких шаровых мельницах. В этом случае воду добавляют в первой стадии процесса и материалы дозируют перед ,поступлением в болтушки.
При сухом способе производства выбор схемы зависит от рода поставляемого топлива, физических свойств сырья, мощности завода и ряда других факторов. При использовании для обжига клинкера угля с большим содержанием летучих обжиг ведут во вращающихся печах, — если же применяют топливо с малым содержанием летучих — то в шахтных.
Так как при соприкосновении мелкого порошка, образующегося при помоле, с влагой материала образуется пластичная масса, которая налипает на внутреннюю поверхность агрегата и препятствует дальнейшему помолу, то дробленые сырьевые материалы с естественной влажностью размалывать нельзя. Поэтому после выхода из дробилки сырьевые материалы высушивают и затем направляют в мельницу, где перемалывают в тонкий порошок. Однородные по физическим свойствам материалы можно дробить и сушить в одних и тех же аппаратах. В случае применения гранулированного шлака его подсушивают без предварительного дробления. Помол и сушку сырьевой смеси целесообразно вести одновременно в одном аппарате-мельнице — в том случае, если влажность сырьевых материалов не превышает 8-12%, например, при использовании известняков и глинистых сланцев. Если в качестве сырья используется непластичный глинистый компонент, то при сухом способе производства обжиг ведут только во вращающихся печах. При пластичном глинистом компоненте можно вести обжиг, как во вращающихся печах, так и в шахтных печах. В последнем случае сырьевую смесь вначале увлажняют в смесительных шнеках водой до 8-10%-ной влажности. Затем массу подают в грануляторы, где она вместе с дополнительно подводимой водой превращается в гранулы с влажностью 12-14%. Эти гранулы и поступают в печь.
При обжиге клинкера на газообразном или жидком топливе схема производства упрощается, так как отпадает необходимость в приготовлении угольного порошка.
В ряде случаев может оказаться целесообразным комбинированный способ производства, при котором сырьевая смесь в виде шлама, полученного при обычном мокром способе производства, подвергается обезвоживанию и грануляции, а затем обжигается в печах, работающих по сухому способу.
Выбор сухого или мокрого способа производства зависит от многих причин. Как тот, так и другой способ имеют ряд преимуществ и недостатков. При мокром способе легче получить однородную (гомогенизированную) сырьевую смесь, обуславливающую высокие качества клинкера. Поэтому при значительных колебаниях в химическом составе известнякового и глинистого компонента он целесообразнее. Этот способ используется и тогда, когда сырьевые материалы имеют высокую влажность, мягкую структуру и легко диспергируются водой. Наличие в глине посторонних примесей, для удаления которых необходимо отмучивание, также предопределяет выбор мокрого способа. Размол сырья в присутствии воды облегчается, и на измельчение расходуется меньше энергии. Недостаток мокрого способа — больший расход топлива. Если используют сырьевые материалы с большой влажностью, то расход тепла, затрачиваемого на сушку и обжиг, при сухом способе будет мало отличаться от расхода тепла на обжиг шлама при мокром способе. Поэтому сухой способ производства целесообразнее при сырье со сравнительно небольшой влажностью и однородным составом. Он же практикуется в случае, если в сырьевую смесь вместо глины вводят гранулированный доменный шлак. Его же применяют при использовании натуральных мергелей и тощих сортов каменного угля ,с малым содержанием летучих, сжигаемых в шахтных печах.
При изготовлении сырьевой смеси по любому способу необходимо стремиться к наиболее тонкому помолу, теснейшему смешению сырьевых материалов и к возможно большей однородности сырьевой смеси. Все это гарантирует однородность выпускаемого продукта и является одним из необходимых условий нормальной эксплуатации завода. Резкие колебания химического со·става сырьевой смеси нарушают ход производственного процесса. Высокая тонкость помола и совершенное смешение необходимы для того, чтобы химическое взаимодействие между отдельными составными частями сырьевой смеси прошло до конца в возможно более короткий срок.
При выборе той или другой схемы производства особое внимание следует обращать на рентабельность работы предприятия и возможность снижения себестоимости продукции. Основными мероприятиями, ведущими к снижению себестоимости являются: интенсификация производственных процессов, повышение коэффициента использования оборудования, рост выпуска цемента, повышение его качества (марки), снижение расхода топлива и электроэнергии, механизация производственных процессов и всех вспомогательных работ, автоматизация управления производственными процессами и некоторые другие.
Мощность цементных заводов устанавливают в зависимости от сырьевой базы и потребности района в цементе. На новых заводах она равна обычно 1-2 млн. т цемента в год. Характерным показателем производительности труда на цементных заводах является выпуск цемента на одного рабочего в год, который в 1963 г. составил 915 т. Выработка на одного работающего была 7-62 т. На заводах, оснащенных высокопроизводительным оборудованием, выработка цемента достигла соответственно 2000 и 1600 т.
На цементных заводах, а также на заводах по производству других вяжущих материалов приходится перемещать от одного аппарата к другому большие массы кускового порошкообразного и жидкого материала. Для транспортирования их применяют ковшовые элеваторы, шнеки, ленточные, пластинчатые и скребковые транспортеры, транспортные желоба, насосы, краны с грейферами. Для транспортирования порошкообразных материалов широко используют пневмовантовые и камерные насосы, а также пневмотранспортные желоба.
Транспортирование шлама имеет ряд особенностей, так как он представляет собой сметанообразную текучую массу, содержащую 32-45% воды. Чтобы уменьшить расход топлива на обжиг, стремятся снизить влажность шлама, а чтобы улучшить его транспортабельность, необходимо увеличить содержание воды. По условиям транспортабельности шлам должен течь по желобу, имеющему уклон в 2-4 %. Чем пластичнее сырьевые материалы, тем больше приходится добавлять воды для получения шлама нужной текучести. Обычно шлам транспортируется центробежными насосами.
На заводы сырьевые материалы доставляют из карьера в виде кусков размерами до 1000-1200 мм. Иногда сырьевые отделения расположены непосредственно на карьерах, откуда шлам поступает на заводы. Так, на Балаклейском цементном заводе отделение болтушек размещено на карьере. Сырьевые материалы в виде мела и глины поступают в дробилки, а затем в болтушки. Полученный глиняно-меловой шлам нормальной влажности перекачивается по шламопроводам на завод.
При выпуске цемента обычных марок сырьевые материалы и клинкер размалываются до остатка на сите №008 порядка 8-10%. Для получения цемента более высоких марок материалы размалываю тоньше — до остатка на том же сите около 5% и даже меньше. Измельчать сырьевые материалы до получения тонкого порошка в одном аппарате невозможно. Поэтому сначала материал подвергают в дробилках двyx — тpex стадийному дроблению до величины кусков, не превышающей 8-20 мм, а затем измельчают в мельницах в гонкий порошок с размерами зерен не более 0,06-0,10 мм, глину поступающую из карьера в кусках размером до 500 ММ, измельчают в валковых дробилках до кусков не больше 100 мм, а затем отмучивают в болтушках до получения глиняного шлама с влажностью 60-70%. Этот шлам и подают в сырьевую мельницу.
Удельный расход сырья зависит от его химического состава и зольности топлива и составляет 1,5-2,4 т на 1 т клинкера. Расход электроэнергии на 1 т выпускаемого цемента составляет 80-100 квт/ч.
Все о цементе от компании «АЛЬФА-СПК»
Цемент – связующее вещество при производстве бетонного раствора и других строительных смесей.
Многие люди путают понятия цемента и бетона.
Цемент это мелкий серый порошок, применяемый для производства бетона. Он также является компонентом раствора, который каменщики используют при укладке кирпича и камня, так же он входит в состав того цемента, материалы которого используются при строительстве дамб, мощения дорог, укладки водоемов и т.д.
Производство цемента.
Процесс производства цемента начинается в известняковом карьере. Известняк расположенный близко к поверхности, имеет высокое содержание минералов, таких как: окись алюминия, кремний и железо, чем глубже известняк, тем он чище, в нем содержится меньше минералов и больше углекислого кальция. На заводах по производству цемента используют оба типа породы, что бы меняя пропорции, делать разные марки цемента.
Работники бурят отверстие в стене и закладывают в него мощное взрывчатое вещество. Для безопасности они отходят за пределы взрывной зоны, на расстояние более 50 метров. После произведенного взрыва, подъезжают автомобильные погрузчики, которые загружают известняковую породу в грузовые самосвалы, отвозя руду на ближайшей завод по производству цемента.
Прибывшие на завод машины выгружают породу в первичную дробилку, которая разбивает большие куски породы, на более мелкие кусочки. В такой дробилке постоянно разбрызгивается вода, для того, что бы, пыль не поднималась и не оседала и на желоб. Оттуда раздробленные камни по конвейеру поступают во вторичную дробилку. В ней они еще больше дробятся, уменьшаясь в размерах. Камни с высоким и низким содержанием углекислого кальция дробятся отдельно.
Далее наступает время перемешивания камней, соотношение которых, зависит от марки производимого цемента. Специальный перегружатель формирует кучки в необходимых пропорциях. Затем погрузчик загружает эту смесь в шлифовальную машину — вальцовую мельницу. В зависимости от минералов уже изначально имеющихся в пере дробленой породе на заводе еще добавляют такие минералы как кремний и железо. Для некоторых марок цемента нужна окись алюминия. Роллер равномерно смешивает и размельчает ингредиенты, образуя сухой порошок из камня, называемы каменной мукой. Далее этот порошок идет в подогреватель. На входе температура порошка 80 градусов Цельсия, за 40 секунд она достигает 800 градусов. Начинается процесс соединения минералов и превращения их в материал, затвердевающий при добавлении воды. В подогревателе имеется мгновенный кольценатор. Примерно через 5 секунд с помощью химической реакции он убирает из порошка 95% двуокиси углерода. Отделяется известь, которая является наиважнейшим элементом цемента. Оттуда порок направляется во вращающуюся печь – огромную цилиндрическую топку.
Она установлена под углом, позволяющим порошку перемещаться сверху вниз на расстоянии 49 метров. Печь вращается со скоростью два оборота в минуту, чтобы материал двигался с нужной скоростью. Газовое пламя на дне топки нагревается до огромной температуры – 1700 градусов Цельсия. Когда температура порошка достигает 1500 градусов, он сплавляется в куски размером со стеклянные шарики – они называются клинкерами. При выходе клинкера из обжиговой печи, он охлаждается большими вентиляторами до 60-80 градусов Цельсия. Важно быстро остудить его, чтобы получить качественный цемент. Отсюда клинкер попадает в накопитель.
Последняя ступень производства цемента называется окончательным дроблением. В клинкер добавляется немного гипса. Точное количество зависит от марки производимого цемента. Гипс, замедляет время застывания цемента, поэтому до затвердения с ним можно работать около двух часов. Цементные дробилки или шаровые мельницы, называются так из-за находящихся в них металлических шариков. В самых крупных дробилках их около 150 тонн. При вращении дробилки, шары разбивают и измельчают клинкер и гипс до мелкого порошка. После всех произведенных процессов, получается готовый к применению цемент.
Доставка цемента осуществляется при помощи автомобилей-цементовозов (цементовозный прицеп) или железнодорожными платформами (вагон-цистерна) для перевозки цемента. Это позволяет сберечь от внешних воздействий качество и свойства цемента, а так же транспортировать его на большие расстояния.
Цена и стоимость цемента определяется исходя из нескольких составляющих. Во-первых, она зависит от марки или класса цемента, которые обозначают предел прочности на сжатие (простыми словами – прочность при сжатии). Чем выше марка или класс, тем выше прочность готового изделия. Во-вторых, цена так же зависит от сезона – в зимний период цена выше, так как производство цемента более энергозатратно. Так же зимой необходимо повышать морозостойкость цемента путем введения различных добавок, которые, несомненно, повлияют на стоимость продукции. И, в-третьих, цена зависит от конъюнктуры рынка – удаленности завода-производителя, сезонности, специфики региона, уровня его развития и прочих факторов.
Цемент – Анализ – IEA
Ведущие авторы
Дэвид Ходжсон
Пол Хьюз
Авторы
Тиффани Васс
IEA (2022), Cement , IEA, Paris https://www.iea.org/reports/cement, Лицензия: CC BY 4.0
- Поделиться в Твиттере Твиттер
- Поделиться на Facebook Facebook
- Поделиться в LinkedIn LinkedIn
- Поделиться по электронной почте Электронная почта
- Выложить в печать Распечатать
Выбросы CO2
Сокращение выбросов CO 2 при одновременном производстве достаточного количества цемента для удовлетворения спроса будет сложной задачей.
Выбросы цемента продолжают расти — необходимы дополнительные инвестиции для разработки и внедрения новых технологий, чтобы соответствовать сценарию Net Zero
Интенсивность прямых выбросов при производстве цемента в сценарии Net Zero, 2015-2030 гг.
Открытьразвернуть Ключевые стратегии по сокращению выбросов углерода при производстве цемента включают повышение энергоэффективности, переход на топливо с более низким содержанием углерода, повышение эффективности использования материалов (для снижения отношения клинкера к цементу и общего спроса) и продвижение инновационных способов производства с практически нулевым уровнем выбросов.
Энергия
Во всем мире теплоемкость и электроемкость производства цемента за последние десятилетия постепенно снижались по мере того, как печи сухого способа, включая ступенчатые подогреватели и предкальцинаторы (считающиеся самой современной технологией), заменяли печи мокрого способа, а также развернуто более эффективное шлифовальное оборудование. Согласно оценкам, глобальная теплоемкость клинкера оставалась относительно неизменной в течение последних пяти лет и составляла 3,4–3,5 ГДж/т.
Интенсивность тепловой энергии должна значительно снизиться, а использование биоэнергии должно увеличиться, чтобы цемент соответствовал сценарию Net Zero
Глобальная теплоемкость и расход топлива при производстве клинкера в сценарии Net Zero, 2015-2030 гг.

В сценарии Net Zero теплоемкость производства клинкера снижается чуть менее чем на 1% в год до среднемирового уровня около 3,3 ГДж/т, а электроемкость производства цемента в целом снижается до менее 95 кВтч/т (по сравнению с примерно 105 кВтч/т сегодня), без учета дополнительной энергии, необходимой для технологий сокращения выбросов, таких как улавливание и хранение углерода (CCS).
Ископаемые виды топлива по-прежнему обеспечивают большую часть энергии в цементном секторе, при этом биоэнергия и отходы на основе биомассы составляют лишь около 4% тепловой энергии, используемой в 2021 году. Доля биоэнергии и возобновляемых отходов значительно вырастет до 14% в 2030 году в сценарии Net Zero. Между тем, доля отходов на основе ископаемого топлива (таких как пластик, отработанное масло и промышленные отходы на основе ископаемого топлива) остается на уровне около 5% от использования топлива, примерно на том же уровне, что и в 2021 году.
Активность
В 2021 году было произведено около 4 300 млн тонн цемента, поскольку отрасль восстанавливается после небольшого спада в 2020 году. Китай внес наибольший вклад в мировое производство, на его долю приходится около 55% от общего объема, за ним следует Индия с 8%.
Производство цемента в последние годы оставалось относительно стабильным – в сценарии Net Zero эта тенденция сохраняется благодаря политике повышения эффективности использования материалов
Мировое производство цемента в сценарии Net Zero, 2010–2030 гг.
Открытьразвернуть Производство в Китае, вероятно, сократится в долгосрочной перспективе, но ожидается его увеличение в Индии, других развивающихся странах Азии и Африке по мере развития инфраструктуры этих регионов. Прогнозируется, что это увеличение более чем компенсирует спад в Китае, что приведет к росту мирового производства цемента до 2030 года по базовой траектории.
Это отличается от сценария Net Zero, в котором мировое производство цемента остается относительно неизменным до 2030 года благодаря более эффективному использованию материалов и альтернативным строительным материалам. Действия по снижению спроса на цемент включают оптимизацию использования цемента в бетонных смесях, более эффективное использование бетона, минимизацию отходов в строительстве и максимальное увеличение расчетного срока службы зданий и инфраструктуры.
Развертывание технологий
Клинкер является основным компонентом цемента, и его количество прямо пропорционально выбросам CO 2 , образующимся при производстве цемента в результате как сжигания топлива, так и разложения известняка в процессе производства клинкера. По оценкам, с 2015 по 2020 год глобальное отношение клинкера к цементу увеличивалось в среднем на 1,6% в год, достигнув примерно 0,72 в 2020 году; это увеличение было основной причиной увеличения прямого CO 2 интенсивность производства цемента за период.
Наоборот, отношение клинкера к цементу падает на 1,0% в год до среднемирового значения 0,65 к 2030 г. по сценарию Net Zero из-за более широкого использования смешанных цементов и заменителей клинкера. В долгосрочной перспективе более важными станут заменители клинкера, изготовленные из широкодоступных материалов, таких как кальцинированная глина в сочетании с известняком, поскольку декарбонизация других секторов снижает доступность промышленных побочных продуктов, которые в настоящее время используются в качестве альтернативы, таких как летучая зола из угольных электростанций и измельченный гранулированный доменный шлак сталелитейного сектора.
Соотношение клинкера и цемента во всем мире в последние годы увеличилось — для реализации сценария Net Zero
потребуется более широкое использование заменителей клинкера и инновационных технологий.Развертывание CCS в сценарии Net Zero, 2015–2030 гг.
Открытьразвернуть
Инновации
Для сокращения выбросов при производстве цемента необходимы технологические инновации. УХУ, вероятно, сыграет решающую роль в обезуглероживании цемента, поскольку позволит улавливать технологические выбросы. Альтернативы могут включать производство клинкера из некарбонатных источников, чтобы полностью избежать этих выбросов. Среди достижений прошлого года:
- Проект LEILAC-2, направленный на использование технологии CCS прямого разделения на заводе по производству цемента в Ганновере, получил финансирование в размере 16 миллионов евро в рамках программы EU Horizon и в настоящее время находится на стадии реализации. планируется ввести в эксплуатацию в 2023 г. Другие проекты CCS продолжают развиваться, в том числе Norcem Brevik, использующий химическую абсорбцию, который планируется ввести в эксплуатацию к 2024 г.
- Достигнут прогресс в использовании электрических печей для производства клинкера, и в 2022 году компания VTT Decarbonate запустит первый крупный прототип.
- Компания Brimstone, базирующаяся в США, объявила о разработке нового процесса производства цемента с использованием извести из силиката кальция вместо известняка, что позволило бы избежать образования технологических выбросов в процессе кальцинирования и производить магний- на основе отходов, которые могут даже поглощать выбросы от сжигания топлива. Компания сообщает, что этот процесс будет дешевле, чем традиционные методы производства, и химически идентичен обычному портландцементному клинкеру. Процесс находится на относительно ранней стадии разработки — в лаборатории было произведено около 1 кг — но в 2022 году они объявили о планах построить первый в своем роде демонстрационный завод в Соединенных Штатах.
Чтобы соответствовать сценарию Net Zero, технологии производства цемента с почти нулевым уровнем выбросов должны быть коммерциализированы до 2030 года. например, минимизация потребности в энергии для улавливания CO 2 .
Продвигаются низкоуглеродные инновации благодаря значительным недавним разработкам в области CCS, электрических печей и альтернативных процессов производства клинкера
Вспомогательная инфраструктура
Поскольку CSS, вероятно, сыграет важную роль в сокращении выбросов при производстве цемента, правительства должны разработать планы по строительству инфраструктуры для транспортировки и хранения уловленного CO 2 , поскольку отсутствие вспомогательной инфраструктуры может значительно задержать технологическое внедрение и эффективность. Трубопроводы уже являются наиболее распространенным способом транспортировки CO 2 , и это, вероятно, будет продолжаться. Важным первым шагом для правительств будет получение общественной поддержки для строительства этих трубопроводов, а также CO 2 складские помещения, чтобы обеспечить безотлагательное развертывание в будущем. Поскольку прогнозируется снижение использования ископаемого топлива в сценарии Net Zero, правительства со значительной нефтегазовой инфраструктурой могут также захотеть изучить возможность перепрофилирования трубопроводов для транспортировки CO 2 .
Потребуются значительные инвестиции в расширение инфраструктуры CO2 для реализации сценария Net Zero
Политика
Многие штаты ввели политику, касающуюся промышленных выбросов в целом, что более подробно обсуждается на странице отслеживания МЭА для промышленности. Важные изменения для цемента включают следующее:
Выбросы цемента регулируются схемами ценообразования в ряде юрисдикций, включая Европейский Союз (вместе с Европейской ассоциацией свободной торговли), Канаду и Корею. Совсем недавно Китай, на долю которого в 2020 г. приходится более половины мирового производства цемента, объявил, что установит цену на выбросы цемента, возможно, уже в 2023 г.
Европейский Союз находится в процессе разработки механизма корректировки углеродных границ для отраслей промышленности, включая цемент, который будет применять тарифы на товары с интенсивными выбросами из иностранных юрисдикций со слабой или отсутствующей политикой выбросов, чтобы ограничить утечку углерода и стимулировать более сильные меры по выбросам в зарубежных странах.
Франция и Япония недавно выпустили дорожные карты по обезуглероживанию цементного сектора, установив конкретные цели по обезуглероживанию и наметив конкретные шаги по обезуглероживанию своих цементных секторов. Французский план предусматривает сокращение выбросов на 35 % к 2030 году. В 2015 году Великобритания выпустила дорожную карту обезуглероживания цемента.
Многие страны начинают уделять больше внимания проблемам обезуглероживания цемента
Международное сотрудничество
Разработчики политики все больше координируют свою работу для решения проблем, связанных с декарбонизацией цементной и бетонной промышленности, включая угрозу утечки углерода и потребность в дополнительных инвестициях в разработку и внедрение экологически чистых технологий. Важным событием в 2021 году стала COP26, на которой Великобритания и Индия возглавили инициативу Министерства чистой энергетики по глубокой промышленной декарбонизации, направленную на поощрение государственных закупок стали и бетона с низким уровнем выбросов с целью создания рынка для этих товаров.
Расширение международного сотрудничества обнадеживает, но предстоит еще много работы
Стратегии частного сектора
Ряд организаций выпустили планы по достижению нулевого уровня выбросов к 2050 году. Наиболее примечательной является Глобальная ассоциация производителей цемента и бетона (GCCA), чьи компании-члены несут ответственность за 40% мирового производства цемента (80% за пределами Китая), установив цель достижения нулевого уровня выбросов к 2050 году. Европейская ассоциация производителей цемента выпустила собственную дорожную карту выбросов, к которой присоединились несколько национальных ассоциаций, включая Великобританию, Индию, Бразилию и Ассоциацию портландцемента США.
Существуют программы, помогающие повысить энергоэффективность производства цемента на пути к появлению прорывных технологий, включая Программу службы анализа пробелов в оценке и поддержки (PEGASUS) и базу данных отчетов GNR Глобальной ассоциации цемента и бетона для использования в бенчмаркинг. Другие программы нацелены на инновации, например, программы Innovandi GCCA.
Инициатива ConcreteZero компании Climate Group, которая была запущена 5 июля 2022 года с участием 17 фирм, объединяет ведущие компании для создания рынка бетона с почти нулевым уровнем выбросов, при этом участники обязуются закупать бетон с низким уровнем выбросов 30% к 2025 году и 50% к 2030 году. Коалиция первопроходцев — группа компаний, использующих свою покупательную способность для создания ранних рынков инновационных чистых технологий, — также планирует выступить с инициативой по обезуглероживанию бетона на COP27 в Египте.
Вместо того, чтобы реагировать на политику правительства, многие крупные производители цемента и отраслевые ассоциации берут на себя ответственность
Рекомендации для политиков
Как и в промышленности в целом, обезуглероживание цемента потребует множества мер, в том числе: На национальном уровне это может включать цены на углерод и коммерческие стандарты с низким уровнем выбросов, в то время как корректировки углеродных границ или международные отраслевые соглашения могут рассматриваться для ограничения утечки углерода.
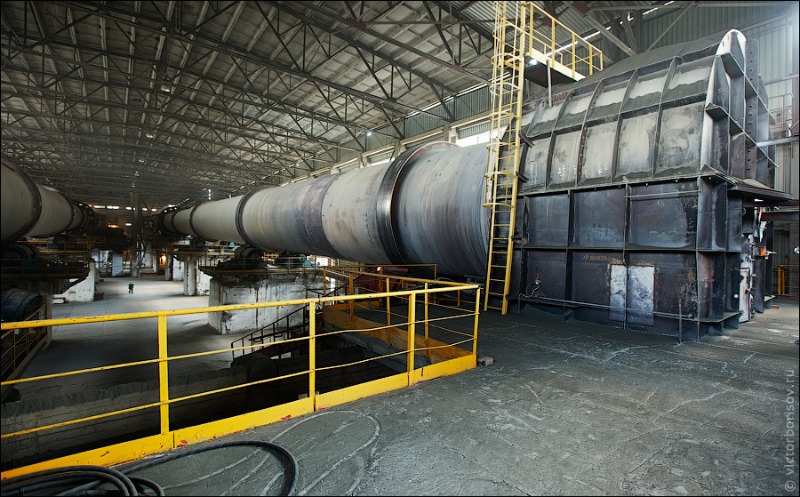
Продвижение комплексной амбициозной политики по сокращению выбросов в промышленности
Рекомендации для политиков и частного сектора
Более широкому внедрению альтернативных видов топлива можно способствовать, перенаправляя отходы со свалок на цементную промышленность и координируя поставки биомассы из устойчивых источников в разных секторах, чтобы обеспечить конкурентоспособный по стоимости доступ к производству цемента.
В долгосрочной перспективе широко доступные заменители клинкера и дополнительные заменители вяжущих материалов, такие как кальцинированная глина в сочетании с известняком, станут более важными, поскольку декарбонизация производства электроэнергии и производства чугуна и стали снизит доступность этих промышленных побочные продукты. Правительствам следует пересматривать и пересматривать соответствующие строительные нормы, политику закупок и стандарты, чтобы гарантировать, что предписывающие требования не являются препятствием для максимального использования заменителей клинкера.
Расширение использования альтернативных видов топлива и заменителей клинкера
Создание спроса на цемент с почти нулевым уровнем выбросов будет иметь решающее значение. Цемент имеет особую потребность в политике, которая стимулирует использование клинкера с почти нулевым уровнем выбросов, в отличие от более широкой политики, которая могла бы вместо этого поощрять переход на другие материалы или использование цемента только с постепенным сокращением выбросов и, таким образом, не закладывая основу для производства с почти нулевым уровнем выбросов. в долгосрочной перспективе. Это важно, поскольку в мире с нулевыми выбросами потребуется значительное количество клинкера, поскольку цемент очень трудно перерабатывать, заменители клинкера могут составлять лишь около половины цемента для большинства применений, а альтернативные вяжущие, которые могут полностью заменить клинкер, либо на самых ранних стадиях разработки, либо могут использоваться только в определенных приложениях.
Кроме того, остаются значительные препятствия для разработки необходимых технологий, строительства заводов и создания цепочек поставок для производства клинкера, поэтому необходима целевая поддержка. Примерами могут служить политика государственных закупок, в которой конкретно указывается, что часть цемента должна поступать из производства клинкера с практически нулевым уровнем выбросов, или предварительные рыночные обязательства, гарантирующие закупку цемента с практически нулевым уровнем выбросов. Углеродные контракты на разницу также могут сыграть свою роль.
Внедрение стратегий по созданию спроса на цемент с почти нулевым уровнем выбросов для стимулирования дальнейшего развития и внедрения
Дополнительные ресурсы
Благодарности
- Роб ван дер Меер, CEMBUREAU, обозреватель
- Нур Амрани, FLSmidth, обозреватель
- Коди Финке, Brimstone, обозреватель
Связанные отрасли и технологии
Промышленность стрелка вправо |
Подача водорода стрелка вправо |
Улавливание и утилизация CO2 стрелка вправо |
Химикаты стрелка вправо |
Железо и сталь стрелка вправо |
Исследователи данных
Все обозреватели данныхcircle-arrow
набор данных карты
Ссылки
Геологическая служба США, статистика и информация по цементу, https://www.
usgs.gov/centers/nmic/cement-statistics-and-information
GCCA (Всемирная ассоциация производителей цемента и бетона), Правильные расчеты, https://gccassociation.org/sustainability-innovation/gnr-gcca-in-numbers/
Геологическая служба США, статистика и информация по цементу, https://www.usgs.gov/centers/nmic/cement-statistics-and-information
GCCA (Всемирная ассоциация производителей цемента и бетона), Правильные расчеты, https://gccassociation.org/sustainability-innovation/gnr-gcca-in-numbers/
Отслеживание прогресса в области чистой энергетики
Оценка важнейших энергетических технологий для глобального перехода к экологически чистой энергии
Исследуйте hubcircle-стрелкаСократите выбросы углерода и токсичных веществ, сделайте цемент чистым и экологичным
Экспертный блог › Вина Сингла Саша Сташвик
18 января 2022 г. Вина Сингла Саша Сташвик
Декарбонизация цементных заводов является важной частью достижения наших целей в области защиты окружающей среды. Цемент является ключевым компонентом бетона, который является наиболее широко используемым искусственным материалом на планете, и практически не имеет жизнеспособных альтернатив. Цемент невероятно грязен в производстве: хотя он составляет всего 10-15% массы бетона в обычной смеси, на его долю приходится до 90% выбросов парниковых газов (ПГ) (рис. 1).
Рис. 1. Слева показан процесс производства бетона, а справа показаны выбросы парниковых газов из бетона, из которых 90 % приходится на цемент и 10 % — на заполнители и другие материалы, а также на разработку карьеров, транспортировку и подготовку сырья.
Источник: Carbon 180
Если бы цементная промышленность была страной, она занимала бы четвертое место в мире по объему выбросов парниковых газов, уступая только Китаю, США и Индии, на долю которых приходится примерно 7-8% мирового выброса CO 2 загрязнение (рис. 2). Если мы не предпримем шаги по обезуглероживанию цемента, это число, вероятно, увеличится, поскольку спрос на бетон продолжает расти.
Рисунок 2: Доля мировых выбросов CO2, связанных с производством цемента (данные за 2017 г.).
Источник: McKinsey
При производстве цемента также выделяется много опасных загрязнителей воздуха, которые наносят вред здоровью; Цементная промышленность является третьим по величине источником промышленных загрязнений воздуха, таких как двуокись серы, оксиды азота (NOx) и окись углерода.
Проще говоря, очистка цементной промышленности имеет решающее значение для достижения наших целей в области климата и здоровья. Но, в отличие от двигателя внутреннего сгорания, у цемента нет доступной замены, которая могла бы масштабироваться достаточно быстро, чтобы соответствовать требованиям чрезвычайной климатической ситуации. Таким образом, хотя сокращение портландцемента и замена его существующими и появляющимися альтернативами может и должно быть приоритетом, наша зависимость от этого материала не только сохранится, но и, вероятно, возрастет в ближайшие десятилетия — сроки, наиболее важные для борьбы с изменением климата, — по мере урбанизации и обновления инфраструктуры. нарастить. Поэтому крайне важно, чтобы мы поддерживали инновации, которые помогают производителям цемента адаптироваться к чистому будущему.
Хорошей новостью является то, что импульс растет в штатах и на федеральном уровне, поскольку законодатели ищут разумные подходы к ограничению выбросов от производства цемента и используют покупательную способность правительства для расширения рынков более чистых альтернатив. Обязательства отрасли по углеродной нейтральности и дорожные карты также распространяются. Хотя некоторые из стратегий обезуглероживания, которые используют некоторые производители цемента, весьма проблематичны с точки зрения окружающей среды и/или здоровья, это говорит о том, что отрасль знает, что должна сформулировать план по борьбе с выбросами.
По мере того, как эти усилия продвигаются вперед, важнейший принцип, за который выступает NRDC, заключается в том, что снижение углеродного загрязнения от цемента не должно происходить за счет местного загрязнения.
Почему при производстве цемента так много углерода: горение и технологические выбросы.
На два аспекта процесса производства портландцемента приходится огромная доля его углеродного следа. Цемент в основном производится путем сжигания ископаемого топлива, такого как уголь и нефтяной кокс, в цементных печах, похожих на большие печи, для нагревания известняка (сырья) до очень высоких температур (~2640°F/1500·9).0298 или С). Тепло вызывает химическую реакцию, которая превращает известняк в клинкер, который затем измельчается вместе с гипсом для образования цемента. Выбросы от сжигания топлива составляют примерно 40 % выбросов CO 2 в цементе в течение жизненного цикла (часто называемых воплощенными выбросами) (рис. 3). Остальные ~60% являются результатом неизбежной химической реакции (прокаливания), происходящей при нагревании известняка, в результате которой из карбоната кальция в известняке выделяется CO 2 .
Рисунок 3. Источники выбросов CO2 в цементной промышленности Калифорнии в 2015 г.
Источник: Global Efficiency Intelligence
Опасные загрязнители, в том числе загрязнители воздуха и ртуть, также выбрасываются в выбросы, связанные как с топливом, так и с выбросами, связанными с технологическими процессами. Эти загрязнители связаны с преждевременной смертью, неврологическими проблемами, астмой и другими респираторными заболеваниями.
Некоторые альтернативные виды топлива, продвигаемые промышленностью, обходятся местному населению неприемлемо дорого.
Среди рычагов, часто упоминаемых для декарбонизации цементной промышленности, переход на твердые отходы топлива для замены ископаемого топлива в цементных печах. К сожалению, эти альтернативы, часто называемые цементной промышленностью «низкоуглеродными», включают пластик и твердые отходы, такие как шины (иногда называемые «топливом, полученным из шин»), которые выделяют очень опасные токсичные загрязнения.
Независимо от того, что сжигается, при сжигании отходов образуются и/или выделяются вредные химические вещества и загрязнители, в том числе загрязнители воздуха, такие как канцерогенный бензол, ПФА, диоксины и твердые частицы, а также тяжелые металлы, такие как свинец и ртуть, которые вызывают неврологические заболевания, как обсуждают здесь наши коллеги. Эти химические вещества и загрязняющие вещества попадают в воздух, воду и продукты питания вблизи мусоросжигательных заводов и попадают в организм людей, когда они вдыхают, пьют и едят загрязняющие вещества.
Сообщества десятилетиями боролись с токсичным загрязнением от цементных заводов, и NRDC утверждает, что снижение выбросов углерода может и должно быть достигнуто без увеличения токсического загрязнения. По этим причинам NRDC выступает против использования в качестве топлива для декарбонизации цементных печей топлива, которое выделяет токсичные загрязнения, включая пластик и другие отходы.
Ключевым решением для обезуглероживания цемента является сжигание меньшего количества
чего-либо .
В дополнение к отказу от перехода на другие токсичные виды топлива, статус-кво сжигания газа и угля также токсичен. Вот почему NRDC выступает за:
- Использование меньшего количества цемента — например, за счет снижения требований к цементу в бетонных смесях и поощрения использования дополнительных вяжущих материалов, таких как пуццоланы из молотого стекла, для частичной замены цемента в бетонных смесях;
- Сделать печи для обжига цемента более эффективными, чтобы они потребляли меньше топлива; и
- Окончательный переход на действительно более чистые виды топлива — например, электрификация из возобновляемых источников, если и где это возможно, а также зеленый водород.
Кроме того, NRDC поддерживает политику, направленную на то, чтобы цементные заводы могли получить доступ к набору передовых технологий для сведения к нулю своих выбросов, включая варианты улавливания, утилизации и хранения углерода, как мы обсуждаем здесь. Улавливание углерода в цементе — это не способ продлить сжигание грязного ископаемого топлива, которое можно заменить, а способ уменьшить большую часть технологических выбросов, которые невозможно уменьшить иным образом для материала, на который мы полагаемся.
Сжигание отходов не является хорошим способом уменьшить загрязнение климата цементом или справиться с потоками пластиковых отходов.
Реальные решения по обращению с пластиковыми отходами должны быть сосредоточены на сокращении отходов в источнике, производстве меньшего количества пластика и использовании эффективных и проверенных методов механической и органической переработки, а не стимулировании сжигания этих материалов.
NRDC поддерживает четыре направления деятельности по сокращению загрязнения пластиком:
- Устранение проблемных и ненужных пластиков, таких как одноразовые пластики;
- Инновации и масштабирование моделей повторного использования и заправки;
- Создание нетоксичных материалов для замены пластика, полученного из ископаемого топлива; и
- Масштабируйте проверенные решения по механической переработке или компостированию.
Пример политики обезуглероживания цемента и бетона должен снизить токсическое загрязнение парниковыми газами
и .
Поскольку правительства штатов и федеральные правительства являются такими крупными покупателями бетона, политика государственных закупок является мощным способом создания спроса на низкоуглеродистый бетон и, в более широком смысле, стимулирования использования цемента с меньшим и меньшим содержанием углерода. Законодательные собрания многих штатов приняли или активно обсуждают законы о закупках низкоуглеродистого бетона для строительных проектов, финансируемых государством, включая Калифорнию, Нью-Йорк, Нью-Джерси, Колорадо и Вирджинию. Ключевым принципом в этой работе должен быть запрет на включение цемента, произведенного с использованием грязного топлива, в государственные спецификации низкоуглеродистого бетона, другими словами, на получение «зеленого» кредита за изменения, которые могут снизить выбросы парниковых газов, но увеличить местное загрязнение воздуха.
Но политика закупок со стороны спроса — не единственный рычаг, доступный для политиков, стремящихся решить проблему воздействия цементной промышленности на климат и здоровье населения.